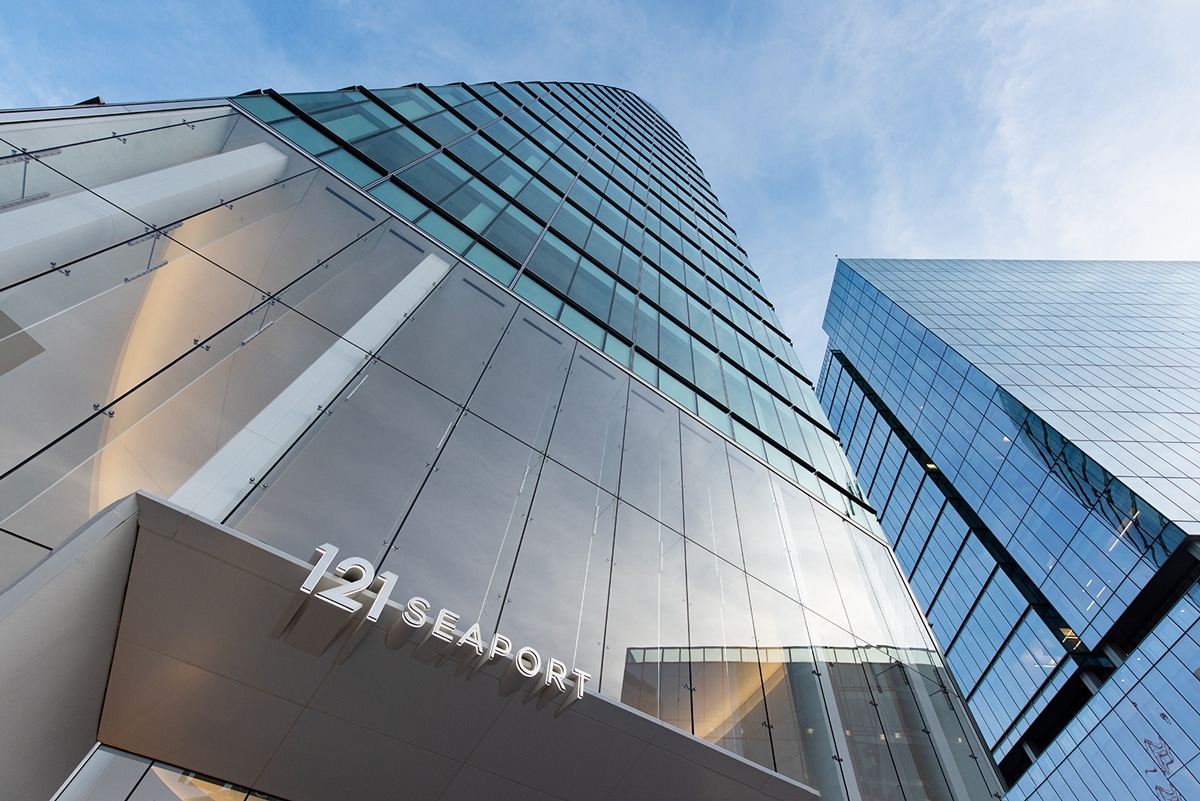
A new office building in downtown Boston is LEED Platinum. [Photo: Courtesy of CBT]
PROJECT: 121 Seaport LOCATION: Boston SIZE: 450,000 square feet COMPLETION: March 2018 COST: $281 million ARCHITECT: CBT GENERAL CONTRACTOR: Skanska LANDSCAPE ARCHITECT: Copley Wolff Design Group STRUCTURAL ENGINEERS: McNamara Salvia GEOTECHNICAL ENGINEERS: Haley and Aldrich MEP ENGINEERS: BalalTMP SUSTAINABLE DESIGN CONSULTANT: The Green Engineer BUILDING ENVELOPE/FAÇADE CONSULTANT: Vidaris INTERIOR DESIGNER: CBT
Along the Boston seaport skyline, one building stands out among the uniform glass buildings. The elliptical shape of 121 Seaport is more than a creative choice—it’s a step toward prioritizing sustainability in design. From interior to exterior, designers of the 17-story urban office building kept environmental impact in mind throughout construction, resulting in LEED Platinum certification. David Nagahiro, principal architect at CBT, says his team set out to create a structure that would not only be iconic, but elevate the standards for both design and sustainability within the neighborhood. We recently sat down with Nagahiro to find out more about the evolution of this project.
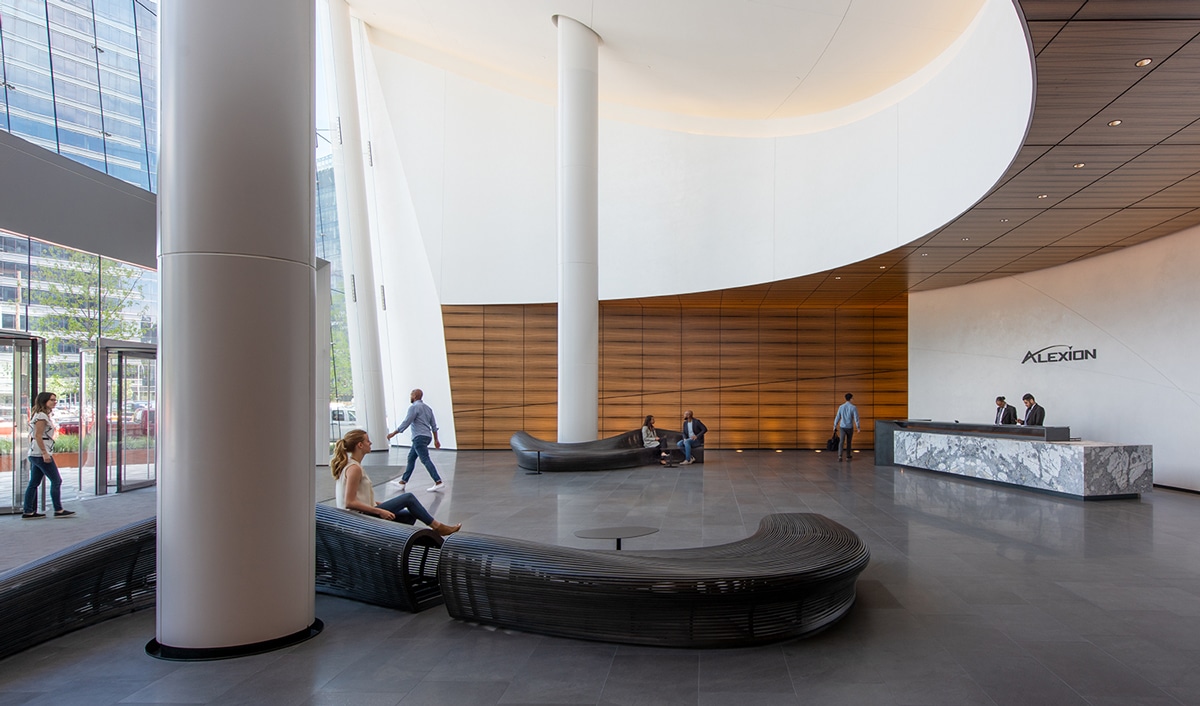
[Photo: Courtesy of CBT]
Tell us more about 121 Seaport. What was that project’s biggest challenge?
The biggest challenge was the underground MBTA Silver Line tunnel that runs beneath one corner of the parcel and significantly limits development opportunities on one of the most prominent areas of the site. This challenge ultimately became one of the project’s greatest strengths in that it drove sustainable strategies early on and allowed us to achieve the same amount of square footage by shifting the massing, reorienting the tower, and resculpting its shape. The result was an elliptical building form that not only avoided the tunnel below-grade, but also created a highly efficient office plate with unparalleled views, reduced shadow on the public realm, and laid a foundation for significant sustainability strategies moving forward.
What was most surprising to you about this project?
During construction in May 2016, the building crew discovered the hull of a shipwreck lodged in the land that would become the building’s foundation. It had been preserved in the clay of what used to be the South Boston Commonwealth Flats and is thought to have been traveling from Maine when it arrived in Boston in the late 19th century. That discovery was definitely surprising and has remained one of the most interesting events I’ve witnessed on a construction site. In fact, upon 121’s completion, Skanska and Copley Wolff Design Group constructed Harbor Way, an interactive open-air museum that celebrates this piece of Boston’s history at the very site on which it was found.
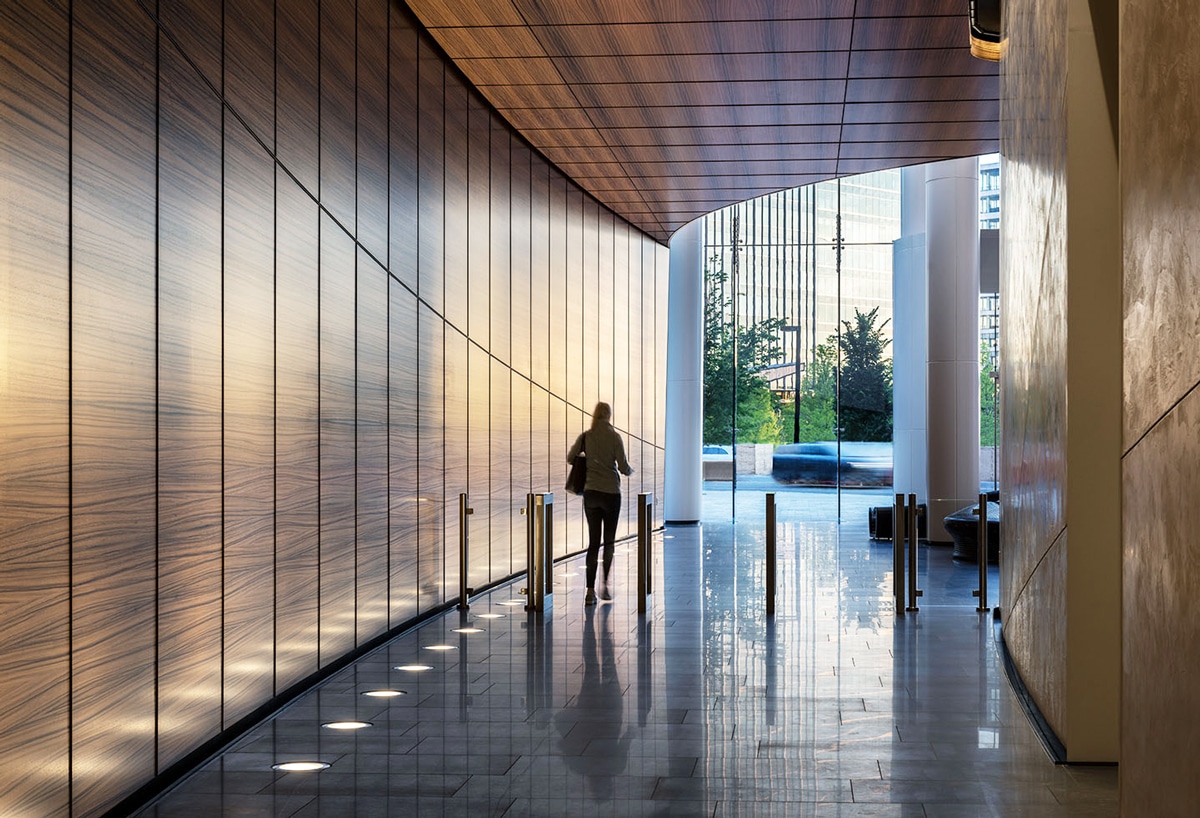
[Photo: Courtesy of CBT]
What are the benefits of the building’s elliptical design?
The design offers many benefits aside from its impact on the skyline. The elliptical form actually reduces the amount of the building’s skin by 10% when compared to a traditional rectangular structure, and its alignment and orientation passively minimize solar heat gain on the exterior. This building orientation also aligns with the prevailing wind direction, and its aerodynamic design reduces lateral wind force, decreasing the amount of structural reinforcement needed for the building by 30% and lowering the overall construction costs of
the project.
Its shape also offers panoramic views of the Seaport, the Boston Harbor, and even the Financial District, bringing as much of Boston’s gorgeous cityscape into the tenants’ experience as possible. Its rounded structure allows natural light to penetrate deeper into the floorplate, an important employee wellness goal in today’s office market. The design provides aesthetic, financial, sustainability, and construction benefits, illustrating just how impactful an intentional building design strategy can be.
What features helped 121 Seaport achieve LEED Platinum status?
Aside from the building’s inherent sustainable aspects, 121 Seaport was constructed from 20% recycled materials to lessen its environmental impact from groundbreaking onwards. The building also utilizes a chilled beam mechanical system that circulates water instead of air to reduce energy consumption and lower costs. Further, 121 has a rainwater harvesting system that collects and recycles rainwater from the roof to be used as graywater in the building’s restrooms, cutting water consumption throughout the building by 30%. At every level of design is an intentional aspect that is aimed at reducing impact and promoting a renewable future.
How was the up-down construction approach utilized to save money and time during the overall construction?
Up-down construction is a relatively new approach to high-rise urban construction that works to significantly condense a project’s construction schedule. With 121, the building timeline was reduced by approximately six months, which allowed for a speedier delivery than traditional urban office projects. The up-down method requires the installation of the foundation elements three floors below grade, followed by the installation of the ground-level slab. From here, the building’s superstructure is erected while the underground garage is simultaneously excavated out, a balancing act that brings the project to completion in a quicker timeframe than doing each of the construction phases
separately