More than a decade ago, entrepreneur Steve Glenn noticed a large and growing demographic that didn’t fit into the typical homebuyer mold. These were urbanites who valued both good design and healthy, sustainable products—and were unwilling to compromise.
He calls them the “cultural creatives.” “They’re buying Volts and Teslas, organic produce, and IKEA furniture. They read Wired and they do yoga,” Glenn says. “The production of homes has not traditionally been focused on these consumers.”
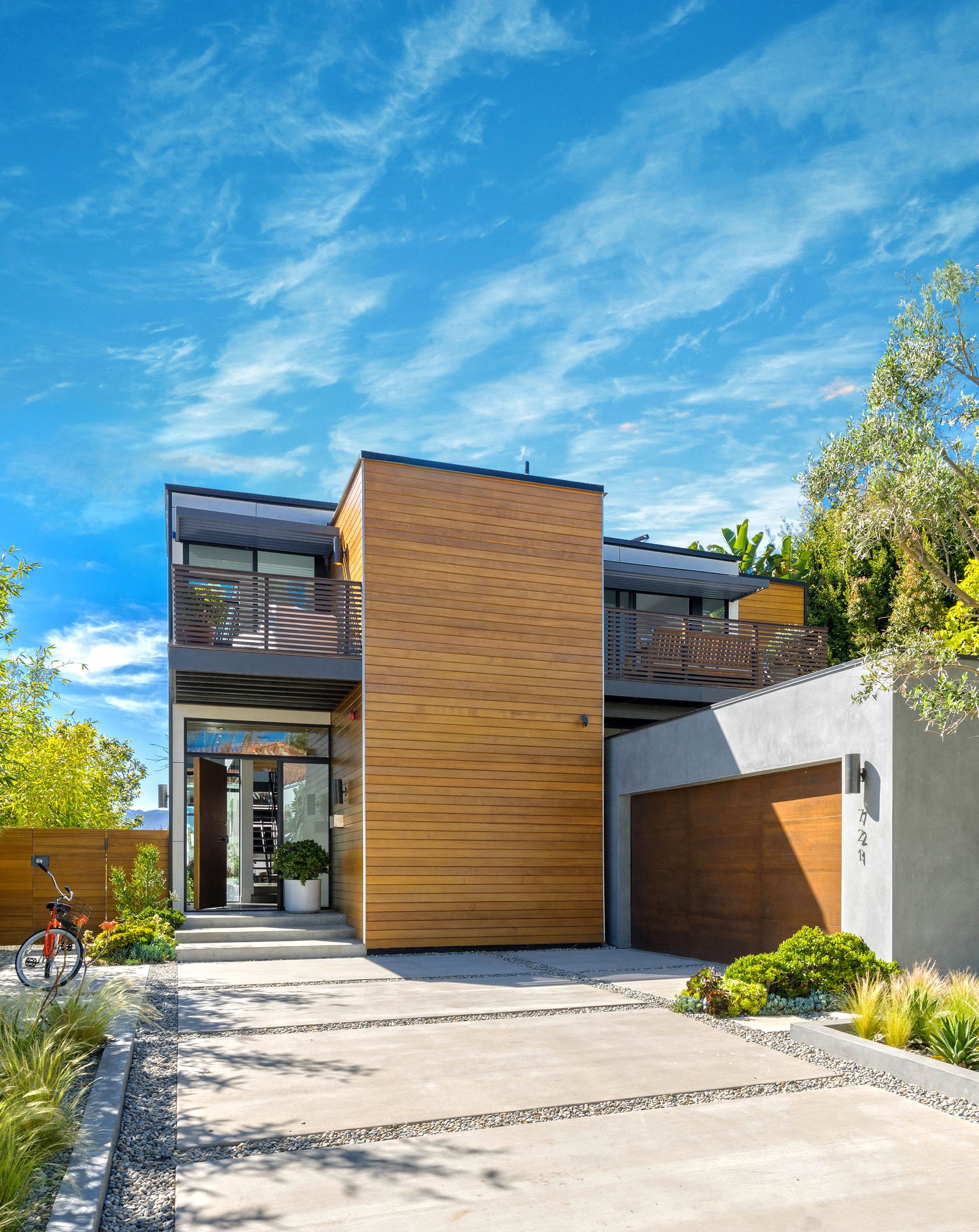
[Courtesy of LivingHomes]
So what is his plan? To get world-class architects to design LEED Platinum level homes using highly efficient prefabrication methods and to market those homes to this urban demographic. Despite one of the worst real-estate downturns in the country’s history hitting shortly after his idea came to fruition, Glenn founded LivingHomes, a company dedicated to the design and development of modern, architecturally stunning yet affordable prefabricated homes that are both sustainable and healthy for consumers.
Sound impossible? Not to Glenn. Since its founding, LivingHomes has made waves. “Our first home was the first in the nation that was certified LEED Platinum. We built the first multi-family project certified LEED Platinum in northern California; the first LEED Platinum multi-family in Silicon Valley; and the first LEED Platinum in Newport Beach.”Â
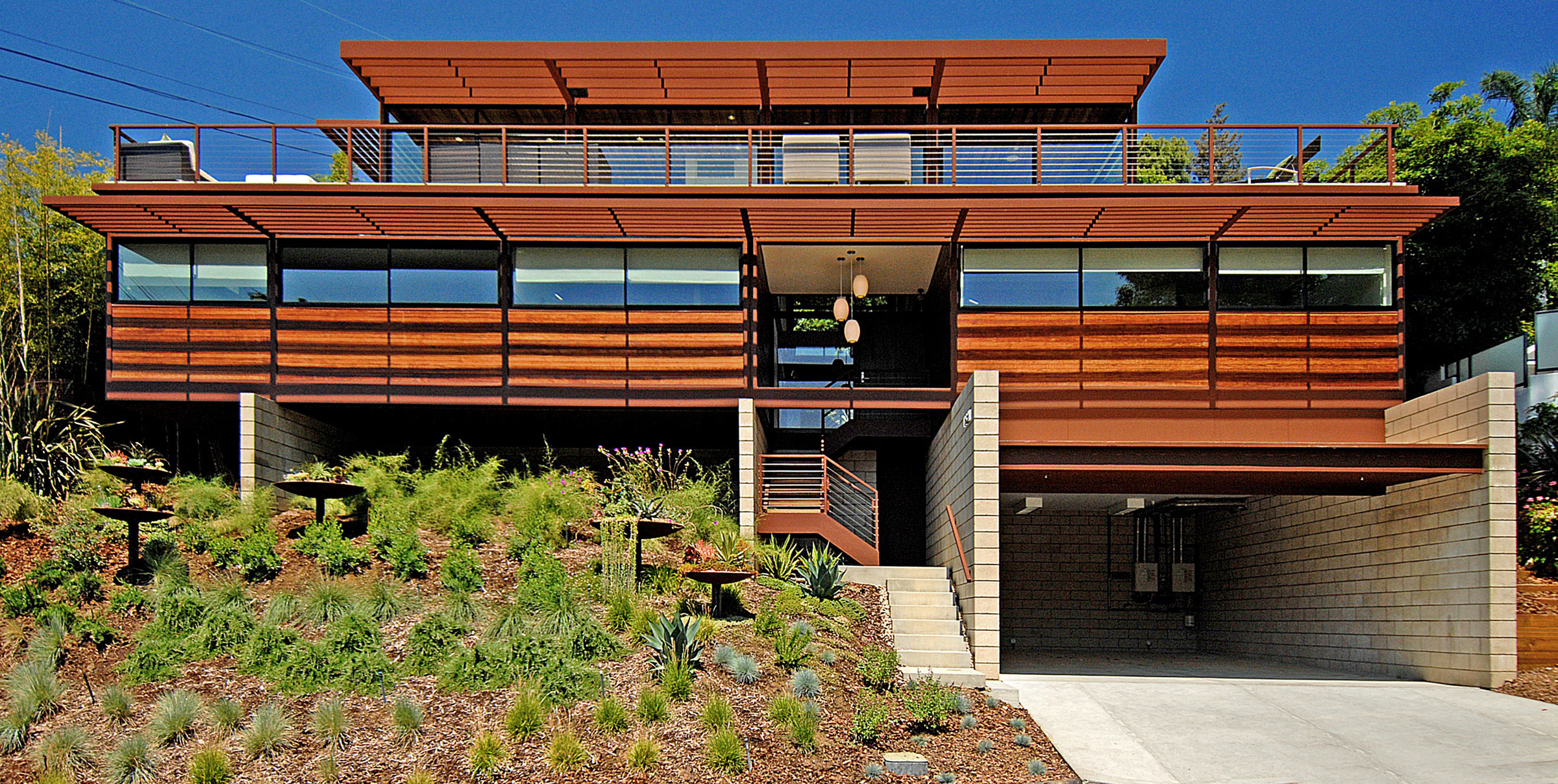
[Courtesy of LivingHomes]
The LivingHomes blend of design genius from architects like Ray Kappe, FAIA; and green functionality, using natural, non-toxic, and sustainably sourced materials; together with the efficiency of building in high-tech factories, quickly made it one of the most experienced LEED Platinum home builders in the country.Â
But for Glenn, the niche he saw—to meet the needs of an exacting group of consumers while addressing rising emissions and sustainability standards in cities across the country—couldn’t be completely filled until he controlled both the design and fabrication processes. For the last 10 years, LivingHomes outsourced its fabrication to factories that make other types of homes—from mobile to modular.
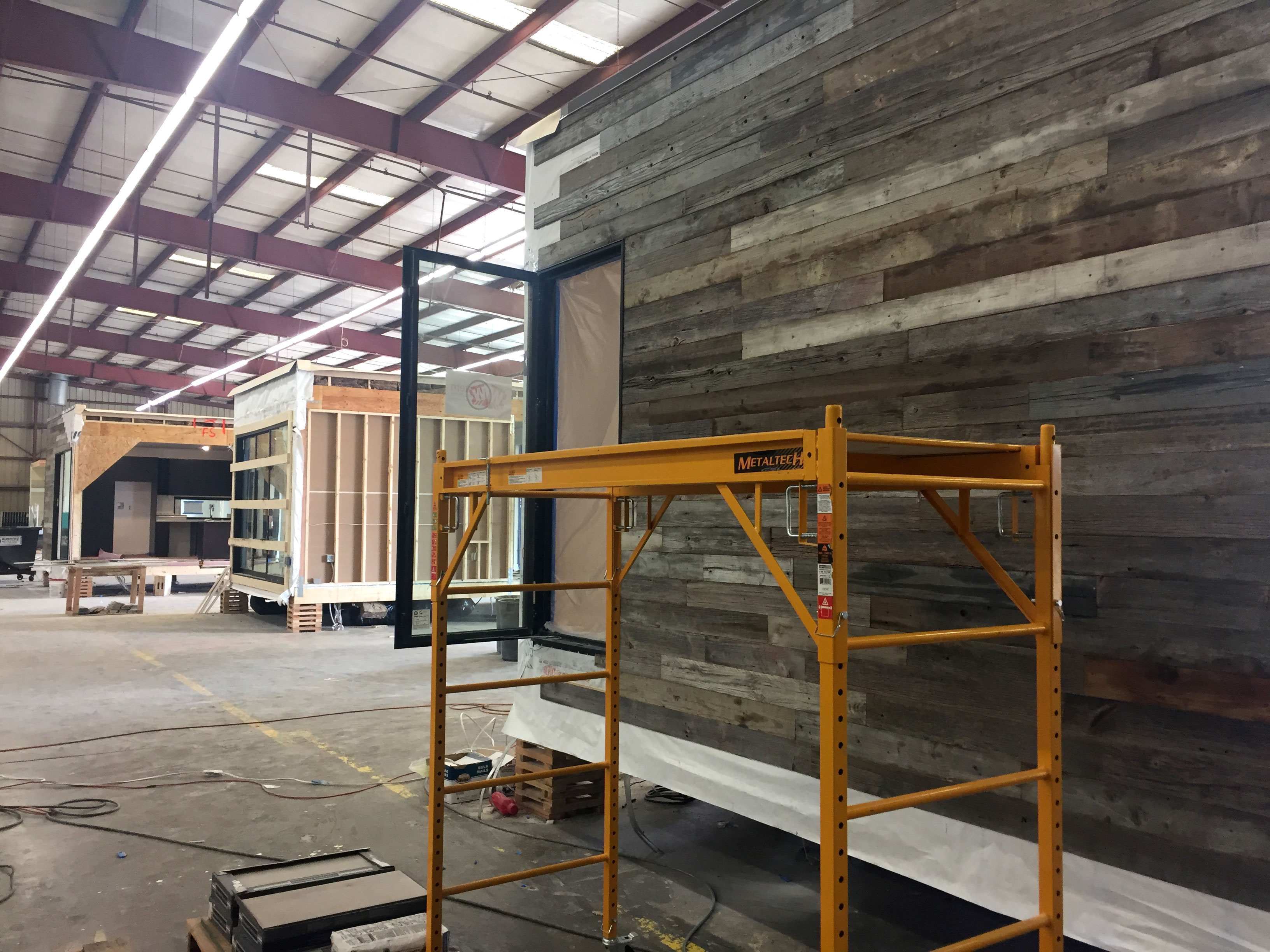
[Courtesy of LivingHomes]
“We never wanted to own our own factory. But now that we have gotten extremely busy, we realized we needed a facility focused just on high-quality, highly sustainable homes.” At the same time he realized that if he solved his own problem he could solve the problems of a lot of other architects and small developers looking for a more sustainable, high-quality way of producing these homes.
The answer was to spin off yet another company to focus on the design and development of sustainable prefabricated homes, especially in urban neighborhoods and cities where populations are booming and housing is scarce. Thus, in 2016, Plant Prefab was born. And with its 62,000-square-foot Rialto, California factory, Plant Prefab is on track to be just as successful as LivingHomes. Glenn says they shipped their third home in fall 2016.
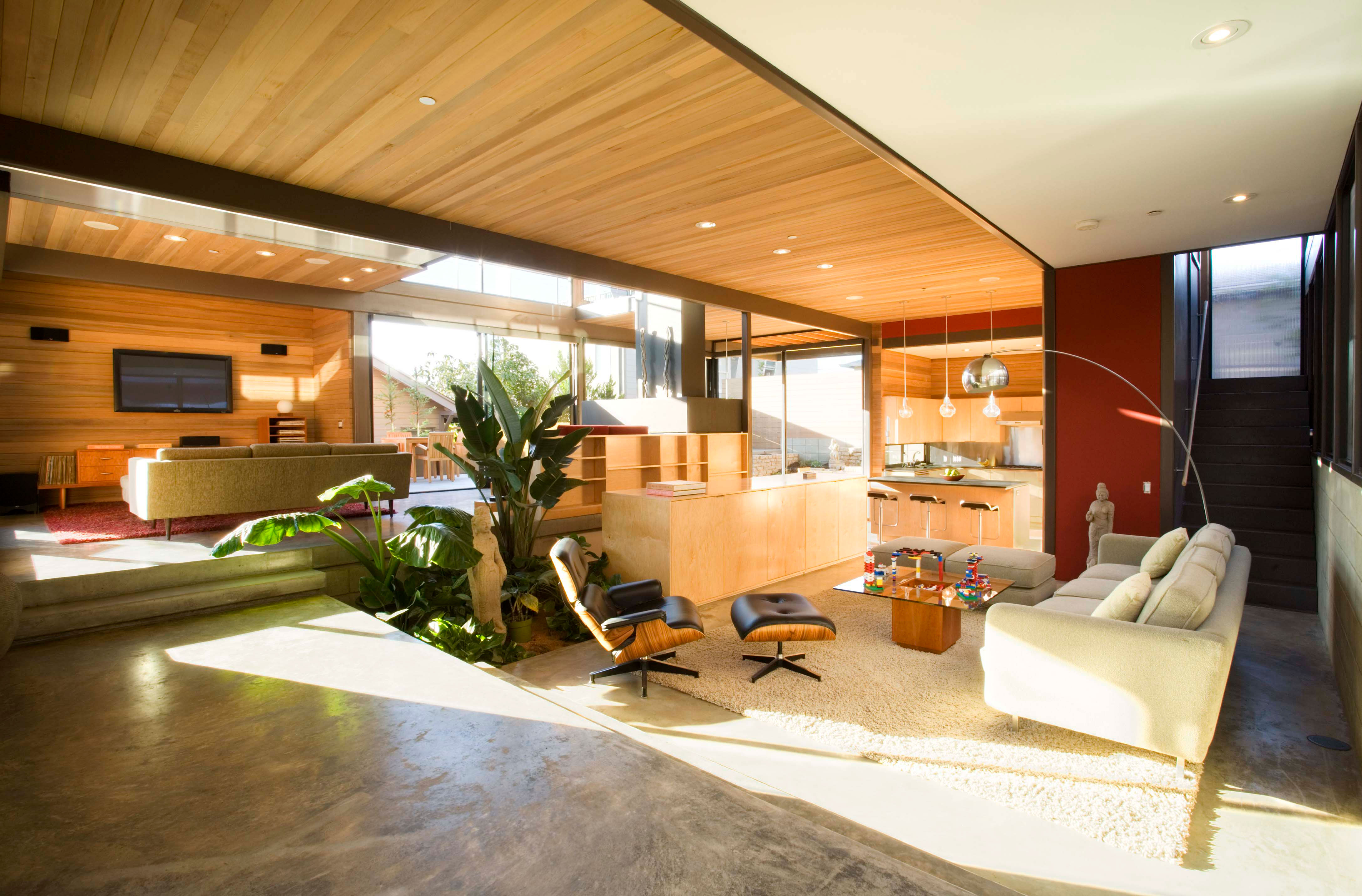
[Courtesy of LivingHomes]
Glenn’s new business targets any individual, developer, or architect doing single or multi-family custom, high-quality building projects. He says in addition to their custom work, they can work with existing plans and love to talk to clients about how to build more efficiently with prefab. Although not everything can be built modularly in the factory yet, he says, the sky might be the limit tomorrow. And the future is coming faster than anyone could have anticipated.