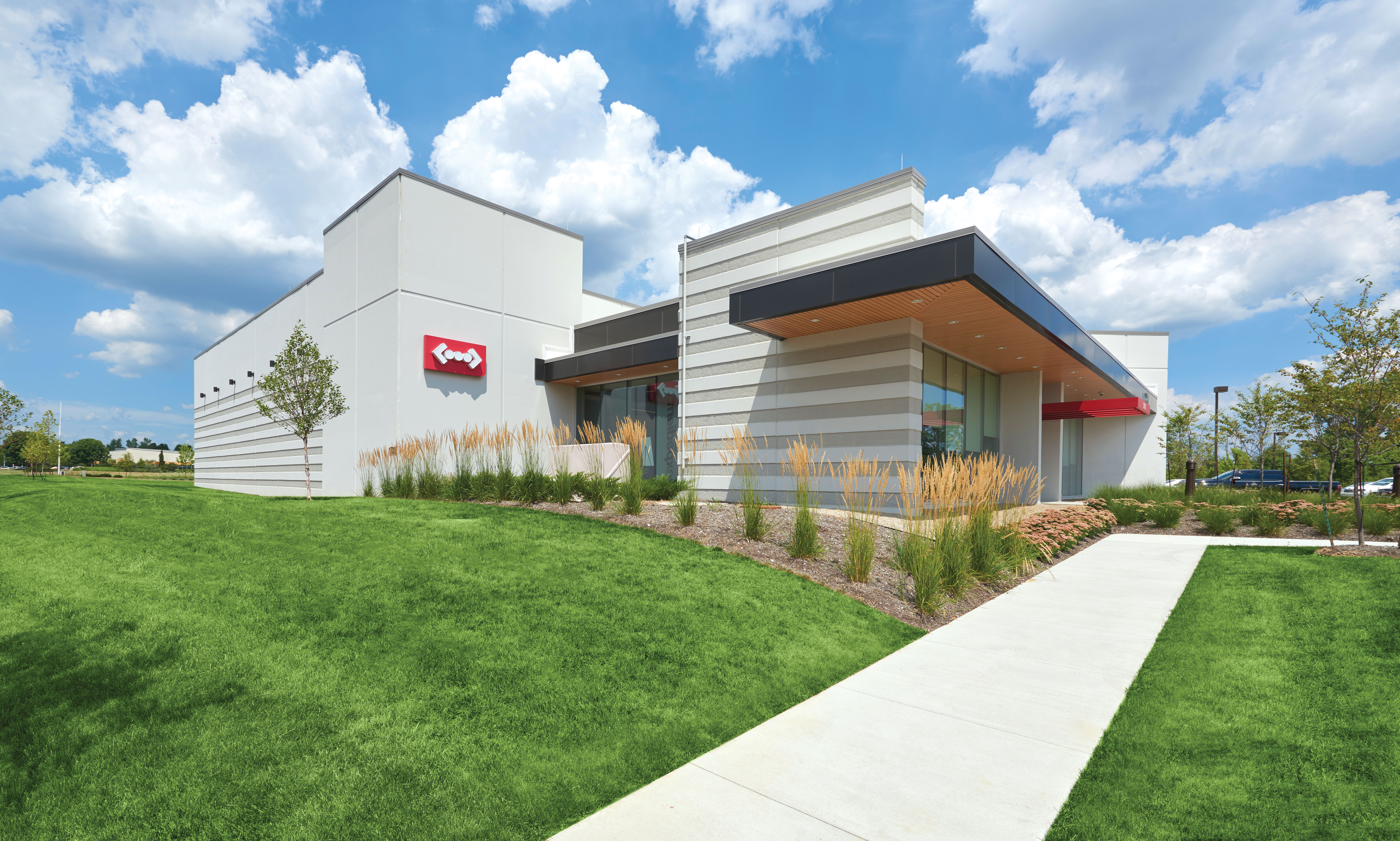
Fabcon got this 30,000-square-foot center up and running quickly, making its panels at its offsite manufacturing facility and shipping directly to the job site. [Photo: Courtesy of FabCon]
As the largest structural precast wall manufacturer in the nation, Fabcon provides precast concrete wall panels to get your building up fast
When it comes to sensitive data, storage facilities have to rise above most typical commercial construction projects, where security and resiliency are critical factors. And considering the growing need for data warehousing—with more and more smart devices and cloud storage comes more and more data—data center development is increasing at a significant pace.
Some major cloud providers are anticipating they’ll need triple the infrastructure by 2020, according to the Jones Lang LaSalle 2017 Data Center Outlook Report.
Structural precast wall panels fulfill extraordinary building envelope requirements that ensure data is safe and secure, with the ability to withstand high winds, fires, and other natural disasters. That’s why when one Ohio company needed to build a new data center, it chose Fabcon—the American company that’s been doing this work for more than 45 years. “First, Fabcon has a great reputation,” says Quandel’s Andy Bensman, the project manager for the Five 9s Data Center in Ohio, a 30,000-square-foot data center that opened in late 2015. “Second, they have an indoor production facility that allows them to maintain operations in winter, which was crucial for our construction schedule.”
Indeed, tight schedules are common in the world of data center construction. Once an owner decides they want to build, has their contractor and architect on board, and secures funding, data center projects move at the speed of light, says Matt Smith, national accounts manager for Fabcon Precast. “They’re very fast schedules. That’s where speed of construction comes in.”
Chris Crosby, CEO of Compass Datacenters, emphasizes that point for his co-location developments. “We have a six-month guarantee to our customers to have their data centers up and running, so I need to find a reliable, efficient solution that is strong enough to meet our rigorous safety standards. Fabcon’s precast walls provide that for us.”
Fortunately, speed is the biggest benefit of using precast wall panels. Precast concrete is one of the fastest building systems available. As for Fabcon, they can set 200 to 250 lineal feet of wall per day. If you think about a building that’s roughly the size of a Kohl’s department store—200 feet by 250 feet—those walls can be up in about four days, Smith says.
Beating the Clock
Fabcon engineers and produces its panels in one of four U.S. production facilities and ships the finished product to the job site in as little as eight weeks, whereas a smaller outfit could take months longer. And you don’t have to hire another crew to erect the panels once they arrive onsite, like with some precasters. Fabcon brings a small team—five or six people—to set their own panels, to further save time and labor, making it easy to do business, rather than having to hire another crew.
Fabcon also has the largest wall panel production capacity of any precaster in the country, Smith says. “Because of our large manufacturing capacity, we have the shortest lead times typically.”
Bensman says the install was fast and efficient—turnkey with no issues. Five9s also just so happened to take home the best office/medical project award at the NAIOP Central Ohio Awards Gala in 2016. “High quality products are a priority on every project for Quandel—precast wall panels are no different,” Bensman says. “Fabcon knows how to push from design to production quickly so you can achieve your overall schedule goals.”
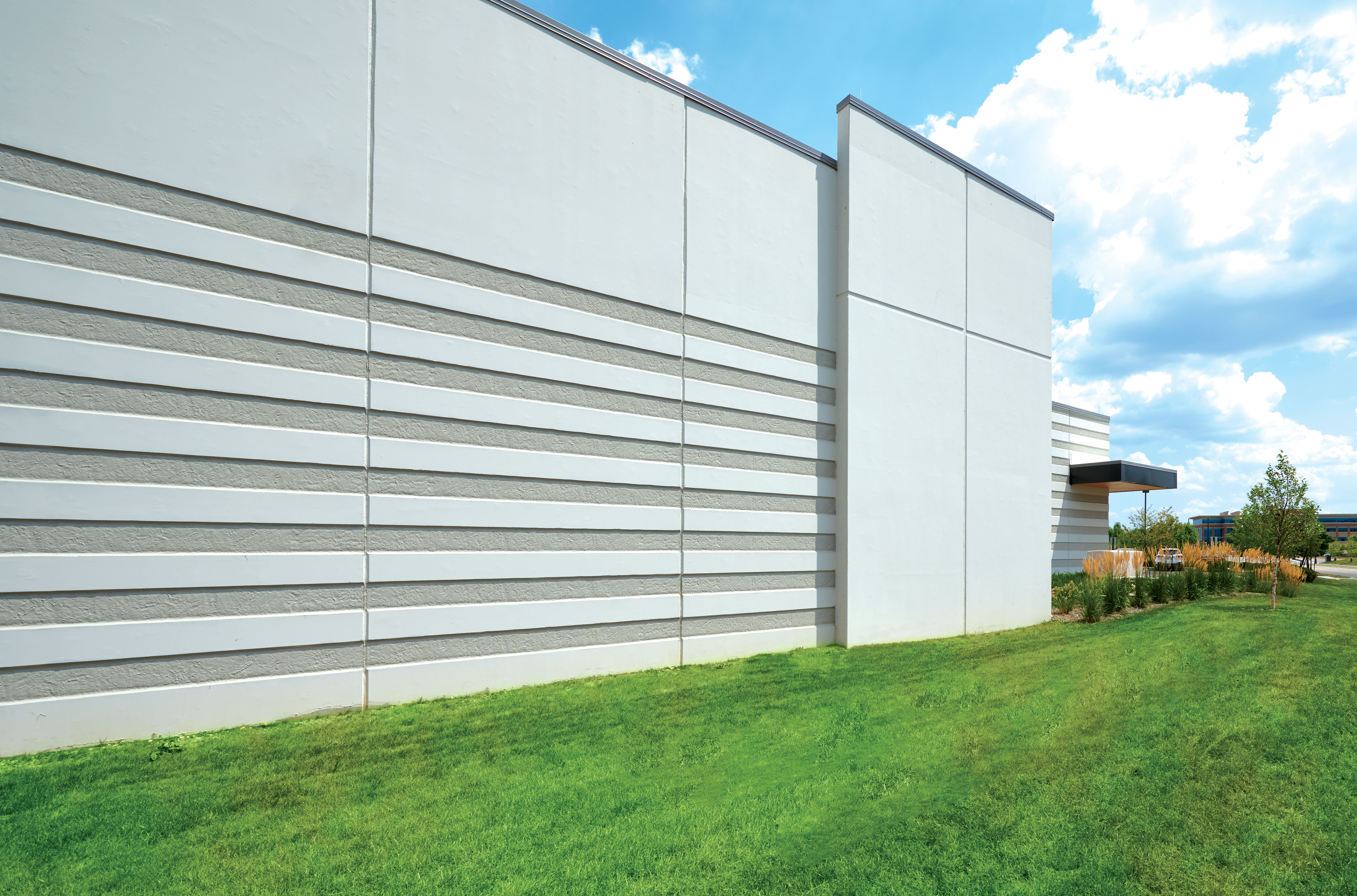
Fabcon has the largest wall panel production capacity of any precaster in the country. [Photo: Courtesy of FabCon]
FABCON BY THE NUMBERS
60
Load-bearing walls up to 60 feet tall
8,000–11,000
PSF resilience
58
Percentage of recycled materials potentially used in the manufacturing of panels
12
The days it takes for Fabcon to enclose a 100,000-square-foot building
20
Possible LEED points
28.2
R-Values as high as R-28.2
4
Panels can be modified for “solid” areas to meet Fire Manual requirements
52
Sound attenuation (STC Sound Transmission Class) rating
Why Precast?
Since the panels are produced at one of Fabcon’s manufacturing facilities and shipped directly to the job site, Smith says the process is less disruptive than other building methods like masonry, which requires you to set the wall block by block, taking up a lot of time, space, and labor.
Smith says other data centers may instead turn to tilt-up construction—a process that involves pouring a slab onsite, letting it cure, then tilting it into place. But that’s not always an option in northern climates near where many of Fabcon’s plants are located (Pennsylvania, Ohio, Minnesota, and Kansas), as you’re often unable to pour during inclement weather. “It’s very messy on many job sites for at least half of the year, but it’s easy for us to set panels year-round,” Smith says. That’s another reason why the Five 9s Data Center project chose Fabcon—construction in winter.
And while you may incur hauling costs to get the panels from, say, Kansas to Texas, you’ll not only save time and labor on the job site, you’ll have higher quality panels, since they were poured in a controlled environment. “There are no weather issues, and we’ve got our quality control professionals at the plant to oversee things,” Smith says. Your site will also encounter minimal disturbance, allowing other trades to move about the site more efficiently.
Resilience & Strength
Fabcon’s precast concrete is stronger than competitors’ because of its unique panel cross-section of solid concrete and prestressed strand—or the cables that run the full length of the panel that give it strength.
Fabcon’s panels can also be load-bearing up to 60 feet tall, while precast panels produced by others only go as high as 40 feet and have to be reinforced with additional steel. And they’re versatile. Fabcon’s wall systems have been used on everything from 5,000-square-foot centers to multi-million-square-foot projects. Fabcon can produce panels that range in width from 24 inches to 13.5 feet wide and depths from 8 to 12 inches. They also offer an extensive variety of finishes—exposed aggregate, integral color, sand-blasted, and acid etch, to name a few.
Airborne debris is often the source of damage to buildings during high winds, but Fabcon’s wall panels are highly resistant to the impact. Fabcon’s panels withstand forces of 8,000 to 11,000 PSF and have been proven to stand strong even after impact from airborne debris in a study conducted by the Wind Science & Engineering Research Center at Texas Tech University. “Providing our customers with the most efficient, technologically advanced and damage-resistant data centers is our point of differentiation, and Fabcon’s precast panels are an important aspect of our success,” says Crosby.
Different buildings often have different security requirements. A bank, for instance, may have a Tier IV security requirement—its walls must withstand everything from high winds to flying debris. Fabcon’s precast panels are made to withstand up to Tier IV load requirements. A few years ago, Fabcon worked on a data center for a major financial institution and went above and beyond to test their durability—shooting 15-pound two-by-fours at 150 miles per hour and 75-pund metal pipes at 75 miles per hour into the panels. “Our panels passed the test with flying colors,” Smith says.
AND SUSTAINABLE, TOO
VersaCore+Green™ wall systems, created by FABCON Precast, meet the criteria for sustainability, giving buildings a higher percentage of recycled-product content, a higher level of energy efficiency, and load bearing wall panels that support equipment loads and protect your data from potential weather or security damage. VersaCore+Green wall panels incorporate up to 58% recycled content, as well as the potential for increased LEED points and tax credits. And because panels are lighter in weight, fewer hauling trips are required, which reduces not only cost, but carbon footprint as well.
- No VOCs
- No food source for mold
- Thermal mass helps to delay and dampen the peak HVAC load
- Locally sourced materials, within 500 miles of plant