Story at a glance:
- Smart technology isn’t just for homes anymore thanks to LG Electronics’ VRF technology and new system of controls.
- Conversations around sustainable HVAC are taking place earlier in green design decisions—and for good reason.
Pretend for a moment that the technology you rely on throughout the day had resisted innovation for the past half-century. Your cell phone would be a blocky device that only placed calls. Your computer (a desktop) would connect to the internet at plodding dial-up speeds. Your TV—those microwave-like boxes—would display fuzzy, muted images.
Yet for another everyday technology—HVAC—you wouldn’t need to do much pretending. In many cases, old-school machinery remains the standard for how we heat and cool our homes and buildings in the United States.
“A lot of people don’t think about AC unless it’s malfunctioning,” says Patrick Barry, LG’s US senior manager of air conditioning product development. “The U.S. has an established system, and people choose what they’re familiar with.” This norm of conventional, unitary central air-conditioning involves pushing cold air through leaky ductwork to cool or heat distant rooms, often resulting in an inefficient system that fails to deliver comfort.
LG Electronics is trying to disrupt this status quo, and to shift the perception of HVAC from “afterthought” to “smart, sustainable design choice.” They’re doing this by placing people at the center of their technology—striving to make their “life’s good” motto a reality.
“LG products are designed to enrich the lives of those who use them,” says Kevin McNamara, senior vice president and general manager of air conditioning technologies for LG Electronics USA. “That’s especially true in LG air conditioning technologies. Our focus is to work to fundamentally change the way the US heats and cools buildings, and in doing so increase comfort and efficiency for those who use our products.” This includes property developers, contractors, building owners, and occupants—all the players who not only design, but also live and work in, today’s buildings.
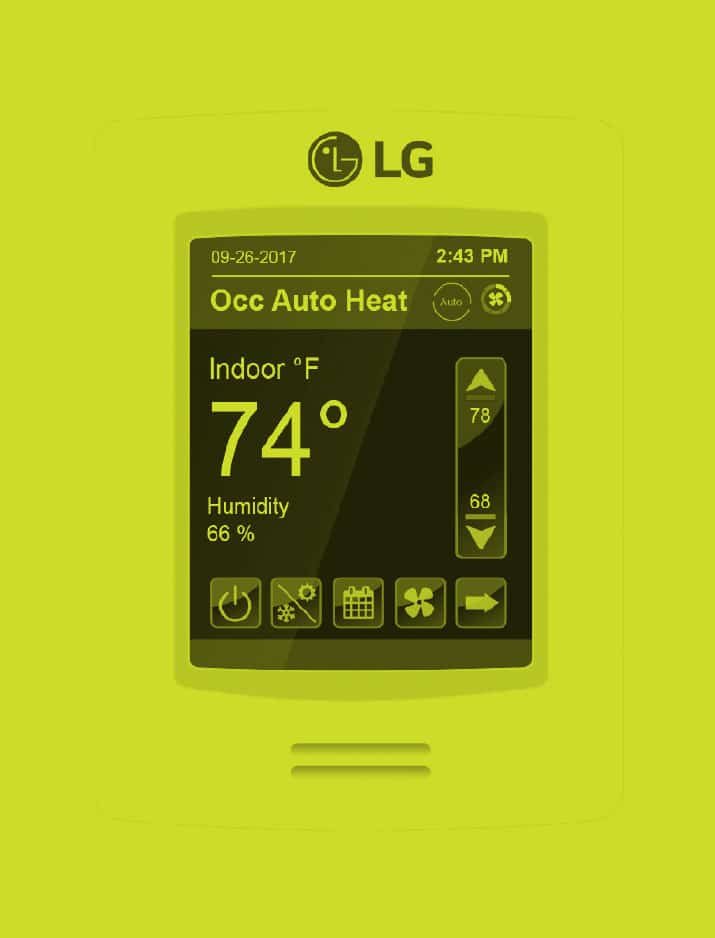
LG ELectronics’ new VRF controls are sleeker, smarter, and more efficient. Illustration courtesy of LG
Go with the Flow
Pushing toward this industry change, the company’s air conditioning technologies division specializes in VRF, or variable refrigerant flow systems. As the name implies, these systems offer varied and zoned rates of heating and cooling throughout a building. Rather than running according to on/off mode or maintaining one temperature for an entire building, VRF can heat or cool spaces at different rates and temps. Think of it in terms of a hotel during winter: The lobby can be heated comfortably for guests, while the hotel kitchen stays cool for chefs. This ability to tailor the temperature to the use of a specific room leads to energy savings.
VRF also saves energy through the so-obvious-it’s-brilliant concept of “heat recovery.” Rather than dumping the heat drawn from rooms being cooled to the outside, the heat is recycled by transferring to rooms needing to be warmed, or even to other systems that need heat like water systems or swimming pools. Further energy is saved by using the heat-transfer medium of refrigerant rather than air. Flowing through a network of narrow insulated pipes, this fluid controls temperature on the spot. “It heats or cools air right where it’s needed,” Barry says. “It’s directly analogous to a tankless water heater.”
These systems are designed to react. and now the owners can see that data, too.
Used throughout Asia and Europe since the 1980s and arriving in the U.S. in the early 2000s, VRF can reduce energy use by around 55% over its conventional counterparts. It also delivers design flexibility to architects and project engineers. Those narrow pipes (around one inch in diameter) and reduced or eliminated ductwork can be easily retrofitted to older buildings and help conserve space in new projects. What’s more, the condensing units require less space and run quietly, a plus for hotels and resorts where utility equipment often sits next to pools and patios.
Industry Firsts
Lately LG has been doubling down on innovation. Earlier this year at the AHR (Air-Conditioning, Heating, Refrigerating) Expo in Las Vegas, the company debuted the smallest footprint, largest capacity single frame VRF model on the market, the 20-ton Multi V 5, designed for commercial applications, and—perhaps most head-turning—a suite of smart building controls.
These controls systems are called LG MultiSITE, and they bring the ease of smart-home thermostats to the complexity of large, multi-purpose buildings such as condominiums, schools, and offices. They not only manage VRF, as did LG’s previous generation of controls, but also sync with the entire building to regulate systems like electricity, lighting, and water. (Good news, mechanical contractors: You no longer need to coordinate multiple controls systems.) “For the first time ever, designers can implement VRF technology directly into an existing BMS through an intuitive platform,” McNamara says. “This is a huge shift in the way VRF technology has been incorporated into building management systems.”
Like most good ideas, MultiSITE was inspired by lots of conversation, listening, analysis, and optimism. “Our engineers and product team talked to everyone from contractors to engineers and owners about what they wanted to do with their buildings,” McNamara says. “Buildings get used in a lot of different ways. So the key concepts that came up were flexibility and customization.”
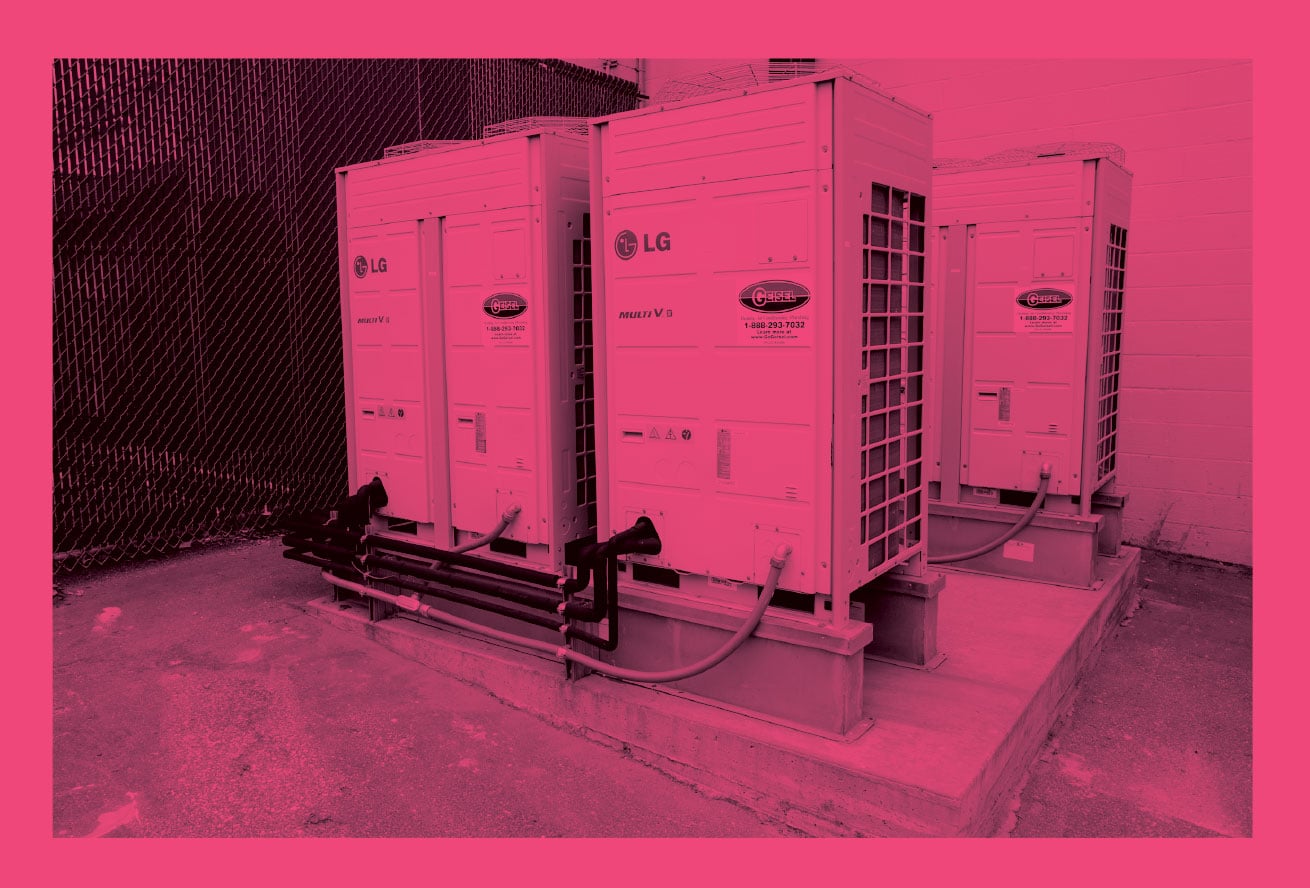
Photo courtesy of LG
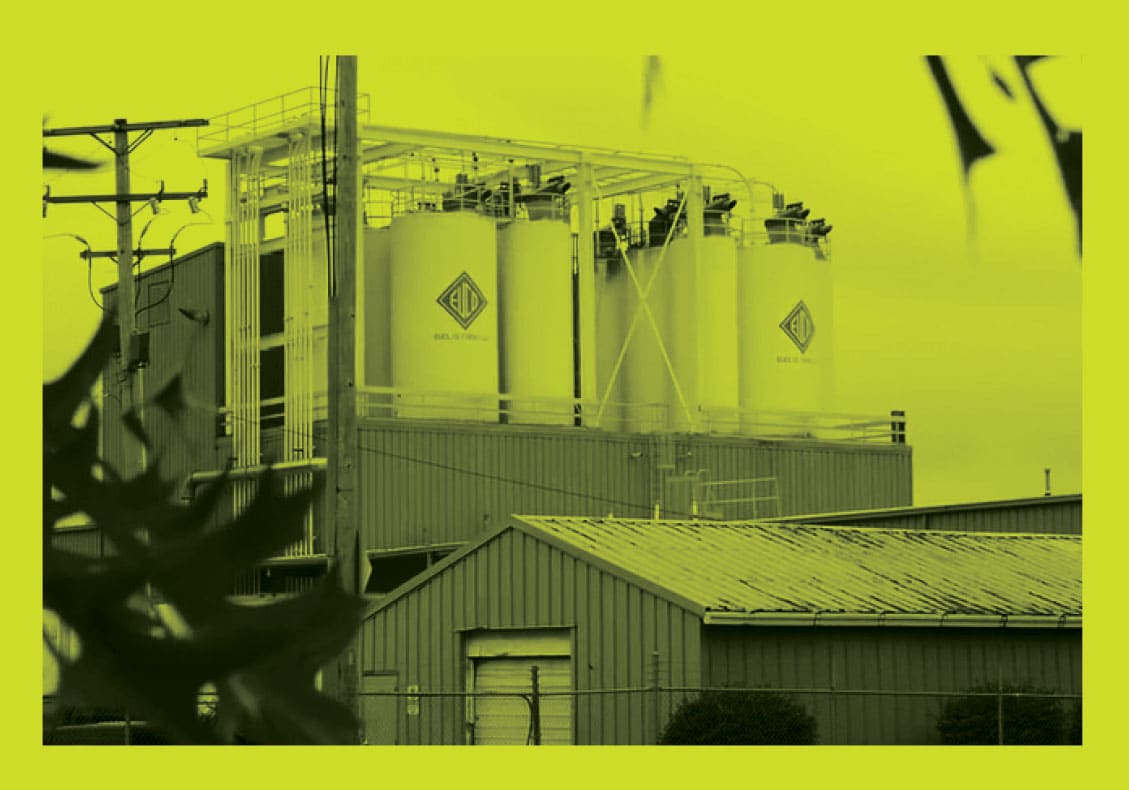
LG completed a retrofit installation at Euclid Chemical Company that resulted in significant savings. Photo courtesy of LG
User-Friendly Flexibility
With these smart controls, property managers own the building rather than the building owning them. And that starts with centralizing everything they need to know in order to monitor the space. “People want to be able to manage their building from a single point,” says James Benville, senior manager of national sales for air conditioning technologies at LG Electronics USA. LG MultiSITE does this by giving people the option to view the control display via an in-building touch-screen panel, a remote control, and/or their tablet, smartphone, or computer.
The display itself received a user-friendly makeover, too. “VRF used to have a European/Asian style control interface,” Benville says. While the look and feel of that design may have worked well for overseas audiences, it wasn’t intuitive to American users. “With these new controls, you still have the same logic and functionality behind the scenes, but the interface is U.S.-friendly, with customizable displays and colors,” he says. “You don’t have to train people to use it.”
The whole setup is also easier to integrate. Previously, control systems were designed by technicians and required a third-party gateway to connect all the parts. Now, with a little training, system integrators can easily incorporate the systems themselves. If a maintenance issue arises, owners simply run diagnostics within the system, then click to send a report to a local service rep if necessary.
Data-Driven Design
Behind the scenes of this front-end flexibility is data-centric engineering. To actually gauge a building’s performance, LG MultiSITE compiles data from sensors within the outdoor unit and throughout the space on humidity, temperature, and occupancy. Based on these readings, the system manages energy use throughout the day, downshifting use during the evening, for example, or when spaces are vacant. In turn, working with the patterns they see, owners can fine-tune how they want the system to respond.
“These systems are designed to react,” Barry says. “And now the owners can see that data, too. They can say, ‘I’m going to manipulate the system to work a little differently.’ It’s just another point of feedback.”
Further, owners can choose which features they want to be displayed, and how much they want to interact with the system. Barry calls this “flexibility to match the application,” which is a technical way of saying “design that fits the setting.”
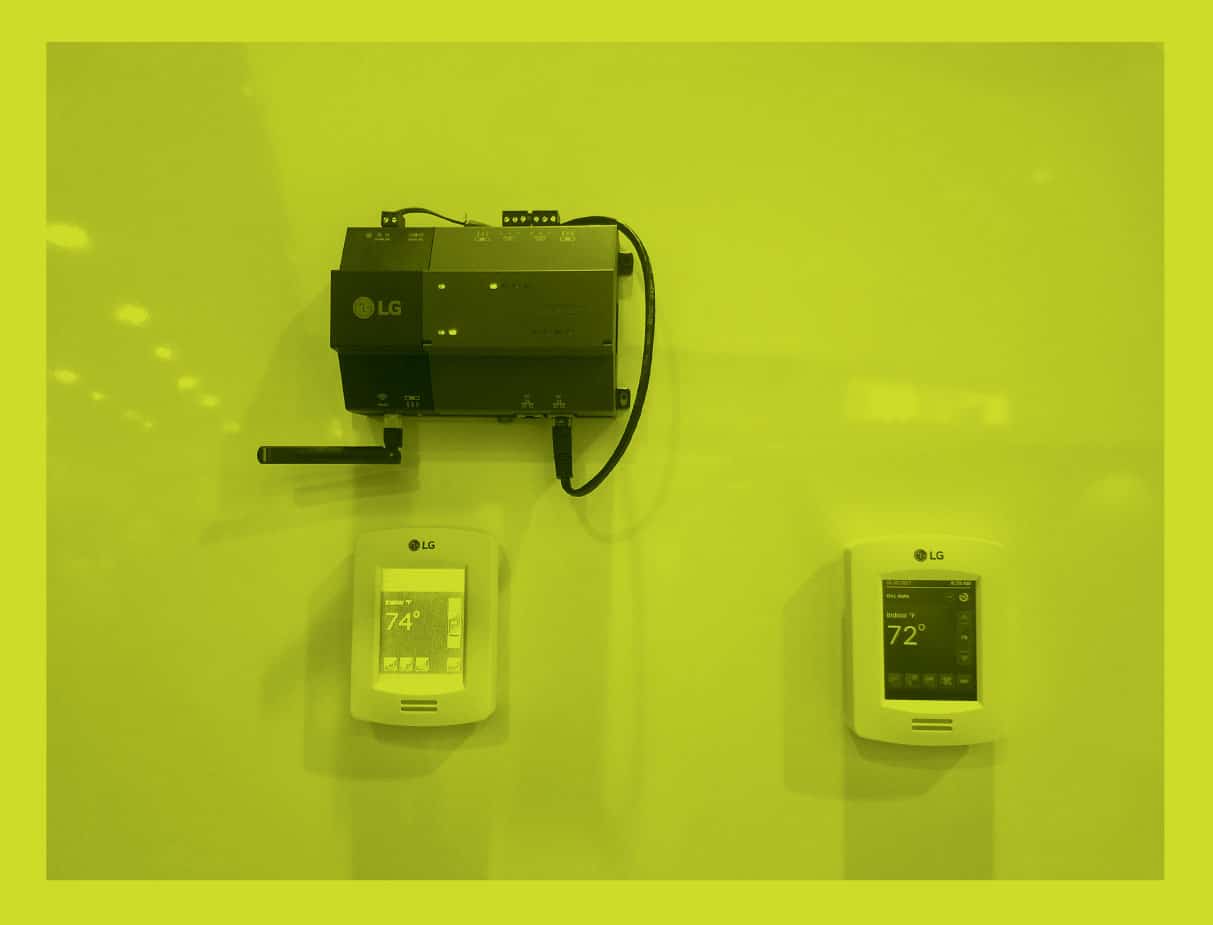
LG recently debuted its Multisite system, with the smallest footprint, largest capacity single frame VRF model on the market. Photo courtesy of LG
The end goal? “You’re making the building work together as a whole so it’s optimized,” he says, adding that it’s a win-win for owners and occupants. The system pays for itself in energy savings (happy owners) and people working or living in a multi-use building can choose how they want their spaces to feel (happy occupants).
A Smarter Future
With all of this latest technology now reaching the market, LG Electronics plans to keep right on innovating. From here, they plan to further “improve and balance” their current VRF models, Barry says, to explore creative ways to redistribute and reuse heat within a building. They also plan to focus on home automation and greater connectivity to the Internet of Things (IoT).
This is all part of intelligent design, whereby technology intuitively works to make life better for humans and the environment. “Buildings will continue to get smarter,” McNamara says, adding that he believes this starts with HVAC, one of a building’s largest systems. And as this more intelligent future arrives, maybe today’s inefficient systems will become one of those outdated memories.
VRF in Context
A retrofit installation within the Euclid Chemical Company, a construction-products supplier in Cleveland:
- A new LG VRF system replaced an old Variable Air Volume system that incurred hefty above-national average utility costs
- The old system kept running while the new one was being installed
- Existing ductwork was reused where possible to cut costs
- The building, which features a diverse group of rooms, can now be controlled on a space-by-space basis
- Heat taken from one room can be used to cool another
- Two years later, utility savings equal around 70% over the previous model