HOLDRITE’s HydroFlame firestop solutions keep water, smoke, and flames from spreading—and they’re easier to install and more cost effective than other methods.
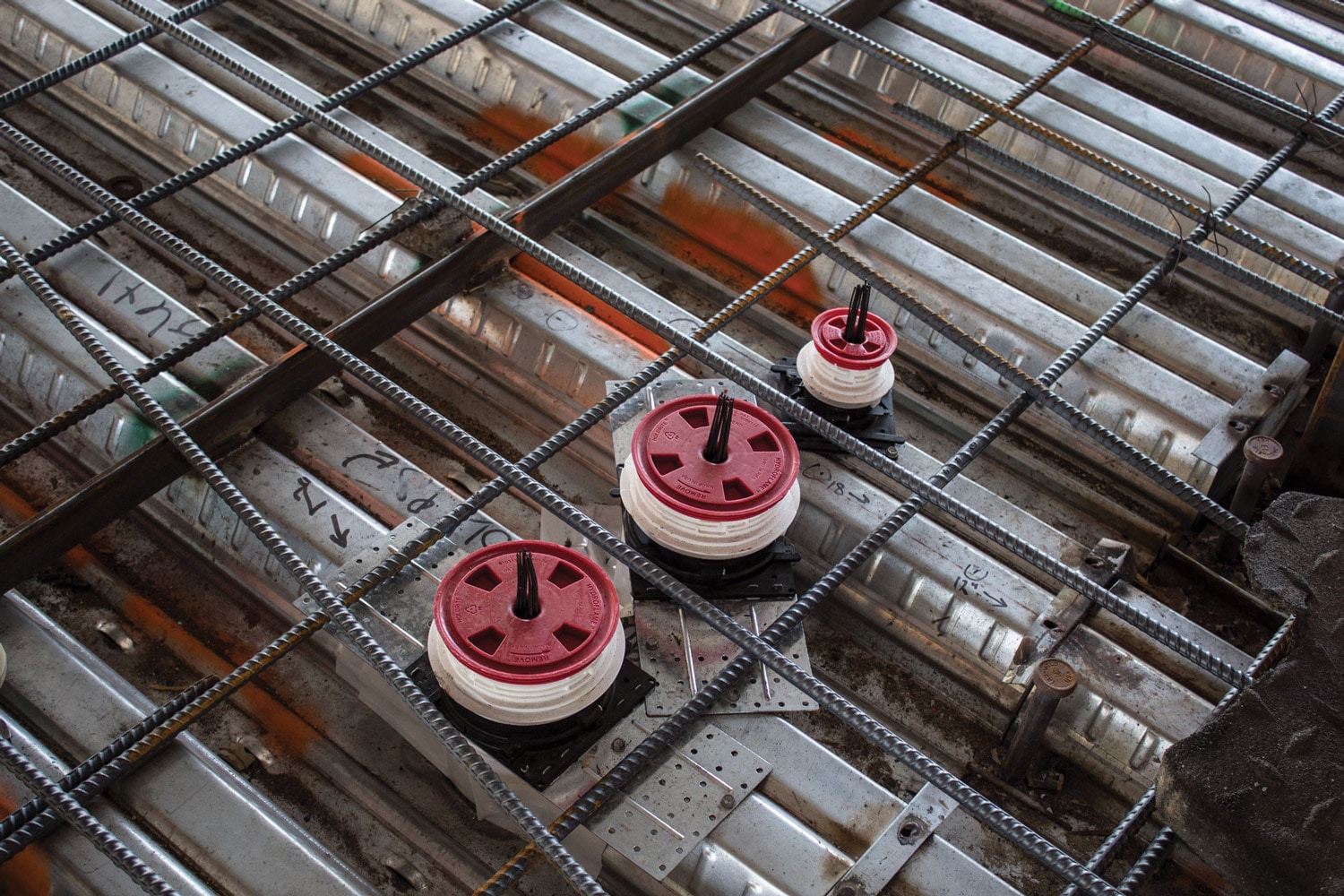
HydroFlame’s telescoping sleeves are secured to the form decking before the concrete is poured. [Photo: Courtesy of Reliance Worldwide Corp.]
When you think of fire protection, devices like smoke detectors and sprinklers come to mind. These products are, of course, essential to alerting inhabitants and combating the flames when a fire breaks out, but they’re only part of the solution. Another critical component is passive fire protection. Unlike smoke detectors, which alert people to a blaze, or sprinklers (active fire protection), which put out the flames, fire stopping (passive fire protection) solutions work behind the scenes.
“It doesn’t put the fire out, but it stops fire, smoke, and poisonous gases from moving to other areas of the building,” says Chip O’Neil, vice president of business development at Reliance Worldwide Corporation (RWC).
Last year, RWC acquired HOLDRITE, which has been developing solutions for commercial and residential construction since 1982. HOLDRITE is an industry leader in creating passive firestops for plumbing and mechanical contractors.
How Firestopping Works
So how do these solutions fit into the construction of a building? O’Neil explains it like this: A building is often divided into multiple fire-rated compartments created by fire-rated assemblies like walls and floors. These rated assemblies are designed to prevent a fire from spreading from one area of a building to another for a set amount of time depending on their “F” rating. However, during construction, those assemblies will be impacted by all the various trades involved in the process: pipes and electrical conduits will penetrate them, and so on. It’s up to those trades to return that assembly to its original fire rating, essentially by filling in the gaps, or “annular spaces.”
For years, those gaps were filled using ad hoc formulations of mineral wool and caulking, O’Neil says. These were accomplished on the job site by subcontractors with varying degrees of expertise in passive fire protection. Today, those makeshift solutions are no longer the only answer. HOLDRITE’s HydroFlame Pro series is a streamlined solution that transforms firestopping. HydroFlame’s telescoping sleeves are secured to the form decking before concrete is poured. Because it’s a telescoping design, the same sleeve can be adjusted to accommodate a variety of depths of concrete without any kind of field modification, O’Neil says.
Within the sleeve is a pliable membrane that can stretch to meet various sizes. This means once the plumbing or cabling is inserted through the sleeve, the pliable membrane will create a waterproof seal. The sleeves also contain a cap and locator whisker to streamline the process of installing pipes or utilities after the concrete has dried. Because the whiskers stick up out of the concrete floor, it’s easier for contractors to find them when it’s time to run the pipe or cable. Then the safety cap and whisker can be easily removed.
FROM OUR MAY+JUNE 2018 ISSUE
The preferred publication of leading green professionals.
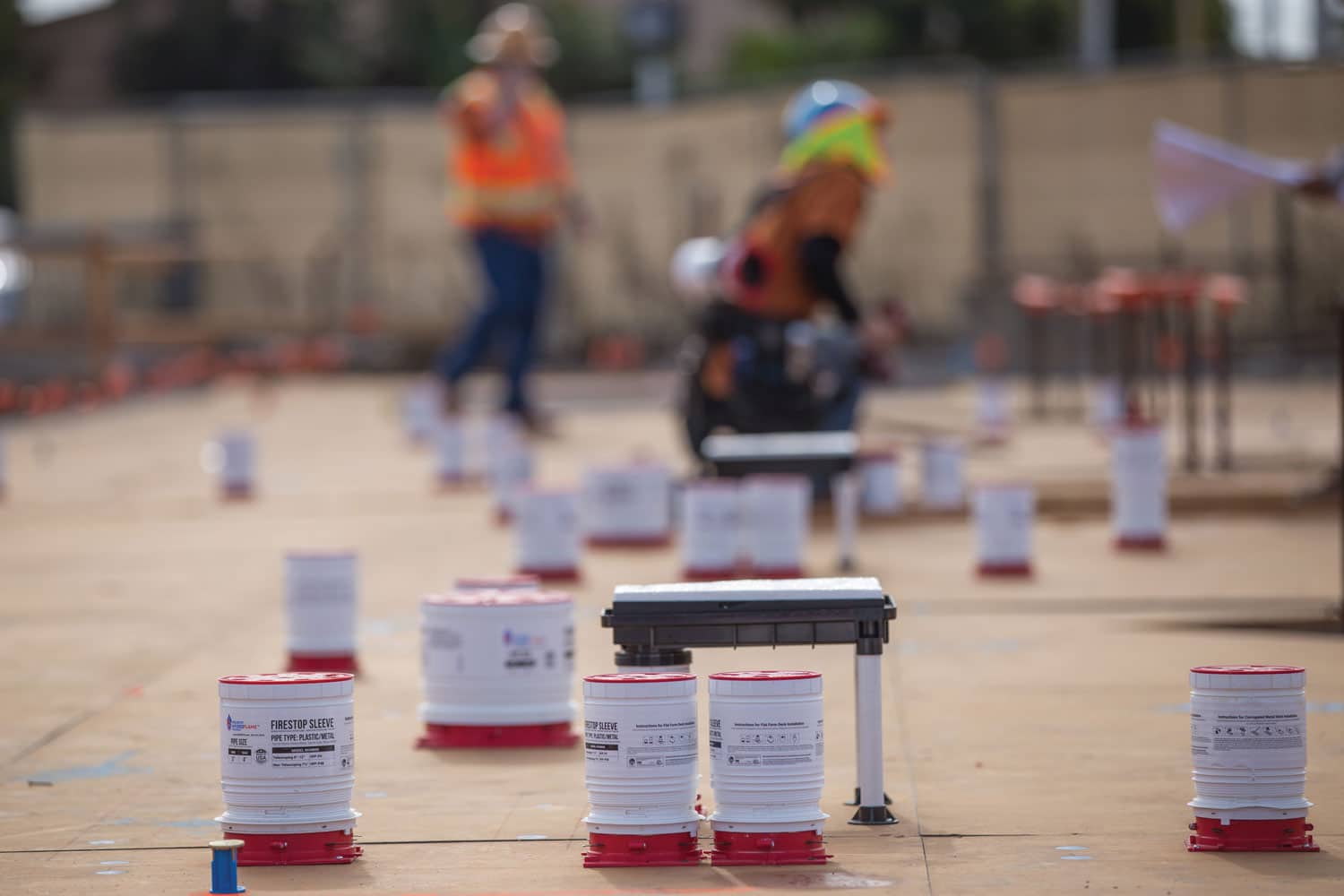
[Photo: Courtesy of Reliance Worldwide Corp.]
Transforming Firestop Solutions with Engineered Devices
Why have building professionals turned to these kind of engineered solutions in recent years? “Codes and standards have become significantly more important in building construction,” says Tim McConnell, senior vice president of business innovation at RWC. Engineered firestops are easier to inspect and ensure consistent installation and inspection across an entire project.
“Products used to install firestop systems have to be rigorously tested in a third-party lab to prove the products can do what they claim to do. Once tested and proven to be able to achieve the fire rating for the prescribed amount of time, they receive a UL or similar listing,” O’Neil says.
McConnell notes that third-party-certified products have been key to meeting increasingly stringent code requirements. “As systems have been developed, the inspector and contractor community often prefer a proven system to a makeshift method,” he says.
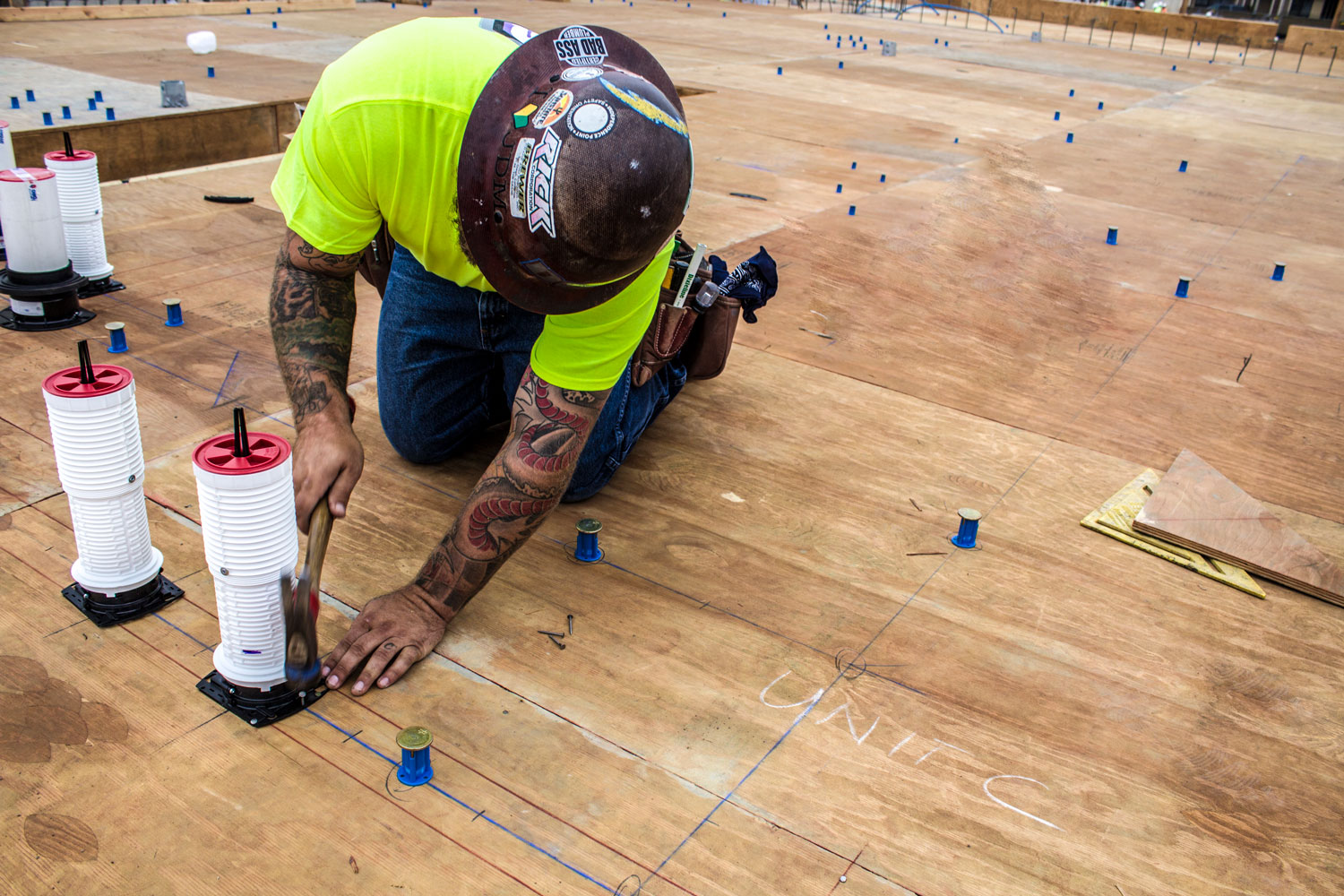
HOLDRITE’s HydroFlame Pro series makes firestopping a much simpler—and more cost-effective—process. [Photo: Courtesy of Reliance Worldwide Corp.]
Cost Savings & Added Value
For developers and contractors, cost is always a major part of any decision. That’s another area where an all-in-one solution has an advantage—though it may not be immediately apparent, O’Neil says as an example. A typical sleeve will cost just $3, compared to the $9 or $10 it might cost to buy a HOLDRITE solution in a comparable size, he says.
However, that $3 hollow sleeve doesn’t account for all the time it will take to apply the caulking and other materials to secure that sleeve. “When all of the labor and material is added up, the installation can actually result in $30 or more per penetration, even though the basic hollow sleeve started at just $3,” O’Neil says. Because a HydroFlame Pro sleeve is so simple to install, labor only adds a few additional dollars—making for a total installed cost less than half that of a manual one.
“One of our goals is to create added value for the contractor and developer,” McConnell says. “You’re getting a better solution without necessarily adding additional costs to the building because of the installed cost savings.”
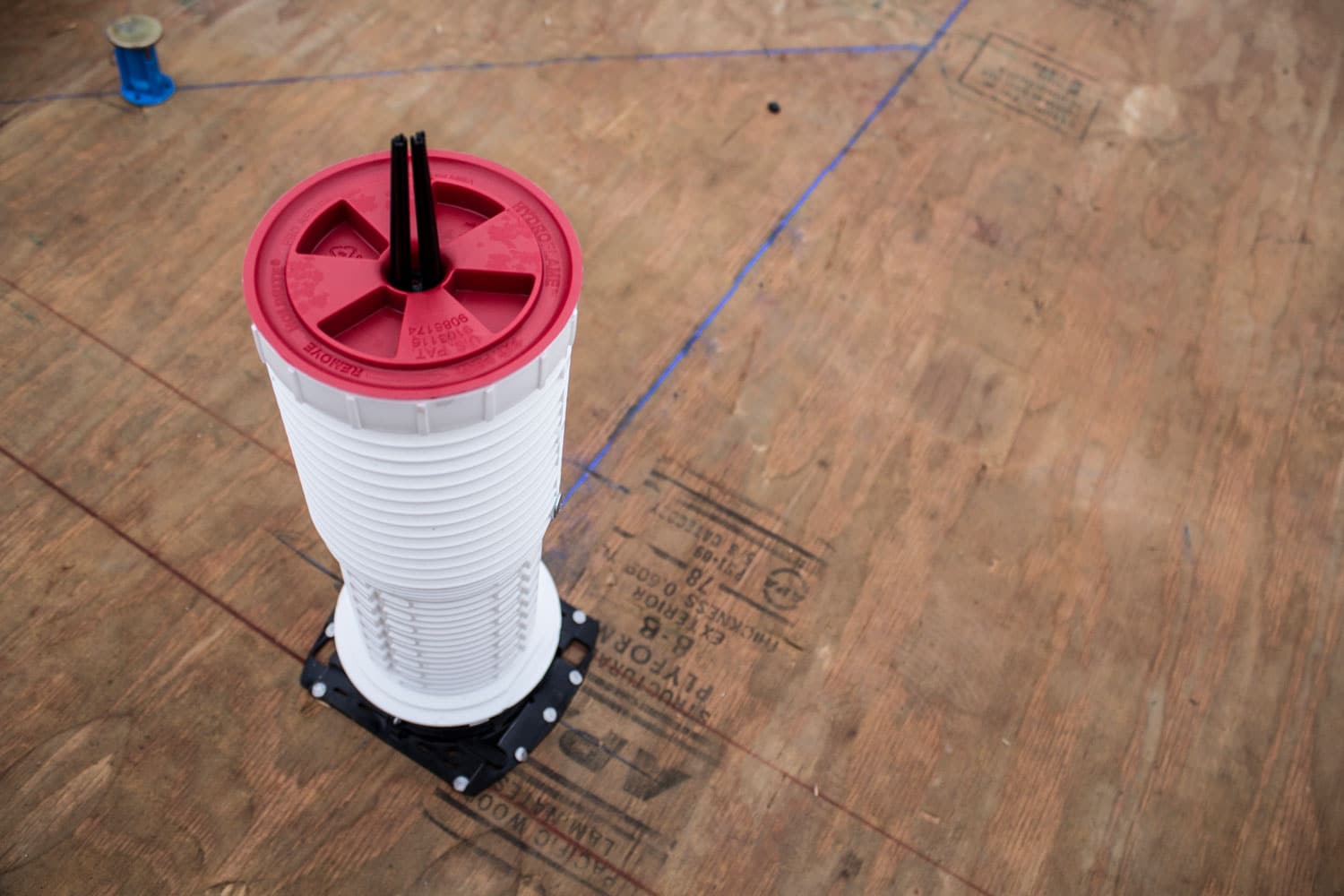
[Photo: Courtesy of Reliance Worldwide Corp.]
4 Green Benefits of HydroFlame Pro
1. HVAC efficiency
Because the sleeves create airtight floor penetrations, there’s very little heat or cooling lost through pipe cable and conduit penetrations.
2. Water savings
Using a core drilling machine to create pathways for utility lines in a building can use a large amount of water. An engineered sleeving system eliminates the need for that drilling.
3. Reduced construction waste
A field-applied firestop system requires multiple components, each of which requires packaging material. In addition, the demolition of temporary sleeves creates extra waste on site. A streamlined solution, which doesn’t generate any scrap materials, eliminates these materials from going into a landfill.
4. Improved air quality
Manual firestopping often requires harsh chemicals, and the process of cutting mineral wool can release contaminants into the air. HydroFlame Pro products, on the other hand, are made out of low-VOC materials. Eliminating the need to core drill or demo a sleeve out of a concrete floor prevents silica dust from being released into the air.