GreenStaxx is revolutionizing modular housing with pre-designed, building block units.
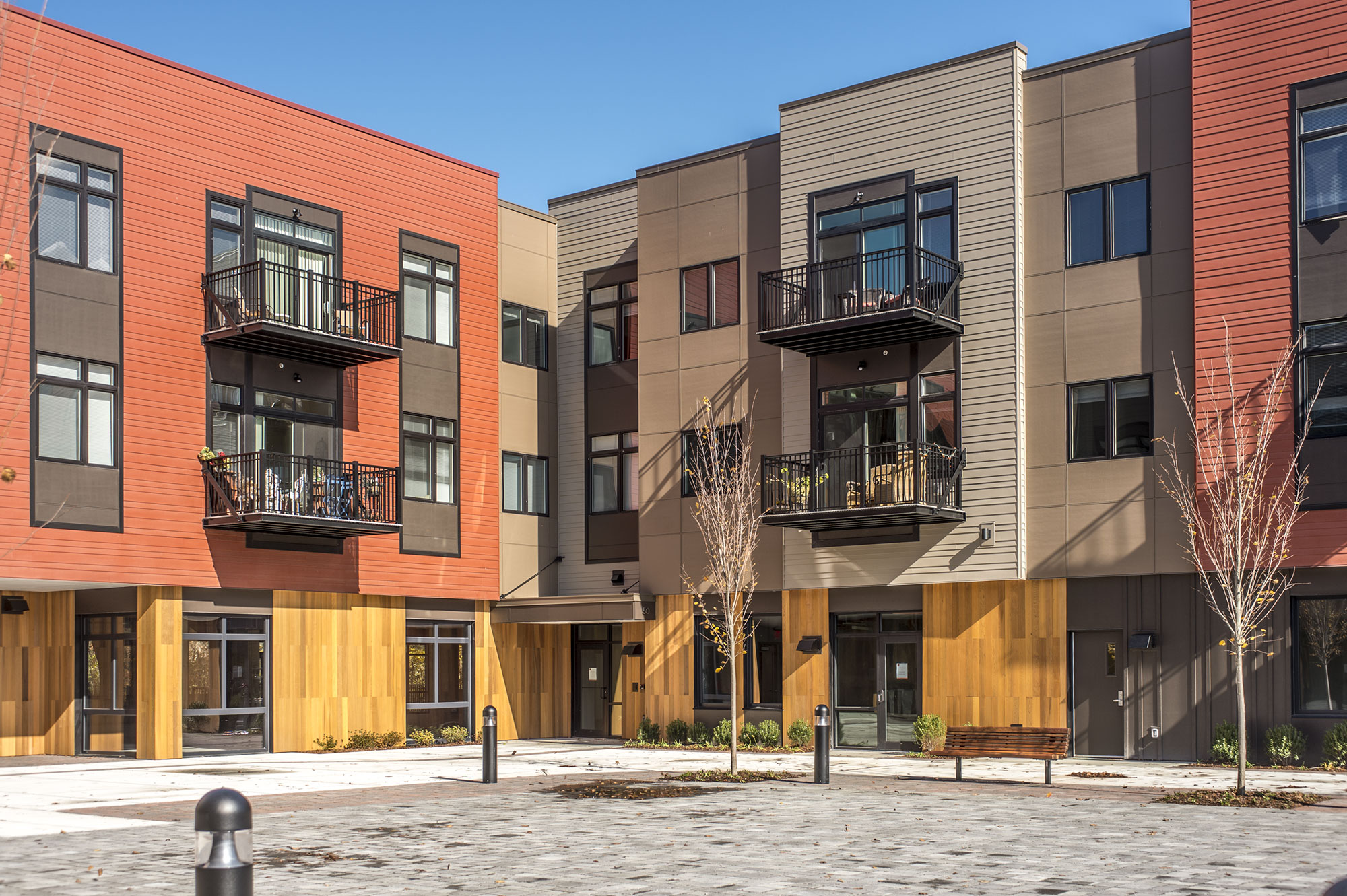
You don’t have to sacrifice aesthetics or customization with modular. GreenStaxx provides plentiful possibilities that are beautiful, too. [Photo: Courtesy of GreenStaxx]
For more than 30 years, Arthur Klipfel and Gwen Noyes have been working to provide better sustainable urban housing at an affordable cost.
The married couple has decades of experience in the world of building and design. Klipfel is the founder and president of Oaktree Development LLC, a design-based development company originally founded as Unihab, Inc. in 1969. Noyes has been a partner of Oaktree since 1973.
While designing multi-family residential projects with Oaktree, Klipfel realized most residential properties are made of units, like building blocks, that remain consistent from building to building—outside corners, inside corners, and corridor units. He envisioned an efficient system of constructing and designing buildings with these repeated “stacks.” His groundbreaking idea became the foundation for his affiliated development and design company, GreenStaxx.
Innovative Technology
Klipfel and Noyes founded GreenStaxx to address the challenges of multi-family modular building. Klipfel designed and patented the GSX system, which includes a computer interface of stackable units, or boxes, that fit together like Legos on a grid. These pre-designed, pre-engineered blocks help streamline the building and design process, saving big on energy, time, and money.
FROM OUR JANUARY+FEBRUARY 2018 ISSUE
The preferred publication of leading green professionals.
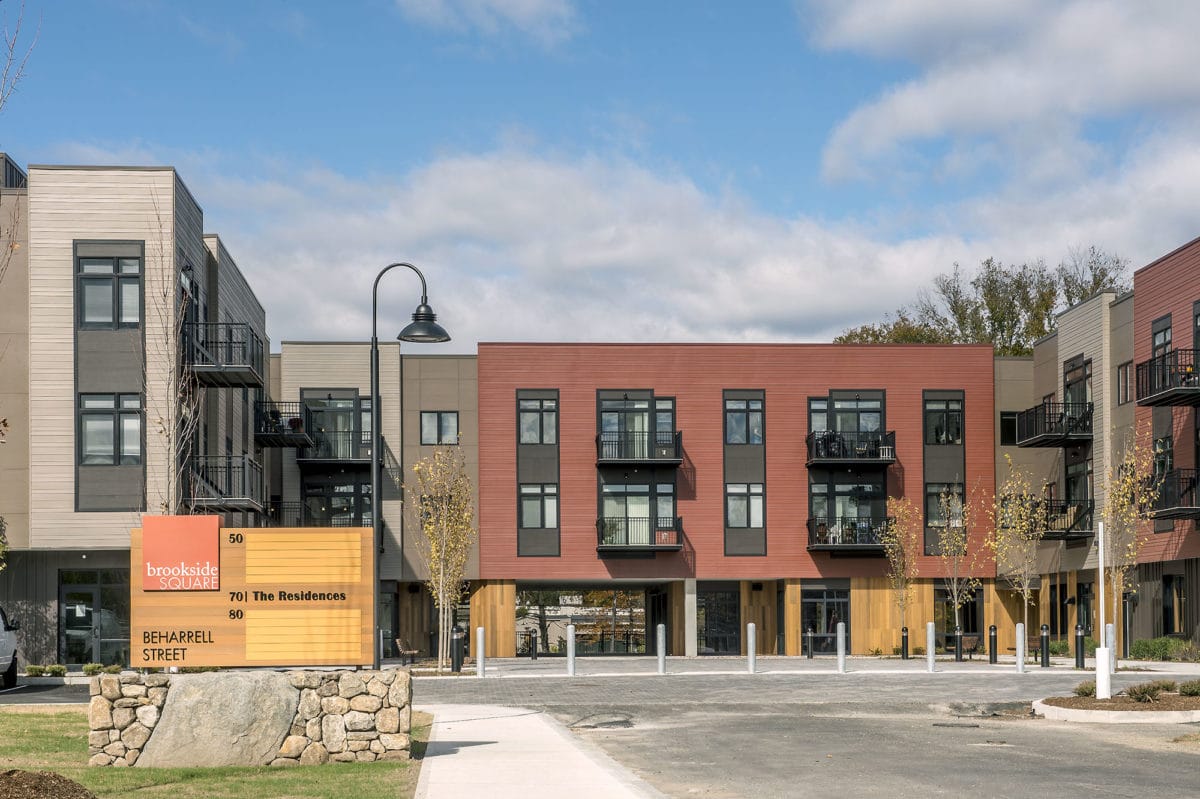
[Photo: Courtesy of GreenStaxx]
The flexibility of pre-designed stackable blocks and the power and data organization of BIM (Revit) make GreenStaxx a technological and engineering powerhouse. With GreenStaxx, it’s as simple as “drag and drop”—the architect chooses the appropriate unit and places it into the graphic interface, which virtually models and assembles the project in 3D on a site-specific grid.
When a project begins, the GreenStaxx team creates a grid that is sized to fit the blocks and customized to suit the local conditions and zoning requirements. The minimum double loaded corridor project uses about 12 unit stacks picked from available alternatives, but the system’s library also includes triple deckers and duplex townhouses. The company’s current largest design project, Cambridge Park Place, is 312 units.
The library of more than 25 unit types sets GreenStaxx apart from other modular building solutions. Their collection includes many configurations—one, two, and three-bedroom units, elevators, stairs, and more. This allows the team to quickly and easily design, evaluate, and construct high-quality multi-family residences.
Noyes and Klipfel say modular is the way to go in terms of speed, flexibility, and sustainability. However, you can use GreenStaxx’s technology even if you don’t want to build modular. “There’s a whole level of design time efficiency that’s achieved even if our clients don’t end up using prefabrication,” Noyes says.
When appropriate, the library of units can work with conventional building projects. “GreenStaxx does both conventional and modular building because modular building has tighter criteria. Not every part of the country has the right facilities to make modular possible,” Klipfel says. Whether clients choose modular or conventional practices, they still reap the benefits of GreenStaxx’s technology. All of the stacks are sustainably engineered, highly vetted, and market tested. Completely customizable, GreenStaxx’s technology allows for creative freedom, and beauty, in modular building.
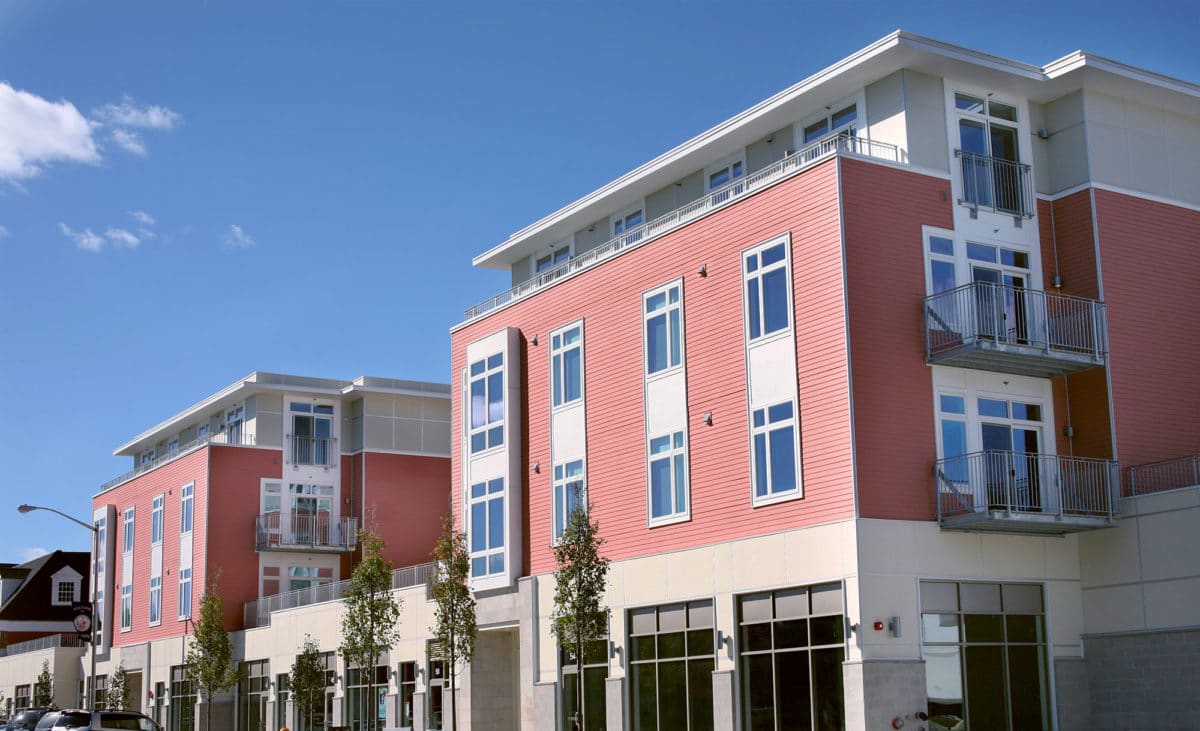
You don’t have to sacrifice aesthetics or customization with modular. GreenStaxx provides plentiful possibilities that are beautiful, too. [Photo: Courtesy of GreenStaxx]
Debunking Modular Misconceptions
“Not all modular projects have to look like chicken coops,” Noyes says. “A lot of people think because you’re going modular you just have a big rectangle, but really you can do whatever your creativity allows.”
Modular can be beautiful, and with GreenStaxx, it is. Countless customizable options—from patios or balconies to the color of the walls—are available with modular construction. “We offer the library of multiple stacks to the developer, and they can then customize based on their needs and budget,” Klipfel says.
Currently, GreenStaxx technology can build five stories in wood constructed over a one or two-floor steel podium, which allows for seven stories total. GreenStaxx is also considering implementing a light gauge steel system, which would extend a project’s maximum height to 18 stories. The triple-decker infill design is geared for urban affordability.
“If a process like GreenStaxx gets legs, which I think it will, it could make modular construction process that much more flexible and easier to build,” says Josef Rettman, NEI contractor and managing director and a local partner on GreenStaxx’s 28 Austin Street project in Massachusetts.
Like Noyes and Klipfel, Rettman isn’t new to the modular building field. His team has completed several modular housing projects in Chelsea. He knows firsthand that you don’t have to compromise aesthetics and customization with modular. “With GreenStaxx, you can pretty much design whatever you want. When you relocate and move the boxes, you can create overhangs, sunscreens, and so much more,” Rettman says. “And as long as it is coordinated properly, you can build the project three to four months faster than a conventionally built project.”
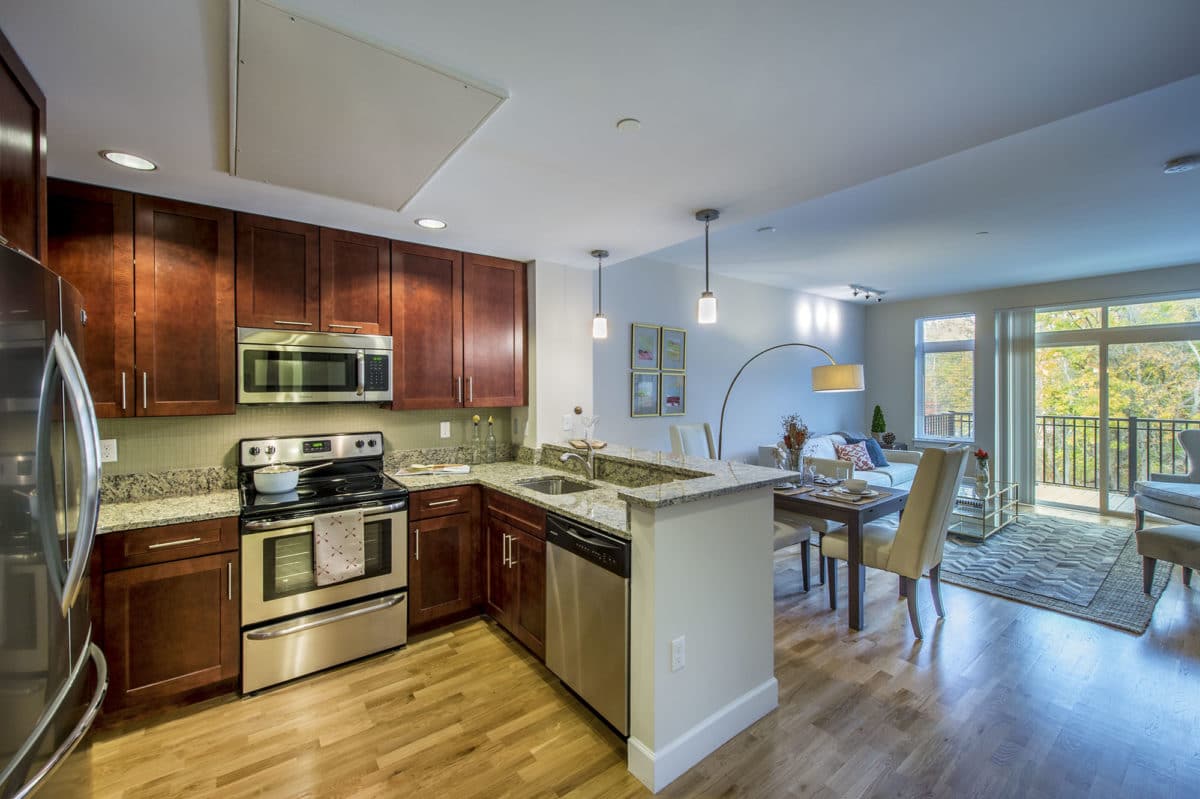
[Photos: Courtesy of GreenStaxx]
Streamlined Coordination
Before GreenStaxx developed its system, multi-family modular construction often suffered from communication issues between offsite and onsite contractors. The GreenStaxx system streamlines coordination between the architect, general contractor, and modular manufacturer. “Each community has its own codes or a certain look to its buildings,” Noyes says. “Working with locals is a better way of fitting a building into a community. And often, certain contractors and architects have already worked together before, so they have a strong sense of camaraderie.”
Teamwork and local expertise make all the difference when dealing with complicated approval processes. “When you’re dealing with an out-of-state modular manufacturer, their engineers are all licensed in the state in which they’re building modulars,” Klipfel says. “But the architect’s drawings must be approved in the state and city where you are building your project.”
This drawing approval process can take as many as 180 days. GreenStaxx solves this problem by giving the architect pre-approved tools they can work with ahead of time—the library of stackable units. This eliminates the time-consuming back and forth between the developer, the local architect, and the out-of-state modular manufacturer. The team follows the unit library protocols, and GreenStaxx provides support and coordination along the way. “We’ve heard many of the horror stories about pre-fab projects. But we work on taking the guesswork out of it,” Noyes says.
The ‘Green’ in GreenStaxx
Klipfel and Noyes are always looking for ways to make GreenStaxx greener, too. “About 20 years ago, Gwen and I said, we want to be green developers. And we were thinking, how do we get green to stick? How do we get developers not to veto it?” Klipfel says. That came down to marketability and educating developers. GreenStaxx is particularly marketable because it’s practical, less wasteful, and less expensive, and the green is “baked in.”
Every GreenStaxx structure is built in a factory, so you can control the temperature for finishes, which means less wood shrinkage. Factories also produce much less waste than traditional construction sites. Thanks to the repetition in the unit manufacturing process, no materials are ordered in excess. “The cost saving is a huge benefit if it’s done right,” Klipfel says. “The know-how goes from one building to the next building, cutting out all of that design time it usually takes.” Greenstaxx clients can reduce their total project costs by 10 to 15%, and reduce timeframes by up to 30%, all while improving the overall building quality.
Rettman says GreenStaxx’s commitment to green is clear. “They’re figuring out how to do modular passive houses, which would break a barrier in the future of energy efficiency. They have the skills to do it and they’re close to their goal—it could be a major breakthrough in modular design.”
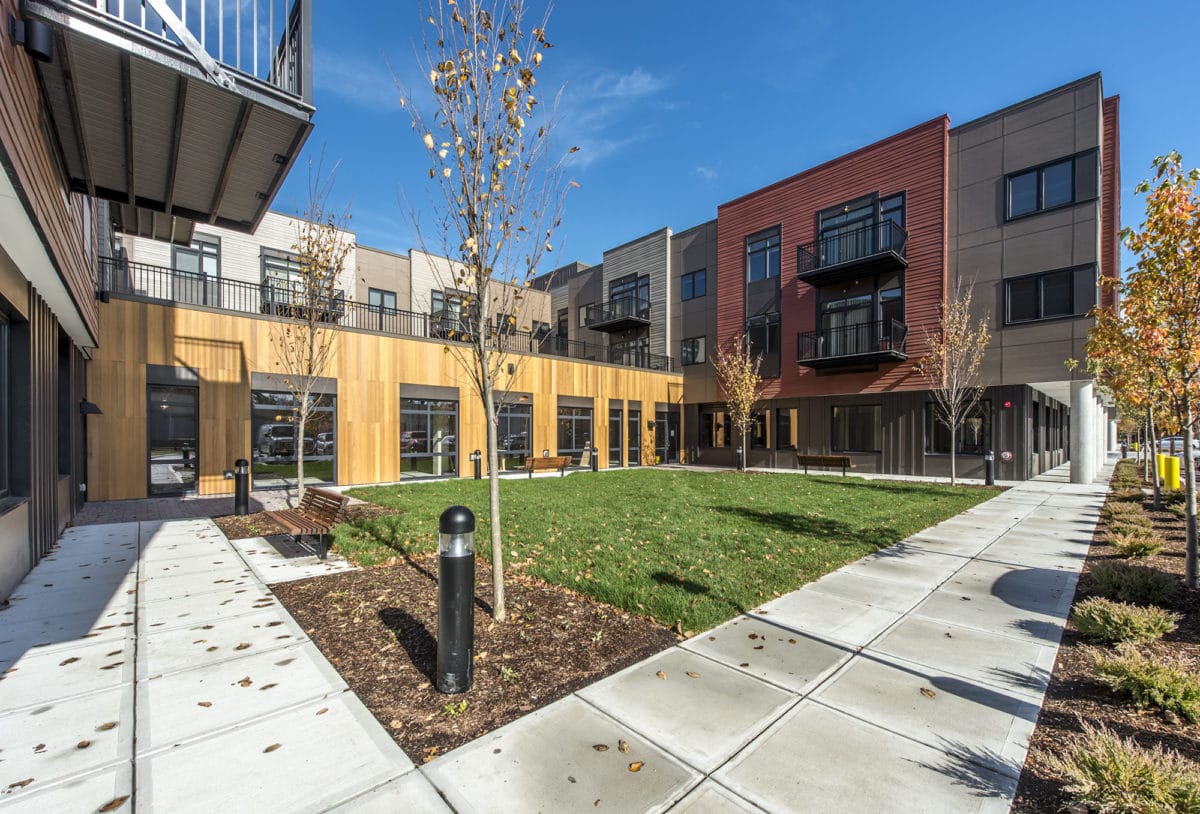
[Photo: Courtesy of GreenStaxx]
Looking Ahead
The future is full of exciting R&D—from creating alternative unit libraries for different climates to expanding the company’s interior design options. By partnering with consulting firms for continued research, GreenStaxx hopes to get ahead and improve their technologies and services.
For example, GreenStaxx is partnering with Mike Browne of Advanced Building Analysis, who focuses on building analytics and measuring energy use and ratings. Their work could help developers receive sustainability-based rebates and incentives. Stantec is also working to make GreenStaxx’s unit library particularly contemporary at the Newton, Massachusetts, project Austin Street. Stantec is helping to provide design, product, and material options that appeal to millennials. In the coming years, Noyes and Klipfel aim to make GreenStaxx available in all major multi-family housing markets in the U.S. They have patents in the U.S. and pending in Europe and India, and they are considering offering the GSX system in Canada.
GreenStaxx in Action
The current 28 Austin Street project is moving along quickly because of GreenStaxx’s streamlined process. “GreenStaxx simplifies the coordination process, which is the most difficult part of modular building,” says Josef Rettman, NEI contractor and managing director on the Massachusetts project. “In the past, we’ve found that coordination between the local architects and the modular shop manufacturers has been extremely cumbersome, but GreenStaxx has tackled that problem.”
In fall 2017, the project was in the design and development stage—deciding whether to include a steel garage or a concrete tension garage, for example. They recently delved into some of the building configurations, including the elevation height and how the units will lay out on the grid. Rettman has been impressed with their approach. “Compared to what we’ve built before, the coordination process has been phenomenal,” he says. “It’s well thought-out and coordinated and flexible to the point where their design criteria and approach allows their systems to be utilized along multiple site commissions.”
The Austin Street project, which is eligible for LEED certification, uses approximately 100 GreenStaxx boxes and includes 5,000 square feet of commercial and retail space.
Learn more about GreenStaxx and see more gb&d modular stories.