Fabcon’s modular concrete panels make buildings stronger and easier to install.
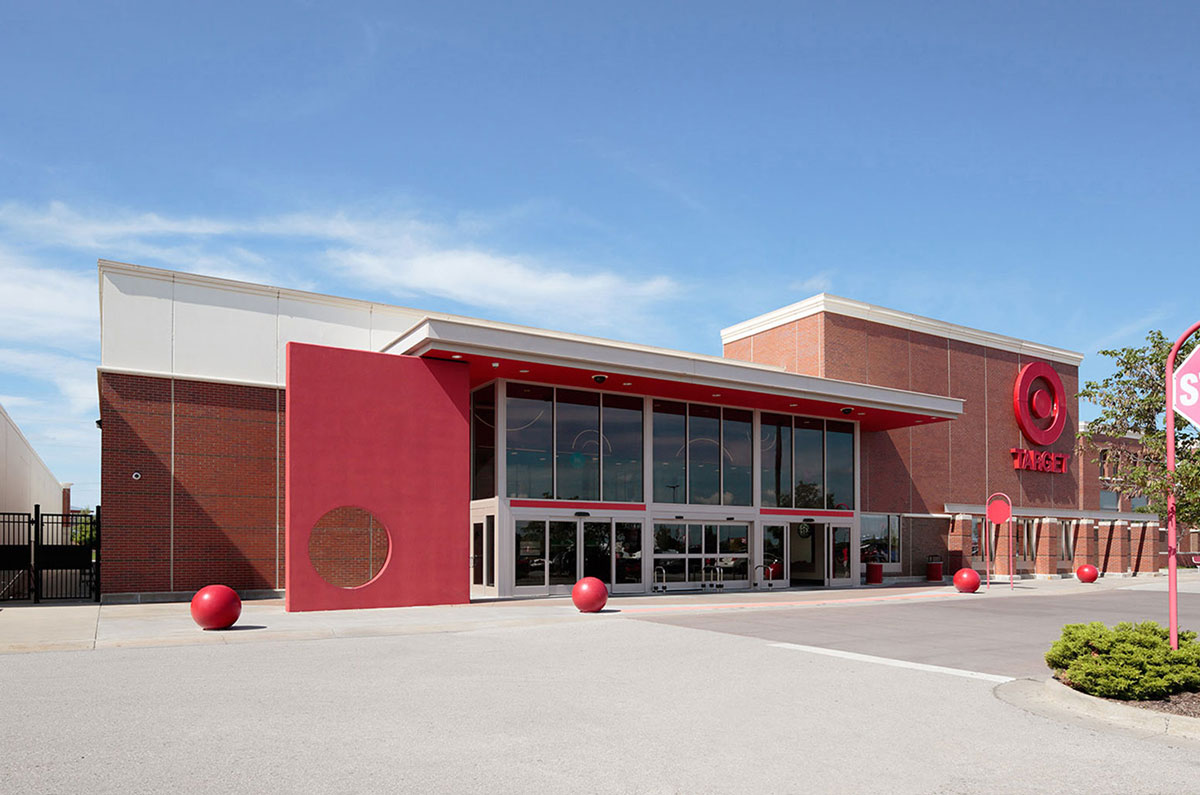
Fabcon’s precast concrete wall panels save projects time and money while being ultra durable and efficient. [Photo: Courtesy of Fabcon]
Fabcon Precast provides front-to-back service for modular construction projects, and their team is growing to meet the market demand for precast concrete wall panels. “In the last two years, we’ve seen volumes that are unprecedented in the company’s history,” says Tyson Intile, business development senior project lead at Fabcon. “Our growth in the near future will help us make more of what our customers want and get it to their job sites faster.”
It’s no wonder demand for precast is rising, especially considering the numerous benefits Fabcon’s panels feature—from quick installation to fire resistance.
1: Thermal Insulation
All elements in Fabcon’s products work together to provide a high level of insulation. Fabcon uses a combination of concrete and EPS foam that maximizes the foam in the concrete piece—increasing insulation capabilities.
Fabcon has also modified its concrete to take advantage of the air inside the concrete for additional thermal resistance, says George Miks, director of engineering. Regular concrete usually has a thermal resistance rating of about 0.11 per inch of thickness, while Fabcon’s concrete provides double the resistance—0.22 per inch of thickness.
FROM OUR JULY+AUGUST 2018 ISSUE
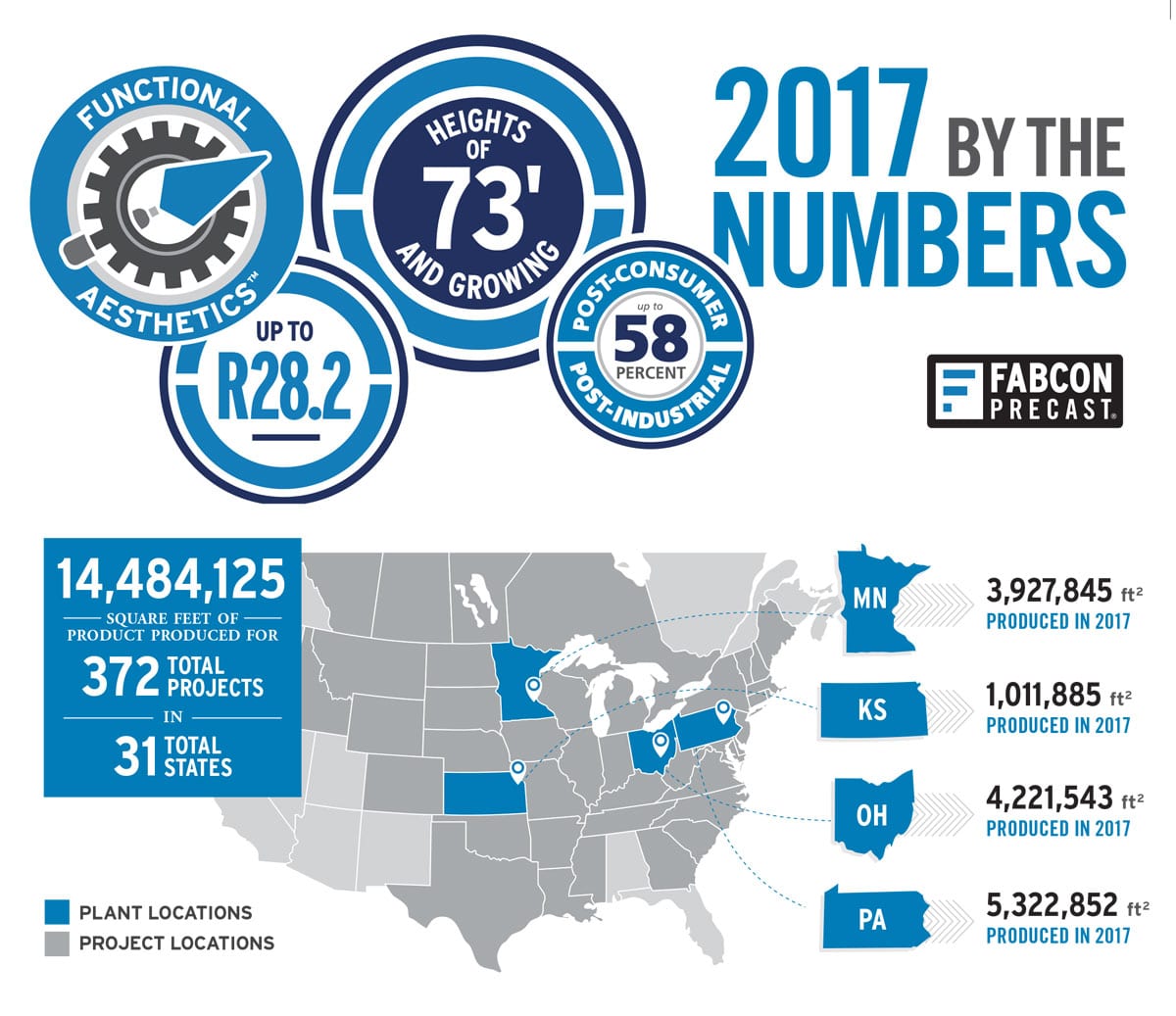
[Infographic: Courtesy of Fabcon]
Fabcon’s panels are also capable of meeting all R-Value requirements—regardless of the climate zone. The sandwich panel is the company’s highest R-Value product; in addition to the core and web insulation pieces, it also features a continuous insulation piece across the width and length of the panel (or bedfoam).
2: Sustainable Materials
With the exception of some of the raw materials that go into the panels’ insulation, materials in Fabcon’s products are locally sourced, including the cement, the coarse and fine aggregates, and the steel. Most of Fabcon’s projects are also within 200 miles of their plant, reducing shipping waste and the company’s overall carbon footprint.
3: Work-to-Existing
Precast allows flexibility for expanding and modifying existing buildings. With Fabcon’s precast concrete panels, you can do everything from add a pedestrian door to remove 75% of a wall.
And unlike other companies, Fabcon has a full staff of professional engineers. “We’re able to offer design and then execution in the field all internally,” Intile says. “If you were to go to a general contractor, you would need a saw-cutting company, a patching company, and an external engineer to do the design.”
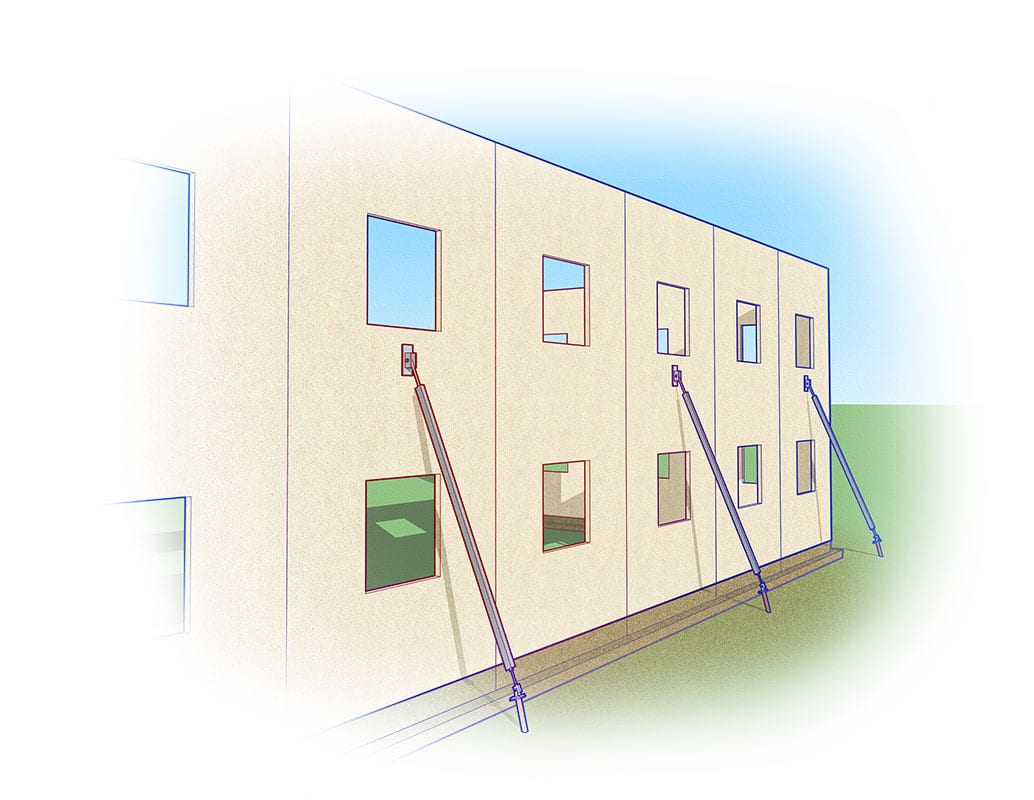
[Illustration: Courtesy of Fabcon]
Intile points out that external engineers wouldn’t have the same knowledge of Fabcon’s product either. Fabcon’s engineers know the design parameters and can design more efficiently. “We’ve seen designs come through that other people have done that have two, three, or four times the reinforcements necessary just because they don’t know enough to be able to design with our product efficiently.”
Fabcon has always offered expansion services to its customers, but now they’re creating business units that focus specifically on work-to-existing projects. “We’re going to have dedicated project management, design, and field staff,” Intile says. “So we’re going to be in a much better spot going forward to meet customer demands and be more available.”
4: Quick Installation
“Fabcon can establish a larger completed footprint in a shorter amount of time,” Miks says. “If you think of a masonry wall, what they send out to the site are a bunch of blocks that have to be assembled and constructed out in the field.” When Fabcon sends panels to the job site, the pieces are ready to install.
As a result, some companies are able to open their doors for business months in advance, Miks says, which is much faster than construction methods like block or stud frame. If things go smoothly out in the field, Fabcon can install 20 to 30 eight-foot panels in a day.
5: Load-Bearing Capabilities & Wind Resistance
Fabcon uses high-strength concrete, too. Many of the company’s precast concrete wall panels have a compressive strength of approximately 7,000 PSI. You can apply loads in excess of 100,000 pounds to the panels, Miks says
Fabcon’s precast panels can support roof structures for dead and live loads and act as the building’s lateral stabilizing piece to withstand seismic shaking. The wall panels also support the building structure for mezzanines and multiple floors.
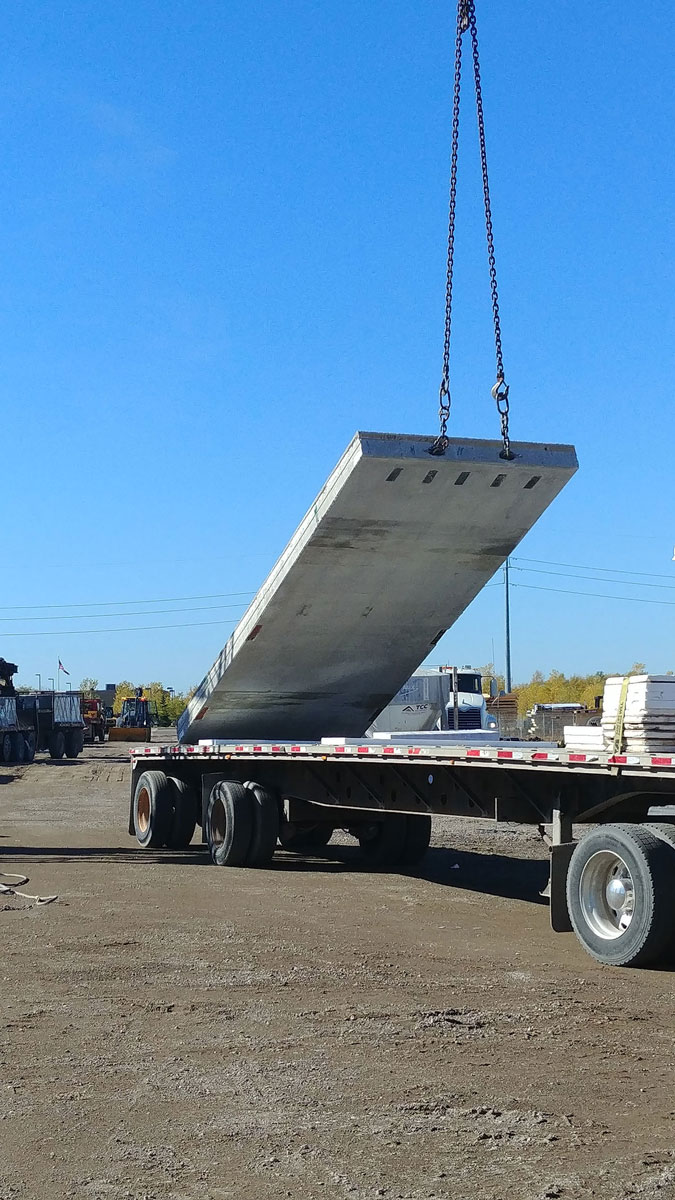
[Photo: Courtesy of Fabcon]
“When you build steel buildings, for instance, you have to put up perimeter beams and columns and then put steel skin against it. All of that steel has to support those enclosure panels,” Miks says. “With our system, you don’t need any of those perimeter beams and columns. You can just tip up the panel and have the roof steel members themselves attach to the precast.”
Fabcon designs to safeguard buildings—even in tornados with flying projectiles and winds up to 250 miles per hour. Fabcon’s precast concrete panels have also been implemented in large data centers that require high wind resistance to protect servers.
6: Large-Scale Projects
Fabcon recently completed a project in Iowa that included the tallest wall panels they’ve ever produced—nearly 73 feet. They used their 12-inch VersaCore+Green technology and an exposed aggregate finish.
And that’s just with a single panel. Fabcon has also constructed buildings as high as 120 feet tall (generally you have stacked panels and some additional supporting floors to reach those heights).
7: Fire & Sound Ratings
Concrete itself is an effective barrier for fire. Fabcon’s precast concrete wall panels are capable of providing a two- to four-hour fire rating. And their precast walls stay intact even in hot chemical fires. Warehouses often use Fabcon’s wall panels as dividers to protect goods on the other side of fire-prone areas. “The more delay you can create from one side to the other, the better chance of getting people out safely without having any incident and also the higher probability of protecting goods and services,” Miks says.