Story at a glance:
- NEOGARD highlights the pros and cons of coating systems to help you avoid costly pavement problems.
- Coating technology protects an owner’s investment by protecting the reinforcing steel and concrete.
- Having the proper substrate to install a traffic membrane system is a key to your success as a contractor
With so many different traffic coating systems on the market, it’s difficult to know which one to use. “First you need to determine what you’re trying to do,” says Mosby Lawrence, waterproofing manager at NEOGARD, a Dallas-based manufacturing and research organization. “It’s important that the coating type you choose is meeting your intention and your requirements.”
For different goals, like aesthetic improvement, supplying waterproofing, or protecting concrete surfaces, there are different coating types you should use. “But straight physical properties aren’t enough to see how a coating will perform,” Lawrence says.
That’s why on top of researching and learning about different systems, Lawrence recommends checking references and service track records from past projects by reaching out to contractors and engineers. He also encourages following the manufacturer’s advice concerning coating thickness.
Sustainability comes into play for NEOGARD, too. When traffic coatings are removed, they’re put in landfills. Lawrence and his team are working to educate clients on how to maintain their systems and about the high cost of replacement. Before you delve into maintenance, be sure you choose the right system in the first place:
Polyurethane Systems
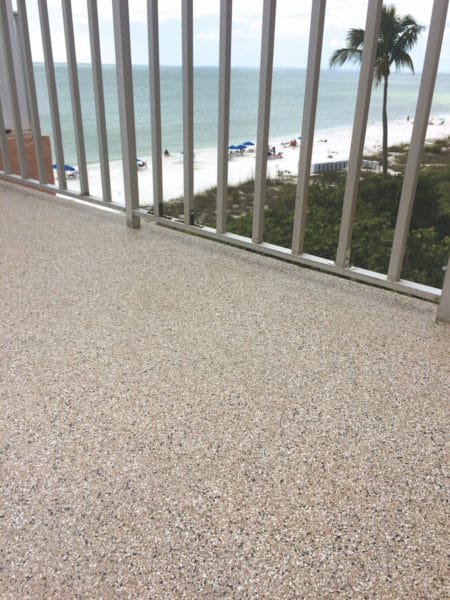
Polyurethane systems provide many aesthetic possibilities. Photo courtesy of NEOGARD
Polyurethanes have been used since the early 1970s. They have strong waterproofing properties and are able to bridge cracks. The systems also offer many aesthetic options.
“Clients can spend a great deal of money for traffic systems, but they are sustainable and meet strict VOC standards. If a client maintains them, you can simple re-apply the coating over it, so there is no need to replace them,” Lawrence says.
Polyurethane systems are sensitive to moisture and difficult to install. The systems also have a very low level of permeability, so they will perform best on elevated concrete structures.
PLUS: Sustainable waterproofing and crack bridging properties
MINUS: Expensive, difficult to install, low permeability
BEST USE: Projects that require waterproofing (apartment garages, etc.)
Epoxy Broadcast Systems
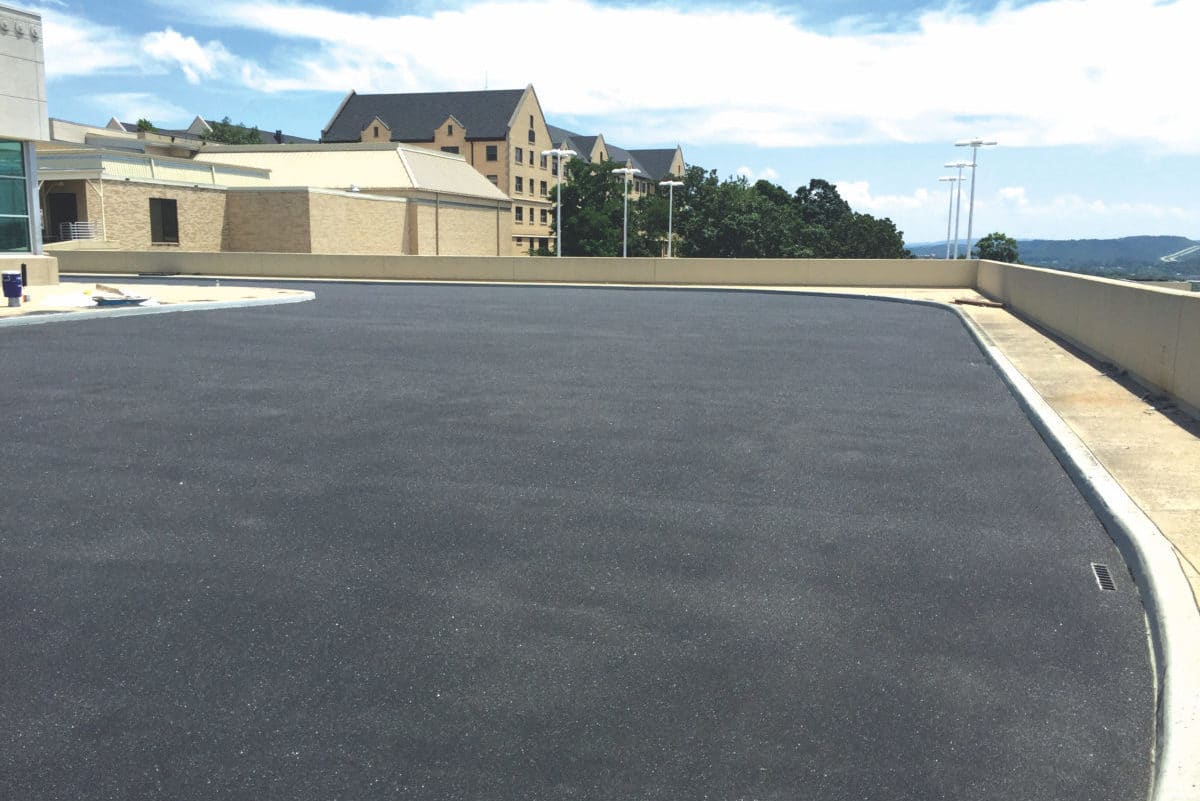
Epoxy broadcast systems are economical and easy to apply. Photo courtesy of NEOGARD
Epoxy broadcast systems have stood the test of time—they’ve been used for decades.
The systems are easy to apply and fairly inexpensive. And there are many options for aesthetics and slip protection. Epoxy broadcast systems provide concrete surface protection and enhanced durability.
“If you’re looking for an economical covering, this is an option,” Lawrence says.
PLUS: Affordable, easy to apply
MINUS: No waterproofing capabilities, corrosion and cracking may occur
BEST USE: Ramps, bridge decks, and parking garages
Polyurethane / Epoxy Hybrid Systems
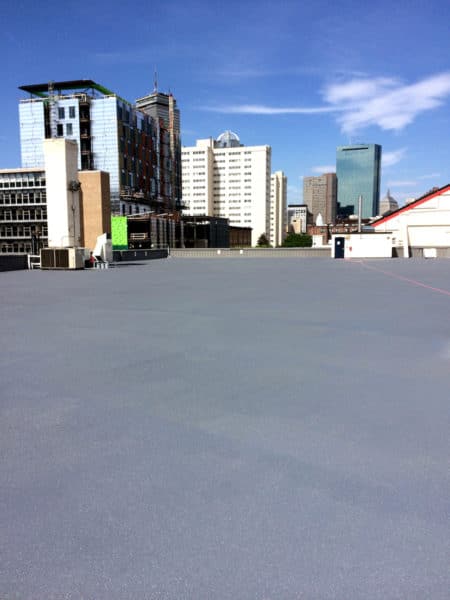
Hybrid systems are a good fit for high-wear areas. Photo courtesy of NEOGARD
Polyurethane/epoxy hybrid systems are growing in popularity. “Even if you don’t want to use hybrid throughout the whole garage, you can use it in high wear areas such as ramps, exits, entrances, and turning areas,” Lawrence says. “This will increase the durability of the entire system.”
PLUS: Durability for high wear areas
MINUS: Low movement capabilties
BEST USE: High-volume, heavy traffic parking garages (hospitals, retail centers, etc.)
PMMA Systems
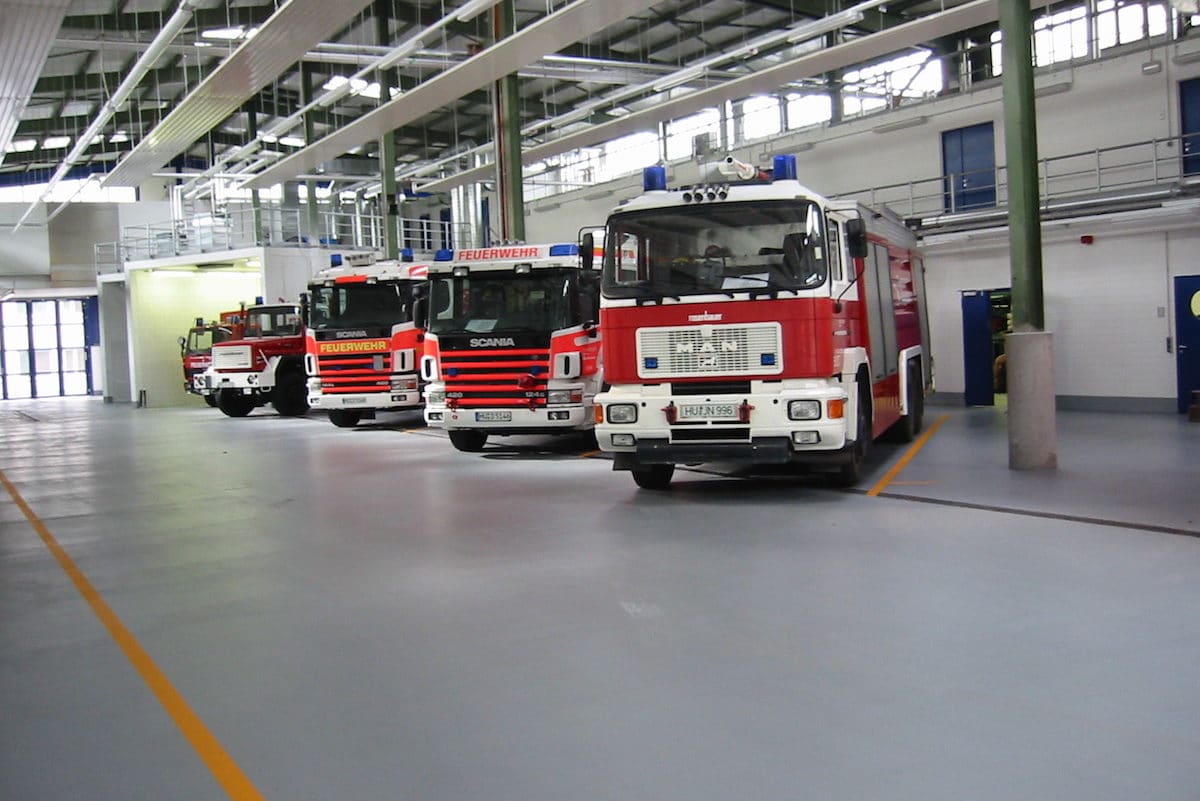
PMMA systems are the best for projects that require a quick turnaround time. Photo courtesy of NEOGARD
Poly-methyl methacrylates (PMMAs) have a growing presence in the US due to their durability, chemical resistance, and warranty programs. The chemistry itself makes PMMA systems more durable.
“The chemistry is used for dental fillings, road markings, and certain types of glass,” Lawrence says. These also have a fast turnaround time—they are frequently opened to service within hours on the same day of application.
PLUS: High durability, quick return to service
MINUS: Expensive, odor during application, prone to cracking
BEST USE: Projects where turnaround time is critical
Latex / Vinyl Copolymer Systems
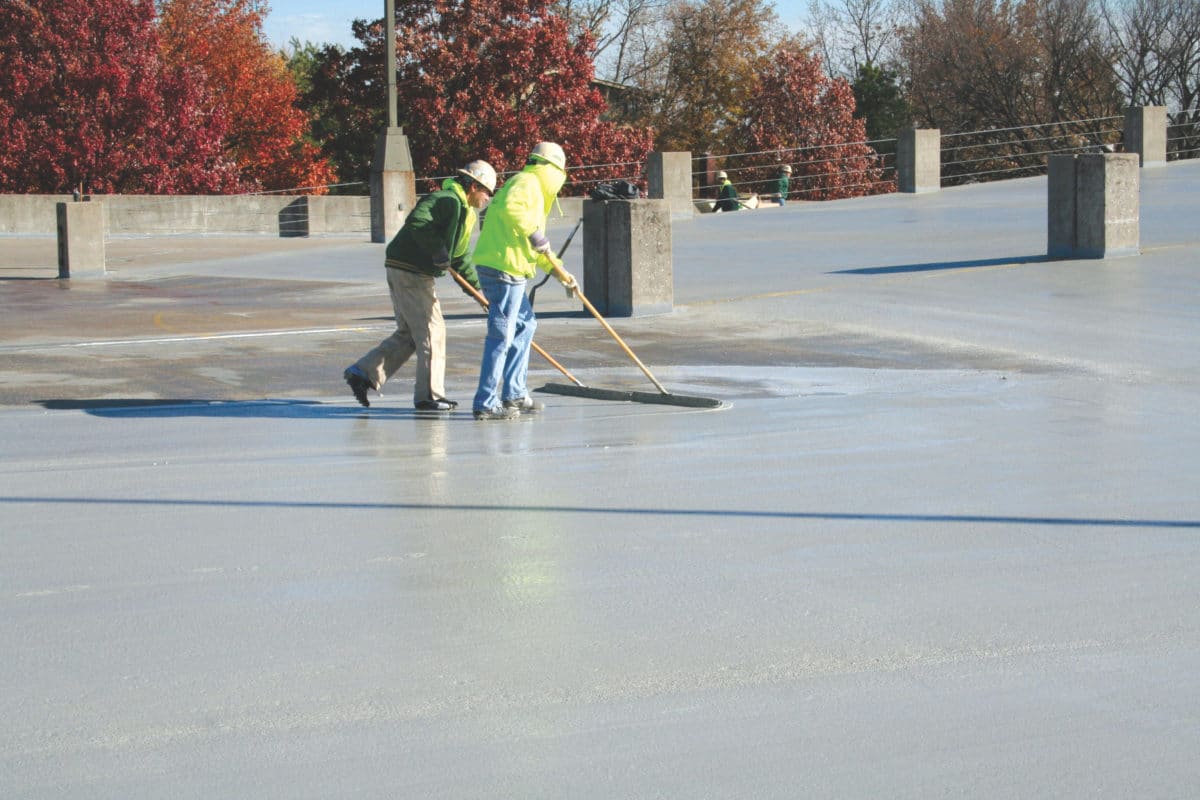
Latex / Vinyl Copolymer systems have high permeability, but no waterproofing capabilities. Photo courtesy of NEOGARD
Latex/Vinyl copolymer systems are an economical, non-flammable option with no odor during application. They are breathable and allow more moisture vapor to transfer out of the concrete. As a result, they’re often applied on concrete surfaces with metal pan deck underneath, which provides no permeability. From an aesthetic standpoint, the final finish color looks very similar to concrete.
PLUS: No odor, easy to apply, high permeability
MINUS: No waterproofing capabilities, naturally rigid and prone to cracking
BEST USE: Concrete surfaces with metal pan deck underneath
Sealers
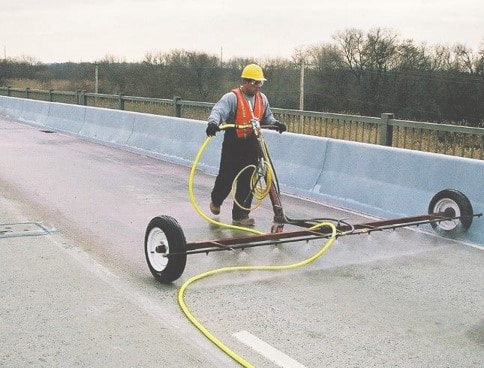
Sealers are easy to apply, but need frequent reapplications. Photo courtesy of NEOGARD
Sealers are economical, easy to apply, low in odor, and don’t change the appearance of the concrete at all. But they will only protect the surface of the concrete for a limited amount of time before a new coating is needed. “The key to get the best benefits for sealers is frequent applications every five years,” Lawrence says.
PLUS: Affordable, easy to apply
MINUS: No waterproofing or crack bridging properties, frequent reapplications needed
BEST USE: New construction projects
How It Works
Coating technology protects an owner’s investment by protecting the reinforcing steel and concrete. Cracks occur when water soaks into the concrete and down into the reinforcing steel. The steel begins to corrode and rust, which causes a crack in the concrete.
“Major corrosion issues can be quite expensive for the repair process and that’s what these coatings are for, to help reduce the amount of repairs needed,” Lawrence says.
But how do traffic coatings work? Waterproofing systems keep the water from permeating the concrete. If you can cut off the flow of water, then you also cut back on corrosion. The membrane is the key part of the system that includes the waterproofing properties. Everything else is added to provide traction and chemical resistance to protect that membrane.
A Contractor’s Advice
“Having the proper substrate to install a traffic membrane system is a key to your success as a contractor,” says Kenny Robbins, restoration division manager and COO at Consolidated Waterproofing Contractors in Beltsville, Maryland. This process includes surface preparations and material mixing, as well as routing and sealing of cracks, patching of voids or delimitations, and shot blasting and grinding the concrete deck to create a dust-free surface.
Robbins says NEOGARD makes mixing simpler by color-coding their products, but it’s always important to follow instructions to make sure the product will cure correctly. “Working with the folks at NEOGARD is like working with family. We know they always have our back,” Robbins says.
Whether attending a pre-install meeting or visiting the installation site, NEOGARD plays an active role in helping contractors create successful projects. Robbins says one of the main benefits of working with NEOGARD is that the employees become very familiar with the traffic coating systems and products, and they also receive a high level of customer support.