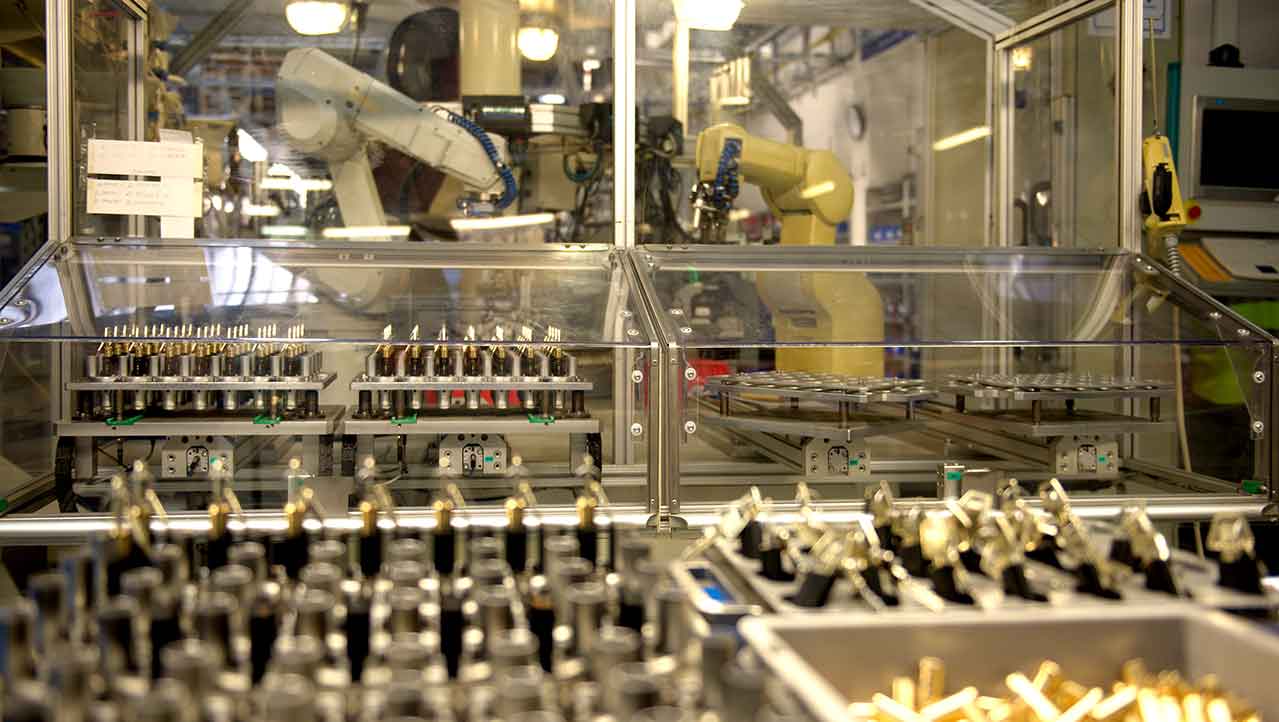
[Photo: Courtesy of ASSA ABLOY]
ASSA ABLOY’s innovative R&D continues to push the limit with the best locking systems in the industry.
The world’s largest manufacturer of door opening solutions has well over 150 products in development at any one time—all of which go through an intense research and development process. By the time the final product makes it to the consumer, ASSA ABLOY’s engineers know exactly how it will function and what it takes for the product to fail.
The company’s qualitative approach means not only understanding the products and how they work, but truly comprehending the needs of customers. “It’s great to have a Cadillac of a product, but if it’s missing a mark with the customer and not really helping to take care of their needs, then we haven’t succeeded,” says Dan Picard, director of innovation at ASSA ABLOY Americas. “We have to be very close with our customers and end users. Walk in their shoes, understand their pain points. We want to understand every point in the chain.”
This hands-on approach is what sets the company apart. “At the end of the day, we and our peers in the industry are doing a good job with traditional security and safety, but what differentiates us is how we understand our customers and how they operate,” says Peter Boriskin, chief technology officer for the Americas. ASSA ABLOY was formed in 1994 and has since grown to an international company operating in more than 70 countries. It has been named four times as one of Forbes’ World’s Most Innovative Companies.
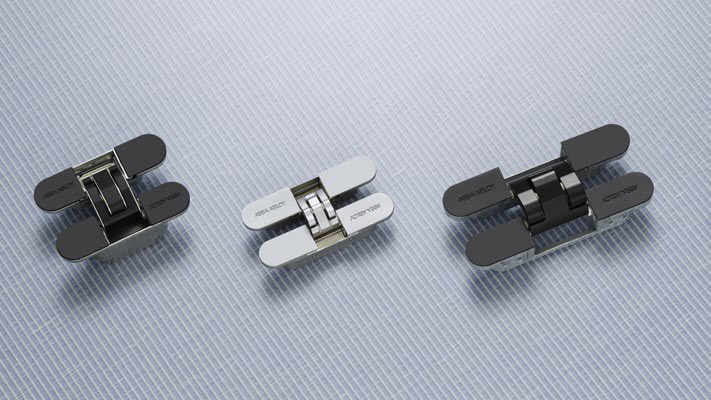
The McKinney Concealed Hinges feature 3D adjustability for easy installation and door alteration. [Photo: Courtesy of ASSA ABLOY]
Employing Empathy
The first stage of the R&D process is empathy with the customer. ASSA ABLOY’s teams get into the trenches, examining every detail. They spend time observing how their products are being used—and in some cases abused—listening to the needs and concerns of customers and end users and interacting directly with the product in the consumer setting. The company’s “Voice of the Customer” research team constantly gathers feedback through roundtable discussions, interviews, and immersion research. They take into account every aspect—from ease of installation, maintenance, safety, and security to sustainability and overall functionality. “We try to get as many different points of view as possible with every type of product we are developing,” says Lee Griswold, industrial design manager for the Americas. “We do deep dives into learning as much as we can ahead of developing a product.”
ASSA ABLOY responds to requests from customers while also looking to uncover needs that have not yet been discovered. “If we can develop a solution to a problem that the end user is not even aware of yet, that’s great,” Griswold says. Part of Griswold’s job is to work on aesthetics, incorporating the lock hardware into a room. He spends a lot of time learning about the look and finishes customers seek while keeping functionality, security, and longevity at the forefront. “Door hardware, in general, is part of a system. The hardware is part of a room—a room which is part of a building, a building that is part of a community. This is why it’s important we develop products that not only accommodate the needs of the system, but are timeless in their appearance.”
FROM OUR MAY+JUNE 2019 ISSUE
The preferred publication of leading green professionals.
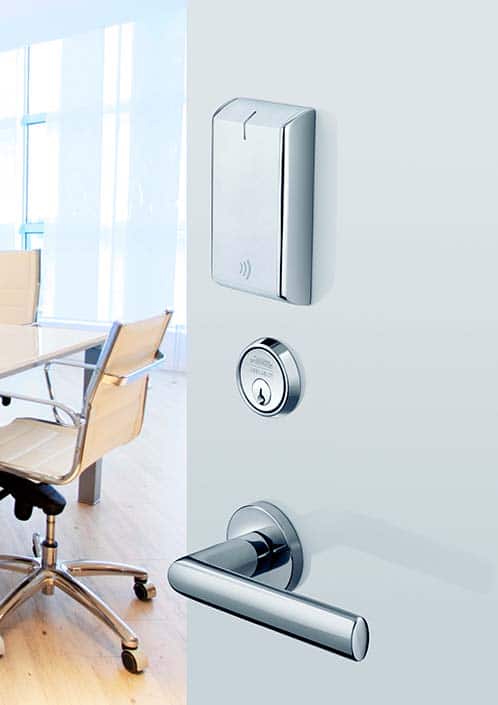
[Photo: Courtesy of ASSA ABLOY]
Expert Collaboration
Each of ASSA ABLOY’s divisions has its own R&D department, allowing them to focus specifically on their market and category. Having specialized departments means each product has its own team of experts to work on design and manufacturing. It also means collaboration is just a phone call away. “Engineering teams can work side by side with manufacturing teams. It is critical to solving problems more efficiently,” Griswold says.
ASSA ABLOY encourages cross-company communication to create total door solutions. Weak points in the systems are more easily identified by having many specialized R&D departments work together, rather than having one overarching department. “The goal of the multiple R&D teams collaborating is to develop a holistic solution, where the sum of the parts is greater than the whole,” Picard says.
It’s a hybrid approach. “You have that collaboration when you need multiple areas of expertise,” Picard says. “But it’s also good to have some separation so you have more subject matter experts. Each product engineer becomes very familiar with the specific product they are working on. It’s their bread and butter.”
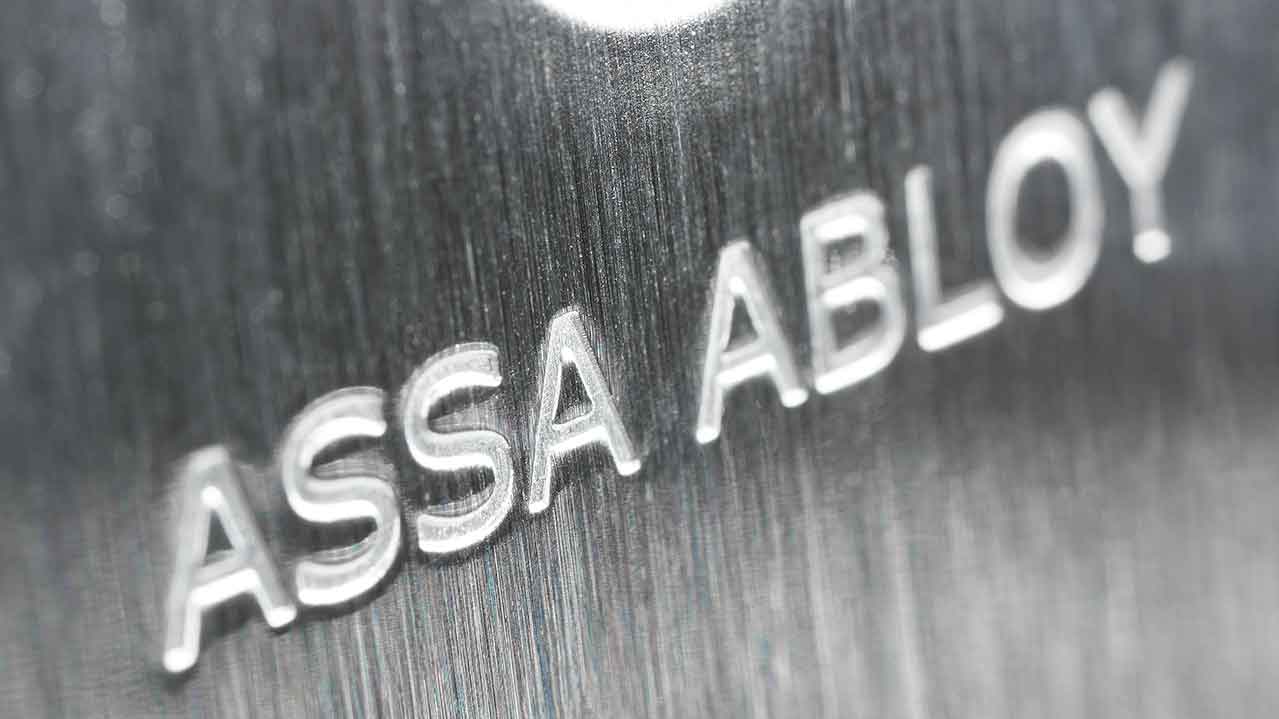
[Photo: Courtesy of ASSA ABLOY]
Testing and Re-Testing
Once a need is identified and a prototype is designed, the development process is far from over. ASSA ABLOY puts all products through a rigorous testing process. Depending on the product, it’s tested for durability, strength, safety, security, and/or fire rating. Door locks are put through a full mechanical-cycle test where the door is opened and closed to the point of failure. “There is a lot that has to be considered when developing a product and making sure it conforms to industry standards,” Picard says.
The bare minimum is never enough for ASSA ABLOY. The company holds all its products to the highest possible standards. Depending on the individual product application, the testing process may take several months. “There is no rule of thumb for how long the testing process takes,” Boriskin says. “Even if the engineering process is short, we make sure to really test and validate our products before launch.”
As a global company, ASSA ABLOY has to consider environmental conditions from all over the world. Many of its products are tested for high winds and other severe weather.
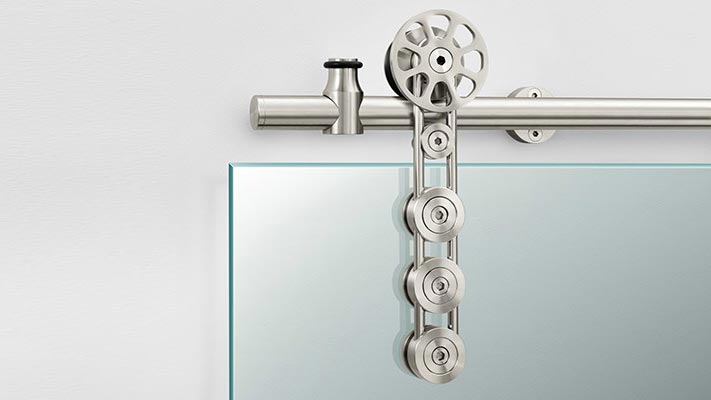
[Photo: Courtesy of ASSA ABLOY]
Sustainable Innovation
Transparency and sustainability are top priorities for ASSA ABLOY. Development teams look closely at suppliers and the chemicals used in products, avoiding potentially harmful substances wherever possible. “Customers want to know what’s in the product,” Picard says. “We pride ourselves on having the safest, most secure, and sustainable products.” All products are designed with longevity and end-recyclability in mind. “We think about the whole life cycle of the product.”
Many products carry Environmental Product Declarations, Health Product Declarations, Declare labels, GREENGUARD Gold certifications, and are designed to increase energy efficiency. Careful attention is paid to how each product can help customers earn credits for green building programs like LEED and WELL, too. And the company recently developed two energy-harvesting lock products.
ASSA ABLOY does more than talk the talk. Its manufacturing plants are focused on reducing energy consumption and carbon emissions, improving water and waste management, and phasing out hazardous chemicals. One of its plants generates more than 50% of its power from renewable energy sources. “Not only is it the right thing to do, but the reality is, at the end of the day, these are the places we live, we work, and we play,” Boriskin says.