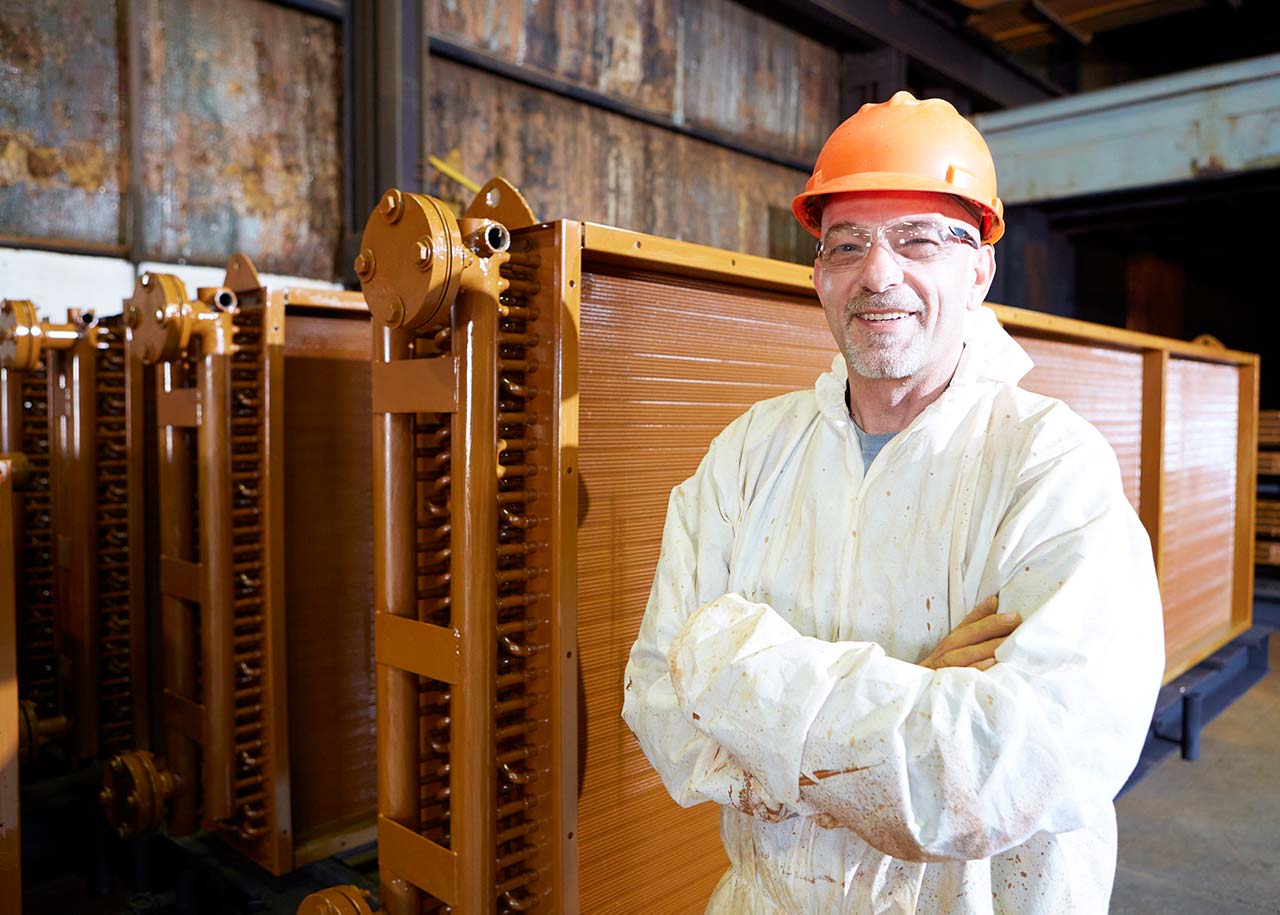
Heresite Protective Coatings offers countless benefits to important equipment, from prolonging longevity to protecting against chemicals and salt spray. [Photo: Courtesy of Heresite Protective Coatings]
Heresite Protective Coatings protect equipment from the toughest environments.
Heresite Protective Coatings has been solving corrosion problems for commercial heating, cooling, refrigeration, and other industrial process coils for more than 50 years. This leader in innovative HVAC coatings also has unmatched solutions for related components like copper piping exposed to corrosive conditions. “This company was the first to develop a coating and an application process for HVAC condenser and evaporator coils,” says Peter Hellman, president of Heresite Protective Coatings.
The world of HVAC coatings is unique, considering how you’ll treat various kinds of metals on the same part. “You’re dealing with coils and units with aluminum, copper, and galvanized construction, as well as painted surfaces,” Hellman says. The geometry of heat exchangers with intricate internal surfaces, including microchannels, is also distinctive for this market. The coating process and coating itself has to be designed for these market-specific factors and also has to be an extremely thin film to not affect the unit’s efficiency. The experts at Heresite specialize in all this and more.
Heresite recently expanded its product line with new spray-applied options, following the release of an improved version of its popular full immersion P-413. P-413—a thin film, high-performance coating—is used principally for coil and radiator heat exchangers, and it’s the first HVAC-R coil and radiator coating to meet the ISO 12944-9 Standard for severe offshore marine environments (C5I, C5M, CX). It significantly extends the service life of HVAC-R and other heat transfer equipment.
Consider these additional benefits of Heresite’s standout product line.
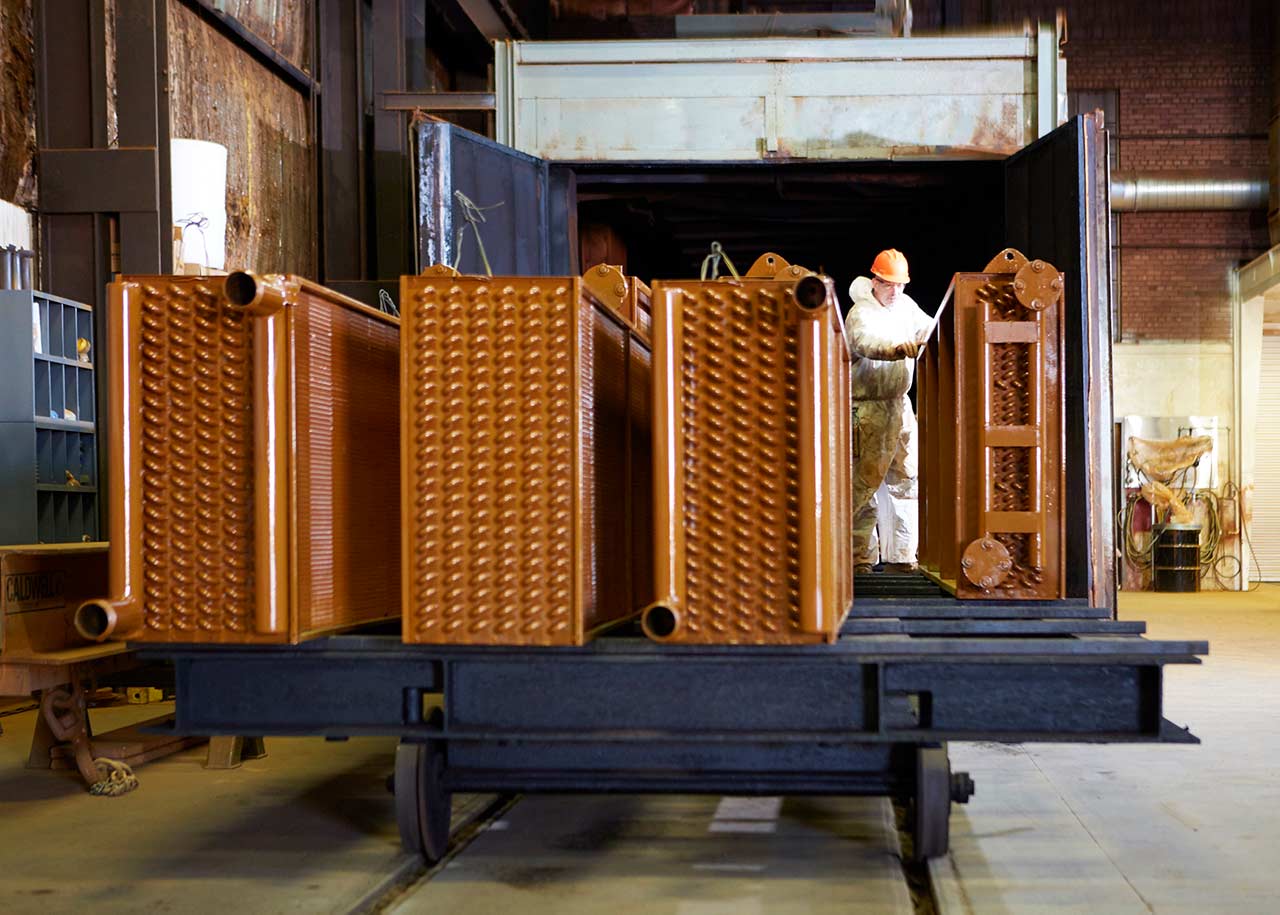
[Photo: Courtesy of Heresite Protective Coatings]
1. Treat More Than Coils with Spray
In 2019, Heresite launched ES-600, a spray-applied coating for HVAC-R coils, cabinets, and components. ES-600 is designed for use as a stand-alone spray for coils, cabinets, and components (like copper piping); or for use with Heresite’s P-413 full immersion coil coating on components, which cannot be oven-cured. Hellman says that while spray-application is not as robust of a process as the Heresite P-413, it is a very robust option when logistics don’t allow for a full immersion process. “The ES-600 also complements the P-413 well, in that it adds to our options and capabilities for protecting units beyond the evaporator and/condensor coils.”
ES-600 has been tested to ensure some of the highest corrosion/environment resistant performance, including some of the same ISO standards as P-413. It’s also been fully tested on aluminum, copper, and galvanized and has been found to deliver an unsurpassed direct-to-metal performance with just cleaning. No primers are needed.
FROM OUR MAY+JUNE 2019 ISSUE
The preferred publication of leading green professionals.
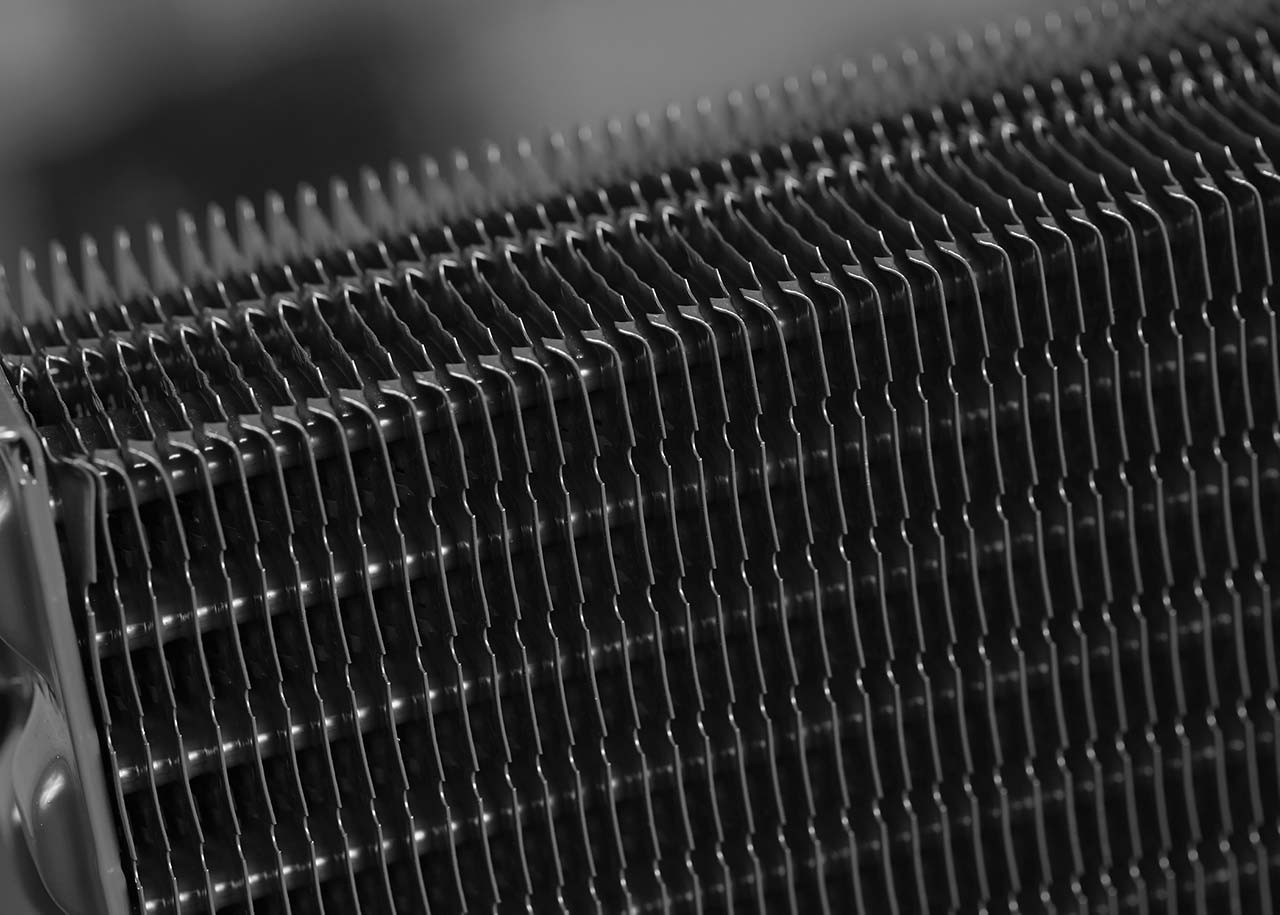
[Photo: Courtesy of Heresite Protective Coatings]
2. Extend Equipment Life
Even if you have HVAC-R equipment with a long life, you need to consider the equipment’s operating environment and be prepared for the toughest conditions. Consider, for example, an industrial complex in a humid marine environment. Now you’ve got chemicals and salt spray. “If you have a wastewater plant in proximity to marine or salt air environments, or a refinery or something with potentially corrosive fumes but it also happens to be along the sea, you’re really looking at combined corrosive elements that accelerate the attack,” Hellman says. “A lot of the world’s population lives in these coastal areas, and this brings industry in close proximity as well. It is these environments that dictate our testing protocols, using cyclic versus static testing and incorporating multivariate elements like humidity, UV, and chemical resistance.” Heresite has a Chemical Resistance Guide featuring 400 chemicals for clients to reference.
Hellman says Heresite is often asked: How long will the product work in this kind of environment? “On average you’re going to get two to three times the life versus an uncoated unit in our market.” He says it’s difficult to be more specific because, even within 100 miles, you can have chloride deposition rates that differ by a factor of four times—not all marine environments are the same.
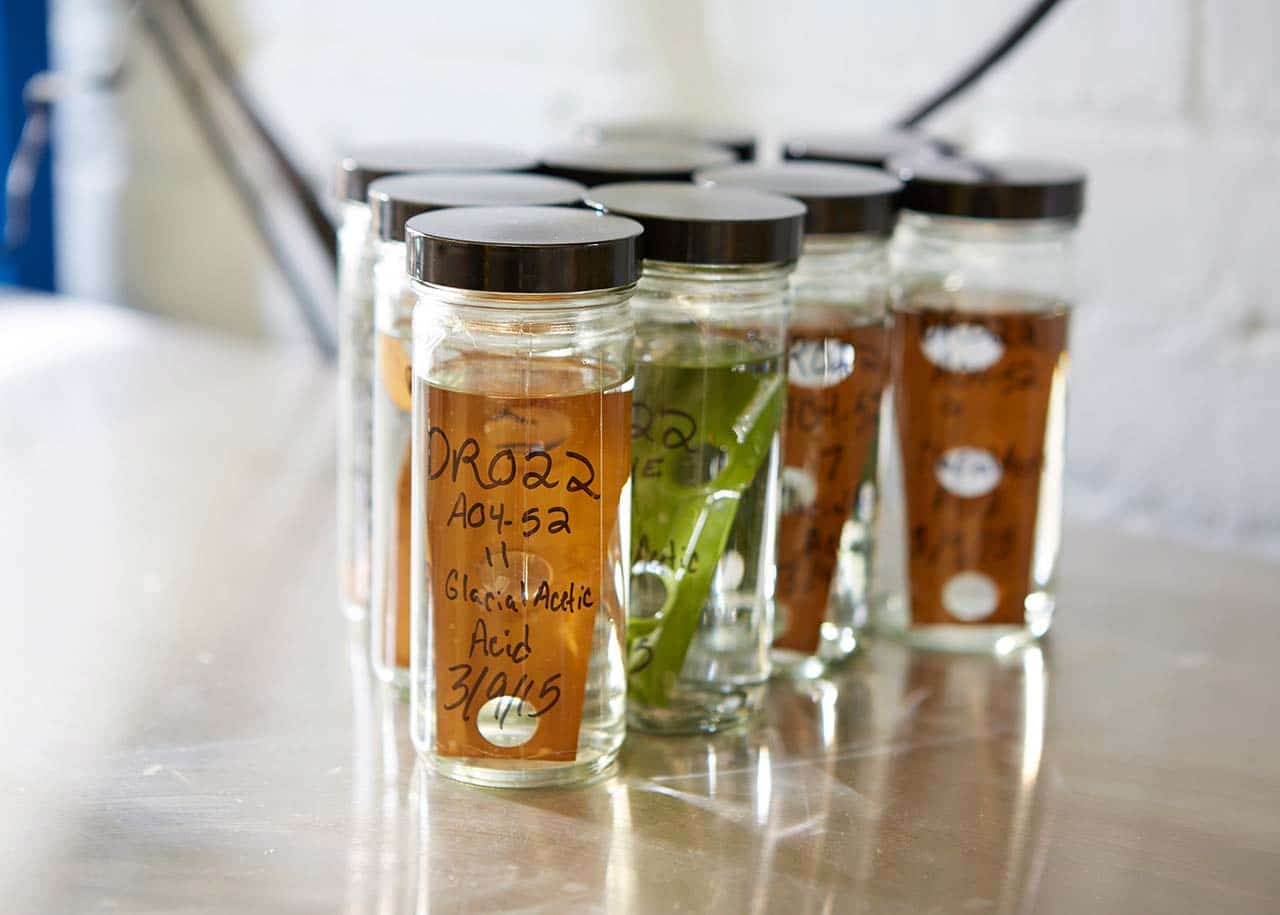
Heresite tests its coatings in all environments, incorporating elements like humidity, UV, and chemical resistance. [Photo: Courtesy of Heresite Protective Coatings]
3. Rest Easy with Proven Testing
Equipment owners need to have the most relevant data at the ready when considering coatings that may be exposed in harsh environments. Heresite goes beyond traditional static salt-spray testing, or ASTM-B117. The company does more intensive cyclic testing, too. Consider Florida, where you have salt air exposure but also sun and rain. Heresite’s use of the ISO 12944-9/ISO 20340 procedure cycles the coating through salt spray, sunlight, and freezing weekly for 25 weeks. “A coating that performs well with static ASTM B-117 salt spray doesn’t necessarily pass this test,” Hellman says. “The ASTM B-117 test has no correlation to the real world.”