Throughout the processes of creating, transporting, and eventually receiving leftover plastic concrete, there’s a lot of room for improvements in sustainability and waste reduction. In order to steer the concrete industry in a more eco-friendly direction, Klaus-Alexander Rieder, R&D director of concrete technologies at GCP Applied Technologies, and his team have developed a number of innovative concrete solutions at their research hub in Cambridge, Massachusetts.
How do you reduce waste and improve sustainability across the life cycle of concrete? That’s been one of the central questions we’re focused on at GCP. It’s been no easy task. One must consider the CO2 that’s emitted in the mining and transportation phases, the water that’s used to make concrete, and the large amount of material that’s often left over. Up to 3 to 5% of concrete production gets returned to the plant where it was produced. That’s why we’ve taken a multi-faceted approach to waste reduction, one that utilizes various concrete technologies to achieve a shared goal.
One of the biggest problems facing the industry is the diminishing amount of high-quality aggregate, with quarry reserves often contaminated with clay. In response, GCP developed the CLARENA® portfolio of materials management solutions to mitigate the negative effects of clay and reduce the amount of wasted aggregate. The CLARENA® chemical additive improves the workability and flow of concrete made with aggregate that has high clay content. Another area of focus is reducing the amount of water used for making concrete. This is especially important in states like California that have tougher standards for water use after suffering years of drought.
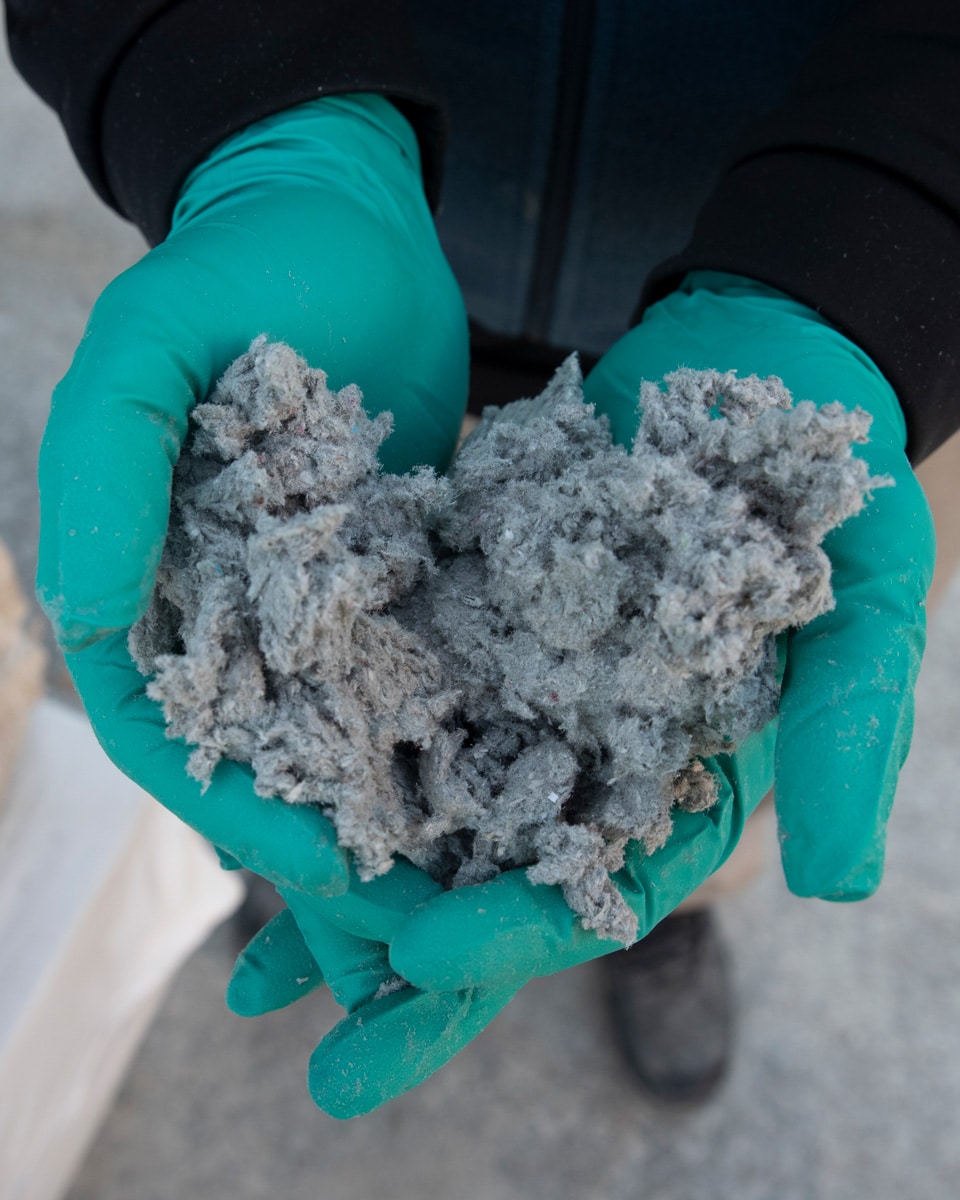
[Photo: Courtesy of GCP Applied Technologies]
With our ADVA® water-reducing admixture technology, we help customers use up to 35% less water while maintaining the workability of the concrete. These additives are highly versatile and have the added benefit of extending workability by up to three hours, without impacting the strength development of the concrete. ADVA® products also reduce the use of cement in each cubic yard of concrete, making the best use of that critical component.
The VERIFI® in-transit concrete management system, which is installed on the ready mix truck, monitors, measures, and manages each concrete batch’s properties in real time, from the plant to the jobsite. This enables concrete producers to deliver more consistent concrete quality to the jobsite using less cement, less energy, and having fewer rejected concrete loads.
GCP recently introduced CLARENA® RC40, a new additive to treat and reuse returned concrete as aggregate. It converts the returned and unused plastic concrete into a hardened granular state that can be broken up and reused in fresh concrete as a partial replacement for fine and coarse aggregate. This granular material can also be used as a high-quality compacted fill material for end uses such as road base.