Story at a glance:
- Natural stone is low maintenance, 100% natural, durable, and leaves less of a carbon footprint.
- Polycor’s natural stone meets the design needs of modern architecture and aesthetics.
- Excess stone is used for roads, curbs, landscaping products, and even furniture.
The Empire State Building, the Pentagon, the Lincoln Memorial. Polycor’s natural stone can be found on some of the most beautiful, iconic buildings in the world.
But it’s not just historic buildings where you’ll find Polycor. The Canada-based company with quarries across North America and Europe has more than 1,200 employees worldwide and has brought beauty and sustainability to the award-winning projects of today, too. In 2020 alone multiple projects won Tucker Design Awards from the Natural Stone Institute using Polycor stones, including the new downtown Edmonton location of the Royal Alberta Museum in Canada. Designed by architecture firm DIALOG, this project used Polycor’s Indiana limestone in standard gray.
We talked to the experts at Polycor about how projects like this and others are made more sustainable by using natural stone.
1. Natural stone offers design flexibility.
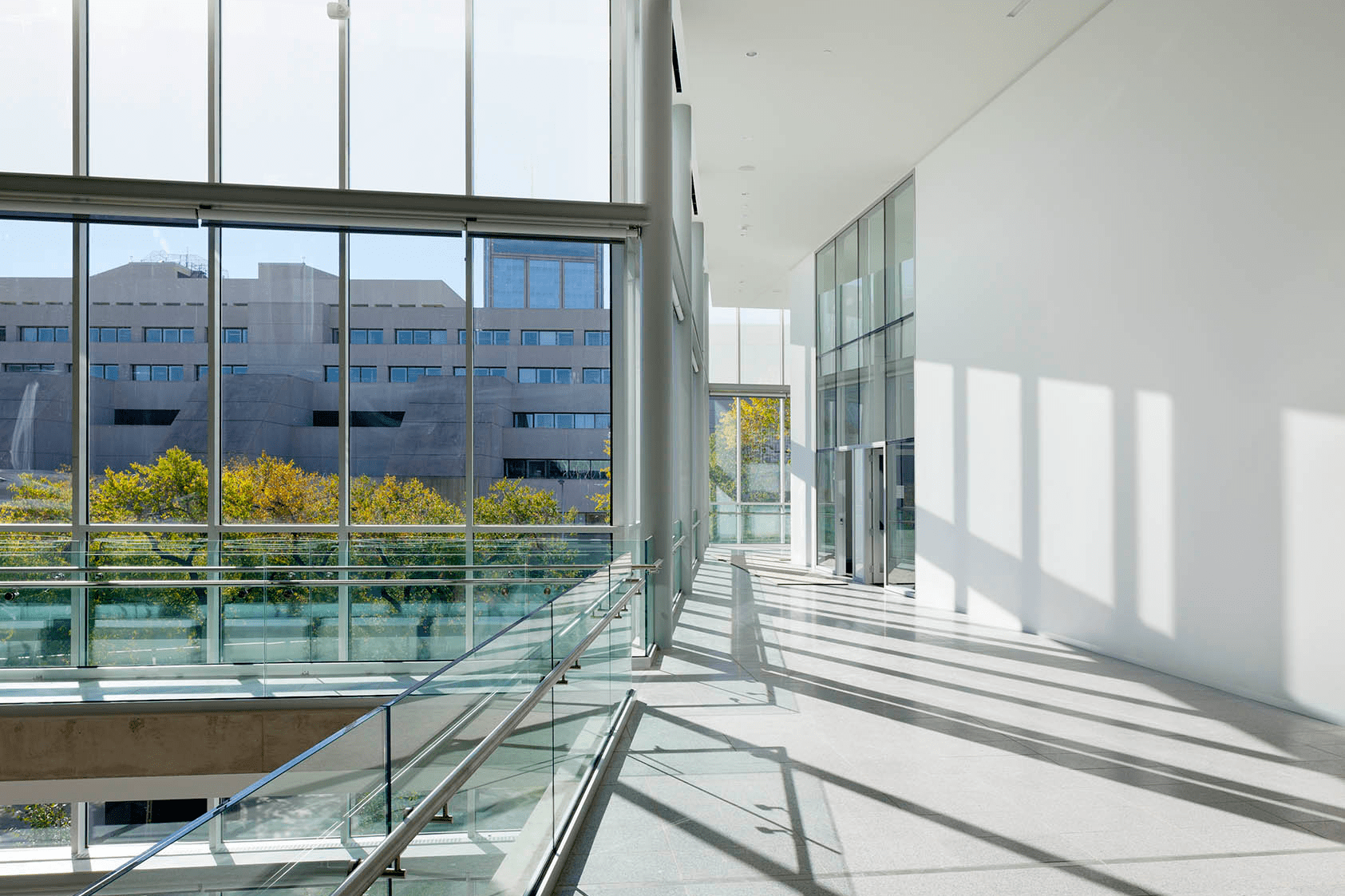
The Royal Alberta Museum in Edmonton received a Tucker Design Award from the Natural Stone Institute in August 2020. Designed by architecture firm DIALOG, this project used Polycor’s Indiana limestone in standard gray. Photo courtesy of Polycor
“When people think about natural stone they think about old buildings, but natural stone can also meet the design needs of modern architecture and aesthetics,” says Jean-François Marquis, communications director at Polycor.
You can see that in real life at both the Royal Alberta Museum and The Grande Arche de la Défense in Paris. The latter, designed by architects Valode & Pistre, uses Polycor’s Bethel White granite, the whitest granite available on the market, according to Hugo Vega, Polycor’s vice president of commercial and institutional sales.
“Natural stone is very versatile. It offers a wider range of sizes and formats and a multitude of styles that concrete and other cast products can’t,” Vega says.
Quarried in Vermont, Bethel White granite was used to restore The Grande Arche, replacing Italian marble that couldn’t last even 30 years. Bethel White won’t rust or change color over time, and Vega points to Washington, DC’s Union Station as evidence. It’s thought to be the first large commercial project from that Vermont quarry, and it was built more than 100 years ago. “It’s still bright white,” Vega says. “That’s the best proof of durability.”
2. It’s 100% natural.
Natural stone really is just that—natural. It’s readily available from the earth, and it doesn’t release VOCs. It requires zero chemicals or additives to prepare it for your next project; it’s quite literally ready to go. “Natural stone is the organic food of building materials,” Marquis says.
Production for natural stone simply means extraction, cutting, and polishing. Compare that to other building materials, like concrete, which uses a combination of crushed stone and chemicals to manufacture products.
Polycor focuses on sourcing the highest grades of stone so that, for instance, a black stone like Cambrian Black® granite, quarried in Quebec, doesn’t need dyes to achieve its rich color. It’s a true black throughout, even when honed or brushed. A manufacturer of a lesser grade stone might apply a black dye or resin to a stone’s surface. Then, if the treated surface of the stone is honed or brushed away, it appears gray.
3. It has a lower embodied carbon footprint.
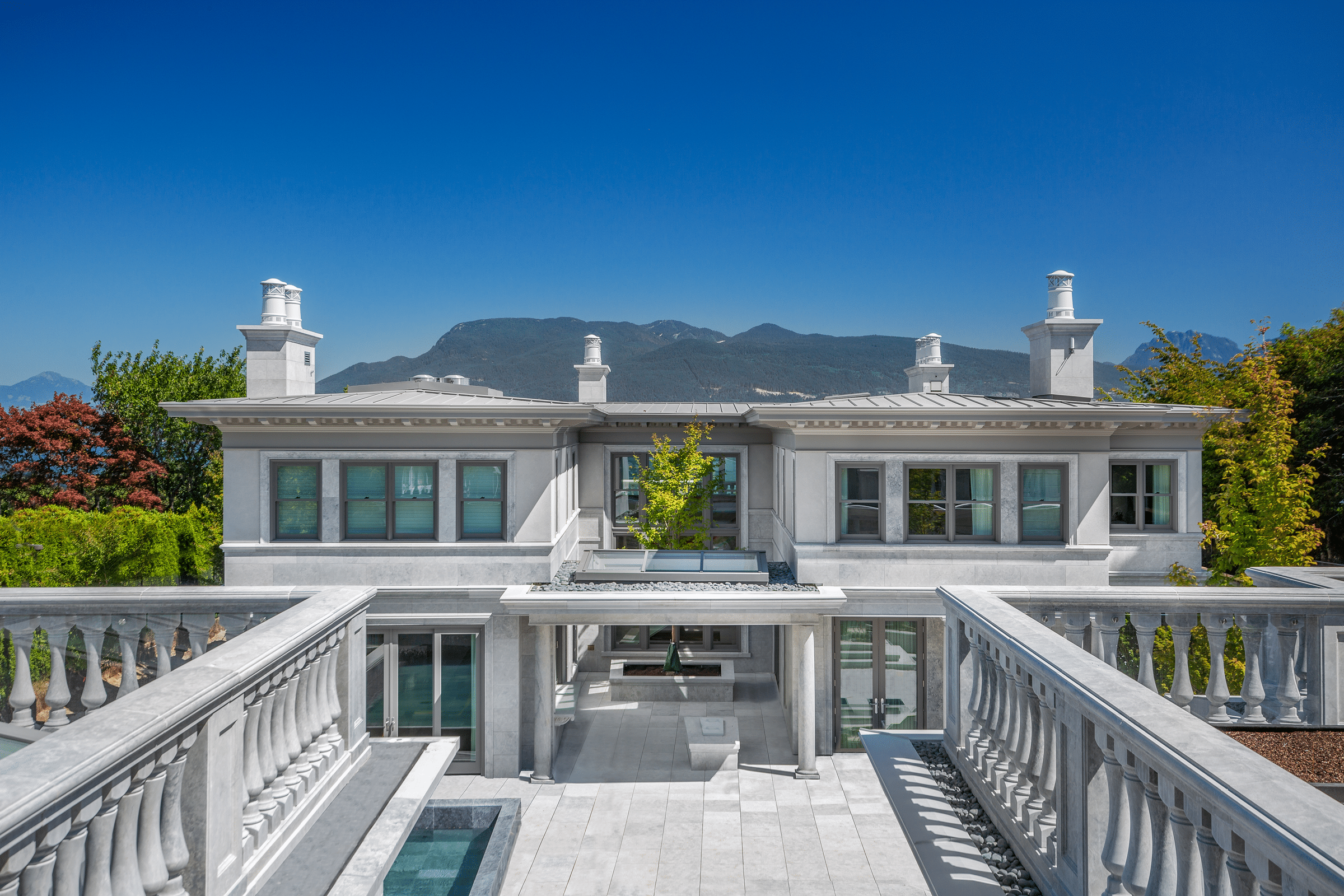
This neoclassical private residence in Vancouver was built with Polycor’s SAINT CLAIR™ – Fleuri Marble from Oklahoma, fabricated and installed by Red Leaf Stone. Photo courtesy of Polycor
The less carbon you have in your materials the more sustainable your project, Vega says. “Stone has an extremely low embodied carbon footprint because it was formed by the planet itself,” he says. “It’s right under our feet.”
A UK study referenced by the Natural Stone Institute also reports that embodied carbon in natural stone is less than building materials like steel, cement, timber, slate, and bricks. “When you compare it to aluminum, steel, or plastic it has an extremely low carbon footprint,” Vega says.
4. Natural stone is low maintenance.
Most of the natural stone used in cladding material or even paving and hardscapes like the ones you see in public plazas don’t need any maintenance; you don’t even need to apply a sealant. Just pressure wash it from time to time and go on your way. “It doesn’t require any other form of protection,” Vega says.
5. It’s also highly durable.
Natural stone lasts longer than concrete, glass, or quartz. “Various limestones, marble, and granite have been made by nature millions of years ago and, when used in construction, will last as long as the underlying structure lasts. Think about the Pyramids or the Great Wall of China; they’re still standing today. Nowadays when we see a stone face being repaired it’s never the stone itself that’s in question but more the structure behind it, whether they’re having to do the waterproofing or repair window surrounds,” Vega says.
Natural stone is perfect for any project that needs to stand the test of time, whether it’s a high-traffic interior floor area like at an airport or a library or school. It’s also a lot more energy-efficient than steel or glass, and it won’t get damaged by de-icing in winter. Marquis says granite paving will essentially last forever, or until you want to change the look of a space.
- Designed by Valode & Pistre, the Grande Arche de la Défense in Paris uses Polycor’s Bethel White® granite, the whitest granite available on the market. Photo courtesy of Polycor
- The Ritz Carlton in Chicago features some of the most iconic marble, Polycor’s Georgia Marble in Pearl Grey, both inside and out. Photo courtesy of Polycor
6. Polycor’s stone is responsibly sourced.
Know where your stone is coming from. Many people don’t realize there are quarries right in their backyard, from Georgia to Vermont. Not only does that reduce emissions when you specify a product close to home, but you can also know precisely how the stone is extracted.
Marquis says the industry has had an issue with child and slave labor overseas, and it’s vital to educate architects. “You have to understand where the stone is coming from,” he says. “Many years ago people started drinking organic Fair Trade coffee, and now it’s common for people to ask for such a product, but there’s an equivalent in the natural stone industry when it comes to where the product is coming from and the working conditions of the people who quarry the stone. When you buy local stone quarried in America or Canada it’s a Fair Trade product.”
7. Natural stone quarries are easily reclaimable.
Because the natural stone industry doesn’t use chemicals in its processes, quarries don’t require soil remediation and are easy to reclaim. “It’s a hole that will be filled when the quarry reaches its end of life, and nature will take its place because it’s not polluted,” Vega says.
Polycor’s excess stone is processed into gravel for roads, curbs, landscaping products, and even furniture. At the Tate, Georgia marble quarry (a zero excess process material quarry), even stone dust is recycled into aggregate for Vetrazzo recycled glass countertops. The natural stone extraction process has little excess material because the stone is close to the surface. That’s a lot different from mining, where large amounts of earth must be removed to extract a small amount of minerals, and the excess turns into contaminated waste.