Story at a glance:
- Oriented strand board (OSB) is an engineered wood material often used as sheathing.
- The high cost of OSB and its moisture susceptibility might make other solutions more attractive to builders and architects.
- An OSB alternative like fiberboard, CDX plywood, rigid foam insulation, diagonal tongue-and-groove planks, or fiberglass-faced gypsum board come with varying benefits.
Oriented strand board (OSB) is commonly used in place of plywood as a sheathing material for walls, roofs, and subfloors. But rising demand, steadily increasing prices, and only an average resistance to moisture means builders and architects may want to consider an OSB alternative.
In this article we’ll explore the pros and cons of five common alternatives to OSB and provide some insight as to which is better in certain contexts.
What is OSB?
OSB is engineered wood that is created when small wood strands or chips are bonded together with adhesive resin and glue. These wood strands are arranged in cross-oriented layers, giving OSB its name. OSB panels come in a variety of sizes, types, and thicknesses. OSB is also known for being especially durable and strong—important qualities when it comes to a building’s structural support.
OSB was originally created in the 1960s as an alternative to conventional plywood, a similar product manufactured by cutting thin sheets of wood from a spinning log and gluing them together. OSB started gaining popularity in the 1970s when plywood production declined due to a shortage of suitable mature timber—something the OSB market wasn’t affected by, as the material can be made from smaller, younger trees than plywood. By the 1980s OSB had cemented itself as a leading structural sheathing material.
Today OSB remains a popular sheathing material that helps give buildings their structural integrity and provides a surface for fastening siding materials, as it does not strip easily and holds screws well. OSB also offers important insulation and thermal properties, characteristics that make it the material of choice for structural insulated panels.
Why Consider an OSB Alternative
When builders first began using OSB regularly, it set records for new product adoption in North America, with 751 million square feet used in the 1980s to a staggering 7.6 billion square feet in 1990. Since then OSB popularity has continued to grow. Today the OSB market has an expected compound annual growth rate of 9.5% from 2022 to 2028. And with high demand comes higher prices.
Other than rising costs, OSB can be susceptible to moisture. Although it does absorb water slower than plywood, OSB also dries slower, which can ultimately lead to fungi, wood rot, and mold as well as warping and swelling that inhibits the material from returning to its original shape. Builders might also consider an OSB alternative because the resins used to create OSB can include and emit low levels of formaldehyde, which can cause health issues for occupants—including breathing problems and irritation to the eyes, nose, throat, and skin.
From a design perspective OSB is also notably challenging to paint because it lacks a smooth texture and, due its wood strand composition, can absorb paint.
5 of the Top OSB Alternatives
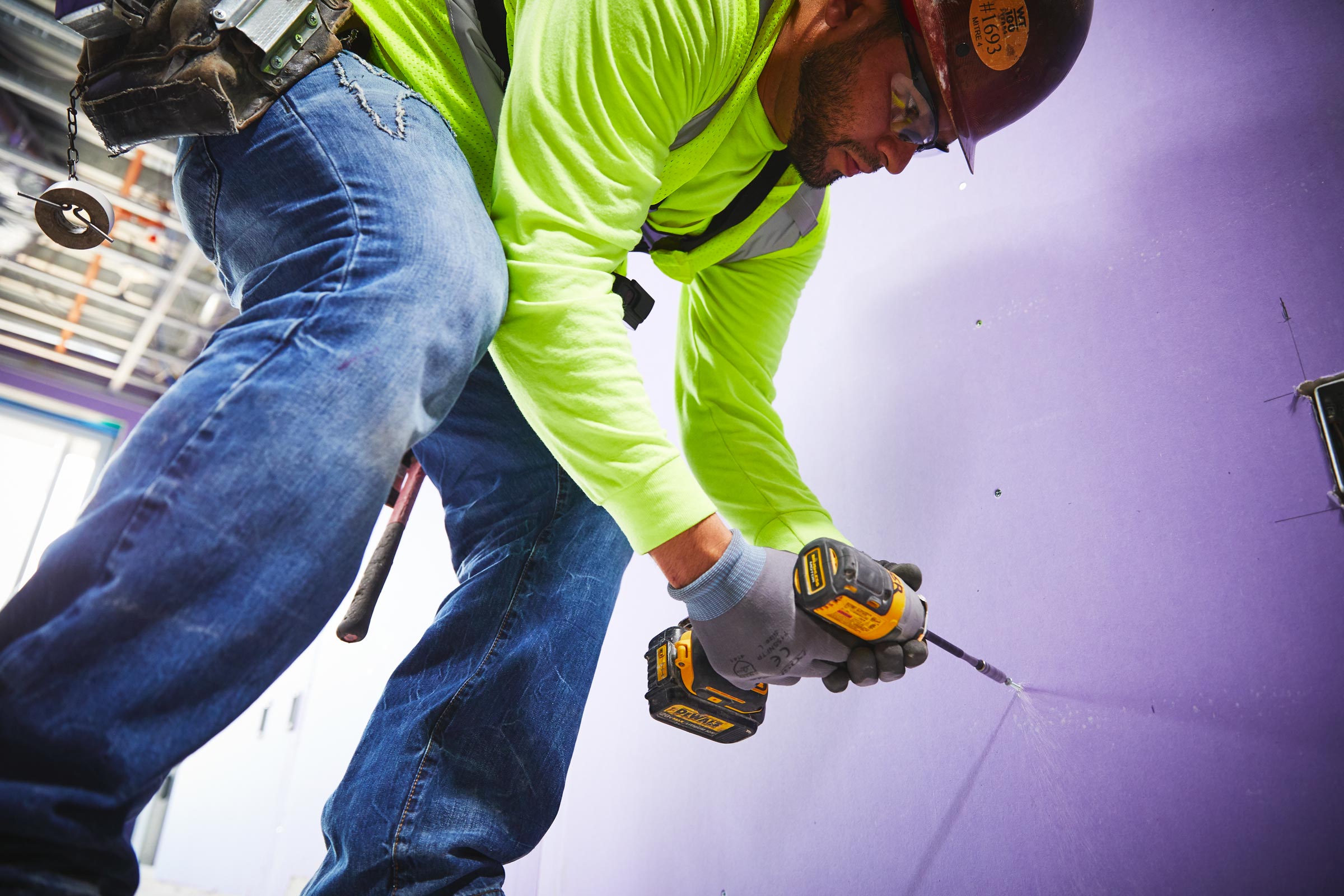
Fiberglass-faced gypsum board is a top-tier alternative to OSB, providing both better moisture- and fire-resistance. Photo courtesy of National Gypsum
When it comes to finding an OSB alternative, these five options are comparable building materials fit for a variety of projects.
1. CDX Plywood
OSB has gained considerable popularity over the last several decades as a top-tier sheathing material, but there’s a reason plywood sheathing—and especially CDX plywood sheathing—is still in use. CDX is a fairly inexpensive type of plywood made by gluing at least three thin sheets of low-grade C- and D-rated wood veneers together, with one of each facing out on either side.
The “X” in CDX refers to the way in which the veneers are actually glued together and signifies exposure, meaning CDX is relatively water-resistant and can withstand a limited amount of moisture before it starts to show signs of damage. During the gluing process, manufacturers position the wood grain elements of the plywood in such a manner as to reduce shrinkage and prevent warping.
CDX plywood can be pressure-treated to improve its durability and water/pest resistance. This is done by soaking the wood in targeted chemicals and subjecting the panels to high pressure, which in turn forces the chemicals deep into the wood. Like any wood product, however, it is recommended that CDX plywood sheathing be covered with an air and moisture barrier to drastically reduce the likelihood of moisture intrusion.
Despite being one of the cheaper plywood varieties, CDX plywood is still more expensive on average than OSB, although it is typically lighter, easier to work with, and holds nails/screws better.
2. Rigid Foam Insulation
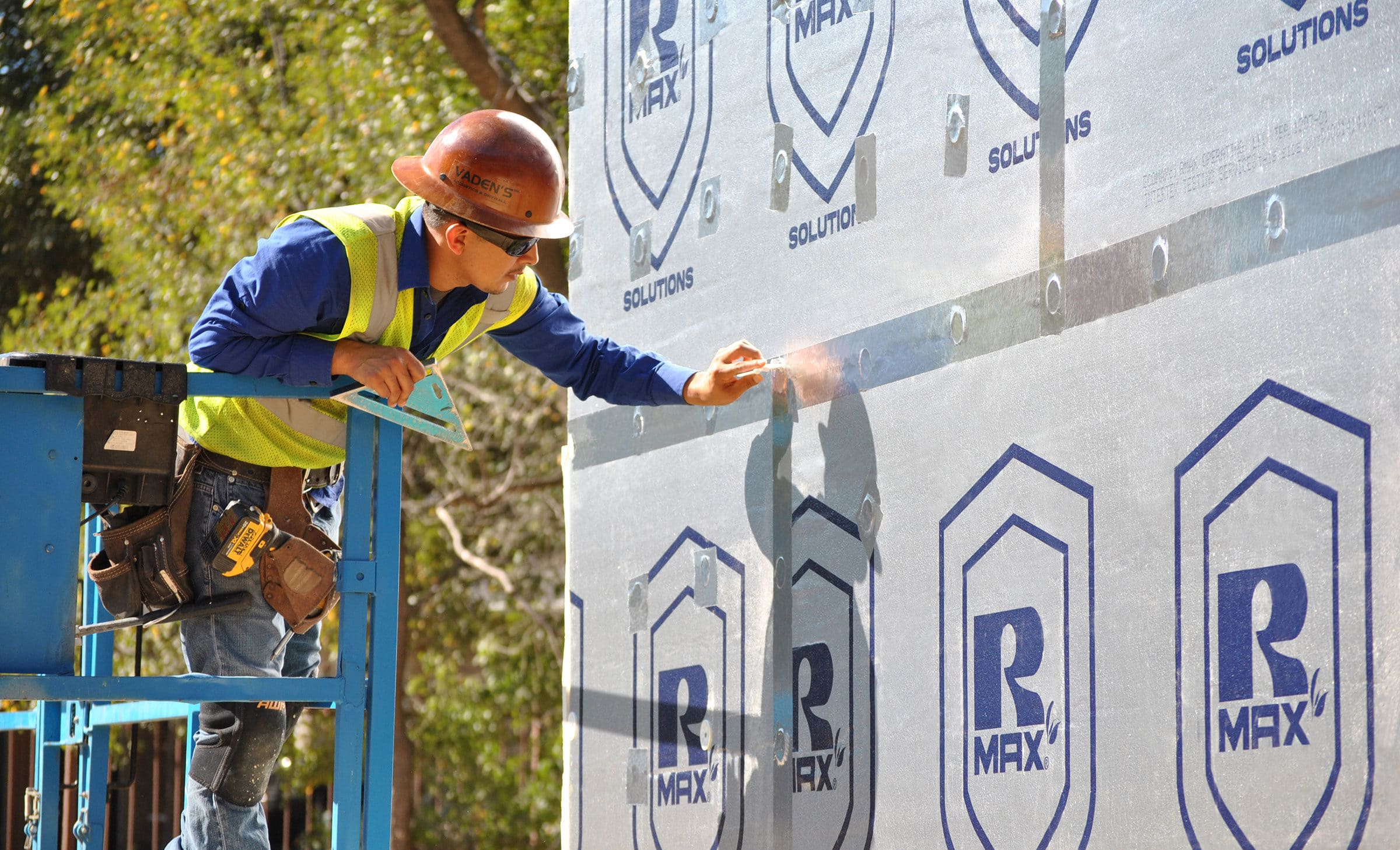
Polyiso rigid foam sheathing provides greater thermal protection than OSB. Photo courtesy of Rmax
Also known as rigid foam sheathing, rigid foam insulation is a continuous plastic foam that provides maximum thermal efficiency, as the absence of any gaps, holes, or leaks in the material itself can prevent air leaks, better control indoor temperatures, and help reduce a building’s energy use. Like fiberboard, rigid foam insulation also comes at a lower price point than OSB, helping to reduce construction costs.
Rigid foam insulation also creates a strong barrier against moisture and comes in a variety of thicknesses. However, it is less stable than OSB and may require additional bracing. If you’re building a residential or commercial project in an area with high wind, you may want to consider an OSB alternative that provides greater structural strength. Additionally, rigid foam sheathing cannot withstand direct sunlight and will require proper siding for protection.
There are three main types of rigid foam insulation—extruded polystyrene (XPS), expanded polystyrene (EPS), and polyisocyanurate (PIR/Polyiso)—each of which varies slightly in terms of R-value.
- Extruded polystyrene. XPS is a strong, lightweight, and water-absorption-resistant type of closed-cell rigid foam insulation that typically possesses an average R-value of R5 per inch.
- Expanded polystyrene. EPS rigid foam boards are very similar to XPS foam boards but are lighter, thicker, and have an average R-value of R4 per inch.
- Polyisocyanurate. PIR is a kind of thermoset plastic insulation produced as a closed-cell, rigid, continuous foam board; PIR has one of the highest R-values on the market and averages between R6 and R6.5 per inch.
Thanks to its top-tier thermal qualities, polyiso is typically considered to among the best rigid foam sheathing, suitable for both roof and wall applications. Polyiso boards can also be made extremely moisture-resistant through the addition of foil facers. “Not only do foil facers make polyiso a flexible material, capable of acting as both insulation and air and water barrier for roofing and wall applications, but they also reduce redundant materials like exterior gypsum and other air and water barrier membranes, cutting costs and shrinking a project’s overall environmental footprint,” Laurie Hill, technical vice president at Rmax, previously wrote for gb&d.
Rmax is one of North America’s leading providers of polyiso insulation solutions and offers a range of products for both above- and below-grade applications.
3. Fiberboard
Like OSB, structural fiberboard is an engineered wood material. Where OSB is made using strands of wood, however, fiberboard is created when wood fibers are pressed and glued together. Fiberboard comes in three densities: low-density fiberboard (LDF), also known as particle board; medium-density fiberboard (MDF); and high-density fiberboard (HDF), also referred to as hardboard.
- LDF. Particle board is manufactured from wood chips and a synthetic resin binder or some other suitable binding agent, of which is then pressed and extruded; LDF is denser and cheaper than plywood, but is the weakest type of fiberboard.
- MDF. A combination of separated wood fiber, wax, and a resin binder that is formed into panels by applying extreme temperature and pressure; boasts a higher density and strength than LDF.
- HDF. Similar to LDF and MDF but is much denser, stronger, and harder than both because it is made from exploded wood fibers that have highly compressed; the nature of hardboard means that no additional adhesive is required to bond the wood fibers together, though resin is often added.
Because both materials are manufactured using wood fibers, fiberboard more-or-less matches OSB in durability, though it isn’t as strong. Fiberboard also makes a great OSB alternative because it is easily accessible and comes at a relatively low cost.
4. Fiberglass-faced Gypsum Board
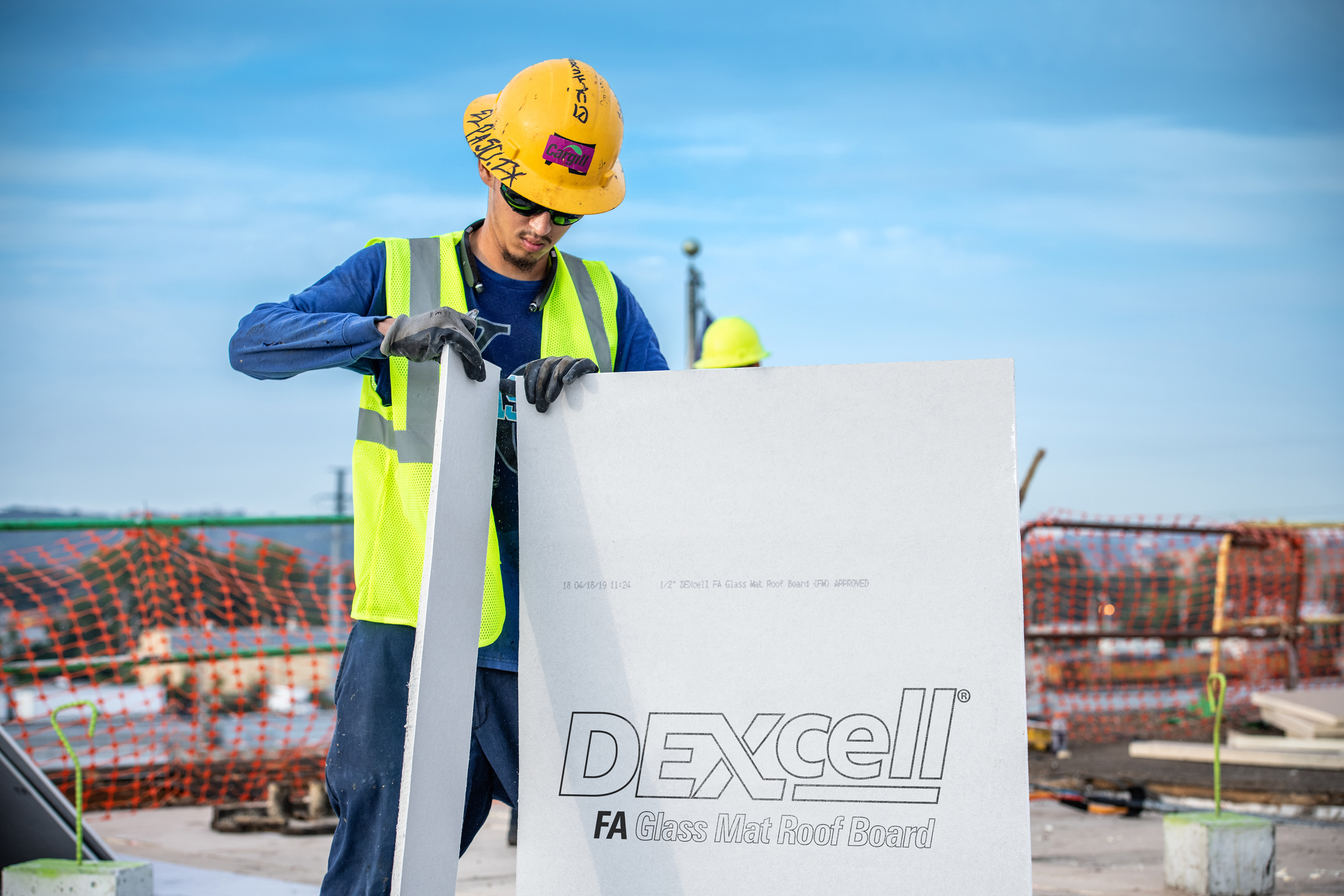
Photo courtesy of National Gypsum
Fiberglass-faced gypsum board is made up of a noncombustible interior panel with a fiberglass-reinforced gypsum core and coated fiberglass mat face. The fiberglass makes the panels highly moisture- and mold-resistant, and the material is also more stable and durable compared to other OSB alternatives. Because of its structural integrity, fiberglass-faced gypsum board can also withstand tough weather conditions.
National Gypsum Company is one of the US’ leading suppliers of gypsum board and drywall products. “Our eXP Sheathing is used on outside walls or soffit framing as a substrate for exterior cladding,” Matt Gallagher, gypsum systems product manager for National Gypsum, told gb&d in a previous interview. “Its gypsum core offers a dimensionally stable base to build high-performance exterior walls, and its PURPLE fiberglass mat encases the face, back, and sides to reinforce and protect the core, providing superior weather resistance.”
Although fiberglass-faced gypsum board is cheaper than OSB, it can be more expensive than fiberboard and rigid foam insulation.
5. Diagonal Tongue-and-Groove Boards
While not particularly common today, diagonal tongue-and-groove sheathing was the industry standard prior to World War II and can be found underneath the cladding of many older buildings. Traditionally made from solid pine planks, diagonal tongue-and-groove sheathing came about in the mid-1800s with the introduction of balloon framing, which saw the need for a more efficient way of bracing walls.
Diagonal tongue-and-groove wood planks act as a diaphragm—or a planar structural element that is loaded in its strong direction, in-plane—just as modern plywood or OSB functions as a lateral-load diaphragm. When used as wall sheathing these planks tie the header to the footer and connect the studs to one another, effectively forming strong braces that deliver extremely high structural strength.
Like CDX plywood, solid wood sheathing planks also provide a very strong fastening surface and hold nails/screws better than OSB. Another benefit of diagonal tongue-and-groove sheathing is that the boards are much easier for smaller construction teams to work with compared to large OSB panels.
The main drawback of diagonal tongue-and-groove sheathing, however, is its price. Because it uses solid wood planks instead of engineered wood panels, it tends to cost more overall than plywood or OSB.
Which OSB Alternative Should You Choose?
Now that you understand the benefits of an OSB alternative and the options available, it’s time to decide which solution will work best for your project.
One of the most important factors is the location of the building and its climate. Projects in areas with high wind should include a strong OSB alternative that provides greater structural integrity, such as medium/high-density fiberboard, fiberglass-faced gypsum board, or diagonal tongue-and-groove boards. Meanwhile, projects in wetter climates should opt for moisture-resistant solutions, which includes rigid foam insulation, CDX plywood, and fiberglass-faced gypsum board.
If energy efficiency is a main goal of your project, however, rigid foam insulation is likely to be a top choice, particularly polyiso rigid foam panels. And where cost is concerned, fiberboard and rigid foam insulation are typically less expensive, while fiberglass-faced gypsum boards and diagonal tongue-and-groove solid wood sheathing can carry a higher price point.
At the end of the day, builders and architects looking for an OSB alternative have a few options that all come with comparable benefits. The right solution for you will ultimately come down to your project’s goals and needs—and your budget.
Sophia Conforti contributed to this article.