Story at a glance:
- An estimated 40% of a building’s energy loss (heating and cooling) is through air leakage.
- Aeroseal’s air sealing technology is in more than 200,000 homes and more than 10,000 commercial buildings.
- Aeroseal’s technology seals from the inside out, providing a 90%-plus reduction in leakage in a home or building.
Many homes and commercial buildings are not as energy-efficient as you think. You may wonder why your own energy bills are so high, maybe you blame the energy provider for high rates. But your system could be leaking air like water running through a sieve. And you’re paying for it.
A central heating and cooling system has ductwork throughout a home or building, but much of it is inside walls, so if there is a leak caused by a hole or tear in the ductwork, it is almost impossible to fix because it’s difficult to find. It could be as small as a pinhole; and even if it could be found, it often couldn’t be reached without the expense and disruption of opening up a wall or ceiling.
In the past when leakage sites were found, the only way to seal them was to patch the exterior with industrial tape or mastic material. More often than not, however, leaks would persist for years without anyone being aware of their existence, let alone repairing them. To compensate for lost energy HVAC systems run significantly longer than necessary, resulting in higher heating and cooling costs.
“Forty percent of a building’s energy loss is through leakage, so it’s a big part of global warming,” says Bob Swilik, vice president of product strategy at Aeroseal. “We have a product that can fix the leakage quickly and easily without large lead times. The work we do has a big impact on the building’s efficiency.”
We recently sat down with Swilik to discuss how Aeroseal’s air sealing technologies solve this problem, both reducing both leakage and cost.
When did duct leakage start to gain awareness?
- Photo courtesy of Aeroseal
- Photo courtesy of Aeroseal
From the ’60s to the pre-1990s energy was cheap. And because it was cheap people didn’t care about energy efficiency that much, so ductwork was made without sealing it tight. At this time specific energy codes for ductwork were absent even while general building energy codes existed. Today it’s well understood and documented that leaky ductwork wastes a lot of energy.
When the industry started to develop the knowledge that we needed energy efficiency for the environment, that led to the realization that we needed to seal up leaking ductwork. But the process was next to impossible because ductwork was in between walls, running across joists, or in areas where you literally could not get to the leak.
How do you evaluate leakage and energy loss?
Typically if it’s an older home it’s almost guaranteed to have leakage in it. We find that on average the leakage is about 20%.
A home without properly sealed ductwork can get uneven temperatures throughout the home. Your upstairs temperature can be too hot or too cold compared with the downstairs because the duct system is not working as it is designed to. You end up with less airflow on longer duct runs due to leakage. And you can get a lot of dust because you’re pulling in air from the outside, the attic, and crawl spaces, and that’s all blowing throughout the house. Uneven temperatures and excessive dust are telltale signs that you have a duct problem. And of course you will likely have high energy bills. That’s another indication.
Also, in addition to uneven temperatures, there’s also the issue of velocity—the force at which the air is coming out of the register. Leakage causes less force and less air to come out of the register. Then that air is picking up unwanted heating or cooling as it goes along. So it comes out at a temperature lower or higher than it should be.
How does Aeroseal’s technology solve that problem?
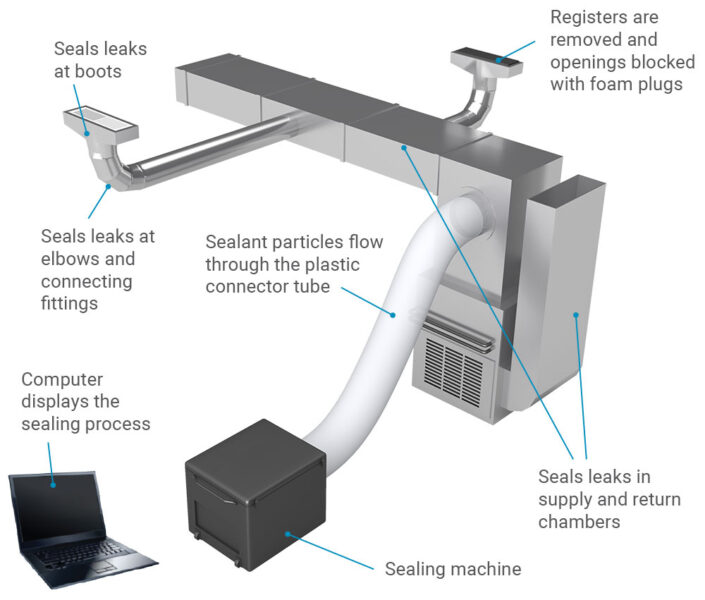
Illustration courtesy of Aeroseal
Aeroseal employs a fog-like aerosol substance that, when introduced into ductwork and pressurized, effectively seals leaks from the inside without the need for external interventions. This innovative approach eliminates the necessity for wall alterations, demolition, or construction work. It is a straightforward and convenient solution suitable for both residential and commercial applications. Aeroseal minimizes the need for extensive labor and complies with all prevailing energy efficiency standards.
We have three applications. One is to seal the envelope (or outer shell) of a house. We typically do that in new construction. The second is to seal the inside of the ductwork of central heating and cooling systems throughout the house. And the third application is to do the same in commercial buildings.
The technology used in a residential and a commercial environment is the same, but the applications are vastly different. With commercial applications you have a lot more variables with dampers and fresh air returns. Residential and commercial is also done at the new construction stage, and they have requirements that you have to seal to a certain percentage of air flow.
We test the leakage at the start and come up with a leakage percentage. Then we run the same test after the ductwork is sealed to show the difference and the value we’ve created through our air sealing process.
On the commercial side, for existing buildings, we’ll come out first and do an audit of the system and tell you how much leakage there is, and we’ll guarantee the amount of leakage we’re going to seal for you. Then we will come out and seal the ductwork. We have zero lead time. As long as we have the capacity in the area, we can respond very quickly.
What happens during installation?

Photo courtesy of Aeroseal
First we block off all the registers in the house to pressurize the system and measure how much air gets out at a certain pressure. Then we know how much leakage is in that system.
After we pressurize the system we inject it with the aerosolized sealant—essentially a fog of sealant. That sealant finds all the little cracks and holes and fills them up. After we’re done we measure pressure and leakage again, the same way we did when we started, and we look at the difference between the starting and ending point. The difference is usually in the neighborhood of more than 90%.
How does air sealing technology help with electrification?
Today there are a lot of places that want to shift from gas to electricity—known as electrification. But in a residential application some people are very nervous about whether the heat pump will be able to keep up with the load. A lot of times you’ll get colder air blowing out of a heat pump and the temperatures coming out of the registers are not as hot as a gas furnace. It makes people a little bit uncomfortable.
When you seal the ductwork you now have a higher velocity in the ductwork so the temperatures coming out of the registers are a lot higher. That makes the heat pump more comfortable, which in turn alleviates the fear of going from gas to electricity. Also, because we lower the energy load of the house, you’re lowering the amount of work the pump has to do, especially backup heat, and you’re saving money.
Does your system work with solar?
Yes, solar is a big part of our application. Solar companies will use us to lower the load so you don’t need as many panels, or you can sell that electricity back to the electric company.
What is the return on investment?
Payback is generally five to seven years, but it depends on where you are geographically and what you’re currently paying for electricity. The average leakage reduction is 90%. For homes with electricity and heat pumps, it can reduce the whole house’s electricity by up to 15%. In a commercial environment you’ll see a reduction in electricity of between 2 and 10%.
What happens after you leave?
When we’re done we have a certificate that shows where the leakage was when we started, how it dropped as we were going through it, and then the leakage at the end to show the customer exactly what we did.
In the case of commercial we also show them how it saved money. Both their engineers and ours will have agreed on the calculations and everything beforehand so we guarantee we did what we said we were going to do. Our process is guaranteed for 10 years in residential applications, although we’ve tested it to 40-plus years. And there’s no maintenance necessary. Once it’s sealed, it’s sealed.
For new construction homes we help contractors achieve ENERGY STAR levels more easily. In the new construction envelope space we definitely get points and credit for sealing up the house.
On the commercial side we were an integral part of LEED certification achievement for both a new housing development in Cambridge, Massachusetts and a very large university based in Ohio.
What is the future of this technology?
We believe the future is going to net zero, and we think we are going to be a very big part of that. We’re worldwide, and there are buildings all over that can use our services. In fact, we’ve recently gotten some funding to grow and become bigger to scale the product and the process.
We also believe new homes, not only with the duct side, but with the envelope side, over time will start to migrate to passive home standards. As they move to become passive homes, the need to seal the envelope will become greater and greater. We think sealing technology will automatically become part of every new construction build and every HVAC change out, both commercial and residential. For these systems to work effectively and efficiently, there is going to be more need for our product to help meet that demand.