Story at a glance:
- Off-site manufactured and assembled exterior wall systems reduce construction time by as much as 50%.
- Recent improvements in thermal breaks improve building energy performance, consistent with other energy savings and waste reduction in the manufacturing and assembly process.
- Building contractors, owners, and architects increasingly choose modular systems due to the multiple cost- and energy-saving benefits, logistical simplification, and reduction in on-site labor requirements.
Modular construction—components of structures manufactured and assembled off-site—has a surprisingly long history, but new demands on building delivery and performance make it an important method in present-day construction.
Examples of modular buildings stretch back to the 17th century when American settlers disassembled homes shipped from England and reassembled them in the New World. Later, 19th century miners in California had simple homes sent from the East to West Coast. In post-World War II America, manufacturers pivoted from making aircraft to prefabricating aluminum and steel homes for returning veterans, although only a few thousand were ultimately built.
For a while the technique was somewhat dismissed, but today’s prefabs are nothing like the modular buildings of old. Today, 21st century companies with a long history of innovating, like Kawneer—a Georgia-based manufacturer of architectural aluminum systems and products—are jumping on the burgeoning trend toward off-site, modular systems. Why? Because modular building systems are smarter, faster, and greener.
Kawneer is not new to modular solutions. The company has made unitized curtain wall, storefront, and modular window products for decades. But its systems incorporate more parts, accommodating the increasing complexity of contemporary building design—right angles are a little harder to come by in mid- and high-rise commercial structures—as well as the urgencies of climate change and sustainability, which place greater demands on building energy performance. The challenges of a tight labor market are also driving the more efficient off-site assembly of building parts.
Chris Keller, market segment manager at Kawneer, works with the new applications for its products. He recently shared some of his experience in this evolution of Kawneer, its methodologies, and what it means to the marketplace.
What is a modular wall system, and what is Kawneer’s role in it?
- Photo courtesy of Kawneer
- Photo courtesy of Kawneer
Simply put, these are prefabricated wall systems that are made in a factory before they are shipped to the project site. More specifically, the walls are constructed with metal studs, roll-formed steel, between six and eight inches deep, with openings for external finishes, insulation, electrical and plumbing, and space for the windows.
These are known in the construction industry as “light walls,” as they weigh about 10 pounds per square foot. Compare that to pre-cast concrete walls, which can be around 80 pounds per square foot.
The select group of customers are pre-fabricated panel manufacturers. In addition, we consult with architects concerning the design and general contractors with logistics.
Modular systems have been around for a while. What’s new about them today?
The biggest change in the last five years or so is the upgrading in thermal performance. Aluminum is an efficient conductor of heat, which is not what is wanted, so we’ve incorporated thermal break technology into the glazing systems. This is driven of course by more stringent building codes—which vary by region, by municipality, and by customers. College campuses, for example, may have much more demanding sustainability requirements, and we are able to serve them.
But product features go beyond this one factor. Prefabricated walls are designed and built systems for the challenges in different regions. For example, the wall and glass system must withstand hurricane force winds for projects in coastal regions and seismic activity in regions where that is more common.
Are there examples of modular-built structures that use Kawneer products?
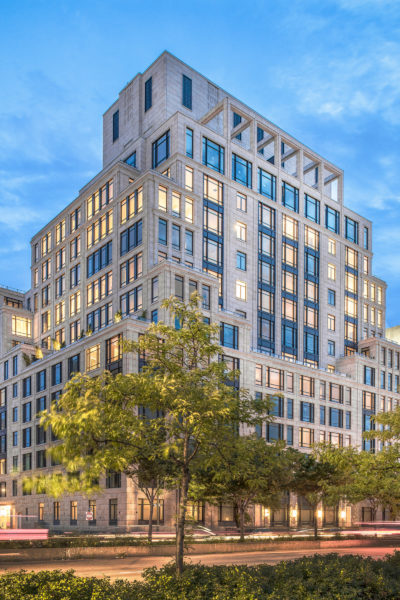
70 Vestry. Photo courtesy of Kawneer
Yes, two multifamily buildings in two cities use Kawneer windows in precast concrete wall components. One is 70 Vestry—luxury condominiums on 14 floors in the Tribeca neighborhood on the Hudson River in New York City.
The other is Eleven on the River, a 41-story luxe condominium tower in Minneapolis. Both developments were designed by Robert A.M. Stern Architects.
What defines excellence in a modular component from the company?
The controls of building off-site in climate-controlled circumstances (indoors) enable a better and more consistent product.
We are able to pre-test for air and water leakage, structural integrity, thermal properties, and acoustical performance. All components must meet the operational guidelines of the American Architectural Manufacturing Association, which we document in a report to customers. The organization represents window, door, skylight, curtain wall, and storefront manufacturers and suppliers.
A purported benefit of modular construction is waste reduction, which of course has a sustainability benefit. Tell us about that.
From a materials management standpoint, modular construction reduces waste by about 10%. There is less breakage or other damage to the products and less packaging material used. The fabricator can recycle materials better and experience better overall economies of scale.
The challenges created by rain, cold winter temperatures, and hot summer temperatures from the construction site, all of which can impede the construction cycle, are removed. This has a significant impact on quality control and shortens the duration of the construction process, bringing earlier revenues to the building owner.
It is also a benefit to the workers, who can commute to the manufacturing location instead of a construction site, which can be a very long commute. This is a quality of life improvement for tradespeople.
How do you interact with the building architects and the design process? Is there an educational process?
To be clear, modular construction has little impact on the design of the building. We sometimes have a conversation on the details around joints, but in general that’s a greater concern to the general contractor and owner because of the importance of preventing leakage. But we are part of the design process; we get involved before simply providing a quote on the work. We meet early in the planning phase with the architect, the panel manufacturer, and the general contractor to discuss the modular approach.
For the customer who is new to modular panel systems, this is a big change, both in how to work with it and how to quote it. The people who do not understand or want to work with modular systems might be left behind if they don’t adapt.
Every building of size has some problems, including leaks. What’s the experience with modular wall systems?
While it’s true that many buildings initially have some leaks, it’s generally due to installation issues rather than design. But in modular off-site assembly, we can test windows and walls independently, as well as in units, to address leaks before we ship the product. This gives the panel manufacturer the ability to provide a single warranty to cover the whole wall system.
Market demand for off-site modular construction is on the upswing. How fast is it growing?
We are experiencing more than 50% growth in 2021. Customers recognize the speed in construction that is possible with this system. They also see there’s greater on-site safety, less waste, and even less energy used on-site to buffer against weather—for example, heaters required in winter construction.
Given that many of these large-scale projects are in urban environments, customers appreciate how this reduces deliveries in congested areas by as much as 90%.