Story at a glance:
- HQ2 is 100% powered by renewable energy and sees a 24% overall energy savings relative to a comparable new office building—enough electricity to power 572 homes in the US every year.
- The project achieves a 20% reduction in the carbon footprint of Met Park’s concrete structures compared to the industry baseline—saving more than 14,700 metric tons of carbon—or the equivalent of taking more than 3,200 cars off the road in the US for a year.
- ZGF worked with Amazon, JBG Smith, and Clark Construction to plan, design, and deliver HQ2, which is targeting LEED Platinum.
Low-carbon concrete, mass timber, electrified energy-efficient operations, advanced water reuse, and two acres of landscaped roofs with native plants—these are some of the strategies that add up to make Amazon’s “HQ2” in Arlington, Virginia, a zero operational carbon success. The Amazon campus project at Met Park does not rely on any fossil fuels for daily operation.
When Amazon set out to establish its second headquarters in Arlington, the company knew it wanted to push the boundaries of sustainability—both for its employees but also for the surrounding community, as the project includes a 2.5-acre public park and all-electric retail spaces. ZGF worked with Amazon, JBG Smith, and Clark Construction to plan, design, and deliver HQ2, ultimately establishing 2.1 million square feet of space, 50,000 square feet of retail space (emphasizing local minority and women-owned businesses), and a public park.
“As a firm ZGF has always been at the forefront of promoting sustainability and healthy buildings, and we couldn’t have been more excited about this project when Amazon came to us and wanted to push the bounds,” says Brian Earle, principal at ZGF Architects, who worked on the project. “We were designing this project as the Climate Pledge came out, and while Amazon already had pretty high sustainability standards, that took them to another level.” The Climate Pledge captures Amazon’s commitment to decarbonize its entire operations by 2040.
The Amazon team says they wanted to demonstrate the possibilities in sustainable office design while being a good neighbor. “HQ2 has been very well-received, not only by employees but the community at large,” says Jemila Campbell from Amazon Corporate Communications. “We were pleasantly surprised to see an increase in foot traffic in this region, just one year after HQ2’s opening.” The area saw 13% more visitors and $1 million spent with local small businesses, she says. “It’s great to see actual data showing folks are coming to HQ2 to enjoy the building and its amenities because we were purposeful in building this for the community.”
Since the project began, much of what the team tried and accomplished has also been incorporated into other building and design projects, says Gina Klem, Amazon’s director of workplace innovation and sustainability. “For example, the low-flow fixtures from HQ2 are now our standard. It’s the same for materials and construction waste,” she says.
“We began this project by asking ourselves and our project partners, ‘How far can we go?’ HQ2 was meant to demonstrate the art of the possible in sustainable design and construction, and we wanted to do everything that we could do.”
But takeaways like these haven’t just helped Amazon projects. They’ve educated others in the industry, too, Earle says. From the beginning he says the mega retailer wanted to achieve two major sustainability goals—to go all-electric to eliminate operational carbon from the building, and to reduce the carbon footprint of the construction. “We really focused on reducing the carbon in the concrete superstructure of the building, which is something that hadn’t been done in this market before,” Earle says.
Not only did they figure out a way to do it competitively, what they learned is now available to projects across the region. “We went from a region that had very little experience with low-carbon concrete to now all of the biggest players in the region with experts in it,” Earle says.
Reducing Carbon in Concrete
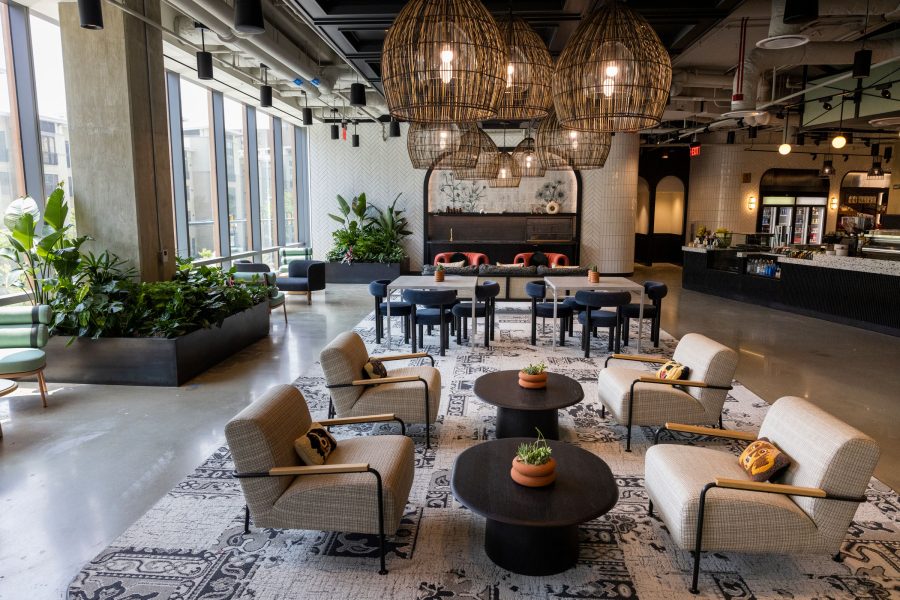
Amazon reduced the carbon footprint of its concrete structures over 20% below the industry baseline by using advanced low-carbon concrete mix design and CarbonCure technology. Photo courtesy of Amazon
It’s no secret that concrete is the largest producer of greenhouse gas emissions in the building industry. “It’s a tremendous amount,” Earle says. “Here in DC for a variety of reasons, we build almost exclusively in concrete. It has a really big impact on this area.”
Before ZGF went out to bid on the job they worked with local suppliers and contractors in the region to prepare them for what they would have to do to lower the carbon in concrete. “We basically let them chart their own path and gave them metrics they had to hit and a series of resources to help them, whether it was connecting them with suppliers or using our concrete LCA tool that allowed them to analyze the carbon impact of the concrete in real time,” Earle says.
Because of the project’s large scale, they had three of the largest concrete subcontractors bid the job. Two of them delivered the job, and the two largest suppliers of concrete in the region also both worked on the job, Earle says. Now the knowledge of low-carbon concrete is widespread.
Klem says Amazon reduced the carbon footprint of its concrete structures over 20% below the industry baseline. “We did this by using advanced low-carbon concrete mix design and CarbonCure technology, which introduces recycled carbon dioxide into fresh concrete to reduce its carbon footprint without compromising performance.”
Earle says Clark Construction, Clark Concrete, Miller and Long, and Vulcan Materials all played an essential role in delivering the low-carbon concrete on the project.
All-Electric
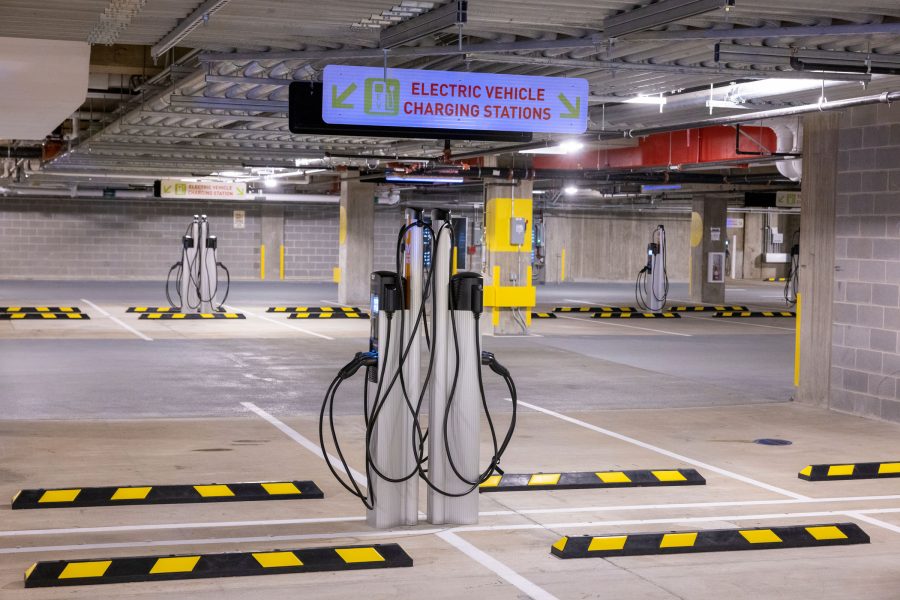
Amazon wanted to go all-electric to eliminate operational carbon from the new HQ2 building from the beginning. Photo courtesy of Amazon
In their quest to go all-electric, Amazon procured a large solar farm for 100% renewable energy for everything from the HVAC to the water heaters to the kitchens. The design team even worked with local retailers and set up a test kitchen with electric equipment to show them how it can be done and test recipes.
“That was something I don’t think had ever been done in this region at this scale,” Earle says. “That’s also paid off for other projects because we have that evidence and those projects can go talk to the retailers about how they did it. That brings a lot more confidence in the market.”
ZGF was also working on a million-square-foot, all-electric multifamily project called the Bridge District in DC, set to be complete in 2025. “It’s basically the residential version of what Amazon did here—zero carbon—and that would not have been possible if we didn’t have the test case.”
Light
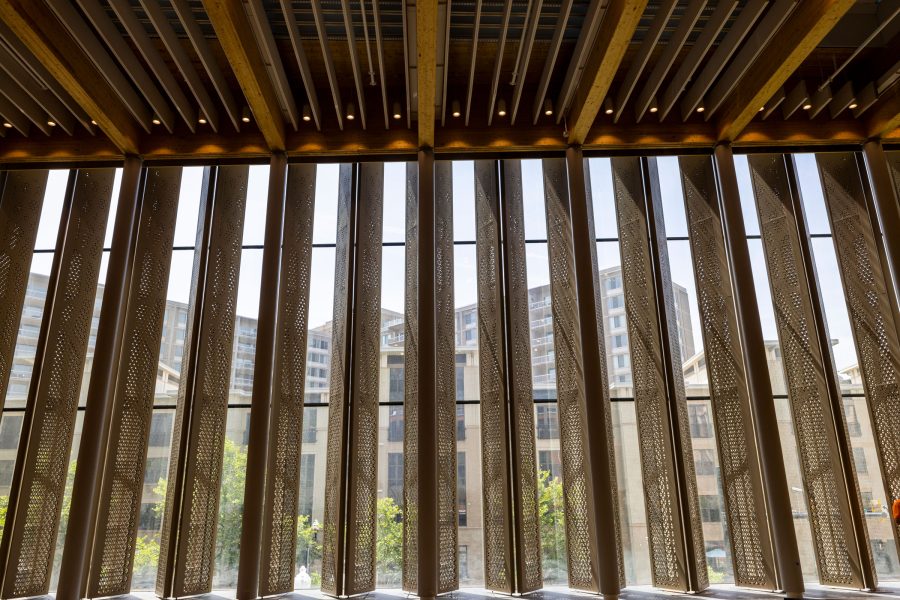
Butterfly shutters pivot automatically with the sun to allow for direct sunlight to light the space naturally and reduce glare. Photo courtesy of Amazon
Working with really big buildings, it can be difficult to get light into some spaces. This was a crucial concern both for the health of the occupants and for wayfinding, Earle says.
On the lower level a skylight helps to bring light in. The project also uses a sophisticated daylighting system from LightLouver. The series of sun shelves inside the building takes light from outside that comes in on the south, eastern, and western facade and “literally throws it deeper in the buildings,” Earle says.
Rather than the typical “daylighting autonomy” strategy of designing just for the daylight needed to do your job at maybe 20 to 25 feet into the building, the light shelves send the light up to 45 feet into the building. “So 95% of Amazon office space has natural daylight. For a building of this size, that’s really important,” Earle says. Not only do employees feel better and more productive, it’s also a key energy strategy. A high-performing envelope combined with the light shelves saved more energy and electrical demand than was lost through the 60% glass facade, Earle says. “It was a key part of how we were able to reduce the building energy demand by about 24%.”
Water
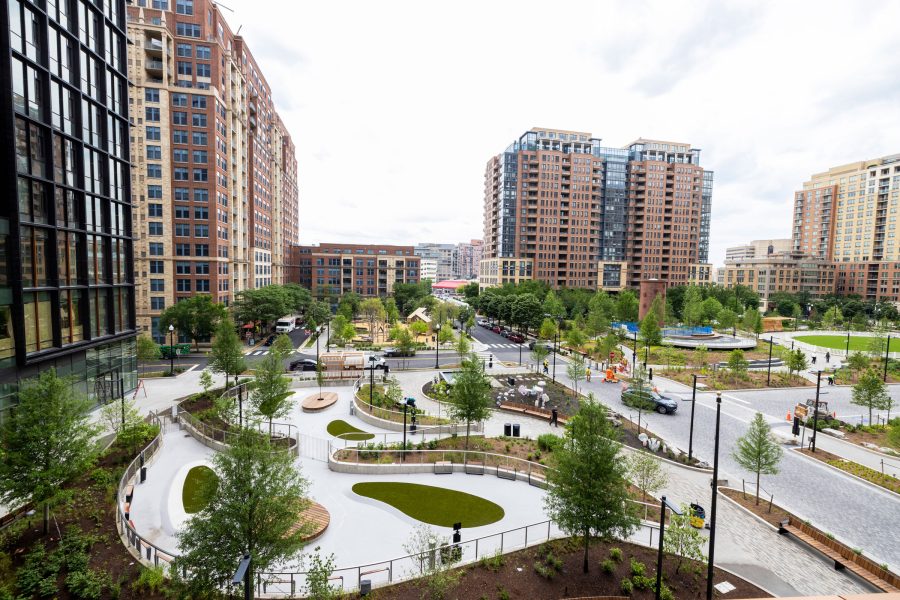
“HQ2 has several human-centric elements, including a 2.5-acre public park with a central green, hundreds of native plants, a community garden, a dog run, children’s play area, and 13 small business retailers. These features are for the community, not just Amazon’s employees,” says Gina Klem, Amazon’s director of workplace innovation and sustainability. Photo courtesy of Amazon
The project was also designed to reduce the water consumption by about 50% compared to a typical building. HQ2 collects rainwater onsite to use for the cooling tower and irrigation as well as water from showers and sinks that is treated and used to provide water for flush fixtures.
“There are a host of factors that save energy, and that’s really important here in the Chesapeake Bay region, given what an important water source that is,” Earle says. “Amazon is focused on being a good steward of that effort and making sure that they were conserving as much water as they could, and what they did use, they had as many opportunities to reuse as they could.”
Mass Timber
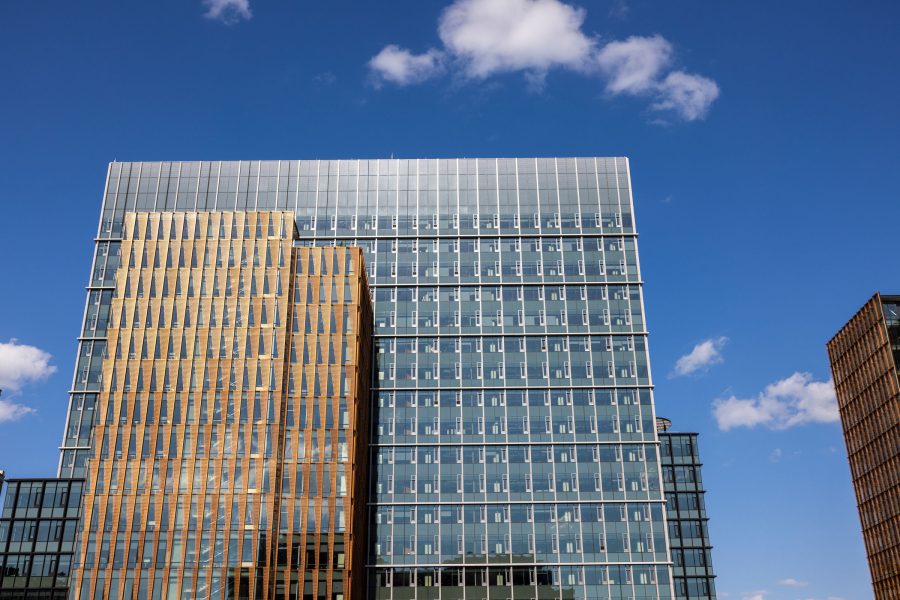
Light Louver provided the light shelves that provide natural daylight deep into the interior. Walker Glass provided the bird frit on the facade to minimize bird collisions, and Vitro provided the ultra-clear Low-E glazing on the facade for high energy performance and visible light transmittance. The project has more than 3,000 operable windows from Wausau. Photo courtesy of Amazon
Amazon’s large production venue is made with cross-laminated timber and supported by 10 70-foot-long glue-laminated timber beams. “By using structural timber we have an opportunity to expand industry knowledge of the material in the region, paving the way for more broad adoption in the future,” Klem says.
Earle says the impressive, 700-capacity space is also entirely naturally daylit with plentiful windows and skylights. Butterfly shutters pivot automatically with the sun to allow for direct sunlight to light the space naturally and reduce glare. Or it can be converted into a black box theater to host a movie screening or concert.
Biophilia
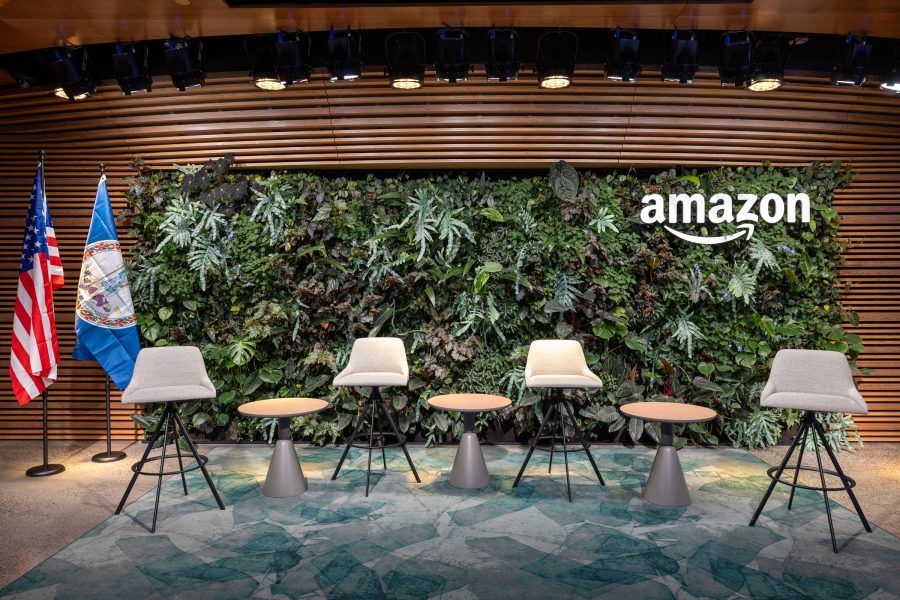
“Biophilia isn’t just natural materials and plants. It’s embracing the natural environment and the natural climate,” says Brian Earle, principal at ZGF Architects, who worked on the Amazon HQ2 project. Photo courtesy of Amazon
Outside, the large public park is programmed throughout the year, but nature also finds itself inside the headquarters, with plant-filled lobbies and natural materials across floors.
“This is something that Amazon has done for a really long time, but biophilia isn’t just natural materials and plants. It’s embracing the natural environment and the natural climate,” Earle says, pointing to features like operable windows. “The ability to open your window on a nice day and hear the city, get that breeze, and hear the birds chirping is so important.”
The project has eight occupiable terraces full of native pollinators that attract birds. “It’s just amazing, and when you’re there you can really feel that. That makes Amazonians more productive and much more excited to be in the office and to think creatively. It makes them happy and healthier.”
Klem says the team designed HQ2 to both conserve natural resources and be resilient to future climate impacts, preparing in the event of increased temperatures and droughts. “We’re using technology to reclaim and recycle water for elements like cooling towers, landscape irrigation, and flushing fixtures. Low-flow urinals, toilets, and lavatories throughout HQ2 exceed US EPA requirements by nearly one-third, which will help conserve water and energy even as the community continues to grow.”
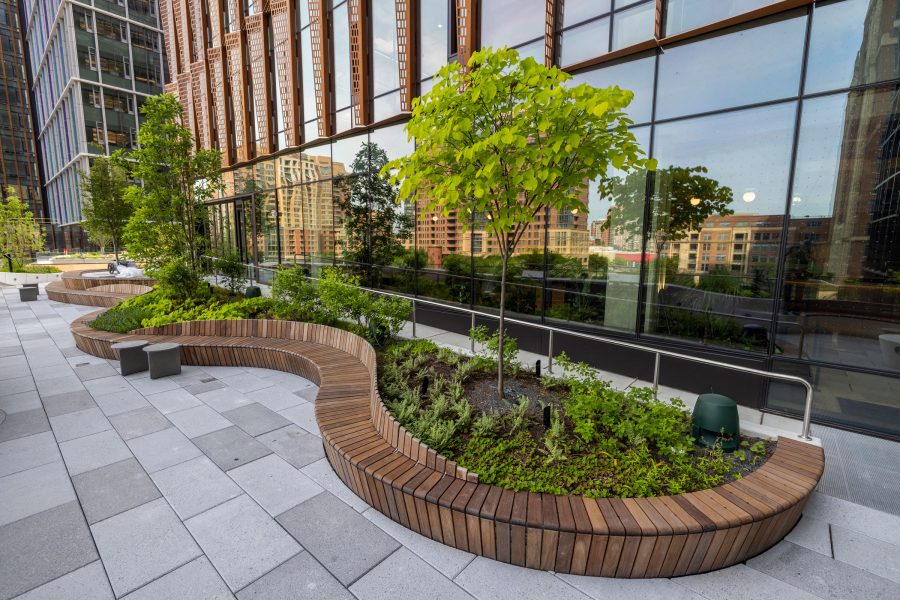
Outside, the large public park is programmed throughout the year, but nature also finds itself inside the headquarters. Photo courtesy of Amazon
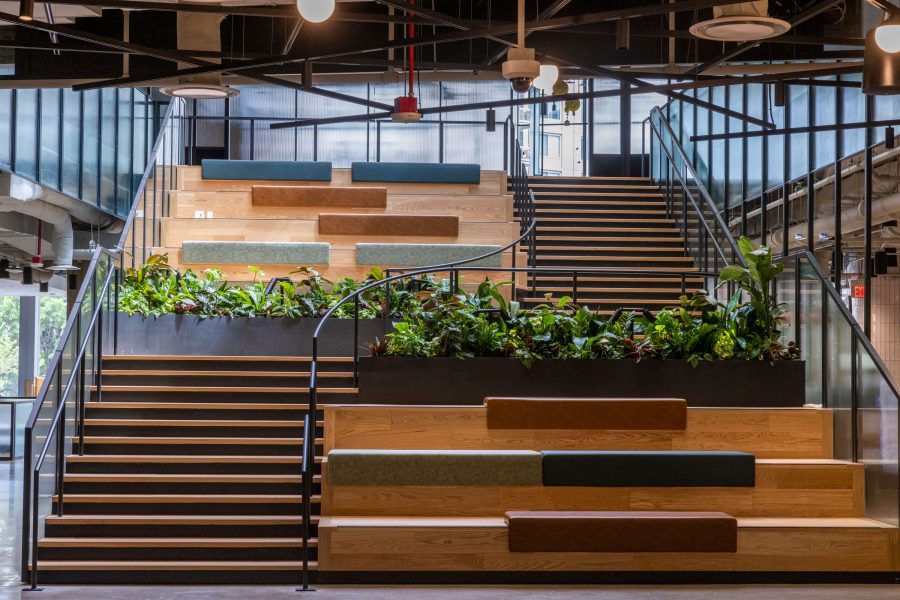
Natural materials, light, and plants fill Amazon’s new hQ2, designed by ZGF Architects. Photo courtesy of Amazon