American AutoPark solves the biggest problem in urban planning with smart parking technology.
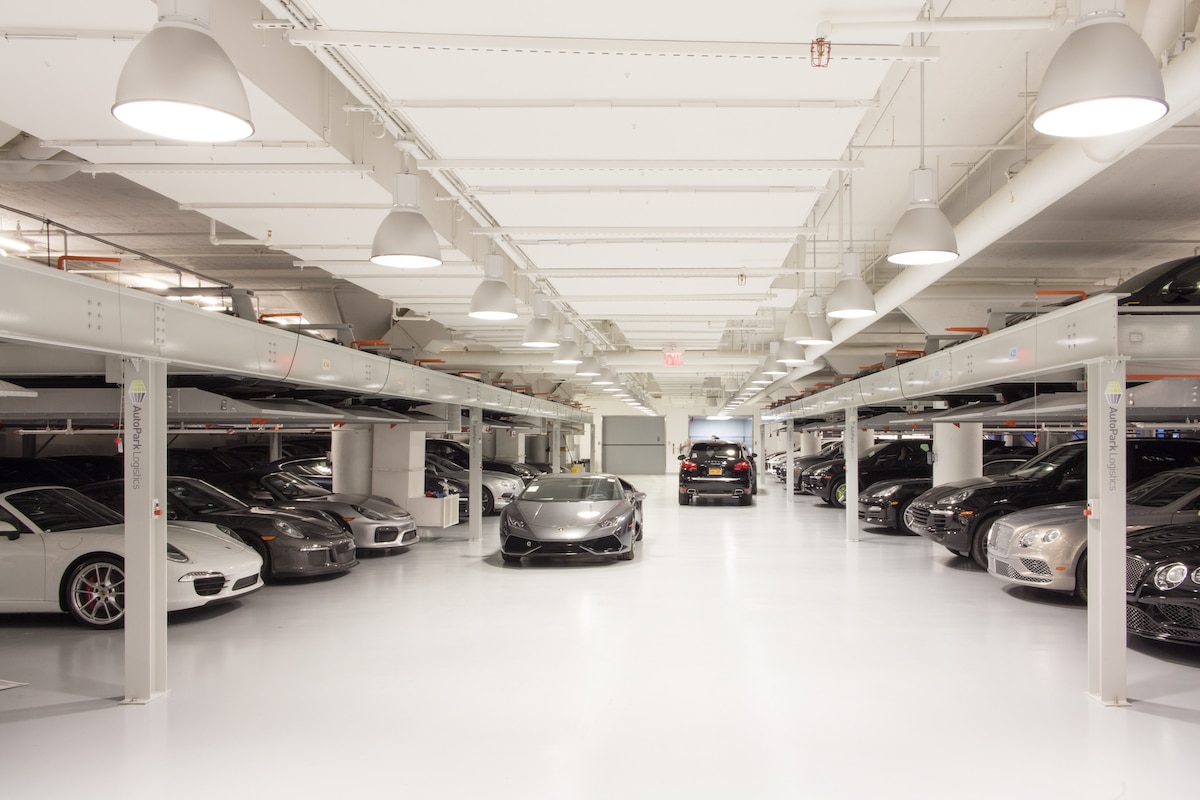
[Photo: Courtesy of American AutoPark]
By 2012 Anderes was convinced, so he formed AutoPark Logistics LLC to sell mechanical parking systems in the U.S. and Canada. His hunch paid off, and business came in faster than he could handle it. In 2016, Anderes partnered with George Wilkinson of American Car Lift to form American AutoPark LLC—a Charlotte, North Carolina–based company with a large service center in northern New Jersey that designs, manufactures, installs, and maintains valet-operated parking lifts.
American AutoPark’s ClearSpan™ valet-operated parking lifts can be customized to fit almost any existing parking lot or structure—more than doubling, sometimes tripling the number of spots in the same volume of space. The company also offers the “Lift-Slide” semi-automated parking system, allowing drivers to park their own vehicles while still maximizing space. Then there’s the AutoPark Cube—the most efficient freestanding parking garage available for high-density vehicle storage applications like auto dealers and hotels.
You can find American AutoPark’s next-generation parking solutions in hotels, hospitals, car dealerships, apartment complexes, and mixed use properties all over North America. We recently sat down with Anderes to find out more about what makes American AutoPark work.
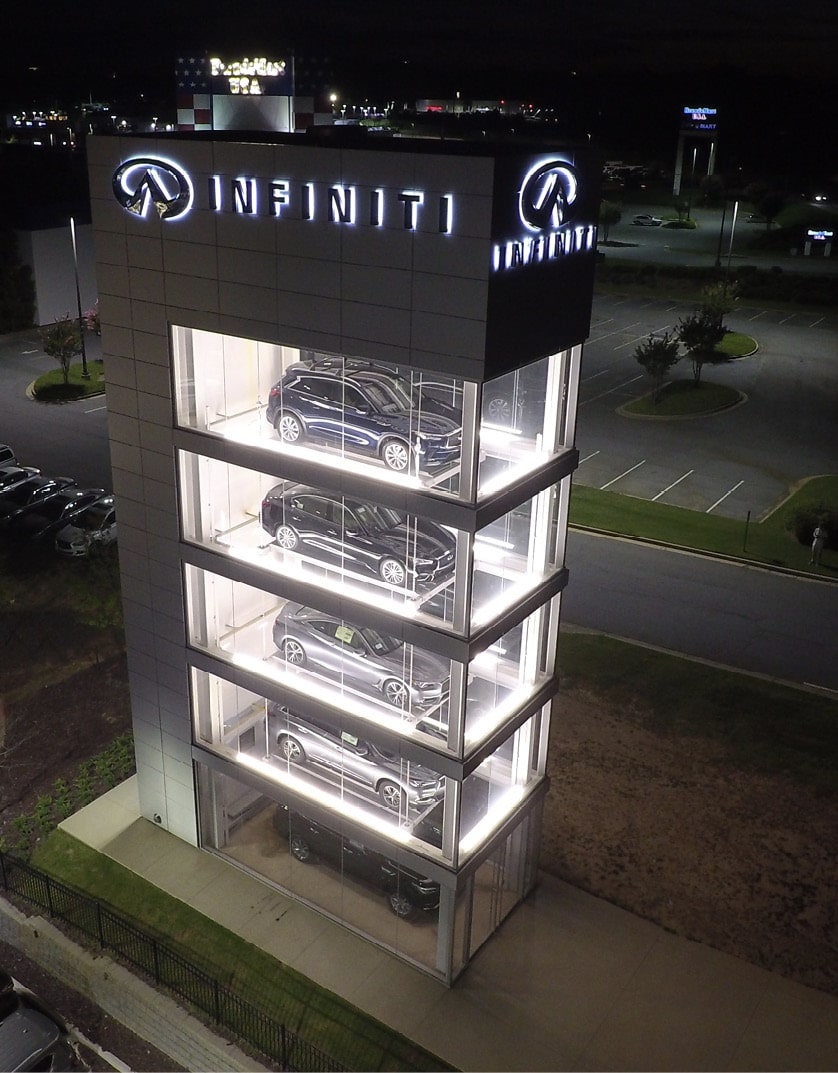
American AutoPark is transforming parking at hotels, hospitals, dealerships, and more. [Photo: Courtesy of American AutoPark]
What did your travels teach you about how other countries approach the problem of parking?
I traveled around the world and noticed overseas developers rarely built mega parking structures like we do in the U.S. Instead, they use parking machines to park the cars more efficiently. I learned that in Asia and Europe, the lack of available land for new buildings forced them to adopt automation before the U.S. did because we just built new subdivisions.
How does American AutoPark’s technology work to fix that issue?
There’s a new way to think about parking. Most architects and developers think about parking efficiency in terms of square feet, whereas we think in cubic feet. As a result, when developers look for property to develop, they only consider sites that are big enough to build a concrete garage. But our parking systems enable them to park the same number of cars in 45% of the cubic space at a cost of up to 50% less per space, so developers can now consider developing the small and irregular shaped lots they previously passed over. And most importantly, we can park the same number of cars where you couldn’t even consider typical structured parking.
What’s the biggest challenge to using AutoPark products in a project?
Since many municipalities require developers to provide parking, parking is like the “tail that wags the dog” in the development business. Since different approaches to parking use different dimensions, it’s best if a developer decides to integrate our parking lifts into their design from the beginning.
Most people think of these lifts as commodity items, and they often design the garage using “stock” CAD blocks from their CAD library. This is like me prescribing medication to my sick child solely based on what I happen to have in my medicine cabinet. While that’s quick and easy, it’s also dangerous. We have many different lifts these architects aren’t aware of, and we can customize those lifts to fit them into tight spaces. Invariably we find we can either increase the car count or reduce the size of the garage when compared to the architect’s design using stock parking lifts. Of course, a bespoke solution will cost more per machine, but our best customers focus on the ongoing revenue we create rather than the one-time purchase price.
For example, let’s say a developer is building in a high water table and there’s a height restriction limiting the building to 200 feet tall. Let’s also assume the parking deck is at the base of the building and is using 40 feet of the available 200-foot tall building envelope. If we can use our parking lifts to reduce the garage height from 40 to 30 feet, we just unlocked an entire floor of additional floor area that would’ve been wasted if the developer stayed with a traditional ramp garage.
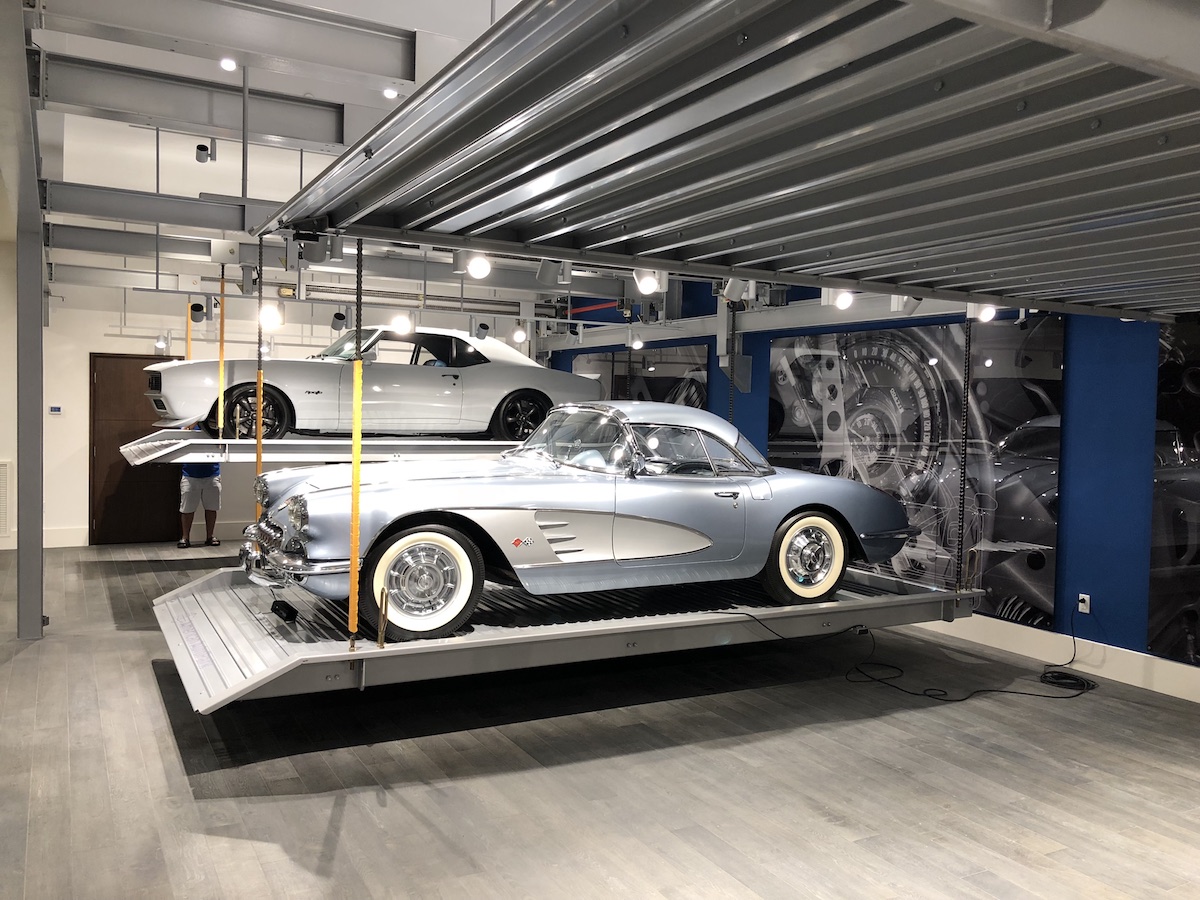
[Photo: Courtesy of American AutoPark]
Mechanical parking solutions aren’t new. What makes American AutoPark’s products different?
We’re willing to take the basic technology and customize the machines to fit them into buildings. It’s never about the price of the machine; it’s about which machine is most profitable for the project. We are the only supplier in the U.S. I’m aware of that has no standard sizes. We customize every machine because every project we work in is different. My life would be a lot easier if we didn’t do that customization, but as a real estate developer, I just cannot stand to watch my customers leave money on the table.
In addition to the technology, valet parking remains an essential piece of AutoPark’s highly efficient parking system. Why is that?
With a fully automated machine, the machine does all the work. Everybody takes their cars to the same location and the machine dictates where your car’s going to be. This all sounds very cool until developers see how much fully automated systems cost. By utilizing valets and parking lifts, we can get the same density as fully automated systems at a significantly lower capital investment.
American AutoPark is also building its own parking garages now. Can you tell us about that?
The AutoPark Cube is a freestanding modular structure built around our parking lifts that can park cars vertically on a lot where you could never put a parking deck. For example, we can easily park 488 cars on a footprint where they currently park 56. To me that’s incredibly wasteful. As real estate prices increase, I am confident others will soon agree.
Is the AutoPark Cube sustainable?
Huge paved parking lots absorb heat but not rainwater. Experts say that’s a big part of what made Hurricane Katrina so harmful—there was nowhere for the water to go. Our Cube sits on a fraction of the land, which enables developers to leave more permeable land. The Cube also uses less building materials and can be an open air structure, so there’s no need for mechanical ventilation. Since it’s only used by valets, we can turn on lights only when valets are on the floor. You can even put solar panels on the roof to power it.