Story at a glance:
- Aluminum is lightweight and naturally anti-corrosive.
- Lorin Industriesā founder engineered a continuous coil anodizing process to make the aluminum surface harder and more durable.
- Anodizing aluminum builds a crystalline structure that reflects and refracts light to bring projects to life.
If youāre looking for a high-design, low-maintenance, environmentally responsible, long-term solution for your buildingās roof or facade, anodized aluminum is an architectās dream. Its lightweight and broad options for color and finishāthat, despite misconceptions, are not painted or sprayed on but bonded at the molecular levelāmake it the perfect solution for anyone trying to achieve a natural metal look without the fuss.
Aluminum has long been touted as a great option for building and design because of its light weight. It is also naturally anti-corrosive and will form a soft, thin, and opaque protective oxide layer when left to the elements. Anodizing enhances this natural process.
Through the electrochemical process of anodizing, the raw aluminum is bonded at the molecular level to create a surface that is thick, translucent, and very hardāmuch harder than the base aluminum itself. Itās not a coatingālike paintāso it will never chip, flake, peel, or chalk, and it will never rust or corrode. āWe take what nature does already and make it better,ā says Phil Pearce, vice president of sales and marketing for the global leader in anodized aluminum Lorin Industries.
Chemists at Lorin have spent nearly 80 years perfecting the process of anodizing. They have never shied away from a challenge. Herb Kersmanāfounder of the third-generation, family-owned company in Muskegon, Michiganāengineered the continuous coil anodizing process, enabling color consistency on large architectural projects and saving manufacturers time and money. Kersman developed the process after being approached by a potential customer. The company also pioneered the first continuous coil UV stable ColorIn process, leading to the first UV stable anodized copper and zinc-look finishes.
A passion for chemistry and the art of anodizing is what Lorin is known for. Multiple generations of families have worked at Lorin, some for much of their lives. The process has been so refined over time that when an employee retires, their successor trains alongside them for several years. āIt is underappreciated how much of this process is an art. It is a skill set you canāt put into a training video. Our employees, our customers, they appreciate that,ā Pearce says.
Lorin is constantly innovating. If you can dream it, they will try to achieve it. Pearce recently sat down with gb&d to explain how anodized aluminum can enhance a buildingās roof or facade, all while keeping things green.
How does anodized aluminum contribute to design aesthetics?
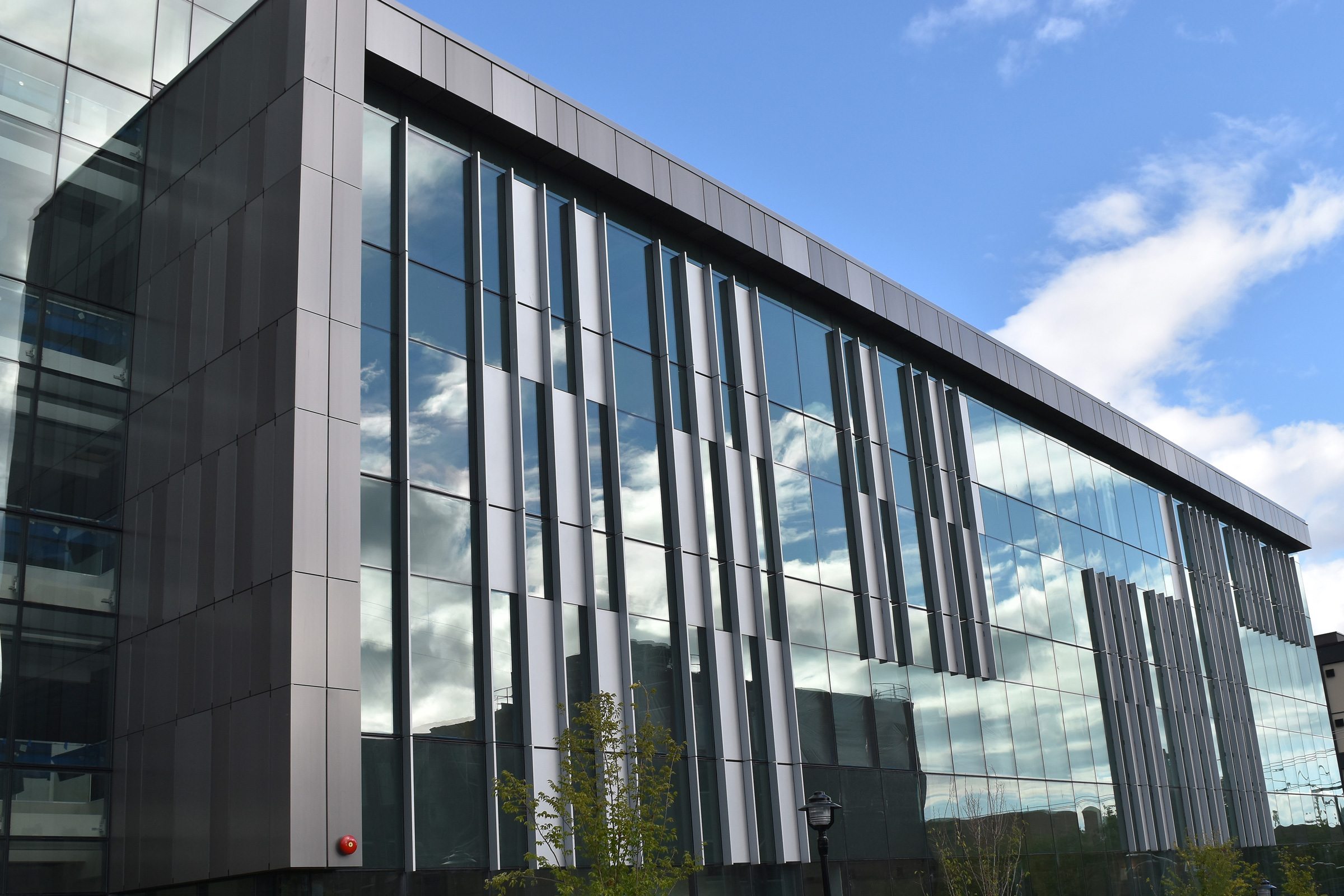
The Holland America Cruise Line Headquarters in Seattle with Aluminum Composite Panels using Lorin AnoZinc I™, AnoZinc II™, and Pewter finishes. Photo courtesy of Lorin Industries
It is so challenging for us to have our product accurately pictured in images. You canāt appreciate it until you hold it in your hand or see it in real life. Anodizing aluminum builds a crystalline structure that reflects and refracts light in a way that makes a project come alive. It creates a three-dimensional metallic look you just canāt get from paint. And, it is all produced in a continuous coil for uniform consistency across the product.
We offer a multitude of colors, shades, and finishes for exterior useā19 standard products we offer currently. We are introducing new ones all the time and do a lot of custom colors for projectsālike interiors colors to match Victoriaās Secret pink and Coca-Cola red. Lorin has UV stable offerings that reflect the look of natural metals without their downsides, including zinc, copper, bronze, brass, gold, silver, stainless steel, and true black.
Anodized aluminum can be embossed in a variety of patterns. Its high strength-to-weight ratio makes it ideal for forming and meeting the challenges of curved and double-curved architectural designs. It can also be roll-formed, put into a press brake, or stamped into many shapes, including corrugated. It can be perforated and used as a screen on parking garages to help with headlight glare or outdoors to block the sun while allowing for airflow. It is perforated before the anodizing process, ensuring the entire unit, including the inside of the holes, is protected from corrosion.
Does Lorin offer any finishes for cool roofs?
Lorinās anodized ClearMattĀ® or Silver White are industry leaders for cool roofs. They contribute to LEED with SRI values above 90, compared to top PVDF paints like Solar White, scoring an 82, and Silver Metallic, with a score of 67. This means Lorinās anodized aluminum lowers the heat load on a roof more than paints, helping reduce cooling costs and overall energy consumption.
How long will an anodized aluminum roof or facade last?
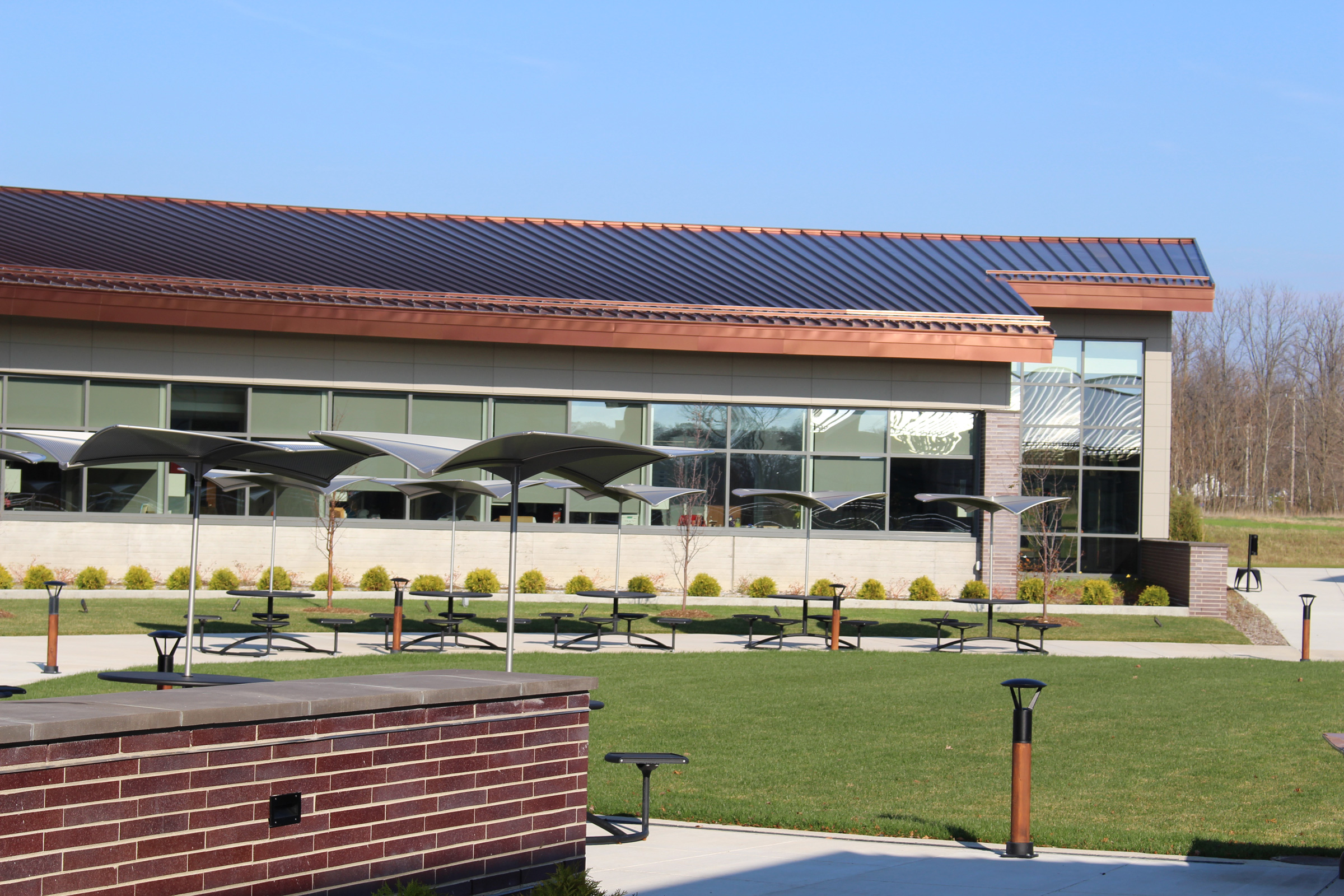
The Gun Lake Casino in Michigan has a roll formed standing seam roof and soffits in Lorin Medium Antique Copper. Photo courtesy of Lorin Industries
We like to ask customers how long they would like the product to last. We provide a minimum 20-year surface warranty for any Architectural Class anodic layer but have provided written warranties for much longer.
The Lorin anodized surface is resistant to stains and common bacteria, including E-coli and Staphylococcus. Maintenance is relatively simple. It needs to be washed with mild soap and water every other year, unlike paint warranties, which require annual cleaning with stronger, often less environmentally friendly, and more expensive cleaning agents.
Anodizing is not a coating so it does not rust or corrode. Other natural metals will oxidize over time, creating a runoff that has to be cleaned. If you have copper near the coast you may see green or, in other parts of the country, muddy brown or black runoff stains. Itās the same with pre-weathered steel. With our materials, we like to say, āIf you pick a Lorin color you like, you get to keep it.ā
Anodized aluminum scores well on both the Taber abrasion and falling sand abrasion ASTM tests, earning a 70 where paint earns a 20 to 25. The Lorin anodic layer is very hardāregistering a 9 (the highest) on the Mohs hardness scale, which is similar to sapphires, also made of aluminum oxide. It resists scratches, but if scratched it can be touched up. It also scores well for graffiti resistance.
Lorin products work well in coastal areas where corrosion can be a detriment to paint or steel. It scores well on the salt spray exposure testāpassing more than 3,000 hours, three times longer than the ASTM requires.
What is required for labor and installation?
Aluminum is lightweight, which means it is easier to handle/fabricate. It offers more options for profiles for roof panels because of its superior formability and tighter tolerances than other metals. It is often faster and less costly to install than other metals. Anodized aluminum in .032 gauge is easier to cut and trim compared to .032 gauge steel. No special tools are required beyond what would be used to install other metal roofing.
How is anodized aluminum āgreen?ā What are Lorinās sustainability practices?
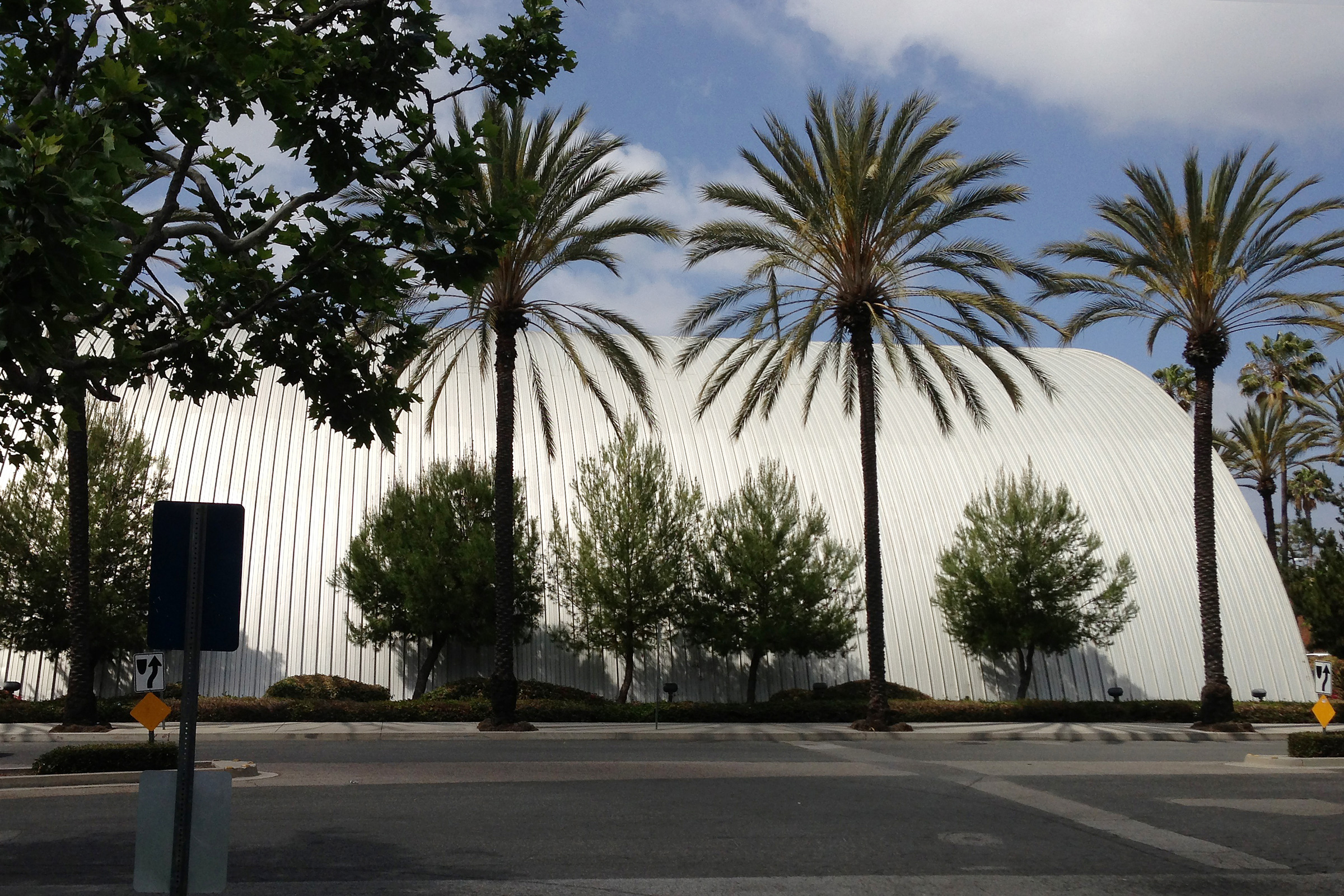
The Anaheim Ducks practice facility features a standing seam roof in Lorin ClearMatt Anodized. Photo courtesy of Lorin Industries
Anodized aluminum is the only metal that is 100% recyclable. It is one of the most recycled and naturally abundant and sustainable materials on earth. Anodizing is a water-based process. There are no VOCs or Red List items in anodized aluminum, and it is RoHS compliant. It is so safe you will see aluminum oxide listed as an ingredient in some antiperspirants.
Most of the chemicals used in the anodizing process are repurposed, and most of our production chemicals are non-toxic. With in-house recycling capabilities, our primary chemicals can be reused as many times as needed. We even purchase chemicals coproducts from other companies and use them in our processes. We have our own wastewater treatment facility, so the water that we treat from our process can go back to the cityās treatment facility. We also have our own cleaner-burning natural gas power plant so we can help offset power needs at peak times by generating a portion of our own power, which helps the local energy company better meet its customersā needs while also ensuring adequate and consistent power for our operations.
We utilize the steam byproduct from our power generation operations for additional clean power. Very little waste goes into the landfill, and the little that goes is sent to a non-hazardous landfill.
Being environmentally responsible has always been part of our heritage, way before it was fashionable to be green. It is in our genes. We care about our neighbors and care what happens to them. We want to do the right thing.