ZGF Architects helps Arizona State University take their research to the next level.
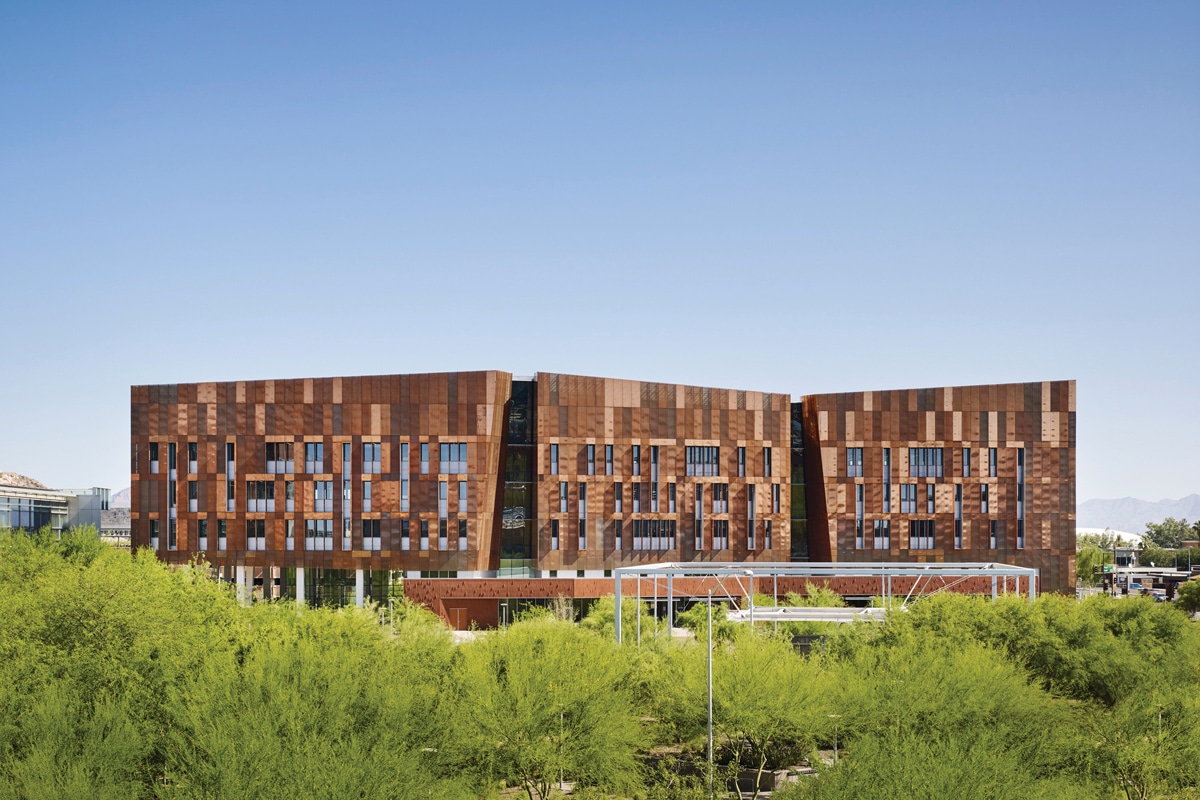
[Photo: Courtesy of ZGF Architects]
PROJECT: ASU Biodesign Institute C
LOCATION: Tempe, AZ
COMPLETION DATE: 2018
SIZE: 188,447 square feet
LEAD ARCHITECT: ZGF Architects
ASSOCIATE ARCHITECT: BWS Architects
CIVIL ENGINEER: Dibble & Associates Consulting Engineers
MEP ENGINEER: Affiliated Engineers, Inc.
STRUCTURAL ENGINEERS: KPFF Consulting Engineers, Advanced Structural Engineering
CONTRACTOR: McCarthy Building Companies
LANDSCAPE ARCHITECT: TrueForm Landscape Architecture Studio
ACOUSTICAL CONSULTANT: Colin Gordon Associates
EMI CONSULTANT: VitaTech Electromagnetics
AWARDS: AIA Los Angeles, 2018 COTE Honor Award
Incredible work is happening at Arizona State University (ASU), so it’s only fitting that the design of the buildings themselves there also push boundaries. Inside ASU Biodesign Institute C, efforts to fight other disease all over the world are happening; the tone for the design of this new building was set early on with the help of ZGF Architects. “From the beginning, ASU intended for the Biodesign Institute C building to make a powerful visual statement at a campus gateway, set a new bar for sustainability and spatial efficiency, and serve as a new venue for groundbreaking scientific discovery to take place,” says Gary Cabo, principal at ZGF Architects.
Cabo says ASU wanted Biodesign Institute C be a “workhorse” addition to the campus’s existing research facilities and significantly expand the research and discovery happening there. “The building was specifically designed to promote and enable the creation of cutting-edge, collaborative research clusters comprised of research faculty, staff, and students,” he says.
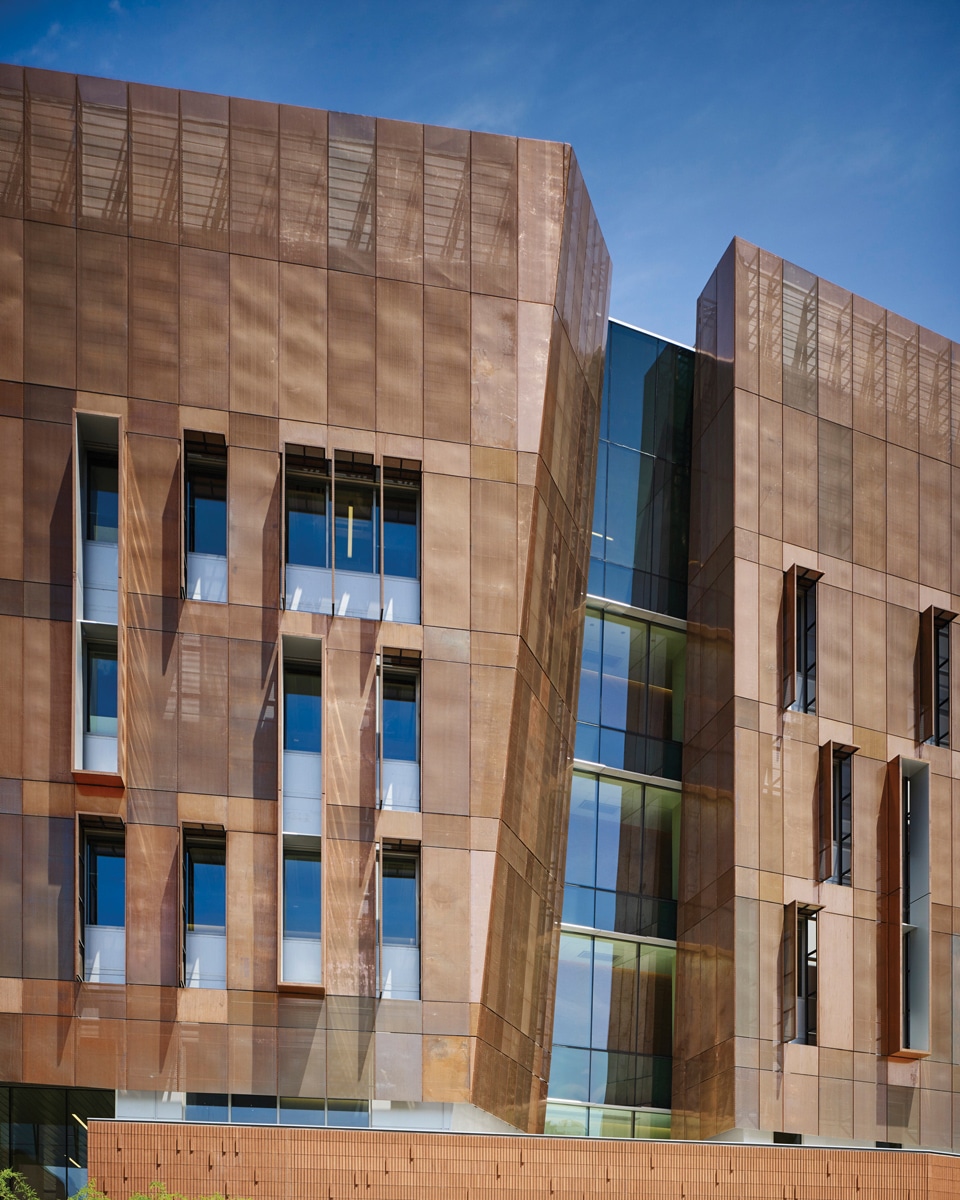
[Photo: Courtesy of ZGF Architects]
Aspirations for the project were high—including targeting LEED Platinum and delivering a new building that was highly flexible and adaptable. “We targeted LEED Platinum by ensuring all design elements and building systems contribute to Biodesign C’s exceptional performance,” Cabo says, adding that incorporating the active chilled beam was one primary energy conservation measure. Overall, the project’s sustainable design allowed for more than 60% energy savings for the campus, more than $350,000 annually in avoided energy costs, and more than 40% indoor water savings.
Cabo is perhaps most excited not just by the project’s design, but by the high-tech innovations inside it. “The building will house the first compact linear accelerator (compact x-ray light source) ever built,” he says. “The high level of science, technology, and engineering that went into creating it is inspiring, as are the talented researchers who will use it and the incredible leaps in scientific discovery and human health that will result from its use. It’s a powerful feeling to know that a building you helped create could be the venue for life-changing discoveries.”
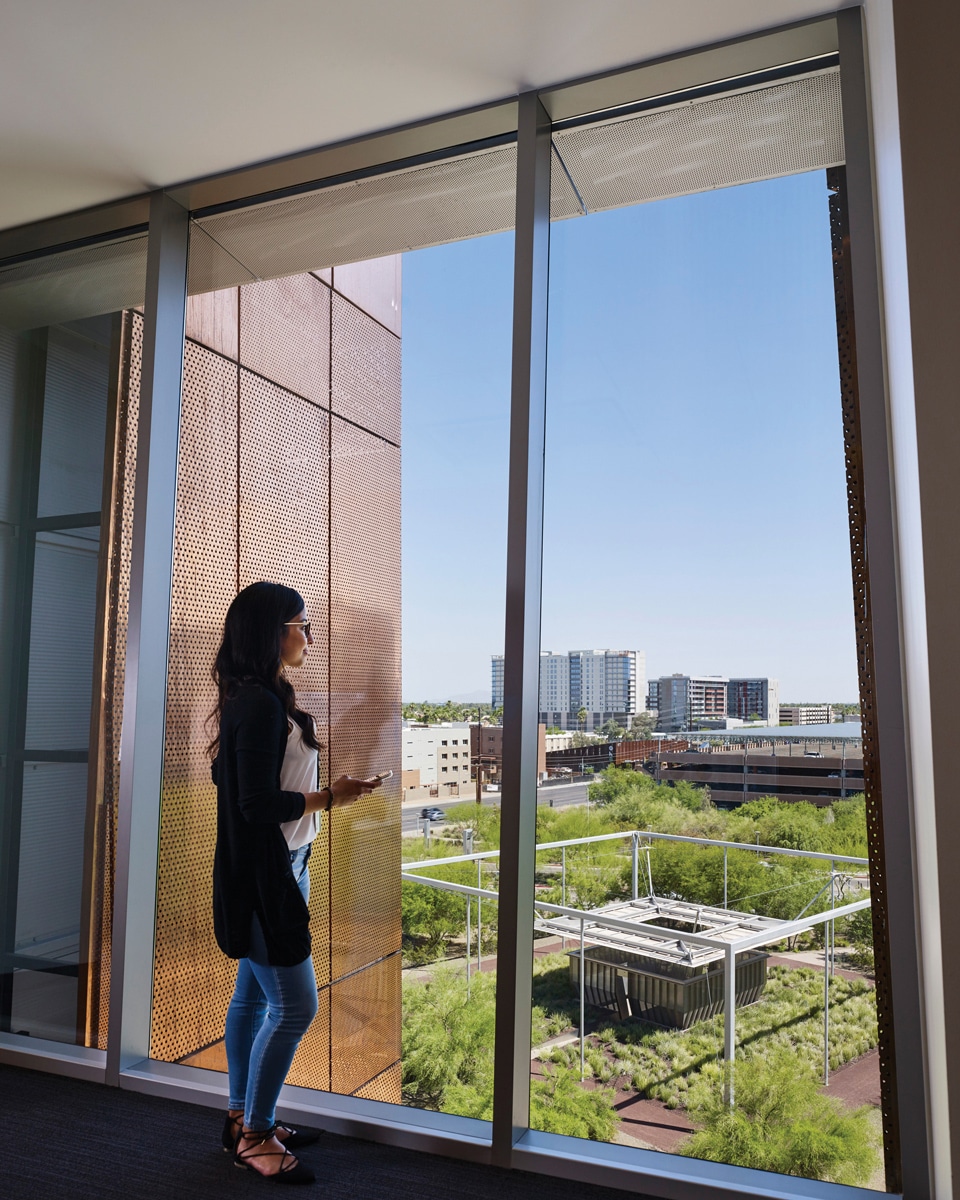
[Photo: Courtesy of ZGF Architects]
Biophilic Design
The building also has a 35% window-to-wall ratio and transparent layering of spaces to ensure daylight floods the above-grade interiors. “The direct visual connection between high technology laboratory spaces and the campus is made possible by the neighborhood plan in conjunction with the high-performance facade,” Cabo says. “The researchers in this building who have chosen to work in an academic environment get to appreciate the campus from their workstations.” The facade also contributes nicely to the overall biophilic design, as the untreated copper will patina over time, emulating the colors of the desert.
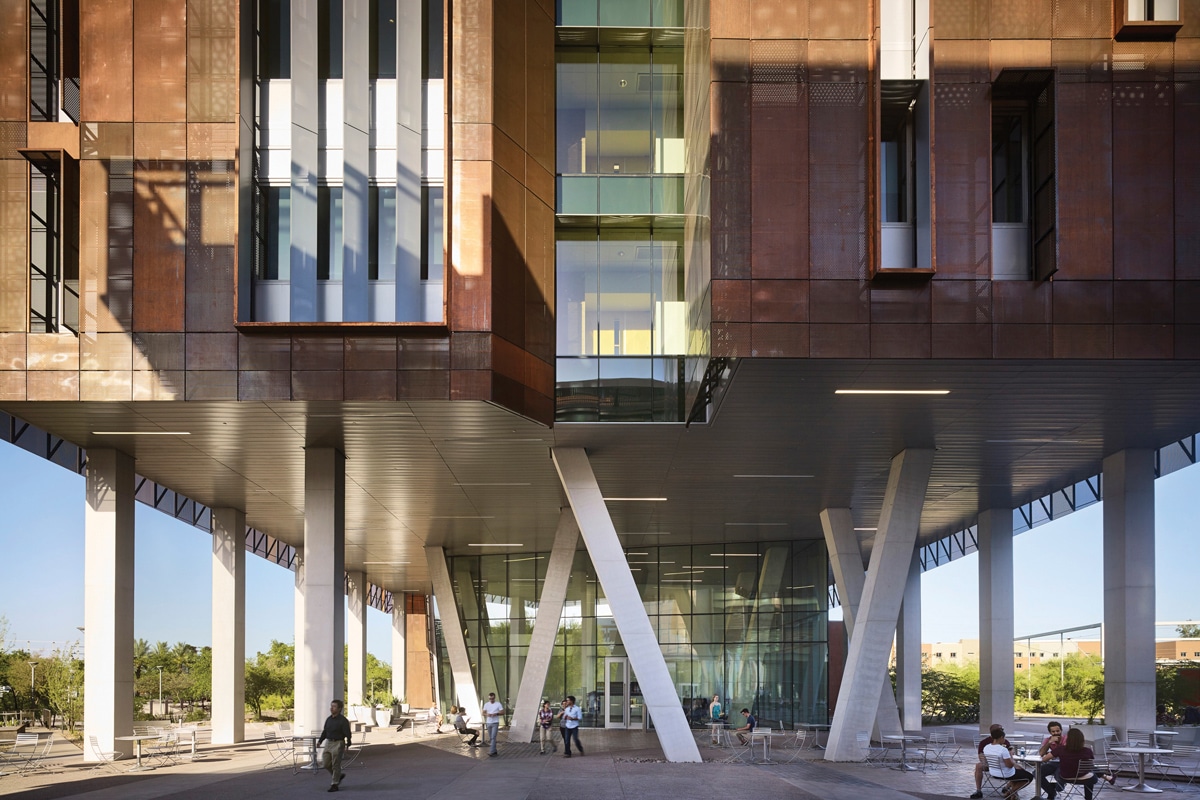
[Photo: Courtesy of ZGF Architects]
Angled White Columns
Cabo says these columns are 100% functional but also 100% stunning. “The columns were a design solution implemented in order to create a shaded public space at the west end of the building. This novel solution was obligatory to deal with the requirement to maintain research level vibration control at the upper floors of the building. Structural engineers at KPFF suggested that if we sloped the columns, they would brace the building laterally, eliminating the need for shear walls. While the series of white cement, square-cornered columns was an elegant design solution, it provided a unique construction challenge —some columns are angled, some are upright, and one is a full three stories in height, reaching from the basement to the second floor. The McCarthy team went above and beyond employing multiple large-scale mockups until they got the mix and formwork exactly right for each condition.”
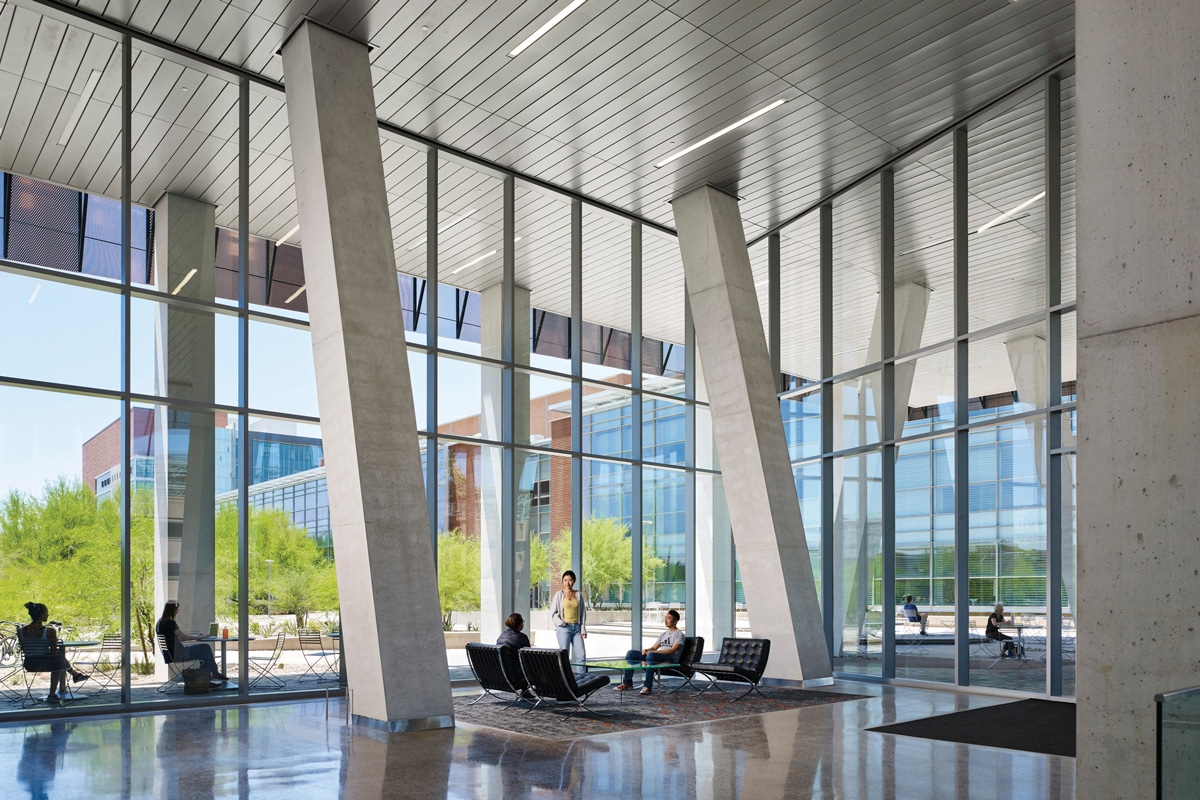
[Photo: Courtesy of ZGF Architects]
Double skin facade
The outer copper screen wraps around a primary skin of insulated metal panels to create a high-performance dual facade. The screen modulates daylight, shades the facade, and creates a vented cavity that lowers the temperature of the skin. The screen is made up of thousands of copper panels with eight levels of perforation. “The way we arranged the perforations varied by facade, allowing a uniform appearance at first glance,” Cabo says. As a shading device, the screen reduces the surface temperature of the inner facade by roughly 65 degrees on hot summer days. This reduces the interior surface temperature of the wall by three degrees, significantly reducing the cooling load on perimeter spaces. Incorporating vertical fins on the east and west facades provides shading from lower sun angles providing both solar control and visual comfort for daylighting in workspaces.
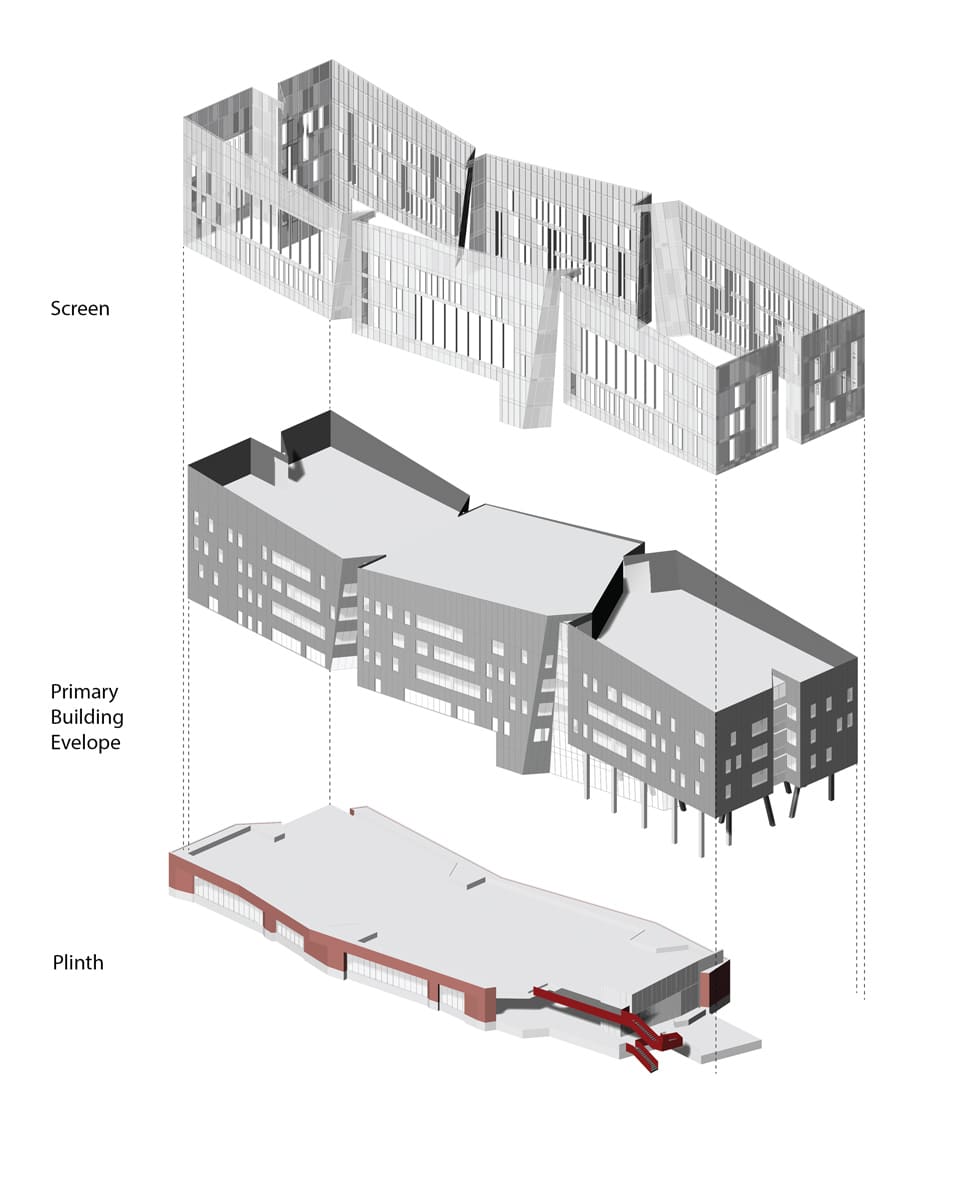
[Photo: Courtesy of ZGF Architects]