Story at a glance:
- Headquartered in New Zealand, Autex Acoustics has built sustainability into its DNA.
- Autex continually tests and brings new sustainable concepts to market at its Innovation Hub.
- Current projects focus on developing infinitely circular product systems and carbon negative manufacturing processes.
In the global built environment, estimates show buildings account for 40% of greenhouse gas emissions. Across the globe Autex Acoustics is extending the Kiwi spirit of sustainability with carbon neutrality across all of its manufacturing processes and a sustainability strategy that emphasizes the environment at every stage of a product’s life cycle.
“Sustainability is in our DNA. Like breathing, we can’t stop, or we would die,” says Autex Acoustics Creative Director Jonathan Mountfort.
The non-woven architectural textiles and acoustic solutions manufacturer developed its sustainability program based on the United Nations Sustainable Development Goals—and it shapes everything Autex does.
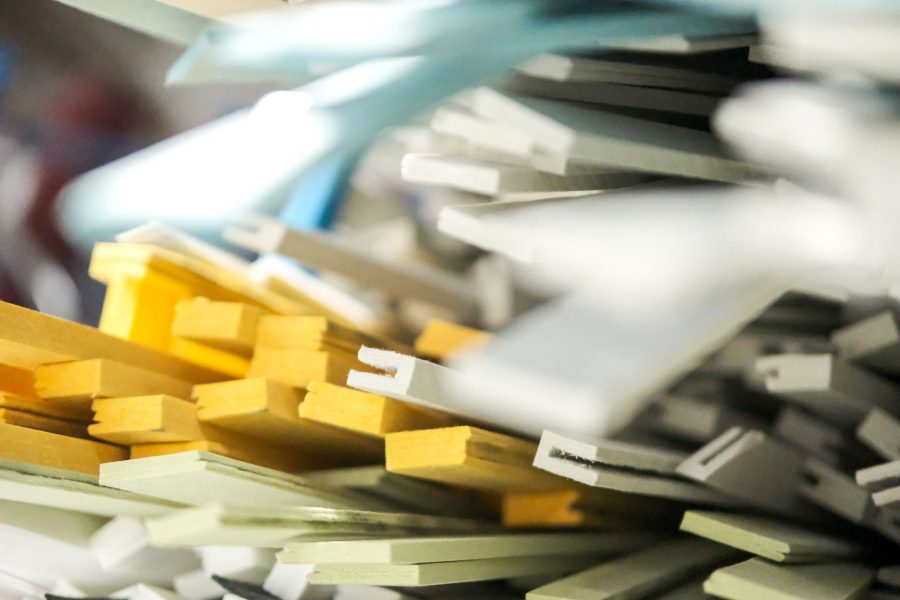
Autex Acoustics innovates and tests sustainable products and processes to push the industry forward. Photo courtesy of Autex Acoustics
“Sustainability is something that’s idealistically and morally built into a lot of designers; it’s a key part to your education. But in a lot of creative fields, when you get out into the commercial world, it kind of just stops or becomes a second priority,” says Sam Wells, product development lead. “Here at Autex sustainability is core to our projects from the start. It’s a pillar that we build every brief on, from sourcing production through our own internal processes, delivery, install, installed life of products, and how we close the loop at end of life to create circular systems so we can start reusing and creating more efficient use of materials.”
These days creating fully circular product systems ranks at the top of Autex’s priority list.
“We’re focusing on the development of completely novel recycling and game-changing material pathways for PET products on takeback. The goal is to create products that improve the environment the more they are used,” Mountfort says. “If we overlay energy flows onto the process, we can create a closed-loop system that minimizes energy consumption in manufacturing.”
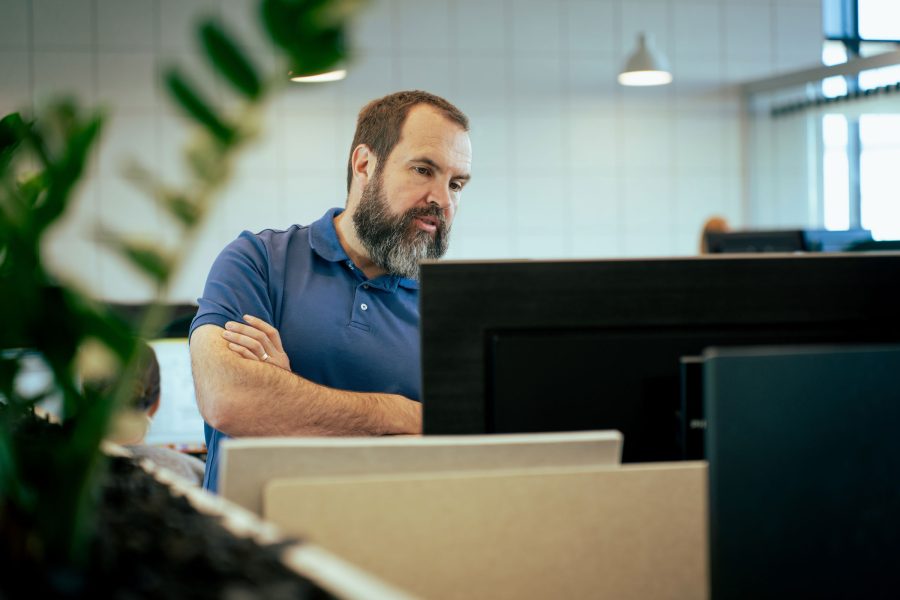
Autex Acoustics Creative Director Jonathan Mountfort says sustainability is in the manufacturer’s DNA. Photo courtesy of Autex Acoustics
Take plastic bottles, for example. Autex transforms these bottles into textile fibers, which become acoustic panels. The panels can then be chipped into shorter fibers to create a backing for products such as the recently launched ReForm acoustic panels.
“A disposable plastic bottle, with a lifespan of a few weeks or months, becomes an acoustic panel lasting 10 or 20 years. If this panel then gets repurposed into another panel, and it lasts another decade or longer, from a short-lived product, we’ve now created 30, 40 to 100-plus years of usable life,” Mountfort says.
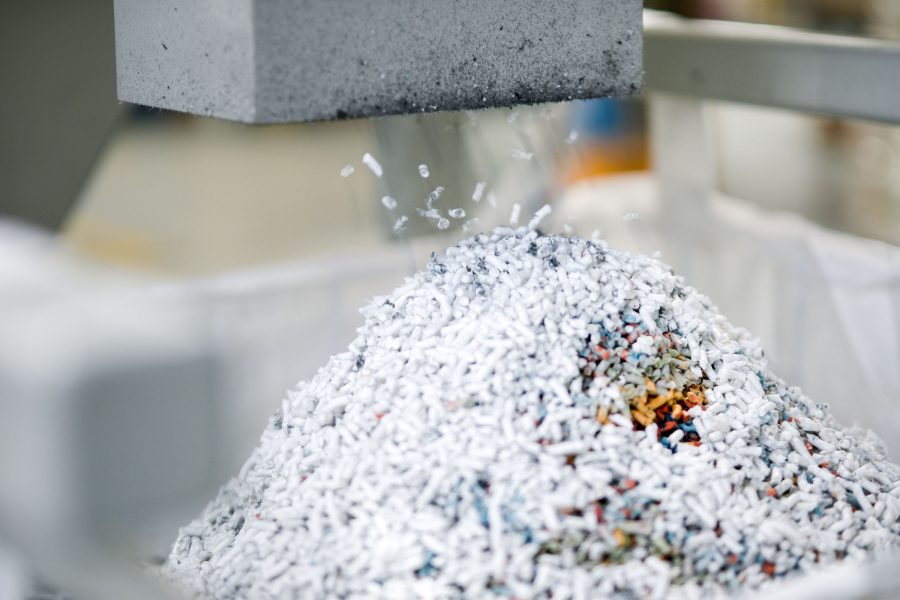
Photo courtesy of Autex Acoustics
This fiber-to-fiber process can be potentially repeated even beyond our lifetimes.
“Eventually it can be re-polymerized, demonstrating multiple pathways for the same material,” Mountfort says. “With this roadmap and emerging technologies that can turn plastic back into oil or other substances, the possibilities extend beyond our industry. The potential exists to derive oil and other resources from this waste, reversing pollution, climate change, and global warming. Combine this with regenerative agriculture, and we have the power to save the world.”
To Wells’ point, saving the world is not the end goal for many manufacturers. But by innovating and testing new sustainability pathways, Autex is proving that it not only can be done but also that sustainable, circular outcomes can be achieved with great success.
“We like to think of ourselves as messy agricultural innovators, but we get the job done,” Wells says. “It’s why we keep our innovation hub here in New Zealand; scale is a real benefit to us. We have the ability to test, taking an idea from concept to a developed idea to market validation very quickly.”
Testing, after all, is what has made Autex a sustainability pioneer. In 1990, before many manufacturers were thinking green, the company established a zero-waste production line. In 2012, it reclaimed waste trimmings, reducing raw material use and related emissions. Autex published its first Environmental Product Declarations (EPDs) in 2017 and actively started measuring its greenhouse gas emissions.
Then came 2020. While it was a challenging year for many manufacturers, Autex pushed further, reducing its raw material use by 30% for its core products. The following year Autex balanced all emissions from acoustic products to zero. By the next year, in 2022, the manufacturer balanced all emissions from its global operations to zero, including at home in New Zealand and across the US, United Kingdom, and Australia.
“We recognize that a lot of the sustainability issues we try to tackle are industry-wide and much bigger than us. What we want to keep doing is get an idea to market and show that it works to try and help push the needle and nudge the wider industry to better practices by seeing what can be done,” Wells says. “That’s a big barrier for a lot of companies—not knowing that it can be done and therefore being too scared to try it out in the first place.”
Beyond developing its infinitely circular PET program, Autex is piloting a takeback program in Australia with eyes on expansion across the entire Autex product portfolio and is in the beginning process of transforming its carbon neutral processes to carbon negative.
“What gets me excited, and it sparked the first time Jonathan and I met, is I realized what could be done in sustainability, and you could see the path where big ideas could turn into real action very quickly,” Wells says.