Story at a glance:
- Viega MegaPress pipe fittings were the first press system in the US market specifically engineered for gas and hydronic applications.
- Beyond being versatile and durable, MegaPress fittings hold up in extreme temperatures.
- MegaPress fittings have also been proven to withstand up to a 9.2 level earthquake.
For well over a century Viega has been innovating in the world of plumbing. Today the leader in press technology is making projects even safer and more efficient—both during the initial install and for years to come.
We talked with Colton Henkowski, a Viega technical training consultant who trains contractors, engineers, and wholesale reps through in-person and online workshops, about some of the surprising benefits of MegaPress and beyond.
3 MegaPress Fitting Types
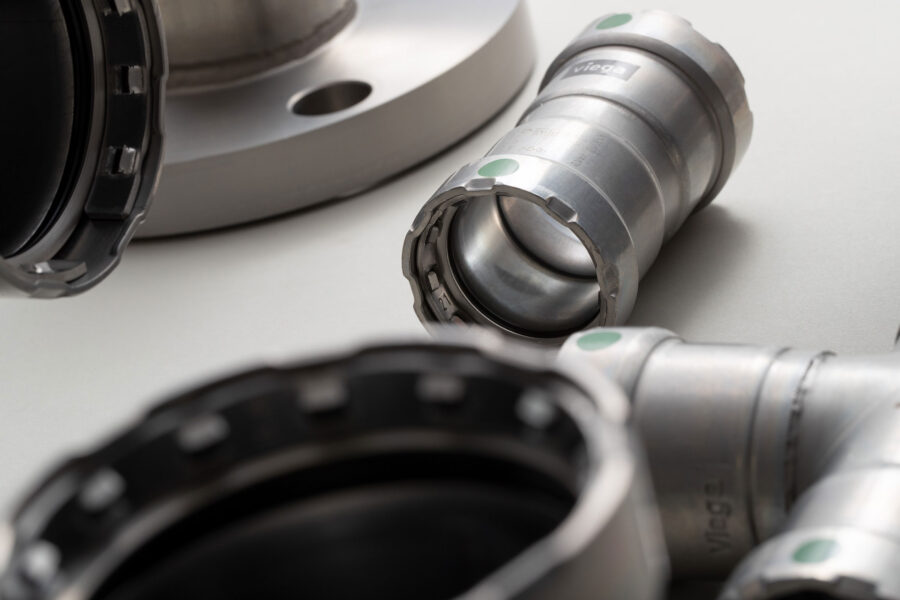
Ethylene-propylene-diene monomer rubber (EPDM) is a synthetic, cured all-purpose elastomer known for its excellent resistance to chemicals and other harsh environmental conditions. Photo courtesy of Viega
MegaPress pipe fittings were the first press system in the US market to be specifically engineered for gas and hydronic applications. More than 10 years later Viega MegaPress systems have expanded to include more than 200 configurations from half-inch to 2-inch and are approved for more applications than any other carbon steel press fitting system.
Each type of MegaPress fitting has different sealing elements, giving them the ability to run the different applications through Viega’s approved applications chart. These sealing elements include:
EPDM Sealing. Ethylene-propylene-diene monomer rubber (EPDM) is a synthetic, cured all-purpose elastomer known for its excellent resistance to chemicals and other harsh environmental conditions as well as its shiny black color. With operating temperatures that range from 0℉ to 250℉, the EPDM sealing element is suitable to any type of water application (including hot water) as well as compressed air and ketones.
“This is used for basic hydronic work and heating and cooling, glycol treated water—anything where you’re doing a hydronic type of heating or cooling system,” Henkowski says. “A lot of people only think of MegaPress gas or gas systems when they think of MegaPress. It’s important they know that they can utilize that fitting with a different sealing element, but the same tool to run different systems.”
HNBR Sealing. MegaPressG has hydrogenated acrylonitrile butadiene rubber (HNBR)—a unique elastomer that stands up to gases and oils better than EPDM. HNBR is yellow in color and boasts a great deal of strength and retention in the face of heat, oil, and chemical exposure. HNBR sealing elements are primarily geared toward gas applications, from natural and propane to mixed and manufactured gases, along with oils and lubricants. If there’s a fire, HNBR sealing elements won’t melt and cause a leak or explosion.
“That opens us up to the world of things like natural gas, propane, and diesel fuel as well as other lubricants and oils,” Henkowski says. “It’s kind of a whole different fitting.”
The HNBR sealing element goes through rigorous specialized testing, especially around pressure and temperature. “We have to pressurize the system to one-and-a-half times working pressure. Working pressure on a MegaPressG fitting is 125. We take it up to 187.5 and then we have to put it in a direct flame oven at 1,000 degrees for an hour and hold that pressure throughout the entire test. HNBR holds the pressure really well and passes that standard, which gives us the CSA stamp on those fittings to approve that press fitting in those natural gas settings.”
FKM Sealing. Fluoroelastomer (FKM) is a specialty-purpose elastomer that is dull black in appearance. In combination with excellent resistance to chemicals and environmental influences, FKM is also characterized by a resistance to extreme spikes in temperatures (up to 356℉) for 24 hours or less. These qualities make the FKM sealing element suitable for industrial environments where there are harsh, corrosive conditions.
“It gives us elevated temperatures and more corrosive media. Our EPDMs can only go up to 250 degrees; the FKM covers the span from 14 to 284 degrees,” Henkowski says. “That gives us the ability to do things like low pressure steam, solar systems, anything where we’re going to have those elevated temperatures.”
Case Study
When a movie theater that uses MegaPress fittings was caught in a large blizzard, its rooftop units were lifted up by the snow. When the snow melted the units essentially fell off of their roof curbs and bent the piping.
“All those MegaPress fittings held together through that bend. The one problem they had on that unit is there was a threaded connection, and that threaded connection broke apart and started a fire,” Henkowski says. “We went back and tested everything after the fire department gave us all the fittings, and we found that all of our fittings held pressure; the only problem was one threaded connection on the unit itself. In those worst case scenarios our fittings hold up better than traditional fittings.”
Specialized Solutions
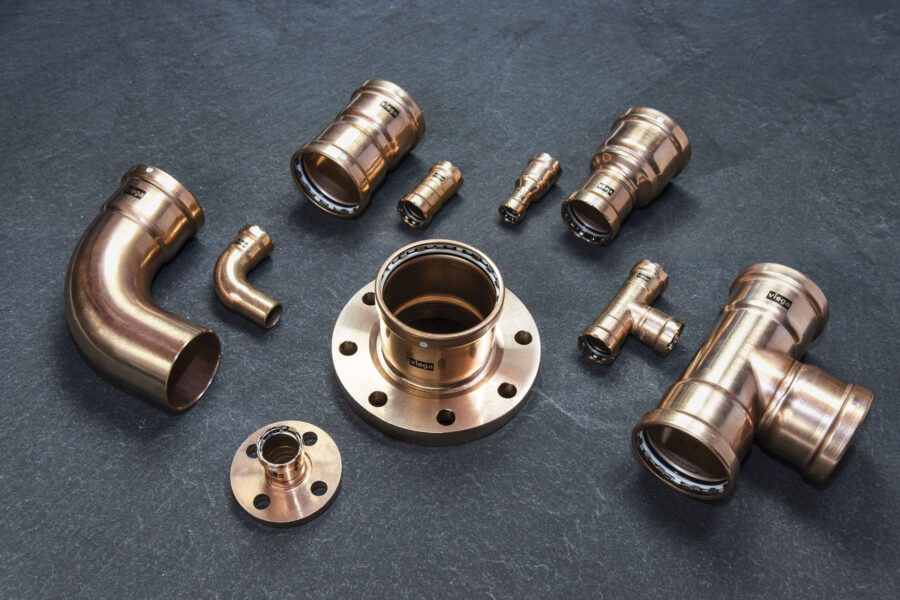
Viega MegaPress CuNi is the only copper nickel press fitting with NAVSEA approval. Photo courtesy of Viega
Viega also offers stainless steel, copper, and nickel MegaPress fittings. “We can get you into different piping methods even if you don’t have the specialized workers to do that.”
If a company has limited staff capabilities they can use that same press around the steel system they already have in different types of applications. MegaPress can even be used to build a ship, as their fittings are Navy-approved—a distinction in the industry.
“The Navy trusts our fittings for the MegaPress CuNi line on their ships to go through torpedo blasts,” Henkowski says.
Efficiency
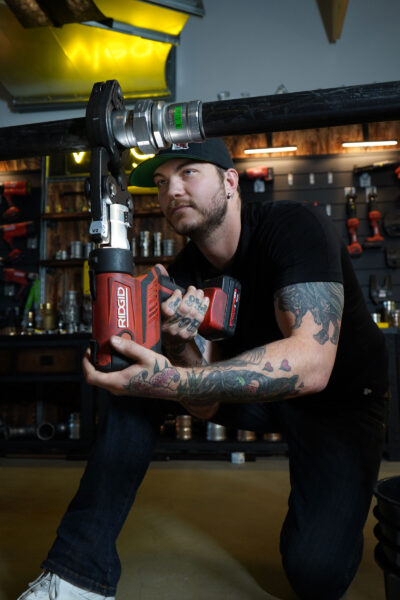
Viega technical training consultant Colton Henkowski presses a MegaPress fitting. Photo courtesy of Viega
Viega’s press technology allows for the same reliable pipe connection every time, but MegaPress also helps with project timelines—an increasingly important benefit in a world where project timelines keep getting shortened.
“Obviously the faster the contractor can get a project done the more money they can make. With MegaPress you can complete a project 30 to 90% faster than traditional methods,” Henkowski says. “We can help them condense those timelines, also offering them a fitting that does what it’s supposed to do and stands the test of time. And you have a good installation the first time around versus having to go back and look for leaks.”
Engineering Services
Beyond state-of-the-art fittings and sealings, Viega also offers engineering. “We can take a blueprint, and then we can give it back to the customer with a fully designed press system,” Henkowski says.
Viega has engineers in the field who can design and build those systems when, say, a company is too busy to do that themselves. “We can help assist and alleviate some of their pain. Or we can offer that to a company who has no engineering and usually hires that out.”
Seismic Testing
Viega also offers fittings that have undergone intense seismic testing. They met the highest standards for seismic durability in testing at an earthquake simulation facility.
The fittings were tested at 200 psi with compressed gas and at 300 psi with water at the Structural Engineering and Earthquake Simulation Laboratory at the University at Buffalo in December 2021. The fitting assemblies withstood acceleration factors up to SDs 2.0 for at least 30 seconds.
The United States Geological Survey considers a 2.0 certification to be the highest level required in the most seismically active areas of North America. That makes Viega the only fitting manufacturer whose press fittings have met the highest US seismic standards at both 200 psi for gas and 300 psi for water. “It was really important in California that we pass the seismic rating,” Henkowski says.
A shake table was built to create an earthquake scenario, starting with a 5, then a 7 on the Richter scale. Finally, they ran a 9.2 level earthquake test twice. “We passed with flying colors—absolutely no leaks and everything held up through all the different situations.”
Fittings You Can Rotate
Being able to rotate a fitting after it’s pressed is another benefit of MegaPress people often don’t consider, Henkowski says. This is especially important if a piping system is done incorrectly or something changes in the layout. “If that fitting actually needs to turn, rather than take it all the way back off and start over again or have to cut apart, we can rotate that on top of the pipe and put it where it needs to be. It just makes that field installation that much easier when things come up.”