Story at a glance:
- Melink’s building health monitor PositiV identified several areas of HVAC deficiency and prescribed solutions to correct the problems.
- Changes made in response to the data collected from PositiV led to the overall lowering of heating and cooling costs and a healthier indoor environment for employees and customers.
- The building’s overall health rating improved from a D to a C.
When engineering managers of a popular national quick-service burger chain were looking for a way to monitor and protect the health of its new or renovated facilities, they turned to PositiV. What they found in one location was a major cause for concern.
Melink Corporation’s building health monitoring system PositiV measures key building health metrics—temperature, relative humidity, carbon dioxide, and building pressure. The system then grades the building based on the data. If it senses any metrics are out of the set parameters, it prescribes solutions to combat potential issues. The standalone, solar-powered digital system uses two wireless monitors to track and remotely monitor a building’s overall health. One monitor is installed on the interior and one on the exterior for the most accurate data collection.
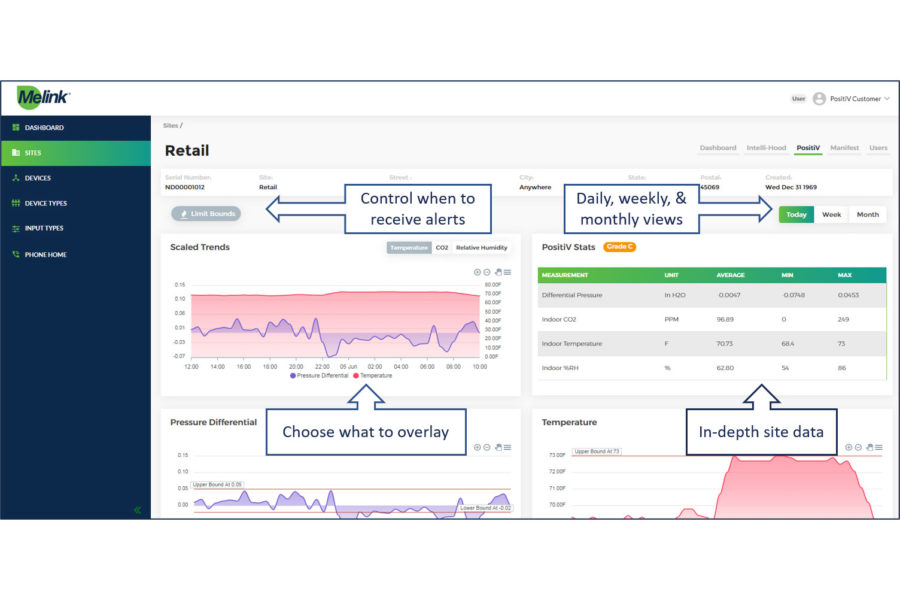
The data seen here is an example of the kind of data you may receive. Image courtesy of Melink
The system has the expertise of highly trained HVAC specialists to back it up. Melink, which started as an HVAC test and balance company in 1987, has spent 30-plus years keeping HVAC systems running as efficiently and safely as possible. Alex Falck, product manager at Melink, sat down with gb&d to explain what PositiV uncovered about this particular restaurant location and how it helped solve the problems.
Why was PositiV used in this project?
In 2019 this popular national quick-service burger chain’s 5,000-square-foot Norfolk, Virginia location was renovated. Part of this renovation included replacing and redesigning the HVAC system. It was a complete overhaul focused on getting the building up-to-date.
Shortly after renovations were complete they began having several HVAC-related issues—high energy spend, high cooling load, and occupant complaints about heat in the kitchen. They were not entirely sure of the root cause of these issues, so they reached out to us. They purchased and installed PositiV to obtain critical building performance and design data. They were looking to identify and correct potential problems and also verify HVAC performance in their newly-designed building.
What did PositiV find?
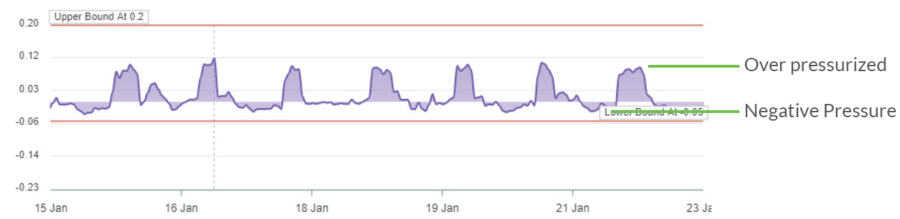
Data from this pressure chart is from the restaurant case study. Image courtesy of Melink
Even in this newly remodeled facility that had gone through many steps to receive its certificate of occupancy at the hands of several contractors, there were significant deficiencies. Data collected by PositiV showed that 88.6% of the time it was operating outside of parameters for pressure; 46% of the time it was outside parameters for temperature; and, 33.5% of the time it was outside parameters for humidity. To clarify, these were parameters set by the franchise’s building engineers as goals they wanted to meet.
Using the data collected by PositiV, we found they were unnecessarily conditioning the buildings’ air during unoccupied times (8 to 12 hours a day). This was causing the high HVAC spend. The data showed the equipment was not maintaining consistent positive building pressure and was inducing large swings dependent on building occupancy and cooking operations. We also found that the system was not supplying a sufficient amount of make-up air during operating hours, causing a negative pressure situation. This was inducing temperature fluctuations, leading to drafts, hot and cold spots, and general occupant discomfort.
To sum the findings up, they were undersupplying fresh air needed in the building during operating hours and cooling/heating the facility when people weren’t there. PositiV issued a site grade of D to the facility. It was too low for what they were trying to achieve for the building.
How did PositiV help solve the challenge?
PositiV helped to give facility managers a better understanding of where operational and design deficiencies were occurring. In addition to the significant time spent outside of parameters, two major HVAC deficiencies were identified. The oversupplying of air during unoccupied times and undersupplying of air during occupied times.
The PositiV system prescribed a solution to facility managers to adjust and balance the HVAC system to ensure proper pressure and fresh air is maintained across occupancy schedules. To improve the situation, PositiV suggested a slight positive pressure be created. It is how building engineers could eliminate the relative humidity, reduce unnecessary cooling overnight, and overall HVAC spend.
We also found the negative pressure condition was causing indoor humidity trends to follow outdoor humidity trends, thus creating a high dew point for the space. This can present a dangerous situation for a space—condensation buildup and mold growth during hot, humid summer months. It can also lead to wood warping.
How has the building changed since PositiV was installed?
The site grade for the building has been increased to a C, indicating better overall health and performance. Data collected in October 2021 by PositiV shows the facility is operating outside of parameters for pressure 58% of the time, compared to 88% in 2019. It is outside of parameters for temperature 19% of the time, compared to 46% in 2019. And, it is operating outside of parameters for humidity 16% of the time, compared to 33% in 2019.
The dew point inside the facility has decreased significantly. It is no longer trending with the outdoor humidity levels due to the reduced effects of negative pressure. Additional supplied-air also means the system is better able to dehumidify the air. Healthier indoor air and less humidity mean fewer potential health issues for occupants and less risk for mold growth. Proper adjustment and balance of the system have caused a reduction in HVAC spending, as the facility is no longer over conditioning the air during unoccupied times to the same degree.
Without the data, building engineers would not have known how or to what level to tweak their HVAC equipment. PositiV provides the data and information to direct the corrective actions and adjustments needed to reach that healthier building environment.