Story at a glance:
- Autex Acoustics offers innovative, carbon neutral acoustic solutions that are also pleasant on the eyes.
- Autex’s acoustic products include a minimum of 60% recycled PET and post-consumer plastic.
In the great migration back to the office, some employees are feeling a bit more sensitive to the sounds around them after many months of remote work. Founded in New Zealand with an office in southern California, Autex Acoustics is innovating acoustic solutions that both make the workplace more beautiful and make it easier to get work done.
Autex is a leading designer and supplier of innovative acoustic products, including everything from ceiling to wall solutions, and they know how much sound can impact a space as well as the people in it. “We’ve started to see a renaissance of focus on acoustic treatment because noise after the pandemic is a little more audible to everybody,” says Antonio Holguin, business development and sustainability lead for Autex Acoustics North America. “You don’t have to be an expert to understand that.”
Why Sound Matters to Sustainability Goals
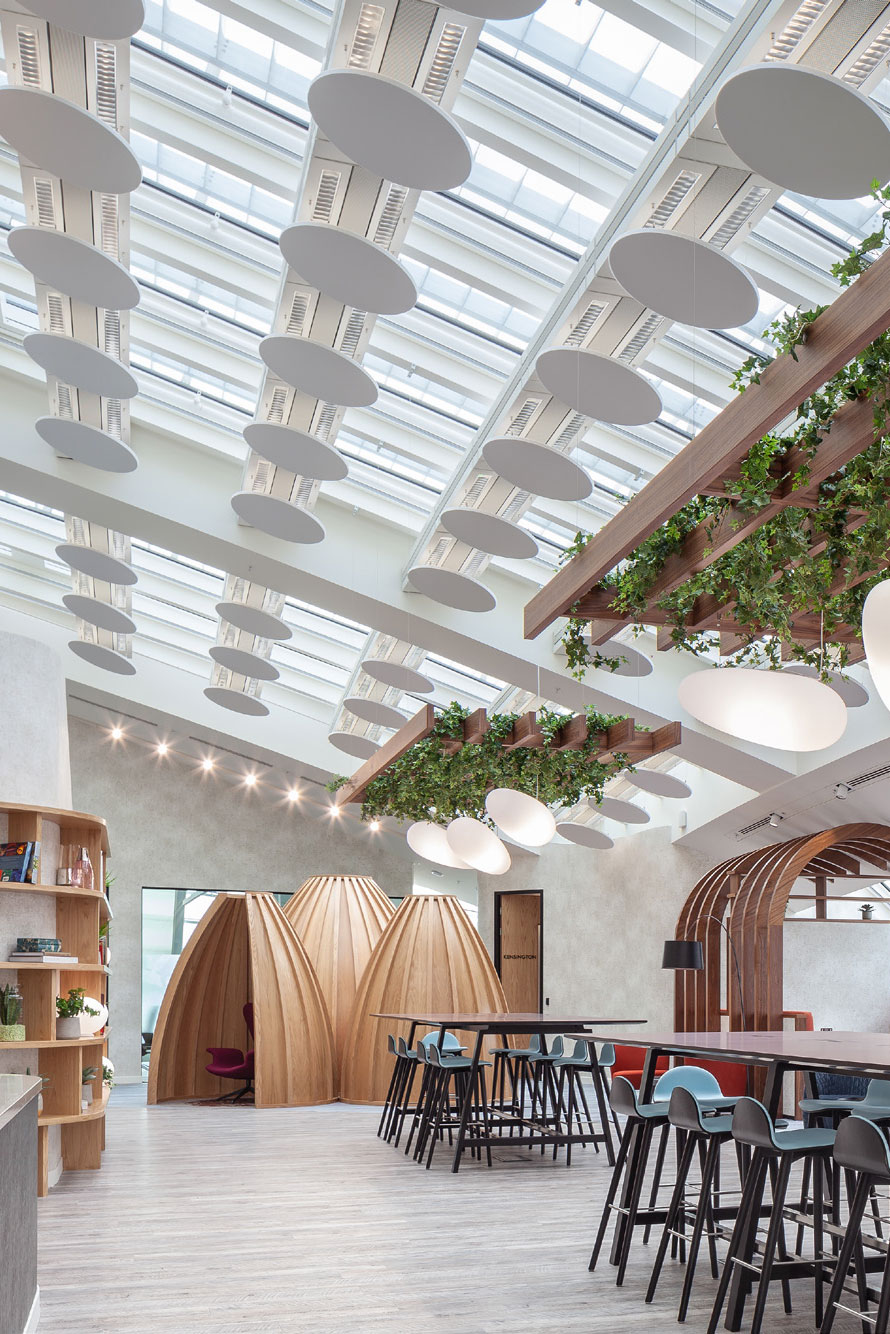
Photo courtesy of Autex Acoustics
Working to help build environments that foster health and wellness is just one aspect of the company’s commitment to sustainability. Autex’s five sustainability pillars and sustainability strategy also align with the UN’s Sustainable Development Goals.
The pillars include fighting climate change by monitoring carbon emissions, closing the loop by ensuring products are sustainable throughout their lifetime, supporting well-being in buildings, balancing purpose and profit, and creating a sustainable and ethical supply chain. All of Autex’s products are carbon neutral, meaning they make no net release of carbon dioxide to the atmosphere.
Estimates show that buildings directly and indirectly cause approximately 40% of greenhouse gas emissions. As the first PET acoustic manufacturer to be carbon neutral, Autex has developed a strategy over its history to meet its sustainability goals and initiatives. “In order to be carbon neutral you really have to take a step back and look at all of your operations,” Holguin says. “You have to be able to measure all of your carbon emissions, and that’s a huge feat, right? It’s not easy to do.”
Carbon Neutral Strategy
Autex’s journey to carbon neutrality started in 2017, with their first published Environmental Product Declarations (EPDs) and GHG emission measurements. “This was before there was a huge push in the industry, much less the acoustics industry, to be looking at these figures and be mindful of the way we operate and how we make our own products,” Holguin says.
The company engages in product optimization by evaluating its product and creating ways to use less virgin material and less material altogether—all while ensuring it has the same high-performing qualities.
In 2020 Autex’s dematerialization project reduced raw material use by 30% for the core product. By 2021 the company balanced all emissions from its acoustic products to zero. By 2022 this included emissions from global operations in New Zealand, Australia, the United States, and the United Kingdom. Autex’s current GHG emission profile is equivalent to the annual emissions of 1,767 passenger vehicles, according to the EPA GHG Calculator.
Translating Sustainability Across the Globe
Part of Holguin’s job is helping to bring Autex’s sustainability initiatives from its headquarters in New Zealand into the US. New Zealand is already a sustainability-minded country; most of its power is renewable, and it has limited resources being on an island. “For them it’s pretty natural. It’s not a big deal for them to live off of renewable resources and be super mindful of their waste and circularity,” he says.
Product optimization looks different for each territory. “Here in the US, how do we better our shipping methods from where we’re based in California throughout the country?” Holguin says. “Those will all look different from market to market.”
Extending Product Life Cycles
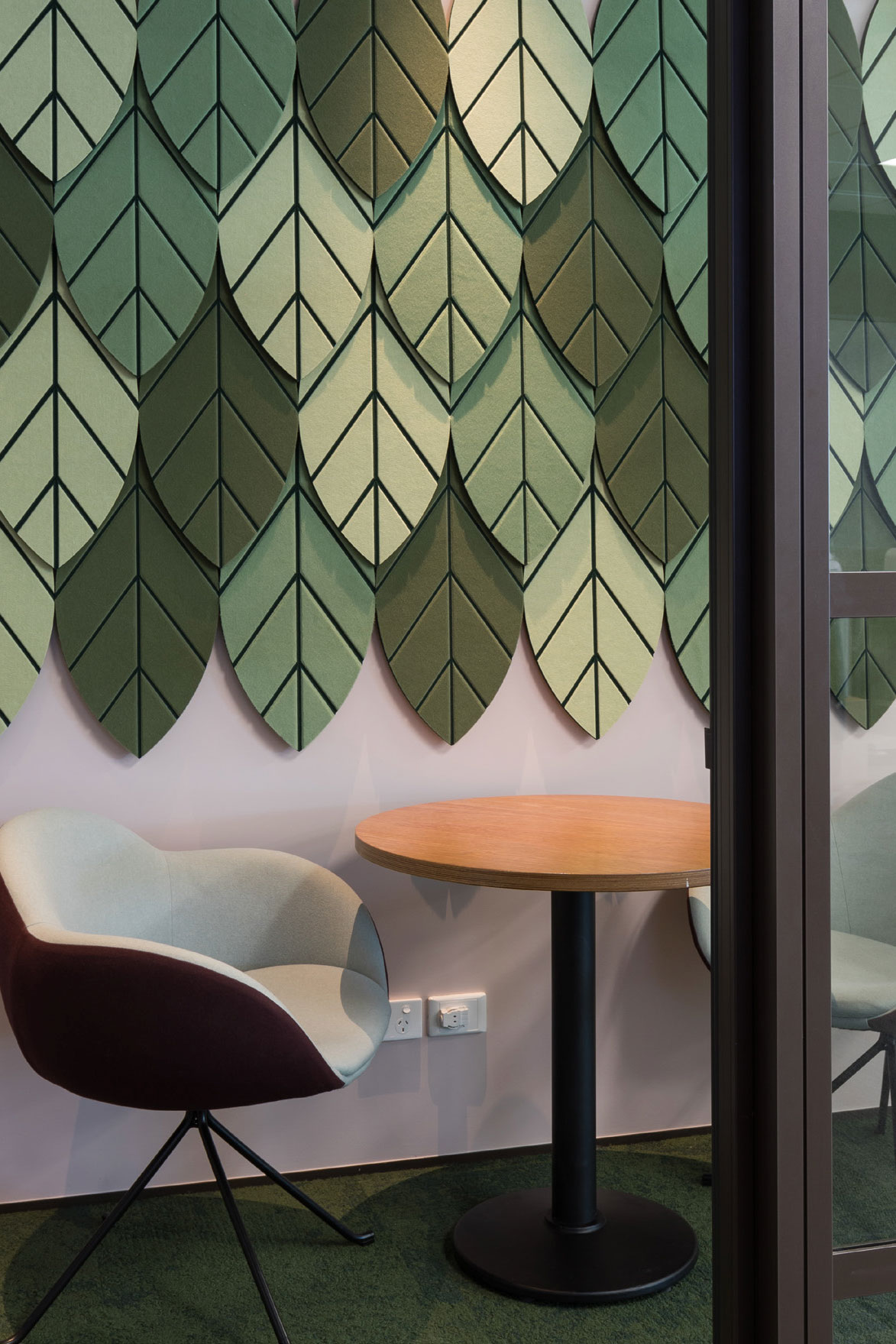
Photo courtesy of Autex Acoustics
Autex strives to be more than just carbon neutral, too. Its products include a minimum of 60% recycled PET and post-consumer plastic. “That means we’re taking plastic water bottles and recycling them into our panels,” Holguin says. “As an industry we’re really starting to look at circularity and the conversation around ‘how do we create products that are working or functioning in this closed loop versus ending up in the landfill?’”
Autex starts by taking waste, in this case used plastic bottles, and turning them into something innovative and useful. Part of that process includes partnering with architects and designers when installing or specifying Autex products to ensure they’re using the acoustic product in a way that is easy to take apart at the end of a project’s life.
“We’ve got a 10-year warranty on our product, and for the most part we’ll see most interiors change within that time frame,” Holguin says. “So it’s working with our designers to make sure that instead of gluing down a panel they’re attaching it in a way where they can come in and remove it so we can build out a take-back program or so it can be reused in some way, shape, or form instead of getting damaged and thrown away.”
The Human Component
How does that reusability and the overall mission of sustainability impact building occupants, though? “For so long we’ve talked about the building component in the industry. What does it mean to have a healthy building? Are we running efficiently? Are we looking at those kinds of things? How do we save energy?” Holguin says. “Now we’re really starting to look at the human component of wellness. How do we make sure the building we’re creating is benefiting the people who are going to be operating there?”
That starts with using materials that help absorb sound and provide comfort throughout the day. Autex also considers how materials are sourced and the wellness of the people who create the designs in manufacturing supply chains.
“We have certifications throughout New Zealand for our factories ensuring that everyone is paid properly and that they’re all working in the safest conditions,” Holguin says. “We’re beginning to look at how we as an operating organization also have an impact on the communities around us and the communities that we operate and work in.”