Story at a glance:
- Flooring and surfaces manufacturer Tarkett is a leader in circular design.
- Sustainability leader Roxane Spears says circular design is no longer nice to have; it’s essential.
- From recycling to design, the circular economy encompasses all elements of responsible manufacturing.
In the built environment the days of “out with the old, in with the new” are long gone. But “out with the old to recycle and reclaim materials, in with the next-generation product made from those materials?” It may be a mouthful, but embracing a circular economy is the only way forward, says Roxane Spears, vice president of sustainability at Tarkett, a top flooring and surfaces manufacturer and leader in circular design.
“When we talk about circularity, it’s not a ‘nice-to-have.’ It’s a necessity,” she says.
She’s not the only one who feels that way. In December 2022 the World Bank released its first comprehensive study on the circular economy, which found that the current “take-make-use-waste” model is increasingly unsustainable for not only the environment but also from an economic and inclusion standpoint.
And yet circularity seems to be shrinking. In 2023 the global economy is only 7.2% circular, down from 8.6% in 2020 and 9.1% in 2018, according to the annual Circularity Gap report.
We can’t keep throwing things away.
“We can’t keep throwing things away. We have to keep finding solutions of how we reuse, recycle, and repair because of our limited resources. We need to be able to create that circular economy,” Spears says. “And it’s not just one product, and we’re done. Once we get one working, we need to move to the next type of product, so we’re always thinking about how we can be better.”
The Road to Circularity
- Photo courtesy of Tarkett
- Photo courtesy of Tarkett
So how do we get there?
“The very first part of being able to design something that’s circular is starting with really good principles of design,” Spears says. “We use Cradle to Cradle and their five pillars as our principle of design. That gives us the ability to create a product that has healthy materials that we know we can recycle, that has good social equity, and is not jeopardizing supply chains, soil, air, or water. We don’t want to develop a product that doesn’t have good materials and create it to be circular to just keep putting bad materials out there.”
Of course every material—its makeup and the processes around its manufacture and recycling—differs. Manufacturers must develop a system that accounts for the proper, sustainable way to work with each material across its entire life cycle.
“At Tarkett we’re really working to make sure each product has its home and its process. It’s always a journey, but as a manufacturer you have to be responsible for what you produce. Even if it’s a product we produced 30 years ago, and we can’t use it back in new product today, we still have that responsibility to make sure we do something with it so it doesn’t go to a landfill, that it is recycled responsibly.”
The challenge, though, is often finding those material waste streams to begin with. Spears admits that, at this stage, it’s a hit or miss process.
“There’s no database or specific place you can go to. Where our team has found success is in simply starting conversations,” she says. “A lot of it starts with our procurement team looking for alternate materials and asking new suppliers, ‘Do you have something that’s recycled content that could fit our purpose?’ Or for our current suppliers, asking, ‘What else do you have? What else is out there?’”
Overall the built environment is lacking transparency around what reclaimed materials exist and are available to be reused or repurposed. If you’re not actively searching for circular materials, you won’t find them, Spears says.
“We really need innovation in the way we manage and process waste,” Spears says. “At Tarkett we probably have materials that could be used in a different manufacturing process, but how do we communicate that? That’s a missing link in the circular world.”
It’s Time to Get Creative
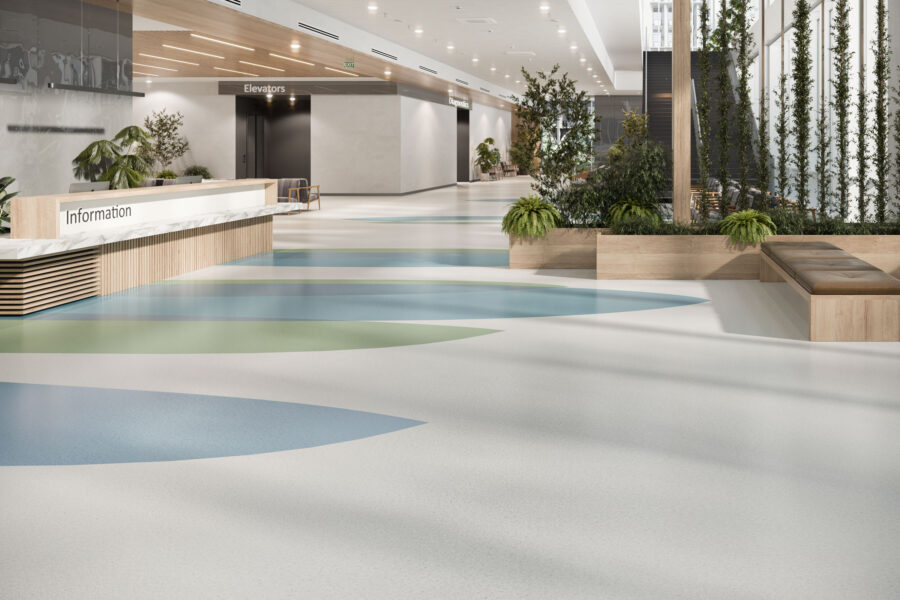
Designed for education and health care facilities, iQ Granit is certified asthma and allergy friendly and is part of ReStart, Tarkett’s program for take back and recycling. Photo courtesy of Tarkett
The other missing piece is creativity.
“I think all manufacturers really need to think outside of the box to discover the next generation of ingredients. I would love to see more diversity in the types of materials that are available,” Spears says. “Flooring has to be durable. It has to be easy to clean. It has to have low VOCs and contain healthy materials. But are there non-conventional ingredients we can use and still achieve our objectives? We’re getting to that point where people are like, ‘You know what, I’m ready to take a little leap of faith and try something really innovative.”
Despite current limitations, the industry is still shifting. Spears says she’s heard more general contractors talking about deconstruction and decommissioning of buildings than ever before, trying to figure out what to do with the waste streams they have and determine ways for those materials to live on. Manufacturers across the entire supply chain are in the weeds trying to grasp how to go circular and be more sustainable.
“Some of the suppliers we work with are now saying, ‘Oh, I need to look at my carbon footprint and make sure I’m doing the right things because it’s affecting your carbon footprint. You’re not going to want to use my product if it’s having a negative impact on your flooring,’” she says. “That’s exciting to me because that’s where we can move the needle. We always say designers have great buying power, but manufacturers do, too. We’re buying those raw materials. Let’s use our buying power to affect change across the industry.”