Story at a glance:
- Cool roofs can help owners and managers of commercial buildings save energy.
- On average commercial buildings account for 18% of the country’s primary energy use.
- Protective coatings can help save energy and extend the life of your roof.
In an effort to reduce operating costs, shrink power plant-generated greenhouse gas emissions, obtain green building certifications, and make building materials last longer, owners and managers of commercial buildings are looking for ways to lower their building’s energy consumption. Among the many energy-savings strategies they may use, cool roofs have gained considerable traction.
Cool roofs are designed to reflect solar radiation and emit heat more efficiently, reduce heat build-up (HBU) on the roofing substrate and inside the building, and potentially reduce air conditioning loads. Cool roofs can be achieved by installing solar-reflective materials during initial construction or refinishing an existing roof with a solar-reflective coating—making cool roofs a winning strategy for new-build and renovation projects alike.
Commercial Buildings and Energy Use
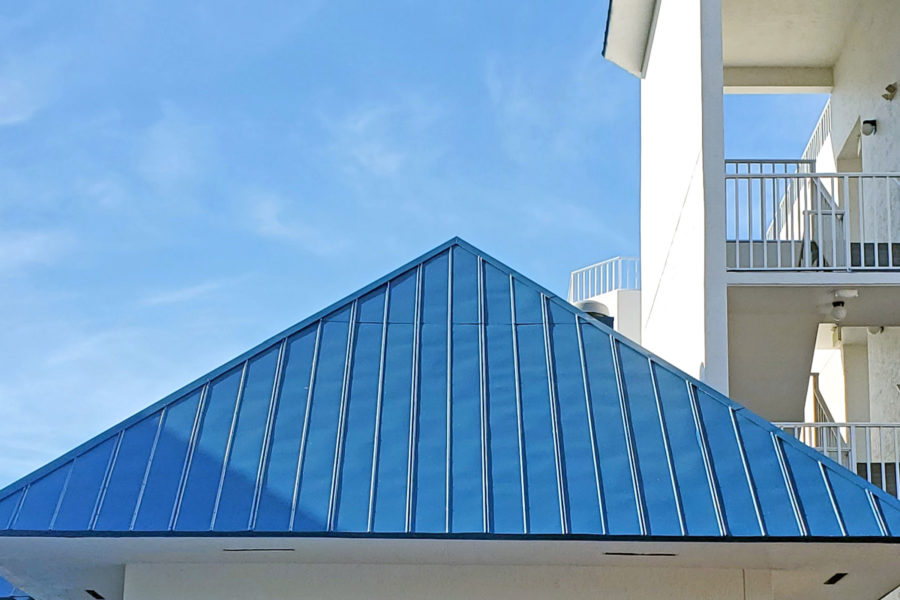
Photo courtesy of APV Engineered Coatings
On average commercial buildings account for 18% of the country’s primary energy use and 35% of its electricity consumption; the US EPA estimates 30% of that energy goes to waste. Because cooling systems consume 15% of the electricity used by commercial buildings, property owners can recognize significant savings by reducing the energy required to run them.
Improved energy efficiency does more than help commercial buildings save on operating costs. It can also help them achieve credits toward green building programs like USGBC’s LEED program, the Green Building Initiative’s Green Globes program, and the International Living Future Institute’s Living Building Challenge. Certifications in these programs provide building owners with a valuable point of differentiation to help them attract and retain tenants.
Improved energy efficiency also helps commercial buildings reduce their contribution to urban heat islands (UHIs), further improving their environmental footprint. UHIs form when trees and other vegetation are replaced with buildings, roads, and other heat-absorbing infrastructures that emit heat and make the outside air warmer. According to the Lawrence Berkeley National Laboratory, UHIs can increase air conditioning energy use, impair air quality by accelerating the formation of smog, and aggravate heat-related and respiratory illnesses.
How Do Cool Roofs Work?
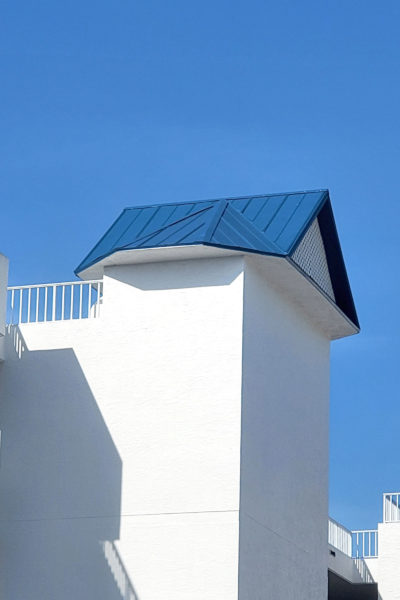
Photo courtesy of APV Engineered Coatings
For more than two decades commercial buildings have been implementing cool roof technology to reduce energy consumption, improve occupant comfort, reduce maintenance costs, and prolong the roof’s service life. Just as wearing light-colored clothing can help keep a person cool on a sunny day, cool roofs use solar-reflective surfaces to maintain lower roof temperatures. While traditional dark roofs can reach temperatures of 150 Fahrenheit or more in the summer sun, a cool roof under the same conditions could stay more than 50 degrees cooler, according to data from the US Department of Energy.
Three material surface properties can be measured to determine how cool or hot a roof is. Better performance in these areas can help to reduce a building’s HBU.
Terms
Total solar reflectance (TSR) is the fraction of sunlight that a surface reflects. Sunlight that is not reflected is absorbed as heat. Solar reflectance is measured on a scale of 0 to 1. A surface that reflects 55% of sunlight has a solar reflectance of 0.55. Most dark roof materials reflect 5 to 20% of incoming sunlight, while light-colored materials typically reflect 55 to 90%.
Light reflectance value (LRV) is similar and is typically applied to paints and coatings. It is defined as the total quantity of visible and useable light reflected by a surface in all directions and at all wavelengths when illuminated by a light source. LRV runs on a scale from 0 percent to 100%. The average blackest black surface has an LRV of approximately 5% while the whitest white has an LRV of about 85%.
Thermal emittance describes how efficiently a surface cools itself by emitting thermal radiation. It is measured on a scale of 0 to 1, where a value of 1 indicates a perfectly efficient emitter. Nearly all nonmetallic surfaces have high thermal emittance, usually between 0.80 and 0.95.
A roof surface’s Solar Reflectance Index (SRI) is another metric for measuring coolness. It is calculated from the solar reflectance and thermal emittance values. The higher the SRI, the cooler the roof will be in the sun. For example, a clean black roof could have an SRI of 0 while a clean white roof could have an SRI of 100. Dark roofs usually have an SRI less than 20.
The Cooling Effect of Coatings
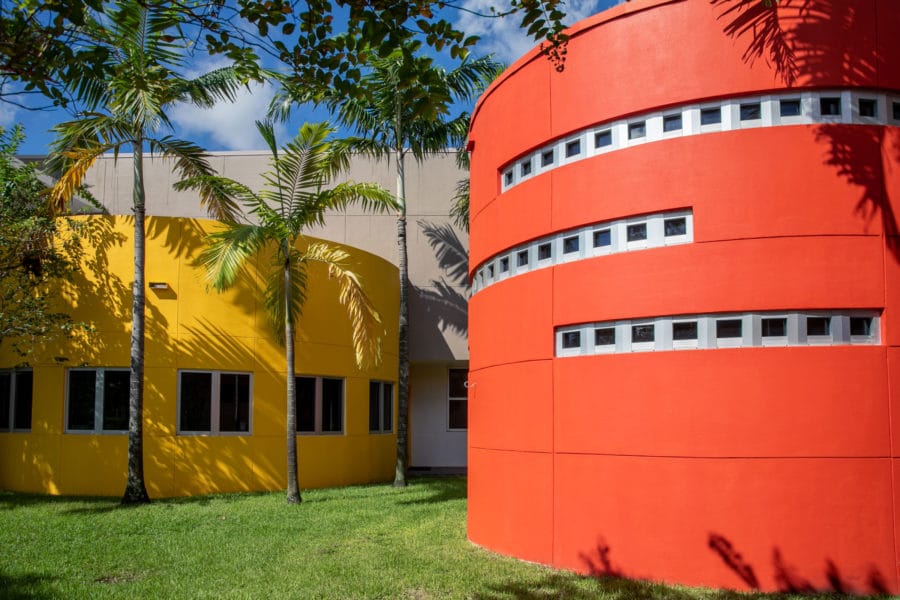
With the help of Restore Construction Group and APV Engineered Coatings, the Children’s Ability Center will be able to keep its colorful facade for years to come. Photo courtesy of APV Engineered Coatings
Short of physical shading, the best way to achieve a cool roof is by coating it, whether in the factory by the roofing material OEM or applied in the field by a professional coating contractor.
But not all coatings provide the performance needed to achieve high TSR, LRV, and thermal emittance. For example, exterior latex and premium acrylic binders in paints will break down when exposed to solar irradiance, allowing dirt, mold, and mildew to infiltrate the coated surface, which reduces TSR and related energy savings. This break down is called film erosion, where the coating chalks and wears away from the substrate and will continue to do so until the coating no longer protects the surface.
Coating systems formulated with polyvinylidene fluoride (PVDF) resin, on the other hand, resist photochemical degradation to deliver better long-term protection. PVDF’s incredibly strong carbon-fluorine bonds stand up to film erosion, even under exposure to the elements, allowing its protective properties—including TSR, dirt shedding, algae and mold resistance, color retention and chalking resistance—to last significantly longer. Dirt shedding and algae/mold resistance properties are particularly important as dirty surfaces reduce solar reflectance.
A coating’s pigments also play a crucial role in its TSR, LRV, and thermal emittance properties. For example, organic pigments can break down over time when exposed to UV energy and the elements. Complex inorganic pigments, on the other hand, contain mixed metal oxides that reflect the sun’s rays. In comparison to organic pigments, complex inorganics, especially IR-reflective types, and when used in a PVDF-based formulation, are encapsulated by the fluoropolymer for additional protection from the elemental exposure that can break them down and therefore maintaining their color for much longer.
More Benefits of Coatings
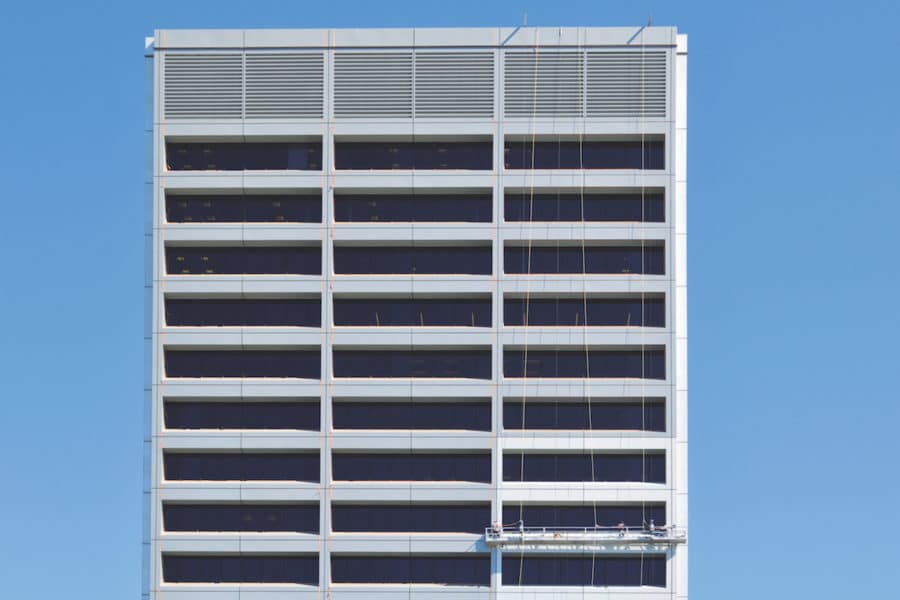
Photo courtesy of APV Engineered Coatings
The sun’s heat is one of the biggest contributors to reduced durability and longevity of roofing systems. The right protective coating can help reduce film erosion and heat absorption by reflecting UV and infrared radiation. Such high-performance coatings can also resist buildup of dirt, mold, and mildew—keeping them cleaner, reducing the amount of maintenance needed, and allowing the reflective properties to be sustained for longer.