Story at a glance:
- R-Hauz shares its experience building its first mass timber residential building in Ontario.
- The architecture firm says mass timber isn’t currently widely used in Ontario, but using it has many benefits.
- Using mass timber also reduces noise and disruption to the building’s surroundings during construction.
We recently built the first (of many, we hope) mass timber residential buildings in Ontario. The six-story avenue townhome is a new building typology for Ontario—and it’s one that offers an opportunity to build faster and more sustainably while giving residents a beautiful, functional living space.
We used mass timber to build R-Towns, our six- to eight-story buildings. Using a sustainable material as a building base is incredibly advantageous and, while not often seen yet in Ontario, achieves a goal the industry has long been struggling to reach. Our construction method creates housing quickly; the structure of our pilot was built in five-and-a-half weeks, while significantly reducing the environmental impact and offering a place people want to live in. Using mass timber also reduces noise and disruption to the building’s surroundings during construction.
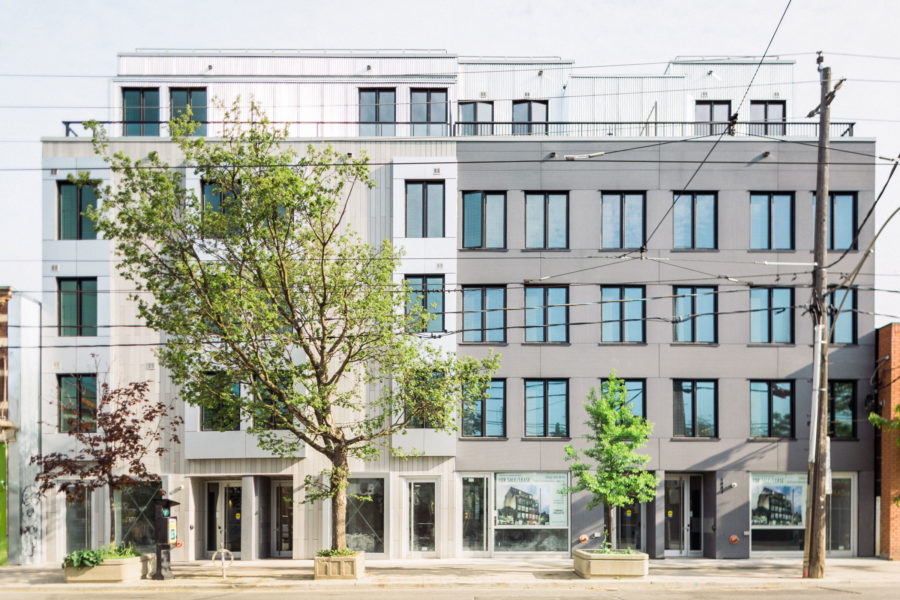
R-Hauz hopes more designers and architects will turn to cross laminated timber in Ontario. Photo courtesy of R-Hauz
The Mass Timber Institute defines mass timber as “a technological advancement that uses engineered wood products such as Glue Laminated Beams (Glulam), Laminated Veneer Lumber (LVL), and Cross Laminated Timber (CLT). They are fabricated by binding together large panels and beams under pressure using adhesives such as polyurethane, phenolic, or polymer isocyanate glues. The wood’s grain in each successive layer is stacked in alternating grain orientations for added strength. Mass timber is considered as an alternative to conventional reinforced-steel-concrete construction and is ideal for low-to-medium-rise building structures.”
So mass timber is a lower carbon alternative that has lasting environmental benefits. Forest waste is used to create prefabricated panels while offsetting emission produced by extraction through carbon sequestration and retention. For every ton of wood used in place of steel or concrete, 2.1 tons of carbon or 7.7 tons of CO2 equivalent are avoided.
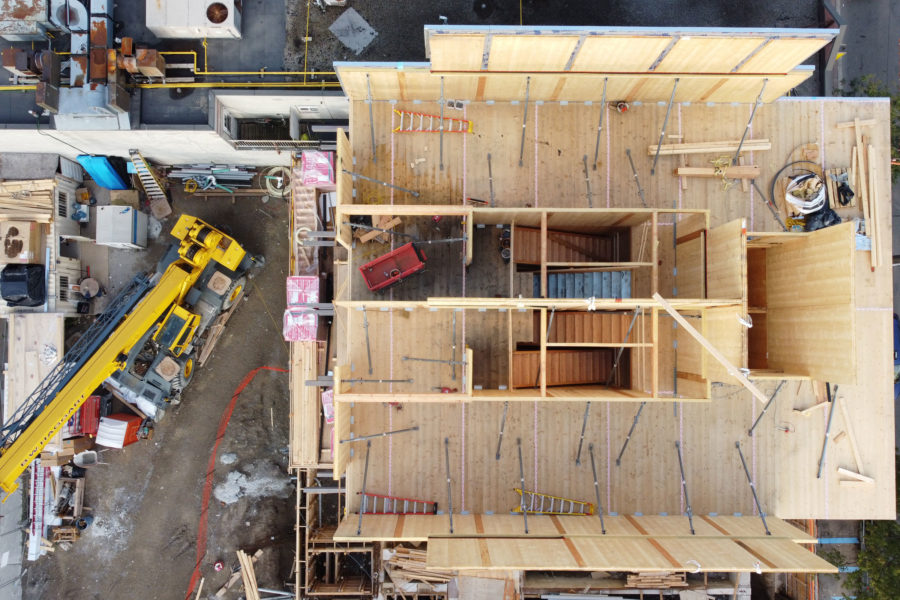
Photo courtesy of R-Hauz
Buildings and their construction account for 39% of global carbon emissions. According to the Tall Wood Institute, 80% of the embodied carbon attributed from building materials comes from structural materials, making it increasingly beneficial to select the most sustainable options. Shifting from concrete and steel construction to mass timber not only reduces the overall emissions of individual buildings but the emissions of the real estate industry as a whole.
We see that as a win-win. To add to that, the storage for carbon in wood products is a unique environmental attribute that is non-existent in other building materials. The Tall Wood Institute says wood is 50% carbon by weight, meaning substituting wood for steel and concrete within the structural systems of buildings can reduce fossil fuel use and cut greenhouse gas emissions by up to 60%.
Decarbonization is a pivotal part of our building strategy, but there are several other aspects within the design and construction phase that differentiate R-Hauz buildings. A typical urban residential construction process involves hiring a team of designers and engineers to create a site-specific design that is usually a one-off concept. Once the design is complete a contractor is hired. The usual outcome in this method is a construction phase filled with disputes, cost overruns, and schedule delays. Too many cooks in the kitchen.
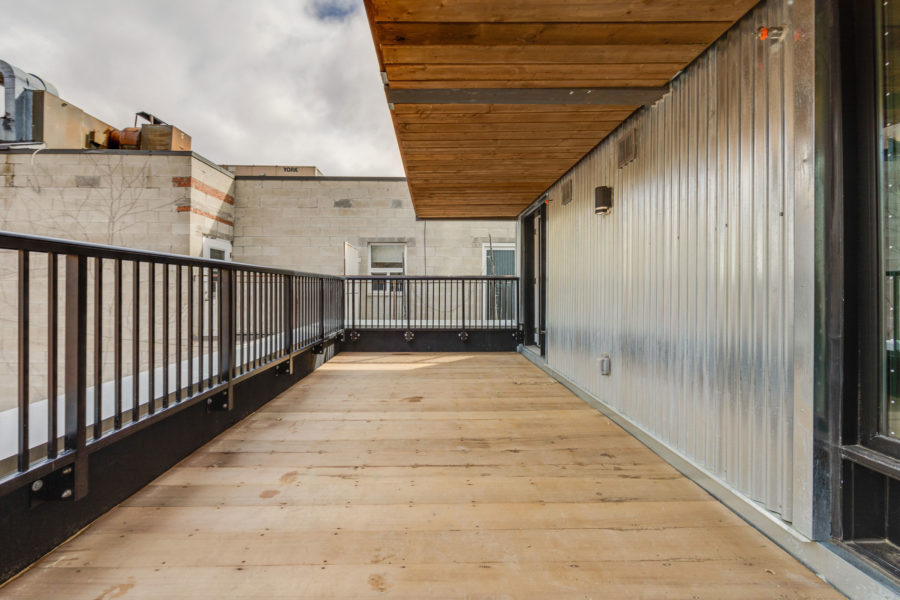
Photo courtesy of R-Hauz
After consistently observing these inefficiencies we knew we needed another approach. To create a solution we redefined the process. Better designs, smarter systems, superior materials, and more effective collaboration. We have designed repeatable building products that can be site-adjusted for different uses. Repeating our designs allows us to learn and gradually lower costs and delivery time frames all while improving building quality.
Our original designs are created using BIM software that transforms the designs into 3D models that can then be manipulated to fit the landowners’ needs. These product designs are adapted to each site by our design team. The supply chain strategy allows for the design and construction teams to collaborate more closely, limiting miscommunications and sharing in cost savings.
Our building strategy is to prefabricate as many building elements as we can off-site for installation on-site. With our wall and floor panels in mass timber, less time is needed to erect our buildings than a typical concrete or steel structure. Other elements like plumbing systems are also evaluated for off-site prefabrication. Prefabrication benefits in our buildings? Better quality (fewer deficiencies) and faster assembly time on-site, saving money and time.
Industries can be reluctant to change, and the construction industry is, for the most part, still doing things the same way it has for 100 years. The sheer number of changes required to introduce new ways of building can be discouraging, but the pilot R-Town serves as a testament to the effort behind these changes—and one that has paid off.
Most recently developers Windmill Developments and Leader Lane Developments announced a partnership to bring this approach to condos, announcing three main street in-fill projects in West Toronto. As a first for a condo project in Toronto, each building will utilize CLT construction prefabricated off-site to significantly reduce embodied carbon for the structure, construction timelines, and construction waste and overall carbon emissions.
Windmill and Leader Lane will be tapping our team, R-Hauz, as the design-build contractor on each building. In speaking about this project, Jonathan Westeinde, founder of Windmill Developments, says that not only will these buildings be built faster and with less waste, but they will also be the most sustainable homes available on the market.
Don Manlapaz, partner at Leader Lane Developments, adds that it will support missing middle housing types, introducing soft density into supply-constrained neighborhoods that are experiencing high demand.
This project demonstrates the ability to build better quality buildings—focused on the health and well-being of the end user. At the same time we are able to build at a lower cost with more certain occupancy dates and shorter interim occupancy periods for buyers. We build by a “small is beautiful” scale and are very excited for this project, which will offer condos in a city at a gentle scale where the neighborhood is the focus. The buildings will blend in with characteristics of the neighborhoods they are in, highlighting ties to nature and fitting in just as a good neighbor should.