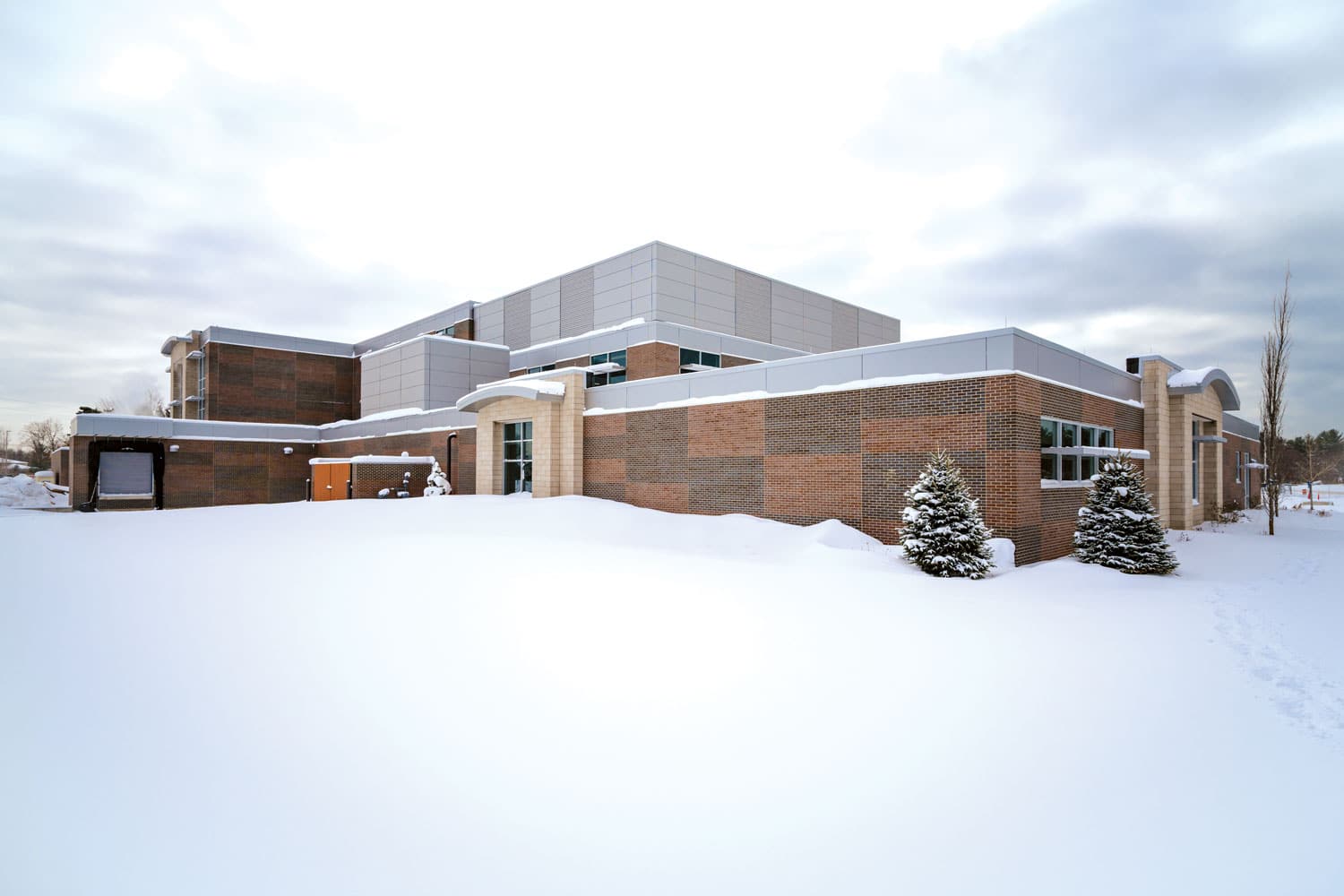
The AECOM team chose YKK AP products to stand up to the cold. [Photo: Joseph Stanford Photography]
Patients need a comfortable environment for the best care, and in a cold climate like that of Michigan, the need becomes even more apparent. Occupant comfort was a critical factor for a new Health Pointe facility in Grand Haven, and the project team sought a high performance curtain wall system from YKK Architectural Products (YKK AP) to achieve just that.
Jim Boles, architect at AECOM, knew his team had to account for many extremely cold days in a row at the Spectrum Health integrated clinical facility, anticipated to open in spring. That’s why AECOM chose YKK AP’s enerGfacade® products—the YCW 750 XT curtain wall
and the ThermaShade® sunshade system—to minimize frost build-up while optimizing comfort and energy efficiency.
Of course, sunlight helps patients, too, and the design team was committed to ample daylighting. YKK AP’s exterior glazing systems provide natural light without excessive solar heat gain. “There are a lot of studies that link natural light as a healing factor, and that was important to the design of the facility,” says Sean Easter, LEED AP architect and manager of planning and design at Spectrum Health. “YKK AP yields one of the best thermal performances, exceeds our standards, and also exceeded green building codes.”
FROM OUR MARCH+APRIL 2018 ISSUE
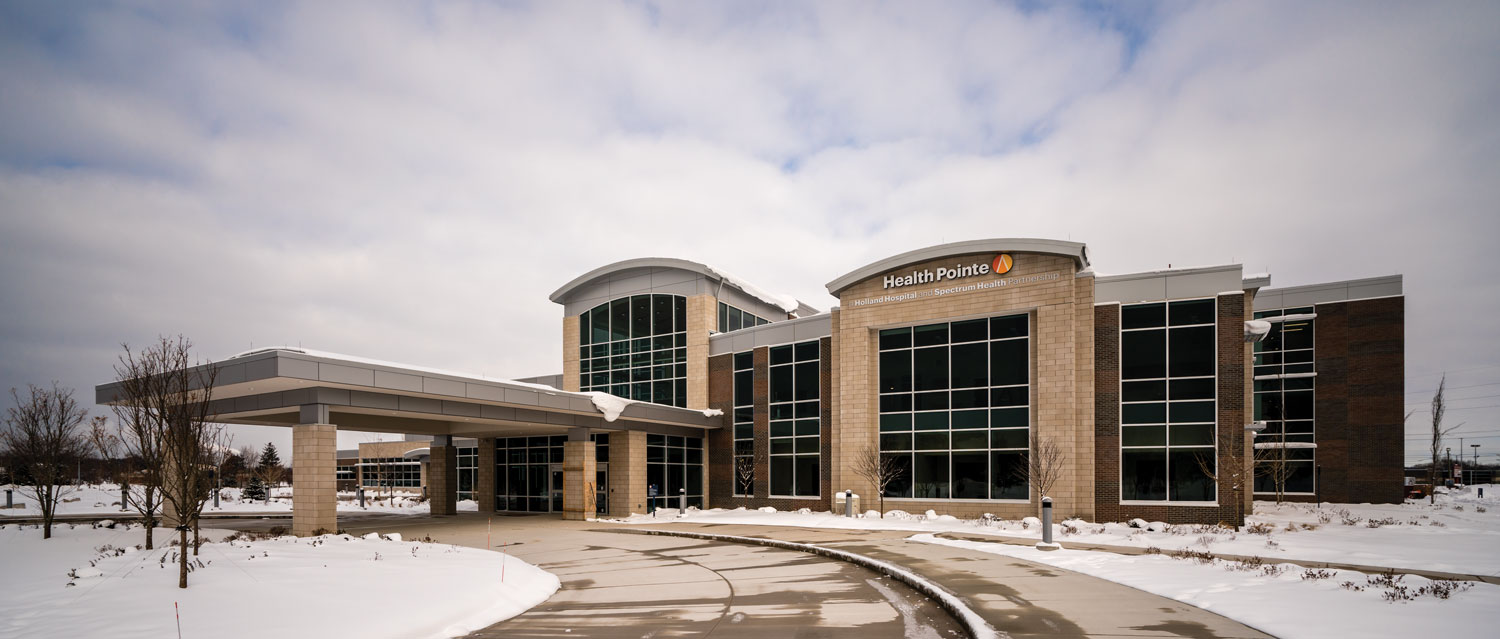
[Photo: Joseph Stanford Photography]
Over the past 25 years, YKK AP America Inc. has transformed from a modest regional facade distributor in the Southeast into a technology-driven, sustainable building products manufacturer nationwide. Its parent company, YKK Group, was founded as a fastening product manufacturer in Japan, but now the international company creates a range of products—from pressurized space suit zippers to car seats to fire-resistant shutters. As the U.S. division of the architectural products group of companies, YKK AP is known for its energy-efficient commercial fenestration solutions and innovative residential doors and windows.
Engineering for Efficiency
“We’re providing sustainable framing solutions for the entire building envelope that improve its strength, energy efficiency, and longevity,” says David Warden, brand manager at YKK AP. The company’s enerGfacade® line provides the highest level of thermal performance, exceeding even the industry’s most stringent green standards by cutting back on waste, controlling energy costs, and simplifying installation. The product line is both sustainable and affordable, and upgrading a building’s framing system can be a seriously cost-effective step toward LEED certification.
YKK AP’s thermally broken curtain wall significantly improves the insulation of the building envelope. The YCW 750 XT is part of YKK AP’s high-performing aluminum fenestration system series, which features multiple thermal barriers to minimize total heat loss. This curtain wall system is combined with customized sun-shades to reduce solar heat gain.
The ThermaShade system is also the only sunshade on the market that includes a thermal barrier in the anchor bracket. “Adding the sunshade improved solar heat gain without deteriorating the thermal performance by 5% or more like traditional anchor options,” Warden says. “With our YCW 750 XT system, even the pressure plate fasteners do not bridge or compromise the thermal break.”
Fortunately, the facade system also leaves room for creativity when it comes to design, as YKK AP offers a range of installation and aesthetic options. “YKK AP was able to get us the matching finishes and accommodated our glass types,” Easter says. “The blend of exterior materials—curtain wall, brick, and metal panels—works well and fits the community and setting.”
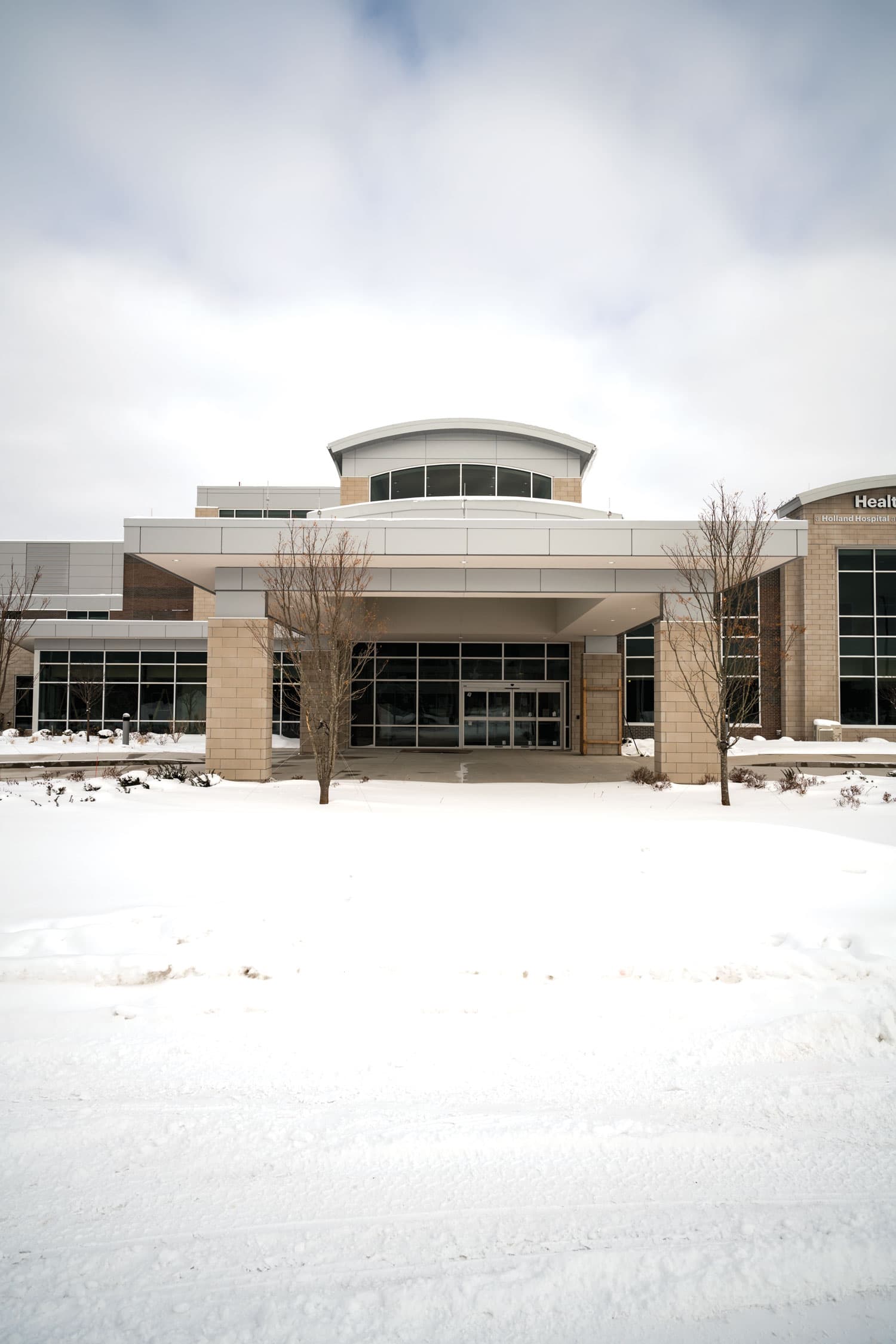
[Photo: Joseph Stanford Photography]
How We Did It
In the Grand Haven project, Boles says the curtain wall around the perimeter of the building was the biggest challenge due to the condensation resistance factor (CRF) requirements. AECOM chose the YCW 750 XT curtain wall and ThermaShade sunshades because the combination offered the best CRF and U-value. Ultimately, he says the curtain wall ended up being a straightforward part of the project.
YKK AP’s accurate anchor conditions helped ease the installation process, too. “YKK was very attentive to detail in creating anchor conditions during the engineering stage,” says Bryan Dennis, glazing contractor at Architectural Glass & Metals, who was installing YKK AP’s fenestration systems at Health Pointe in winter.
Dennis says the engineering documents his team received from YKK AP helped in terms of efficiency when they were in the field as well. YKK AP handled all the shop drawings and developed 15 anchor conditions for the project, all of which were the perfect size and design for the building. “To have a curtain wall manufacturer catch all of the different conditions was impressive,” Dennis says.
The Future is Green
YKK AP aims to become an even more sustainable manufacturer, and Warden says customers can expect even more energy-saving products from YKK AP in the future. “We have a goal to become 75% recycled-based on all processes by end of fiscal year 2018. That means all waste produced in Dublin Plant and emissions.”
The company also plans to utilize Environmental Product Declaration (EPD) and Life Cycle Analysis data to refine and manage the manufacturing stage to better the overall environmental product performance. “We continually look for ways to improve from an environmental standpoint,” Warden says.
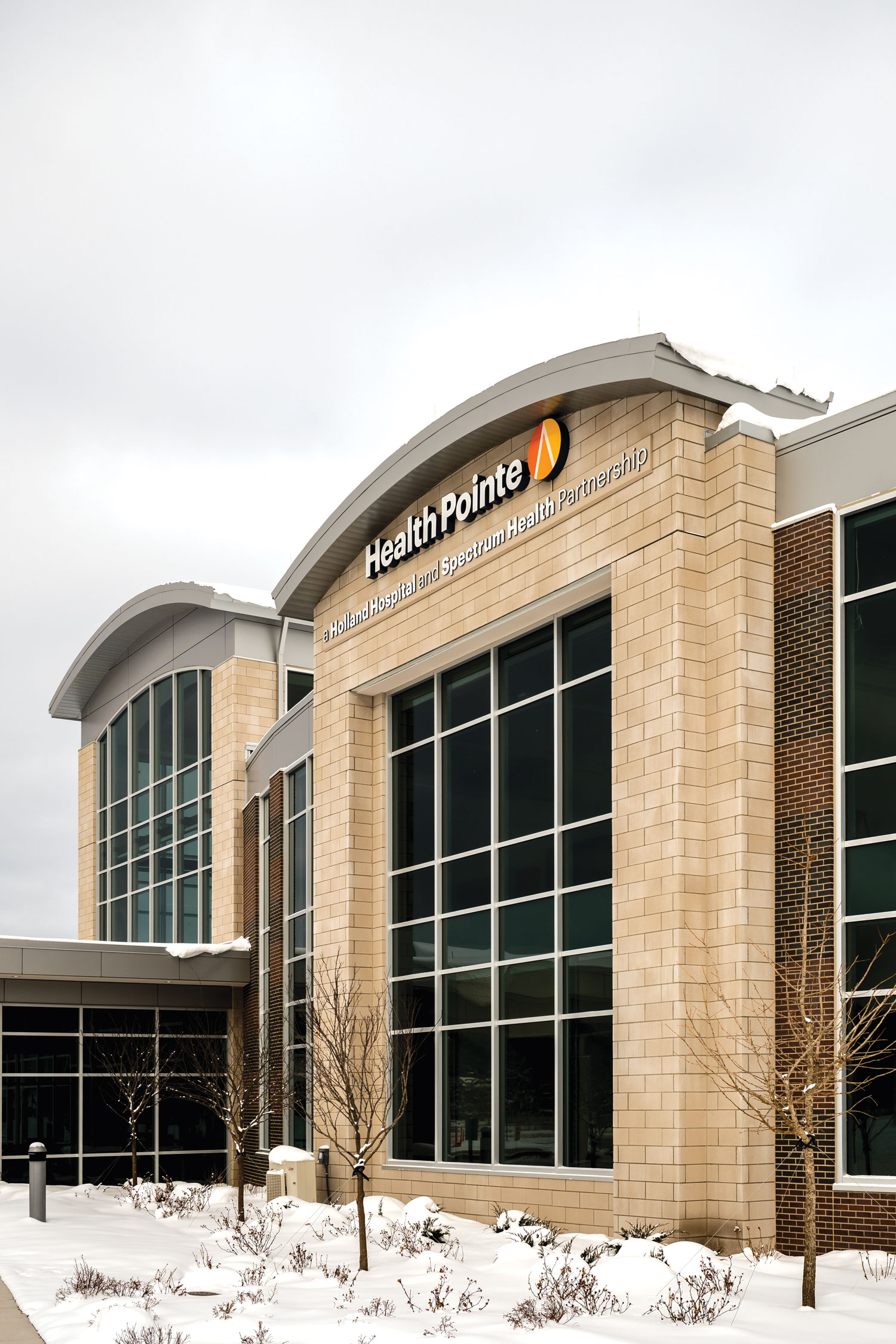
A blend of curtain wall, brick, and metal panels makes up the exterior of this Michigan project. [Photo: Joseph Stanford Photography]
Making Manufacturing Greener
David Warden, brand manager at YKK AP, says the company takes two main approaches to sustainability. First, they develop and manufacture innovative products designed to block heat, provide insulation, and improve ventilation in commercial buildings. Then they take that one step further by making their manufacturing process as green as possible.
YKK AP’s environmentally friendly manufacturing plant in Dublin, Georgia, is a prime example of how the company considers sustainability during production. With a 73% recycling rate, this plant is raising the industry’s green standards. YKK AP recycles all of its aluminum waste on-site and has reduced the amount of other material waste sent to landfills by 40%. The factory’s regenerative burners reduce the fuel used for melting and casting by 50%. The plant also captures and burns 93% of all solvent emissions from the paint line and uses innovative strategies for wastewater treatment.
Furthering its sustainability initiatives, YKK AP became the first facade manufacturer to voluntarily offer third party-certified EPDs for all the products in its portfolio in 2015. EPDs, or environmental product declarations, make manufacturing methods more transparent, as customers can see the exact effects of products to aid them in their decision-making process.
Learn more about YKK AP and see more gb&d framing stories.