Story at a glance:
- Deep energy retrofits can help reduce an existing building’s energy use by at least 40% but can come with a considerable upfront cost.
- Historically deep energy retrofits have been hard to achieve because of lack of incentives and financing from the state and federal governments.
- Prefabricated architectural panels for a building exterior are a cost-effective solution to meet energy requirements, improve property value, and minimize occupant disruption.
Retrofitting older buildings to meet modern efficiency standards and regulations is no easy task.
In a 2021 study of 14,000 people across the US and Europe, 81% believe energy-efficient buildings are important, yet only 11% felt knowledgeable about seeking advice, applying for funding, and finding qualified contractors to help them achieve their energy efficiency goals.
In the commercial space, a different study from global real estate services company JLL estimates 90% of office buildings in the world’s most developed cities are more than 10 years old—and most do not meet today’s energy efficiency standards for new builds.
For architects, developers, and builders looking to update buildings, deep energy retrofits can help reduce site energy use by at least 40%. And with new efficiency legislation on the horizon across state and federal governments, improved efficiency in older buildings may soon be a requirement.
We asked experts David Hutchinson, deep energy retrofit development specialist, and Chuck Bundrick, key account executive for commercial construction and renovation, at Tremco CPG Inc. about the barriers of deep energy retrofits and how solutions such as prefabricated architectural panels can push the industry forward.
The Challenges Behind Deep Energy Retrofits
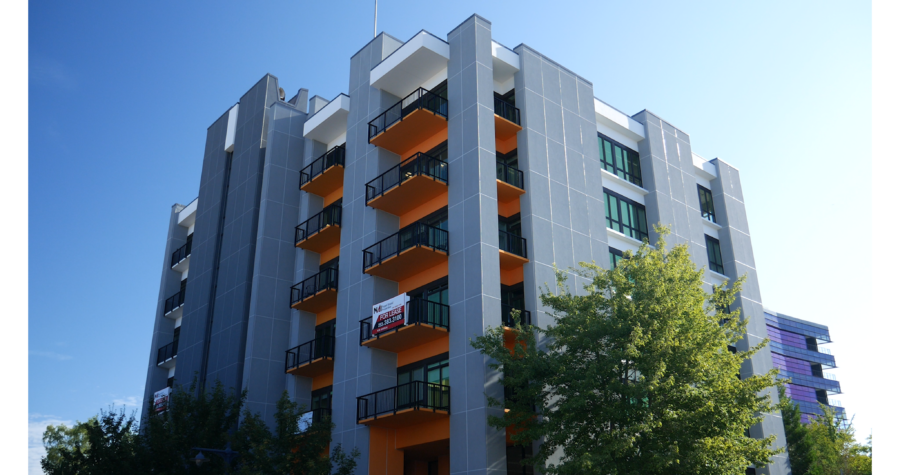
Photo courtesy of Tremco CPG Inc.
Like other energy-saving strategies, deep energy retrofits require a whole-building approach to maximize their long-term impacts.
In states like New York, which is spearheading legislation around deep energy retrofits, it all starts with the building envelope.
“There has been a shift more recently into really focusing on the envelope,” Hutchinson says. “Glazing is obviously a big part of what’s happening now through weatherization, but groups like IIBEC (International Institute of Building Enclosure Consultants) have started to understand that the envelope is really what starts. If we’re going to be fixing the mechanicals, HVAC, and all these things, if you do not fix the envelope first, it’s wasted money and time.”
An airtight building enclosure enables all the other energy-saving practices to stay within the structure, as opposed to leaking out of inefficient windows and poorly insulated walls.
In the western United States, however, the approach has been broader, Bundrick says.
“The West is still several steps behind New York,” he says. “There’s a lot of effort on electrification in California. That being said, Colorado, Washington, and a few other states have started to ramp up their demand for energy efficiencies on existing buildings. They’re starting to break apart from where California is going. They’re saying, ‘Yeah, we still need the electrification, but we do need to deal with the building envelope.’”
The other issue is cost. Deep energy retrofits can involve a considerable upfront investment, and governments are just now starting to provide the incentives and financing programs that architects, builders, and developers need to be successful.
While many champion these sustainability initiatives, the question remains: How is any of this getting paid for? “There have been more conversations that are productive on the insurance side, the finance side, the green bank side, and people are wrapping their arms around what this actually looks like,” Hutchinson says. “The formula is already there. We just have to catch up with it.”
But even with some financing available, Bundrick thinks many builders will still have a hard time. “New York and California are the two states with the densest building stock in the country,” he says. “They have a pretty aggressive goal of trying to retrofit these buildings, and there’s just no way that’s going to happen—unless you’re going to start talking about prefabrication.”
The Benefits of Prefabricated Architectural Panels
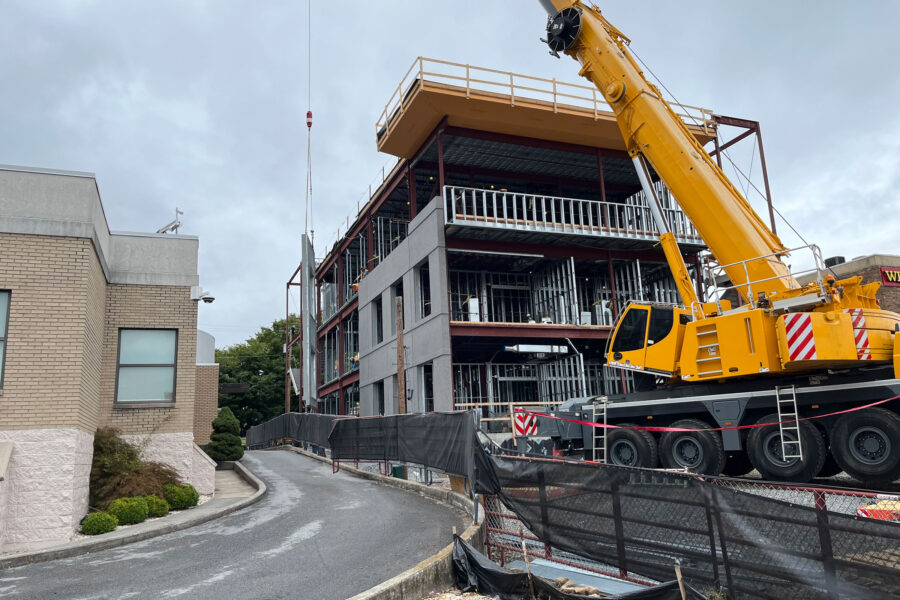
Photo courtesy of Tremco CPG Inc.
Tremco’s prefabricated architectural panels were designed as a cost-effective solution to the envelope-first approach required of deep energy retrofits while eliminating the need to displace tenants in the process. Both Hutchinson and Bundrick were instrumental in their development.
“The majority of all deep energy retrofit projects are generally tenant-in-place,” Hutchinson says, where building occupants remain onsite during the renovations. “If you’re in construction, you know the labor force, you know the timetables. You can’t be working on apartments, for example, for months and months and months. Retrofit projects have very tight windows to get completed. The only way to do an envelope with the timeframes that we’re looking at, with the labor shortage, and everything else, is through prefabrication.”
Constructing the cladding panels in a controlled indoor setting minimizes the space and time required on small, urban jobsites. They can be assembled year-round in the factory and installed on the building in most temperature conditions, reducing weather delays and subsequent costs.
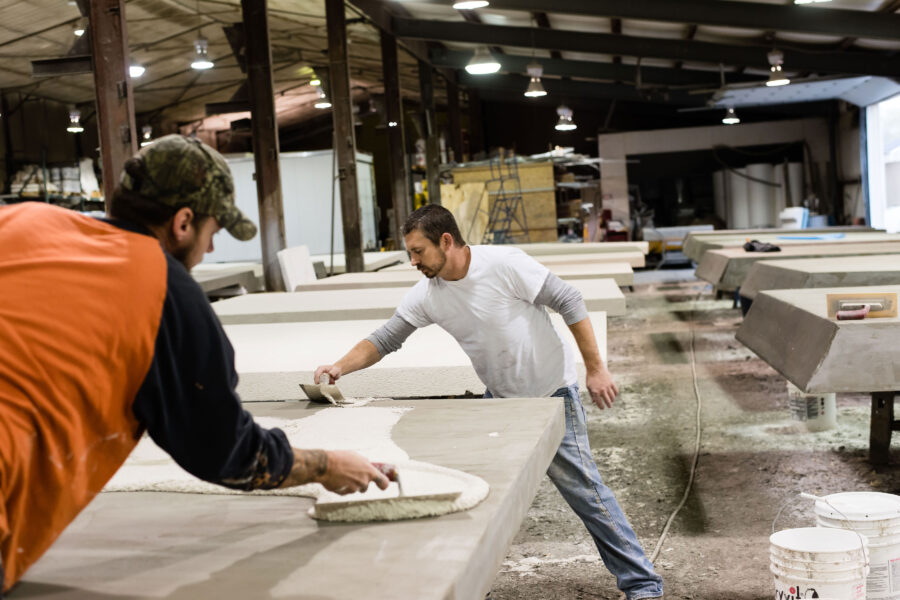
Photo courtesy of Tremco CPG Inc.
Bundrick agrees. “Prefabrication can drive the price point down, which will help accelerate opportunities and create the budgets that makes deep energy retrofits a lot more affordable,” he says.
These exterior panels can be customized in varying sizes, shapes, and modern finishes, which offer more design flexibility for the architect and owner and can have a dramatic impact on older buildings’ facades.
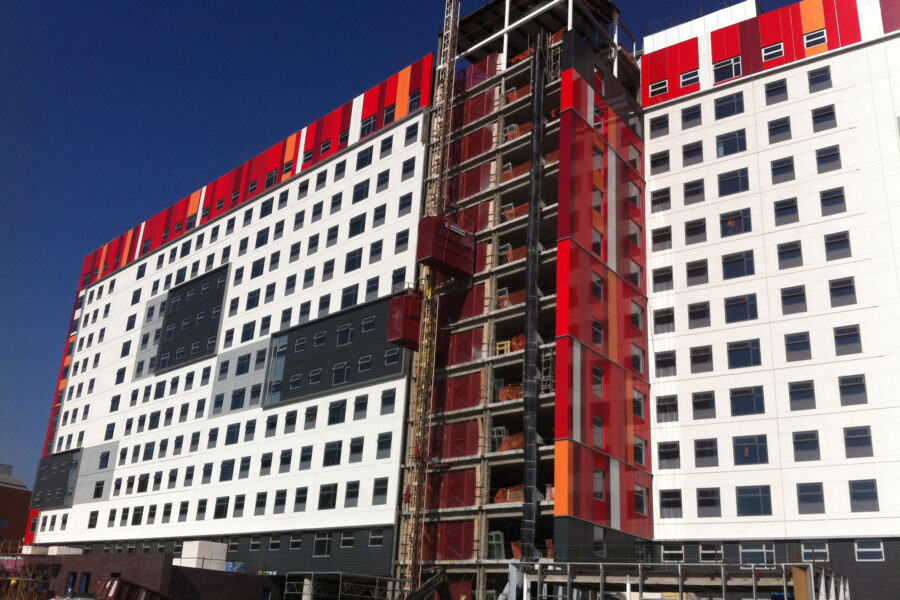
Photo courtesy of Tremco CPG Inc.
“Panels give them more freedom from a design standpoint, and when you’re working, say, on buildings from the 1960s, by the time they are done they’re going to be contemporary-looking buildings,” Bundrick says. “So there’s also the conversation of what you’ve done to increase the property value. Not only is it performing better, but now you’ve changed the look of the building, and now the property value is going to go up.”
Beyond aesthetics, perhaps the most important benefit for deep energy retrofits is that prefabricated architectural panels can be designed to meet specific energy requirements.
“Every deep energy retrofit project starts with an energy model. The panels allow you to design exactly to what you need. You can design to your thermal performance, your air leakage, to everything that you’re requiring to meet your standards and the state’s standards,” Hutchinson says.
“Prefabricated panels are not just an aesthetic play or a get-the-building-sealed-up play. They also look at what a building’s performance is going to be in five, 10, 20, 30 years,” he says. “That’s what you have to be able to explain to owners—that this is not just a short fix. This is not a turn-and-burn building. This is the next 100 years of your building. That’s what the panels are able to do.”