The technology to improve one of the world’s biggest industries is here. 3DR Site Scan’s impact on construction will be huge.

3DR Founder Chris Anderson launched Site Scan, a complete drone data platform, in 2016. [Photo: Courtesy of 3DR]
It’s no secret that construction—the world’s second largest industry—has room for improvement. In many parts of the world it remains an old, traditional business, fraught with delays and inefficiencies. But construction teams are looking to change that, and they’re adopting new technologies, like drones, to build faster and smarter.
“Construction is one of the least digitized industries in the world,” says Chris Anderson, founder of 3DR, the leader in drone software for construction, engineering, and mining teams. “It’s paper and pencil and flip phones. It’s ripe for transformation, but because it’s a large and relatively conservative industry, it’s been resistant. Today, that’s changing.”
3DR came to fruition after Anderson—the former editor-in-chief of Wired—partnered with Jordi Muñoz, a 19-year-old from Mexico who made a fully functioning autopilot using circuitry from a Nintendo Wii remote. In early 2016 3DR launched Site Scan, a complete drone data platform with drone, flight app, and a web app for processing drone photos into maps and models and analyzing results. Site Scan offers a suite of tools for actually getting insights out of drone data, such as measuring distances and volumes, overlaying blueprints to compare design to reality, and it also makes it easy to export data into other tools like Autodesk BIM 360, Revit, Civil 3D, and InfraWorks 360. This helps teams, clients, and other stakeholders get real-time updates about construction projects so they don’t have to be onsite to see whether a project is going as planned.
FROM OUR SEPT+OCT 2018 ISSUE
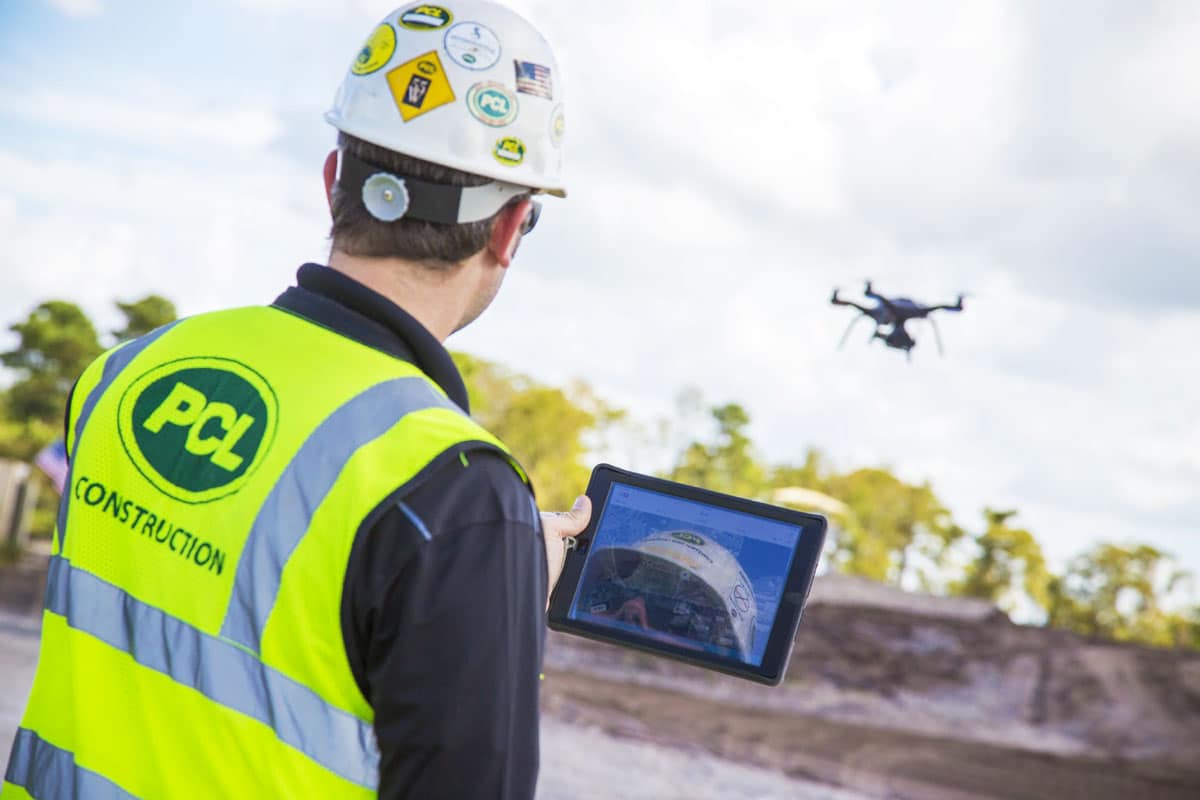
Drones are taking surveying to new heights, as they can survey a site in 20 minutes compared to three hours for a traditional survey. [Photo: Courtesy of 3DR]
The Evolution of Drones in Construction
3DR came to be after Anderson and his wife—both technical people—wanted to get their kids interested in science and technology. “The kids showed almost no interest,” Anderson laughs. But there was one experiment that sparked something—at least for Anderson. He’d come home with a robotics kit and an airplane kit, but the kids weren’t impressed. Robots were boring, they said. Airplanes were boring. “I said, ‘Well, what about a robot airplane?’” he recalls. So they made one, and Anderson was taken aback. “It worked just well enough to blow my mind. I was like, ‘This should not happen. You shouldn’t be able to put Lego parts in a model airplane and create something that is essentially a military drone.”
Anderson had to learn more. He created DIYDrones.com, meeting Muñoz through the website, and things took off. As hardware was revolutionized with the invention of the iPhone, drones suddenly became a realistic—and in demand—product. But taking the technology to the next level wasn’t entirely intentional. He sent Muñoz a $500 check for components, and the demand was overwhelming. Soon they were making 1,000 drones a week. They assembled their first drone kits by hand and shipped them in pizza boxes. In 2012, Anderson left Wired to focus on the venture full-time, scaling up on hardware while keeping the software open source. “We became the software company I always wanted to be,” Anderson says. “The challenge was which part of the world were we going to measure.”
Making a Better Built Environment
3DR considered various applications for drones at first, from agriculture to insurance. They felt Site Scan could make the biggest impact in construction, and they partnered with Autodesk to help make that happen. At the time, Autodesk was helping to digitize construction with its AEC Collection and was putting a big focus on building information modeling (BIM) with its BIM 360 platform. Traditionally, project teams designed buildings on-screen, but the process went analog the moment construction began. “The digital tools to design were not the digital tools to build it or to maintain it afterward,” Anderson says. “If you’re commissioning buildings, you want transparency to see how it’s going because you’re going to be paying for it,” Anderson says. “BIM brought accountability and visibility into the costs.”
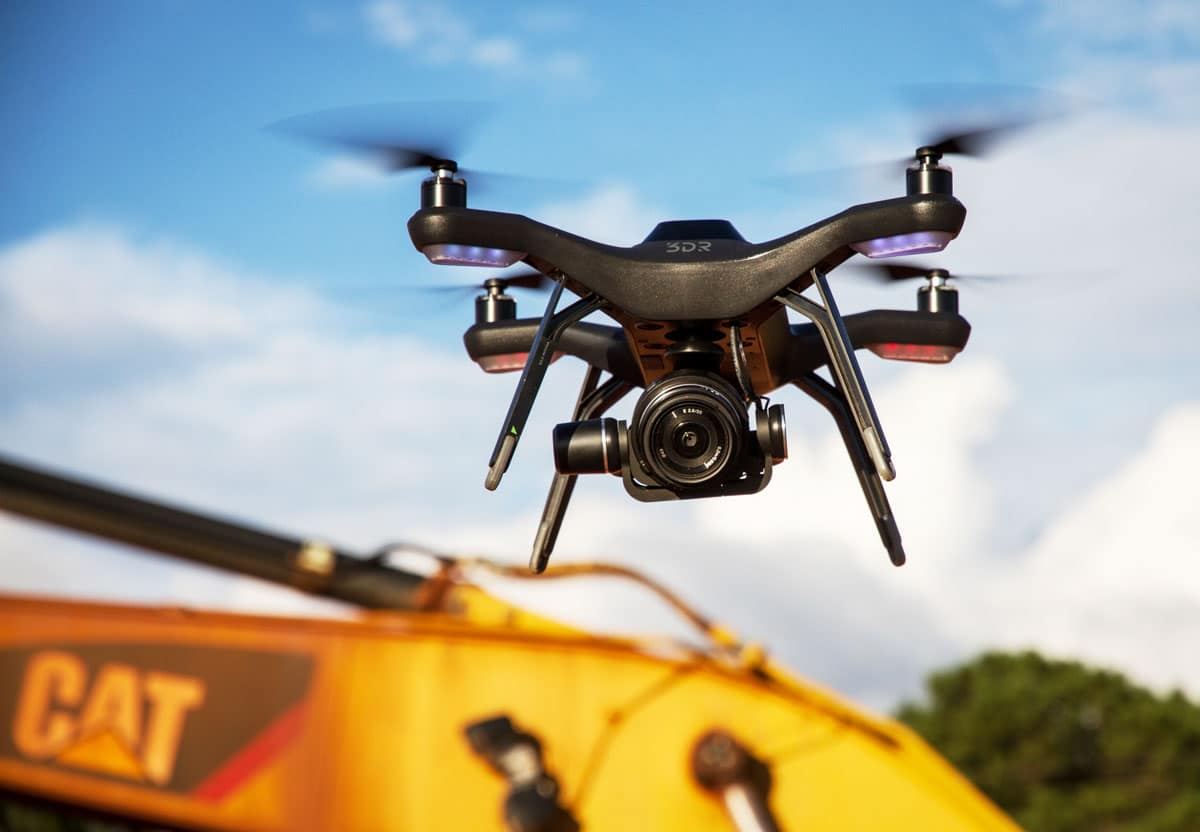
[Photo: Courtesy of 3DR]
3DR wanted to digitize construction projects afterward, too, scanning at every stage. “Today buildings do have a living model, and when you’re done you have a very high resolution model of the building, which continues to be updated and used for maintenance and renovation,” Anderson says. “Autodesk had everything except for the capture part.” The easiest way to digitize the site was from the air, so 3DR became the capture solution, integrating with existing Autodesk tools and focusing on the built world.
The partnership made perfect sense. While a project may look perfect in CAD, the story often differs onsite. Across the industry, trillions of dollars can quickly be lost in change orders, rework, and schedule slips. Anderson says construction companies often underbid projects knowing they’re going to make the money back in change orders and overruns. “When you look at the inefficiency in the industry, the general consensus is there’s a 30% cost savings just waiting to be taken when you introduce BIM, but there may be even more.” The typical commercial construction project runs 80% over budget and 20 months behind schedule, according to global management consulting company McKinsey & Company.
Having a paper trail is beneficial, especially for improving communication and resolving disputes. “Some construction projects end in a lawsuit because of cost overruns or schedule overruns, and someone has to pay,” Anderson says. “Having this transparent paper trail of the entire site settles the disputes really quickly.”
But there’s environmental efficiency to be had as well. 3DR is currently working with cement companies, for example, scanning plants to identify heat leakages and breakdowns in insulation. “That ability to monitor that site from a thermal perspective is an opportunity to reduce emissions,” Anderson says.
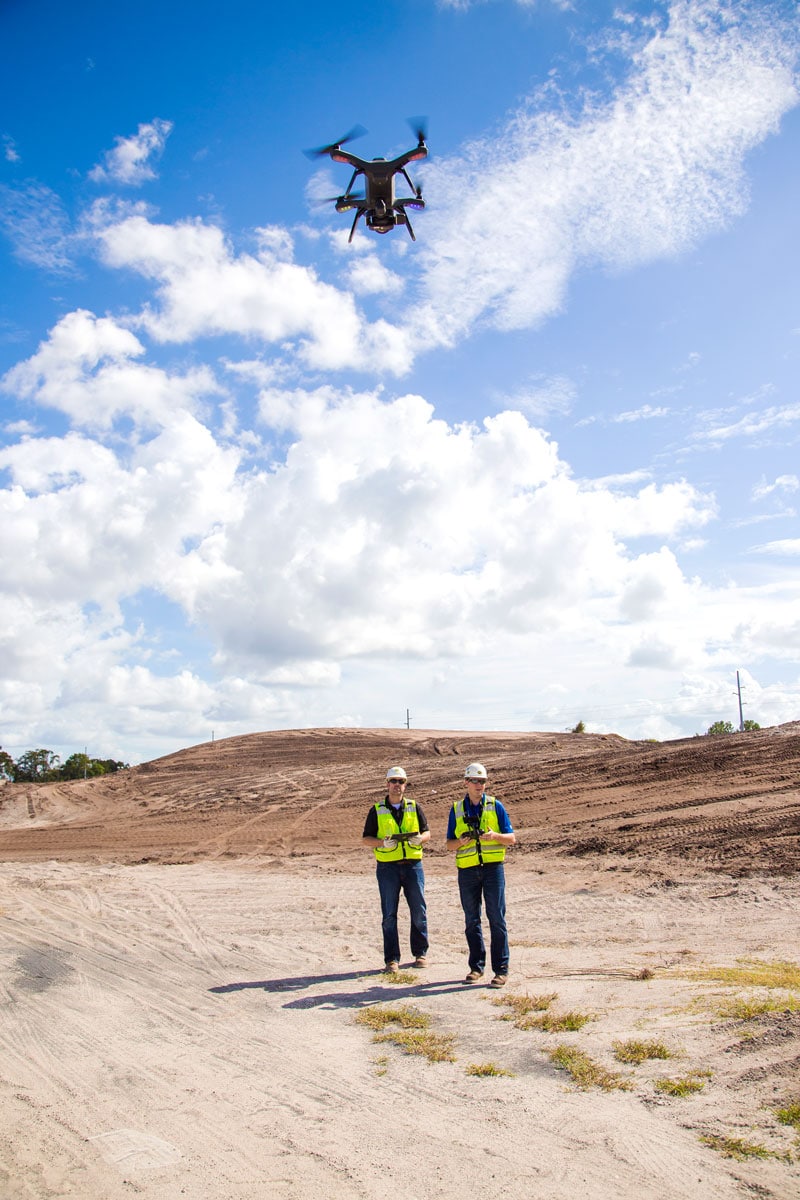
[Photo: Courtesy of 3DR]
Proven Results
Site Scan has already been used on some impressive construction projects, streamlining everything from the Atlanta airport to large factories. Right now 3DR is working with Arcadis in Qatar on a huge highway project to be finished in 2018. The client wanted fast, accurate volumetric calculations for earthwork throughout the roadway. “When we were preparing the business case and looking for a drone solution, Site Scan stood out compared to alternatives,” says Paul Kawuma, Arcadis’ innovation and infrastructure BIM manager. “We liked how easy it was. We could trace the area to survey using the tablet, then the drone will fly itself and capture the images. We could then upload the images directly from the drone to the cloud—which plays a key role in streamlining the drone to data process—and they start processing into orthomosaics and other deliverables automatically.”
The traditional survey took three hours compared to the drone survey, which took 20 minutes. The drone captured substantially more data points, too: more than 1.5 million data points compared to less than 200, and the elevation profile based on that data was far more accurate. “When it comes to ease and efficiency, drones are taking surveying to a whole new level,” says Liam Kirk, business director at Arcadis.
Digitizing and capturing a site has many more benefits, too. For one, it allows you to identify problems, or clashes, early. “If a concrete slab is in the wrong place you can spot it early on because you can compare it with the underlying CAD file,” Anderson says. Without Site Scan, you rely on local site managers to check, but Site Scan is automatic. “If you catch clashes early they aren’t too expensive to fix. If you miss it, you have to tear things down.”
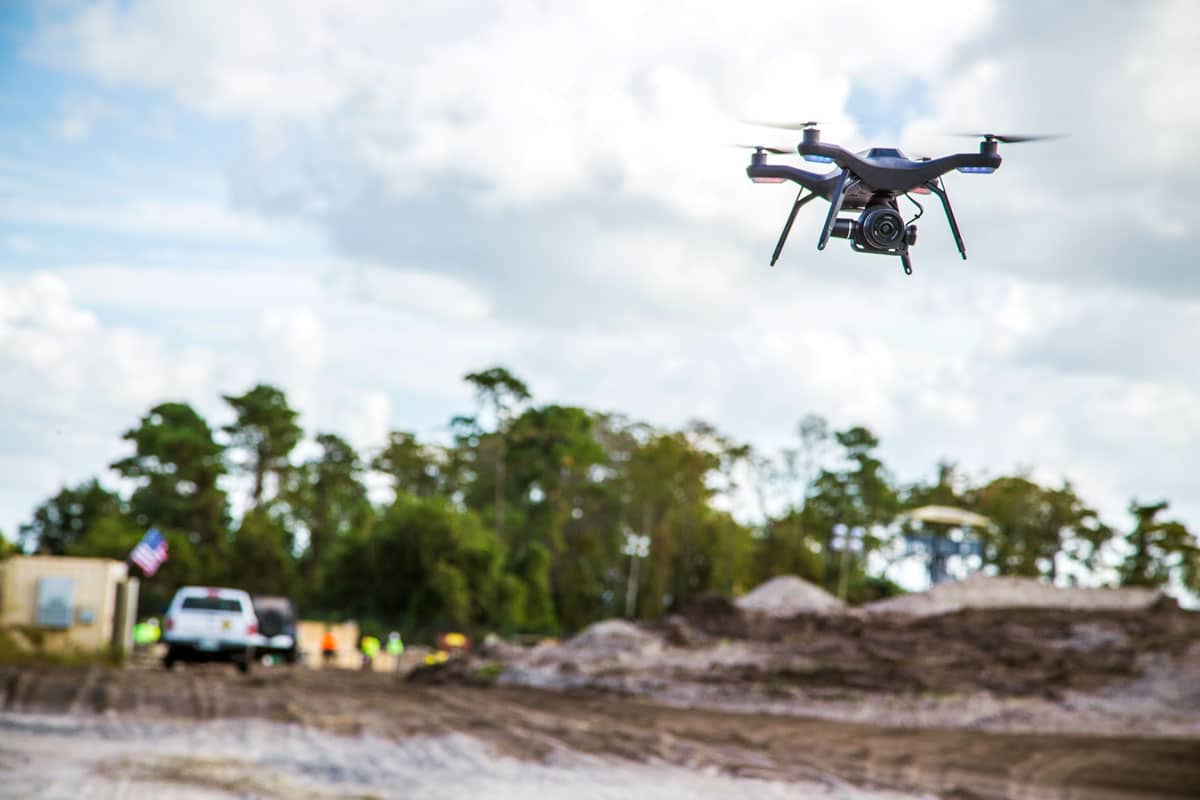
[Photo: Courtesy of 3DR]
Site Scan also reduces wasted resources. Consider, for example, a hole that needs to be filled with sand. Most current contractors estimate how much sand to order by the truck load. “Holes are ‘guesstimated’ in terms of cubic yards. You often have too much or too little,” Anderson says. “If you have too little you delay the project. If you have too much you wasted a resource.”
Just the Beginning
While drones have been used to scan sites all over the world, Anderson says it’s only the beginning. He envisions an industry where sites are scanned daily or even hourly, compared to the current scanning done by a surveyor maybe once or twice in a project.
Right now drones are focused on the exterior, while much of a project’s cost is on the inside—after the walls go up. Anderson says capturing interiors is the next frontier. “We’re working with a number of companies to bring Site Scan indoors,” he says, adding that they can use technology like rovers to get a more in-depth picture of projects even after work moves inside. He expects this to be a reality by late 2018. “Why shouldn’t you have something like this when it’s something as big and important as a construction site?”
Timeline
2007 – Chris Anderson builds his first drone at home with his kids using Lego kit parts and goes on to found DIYDrones.com.
Later in 2007 – Through DIYDrones.com, Anderson meets Jordi Muñoz, who becomes a partner in creating the first drone prototype.
2012 – Anderson and Muñoz found 3DR. Anderson quits his job at Wired.
2014 – 3DR takes drones mainstream. First ready-to-fly consumer products are released.
2015 – Solo, the world’s first smart drone, launches.
2016 – Site Scan launches.