Story at a glance:
- Sustainable concrete has grown in popularity as designers and developers have prioritized low carbon solutions.
- Holcim’s ECOPact low-carbon concrete can reduce emissions by up to 90%.
- Performance standards and government initiatives are helping push the industry toward greener concrete options.
One of the megatrends of the 21st century is the unprecedented urbanization of the world’s population. According to the United Nations, more than half of the global population currently live in urban areas, and that number is projected to rise to around two-thirds by 2050.
“In 2050 we’ll have 10 billion people on the planet, and to be able to accommodate that we’ll have to build the equivalent of New York City every month,” says Michael LeMonds, chief sustainability officer for Holcim US, a leading producer of building materials. “The pace is staggering.”
The scope of the physical infrastructure—housing, roads, schools, places of work and worship—that will be needed will place additional stress on the planet’s resources and climate, driving the need for sustainable construction solutions.
One of the biggest challenges is that the world’s most popular building material is also a major contributor to climate change—with some studies suggesting the production of concrete is responsible for 4 to 8% of CO2 emissions alone.
“Globally concrete is the most used material for construction because it can be made just about anywhere for relatively little cost with mostly local materials and low-skill labor,” says Dan Getz, structures global practice director at HKS, a leading international architecture and engineering firm.
He said concrete’s popularity with architects, developers, and contractors is also derived from the fact that it is a durable, flexible, inherently fireproof, and resilient building material option.
Given that concrete offers such a comprehensive solution for builders, how can the industry drive dramatic reductions in CO2 emissions without lowering the performance of our built environment?
The Move Toward Sustainable Concrete
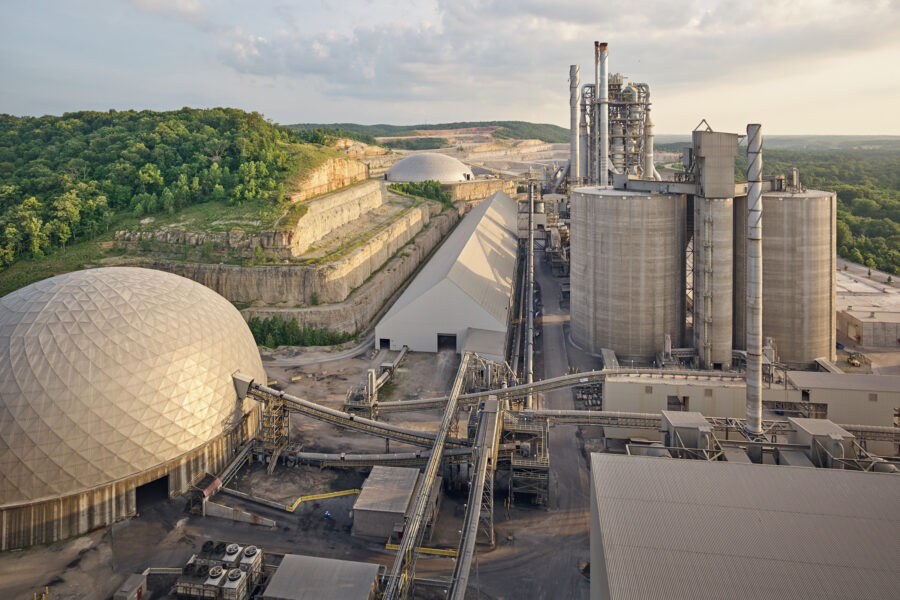
Photo courtesy of Holcim US
Fortunately the last two decades have seen a marked increase not only in the construction industry’s awareness of climate change but also its awareness of the carbon footprint of traditional concrete. This has led to a growing push for green concrete solutions, both from industry players and from government administrations across the US and the globe. “The concrete mix of 20 years ago is not the concrete mix of today,” LeMonds says. “The low carbon concrete space has had significant uptake since the 2000s.”
Across the market there are a wide variety of sustainable concrete solutions. Many innovations include the replacement of traditional Portland cement, which emits large amounts of CO2 in the cement production process, with cementitious materials and the incorporation of recycled aggregates.
“Sustainable concrete often replaces a portion of Portland cement with alternative materials like fly ash, slag, or natural pozzolans,” LeMonds says. “These substitutes reduce CO2 emissions and resource consumption.”
Portland-limestone cement is a popular alternative that is blended with a higher limestone content than traditional cement, reducing CO2 emissions by 5 to 10% on average.
The concrete mix of 20 years ago is not the concrete mix of today.
“It’s kind of like baking bread,” says Erin Winston, structural project manager for HKS. “You use the same materials, but with various ratios you get very different results.” Rather than dictate the exact mix it uses on projects, HKS provides performance benchmarks and lets local producers—who often closely guard their proprietary mixes—decide how to achieve them.
Holcim’s OneCem Portland limestone cement, for instance, is manufactured with 10% finely ground high-quality limestone, resulting in a 10% lower embodied carbon. It has been rigorously tested and can be used in virtually any application—from residential construction to large-scale infrastructure.
Much of the embodied carbon in cement comes from the heating process in manufacturing, “because a lot of those kilns don’t use high-quality energy sources; they’re using coal or dirty coke that create the most emissions,” Getz says.
Concrete producers are beginning to take action on this front. By the end of the year Holcim will be sourcing 40% of its energy needs at its 350 US facilities from renewable sources like wind and solar. “The goal is to drive transformative change,” LeMonds says. “You can end up with extremely low carbon concrete if you add low carbon electricity into the mix.”
Taking Green Concrete to the Next Level
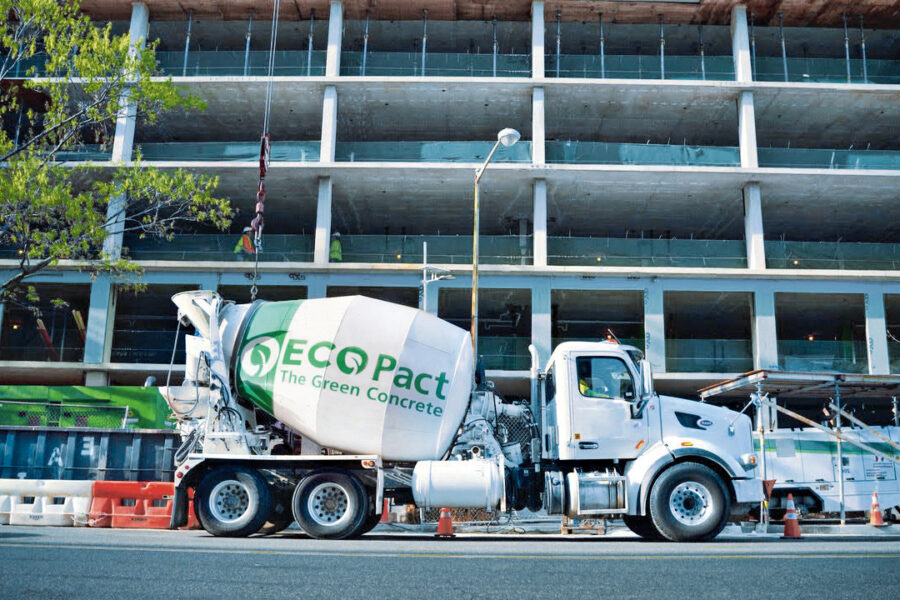
Photo courtesy of Holcim US
There may be an abundance of options for sustainable concrete in the market today, but not all are created equal. One of the industry’s leading solutions is Holcim’s ECOPact low-carbon concrete, which provides a minimum of 30% lower CO2 output—though many applications offer greater reductions, with ECOPact Max capable of obtaining up to a 90% reduction in embodied carbon. “The primary motivation [for developing ECOPact] was the urgent need to reduce our CO2 emissions,” LeMonds says. “We now have the capacity to deliver that change.”
Holcim launched ECOPact in the DC and Boston regions in July 2020 and has since expanded to other major markets like the Minneapolis area, Denver, and Dallas. Developed at the company’s R&D center in Lyon, France, researchers started with small-scale lab experiments to understand the properties and the aggregate mix before applying them to real world conditions.
“While many sustainable concrete solutions aim to reduce carbon footprints, the difference between them lies in the proprietary mix designs, performance attributes, and the extent of carbon reduction,” LeMonds says. “The uniqueness of ECOPact lies in its optimized blend of performance, durability, and sustainability.”
Holcim has demonstrated these attributes with projects like the newly built Georgetown University residence hall at 55 H Street in Washington, DC. The client had a deep commitment to sustainability but also a specified requirement for a 28-day strength design of 5,000 psi while reaching a high-early strength of 3,000 psi within two to three days.
ECOPact Prime met all of those requirements while reducing CO2 emissions by 40% when compared to standard concrete. Holcim can demonstrate these benefits to clients utilizing a number of digital tools that enhance performance by, for example, offering real-time monitoring as the concrete is placed, ensuring consistent quality.
Measuring Performance
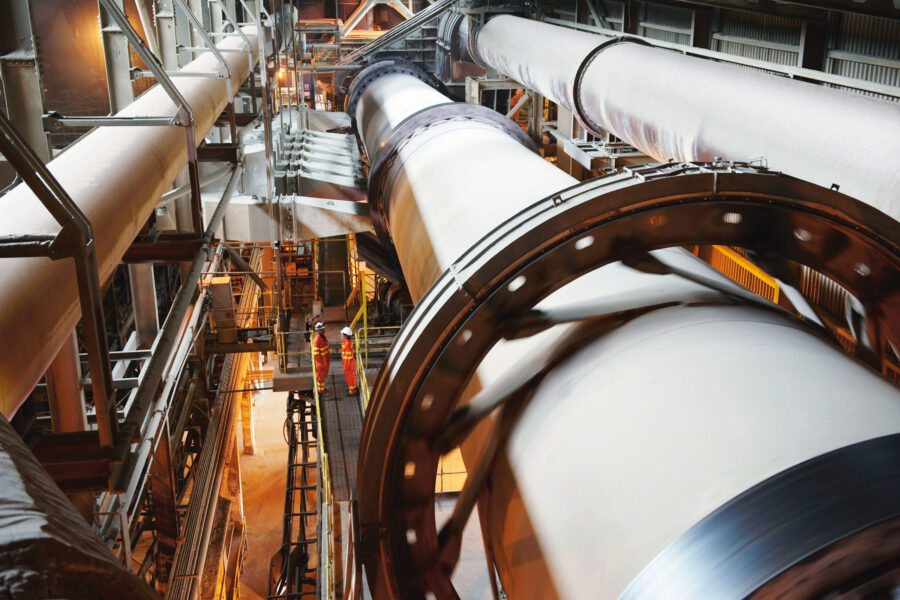
Photo courtesy of Holcim US
Measuring concrete performance, setting standards, and separating the marketing material from the real data remains one of the biggest challenges with improving sustainable practices in the concrete industry. “The big trend in the market is transparency,” LeMonds says. “Transparency is critical to good decision-making. And really, the driver for transparency in concrete is the use of Environmental Product Declarations (EPDs).”
EPDs are a key third-party validation tool that allows industry players—from designers and engineers to developers and manufacturers—to uniformly use data to make credible decisions on what “low carbon” concrete really means.
Though EPDs are currently voluntary, they are becoming increasingly popular as the threats from climate change become increasingly clear. Within the last three years Holcim has begun providing EPDs for all products that the company produces in the US. And design and engineering firms like HKS are beginning to require them on any project that bills itself as sustainable. “There’s really there’s no substitute for that, that uniformly presented document,” Getz says. “It’s great to see the industry coalesce around a standardized methodology.”
Government Initiatives Drive Innovation
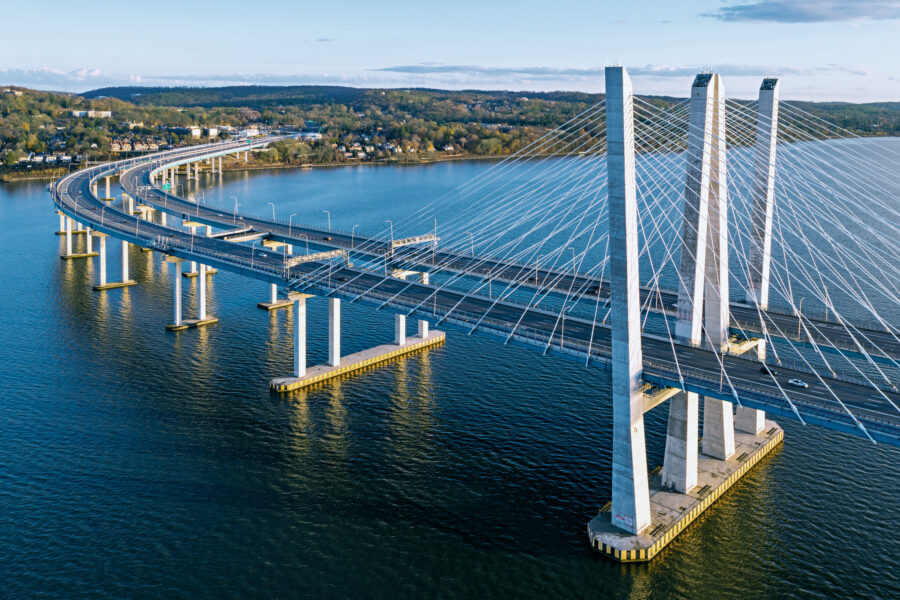
Photo courtesy of Holcim US
Though the industry is pushing itself in the right direction and standardized sustainability tools are becoming commonplace, LeMonds argues “we need radical collaboration in the US to reach net zero.” Public procurement and other government policies play a key role.
The Biden administration’s Buy Clean Initiative, which sets requirements for the purchase of lower carbon construction materials like sustainable concrete, is leveraging the federal government’s enormous procurement power to move the industry in the right direction.
“The federal Buy Clean Initiative is going to drive massive transformative change,” LeMonds says. The federal government’s scale can help set green standards across the construction industry, and its efforts are being complemented by states from California to Maryland.
Furthermore, these sustainability requirements are being set at a time of massive federal investments in infrastructure, manufacturing, and green energy production. Recent legislation, including the Bipartisan Infrastructure Bill and the Inflation Reduction Act, include requirements for the use of sustainable materials like concrete that will be used to build new roads, bridges, factories, and wind turbines.
“As Robin Carnahan at the General Services Administration says, using lower carbon domestic materials is a triple win: it creates good-paying American jobs, tackles climate change, and reduces energy costs,” LeMonds says.