Whether you’re installing a new roof system or remediating on an existing site, the type of coating you choose is critical to your success. Roofs can be remediated using many materials and methods—including silicon, asphalt, acrylic, and polyurethane—but different materials produce vastly different results. It’s important to evaluate roofing choices not just based on up-front costs but the entire life cycle of the roof as well as its environmental impact. Roof lifetime, expected maintenance, disposal, and replacement costs are all important factors.
Speed, cost, and practicality have always been important concerns when specifying a new roof or repair, but today the issue of energy efficiency looms at least as large. In an age of increasingly extreme weather and heat waves, it’s important that whatever coating you use stays cool in the hottest conditions and is durable enough to stand up to hail, high winds, and other tough conditions over time.
Keeping Your Cool
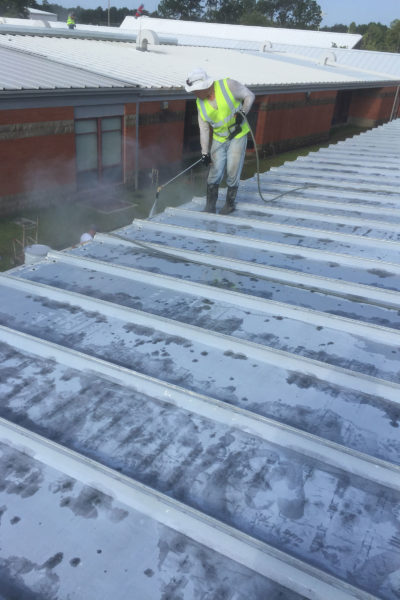
This image demonstrates one method of preparing a metal roof substrate prior to the application of a roof coating system. Photo courtesy of Covestro
Liquid-applied polyurethane reflective roof coatings not only ensure lasting durability and easy maintenance; they also have the all-important quality of reflecting sunlight rather than absorbing it—initially as well as years after application. Dark roofs typically absorb 90% of the sun’s rays, which can drive roof temperatures as high as 150°F on sunny days. Much of this excess heat is absorbed by the building, meaning air conditioning and other cooling systems work harder and consume excess energy. Light-colored roofing on the other hand, has a higher albedo and reflects anywhere from 55% to 90% of sunlight. Former Energy Secretary Steven Chu says deployment of cool materials like liquid-applied polyurethane is “one of the largest and most cost-effective opportunities we have to counter global warming.”
Thermal emittance—the rate at which a given material dissipates heat—is another key factor to consider. Metallic surfaces have much lower heat emittance than nonmetallic surfaces, making them slower to cool down during the evening. We know this intuitively from daily life. An item that’s wrapped in foil—whether that’s a baked potato or a runner after a race—retains heat better than something that is unwrapped. Thus, even if a metallic surface could reflect the same amount of sunlight as white polyurethane, whatever heat that is absorbed is held onto longer.
Heat is not just about energy usage; it’s also a factor in long-term roof durability. The hotter a roof gets, the faster it tends to degrade due to thermal expansion and contraction, and the sooner it will need to be replaced. Roofing material makes up as much as 20% of construction waste and contributes tens of millions of pounds of material to landfills every year. Longer-lasting roofs mean less roofing material that ends up in landfills. Lower roof temperatures also increase the efficiency of roof-mounted HVAC units and reduced knock-on costs (i.e. the less an HVAC system runs, the less maintenance it needs, and the longer it can run before being replaced).
Reflective roof coatings also reduce the urban heat island effect, where densely populated areas see elevated temperatures in the summer due to the lack of vegetation and preponderance of non-reflective surfaces. Urban heat islands contribute to peak energy usage, increasing cities’ pollution and carbon footprint. It’s estimated that increasing urban surface reflectivity could save more than $2 billion dollars a year in energy and air-quality savings in the US alone.
Why Polyurethane?
Polyurethane coatings are extremely durable, providing a unique combination of flexibility and weatherability along with chemical, abrasion, and corrosion resistance, reduced VOC emissions, and edge retention. Well-formulated polyurethane coatings need fewer coats, and their ability to self-prime means they often require less surface preparation, leading to reduced labor costs. Polyurethanes’ fast curing times also make them productivity-friendly and provide a faster finish, limiting damage from rain or environmental contaminants like leaves or insects.
Polyurethane roof coatings come in two broad flavors, if you will—aromatic and aliphatic. Either can be a single or two-component system. Aromatics have moderate-to-high tensile strength and elongation with medium-to-high solids. They are typically used as a base coat (primer), although some formulations can be used for topcoats. Aliphatic coatings are typically used as topcoats since they have similar basic properties while also being light stable, which gives them excellent UV resistance and color retention. These attributes, along with the coatings’ inherent dirt resistance, means they don’t just have excellent initial solar reflectance when applied, but stay reflective long into the future.
Single-component polyurethanes are moisture-cured, meaning they react with atmospheric humidity to form a polyurethane/polyurea coating. Two-component polyurethanes are a mixture of resin and hardener, which react with each other to create faster curing times. This is great for jobs with limited windows or challenging environmental conditions but does require some care in timing and mixing due to their limited pot life. One-component moisture-cured roof coatings are the most common polyurethane-based liquid-applied roofing systems, offering a good price/performance balance and easier application. A range of physical properties such as elongation and hardness can be achieved by varying the resin selection in the formulation.
Moisture-cure aliphatic coatings are relatively new and represent a significant step up in long-term durability, weatherability, and waterproofing. While they cost slightly more than aromatic-based coatings, they offer a higher level of performance and longer service life.
Aliphatic polyurethane roof coverings are a lightweight, versatile, self-flashing solution that provide maximum reflectivity and energy efficiency. Fast and easy to apply, they can work for anything from large-scale industrial applications to small, delicate, high value, preservation-oriented scenarios. Fluid-applied roof coatings can be applied as a new roof system on a new roof deck or in a maintenance situation as a re-roofing system over an existing deck to prolong its life. If properly maintained, a roof tear-off might be delayed indefinitely, keeping roofing material out of landfills for good.
Liquid-applied polyurethane coatings can be installed over virtual any type of surface, from thermoplastic single-ply membranes such as PVC or thermoplastic polyolefin (TPO) to thermoset single-ply membranes such as ethylene propylene diene terpolymer (EPDM) or chlorosulfonated polyethylene (CSPE-Hypalon). They can also be installed over metal, concrete, built-up roof (BUR), modified bitumen (MB), or spray polyurethane foam (SPF).
Case Studies
The next three examples of applications of aliphatic polyurethane each show advantages of this versatile and energy-saving material.
BUILDING LEASE COMPANY, ULYSSES, KS
In 2008 a major hailstorm significantly damaged the 12,000-square-foot metal R-panel roof on Building Lease Company’s rental building. The roof’s metal overlap seams were dented extensively, creating fish mouth protrusions that led to leaks.
Complying with their insurance policy meant either removing and retrofitting the metal or applying a coating to repair the damage. Building Lease Company opted to coat it using Neogard’s Elasta-Gard M aliphatic polyurethane system rather than create more cost and waste with a tear-off.
After a surface prep—including pressure cleaning and applying urethane caulking on all horizontal and vertical seams and every fastener—a base coating with embedded polyester fabric was applied along the roof edges and around penetrations. Then an aromatic polyurethane coating was applied to a thickness of 15 dry mils, followed by a topcoat of light gray aliphatic polyurethane coating to an average thickness of 10 dry mils.
The result was a tough, waterproof polyurethane barrier with an overall minimum thickness of 25 mils. The new seamless roof was completely monolithic, backed by a 10-year warranty, and it’s still holding strong after 12 years and two more major hailstorms. In that time the coating shows no signs of age-related issues of cracking, splitting, or delamination.
FONTAINEBLEAU HIGH SCHOOL, TAMMANY PARISH, LA
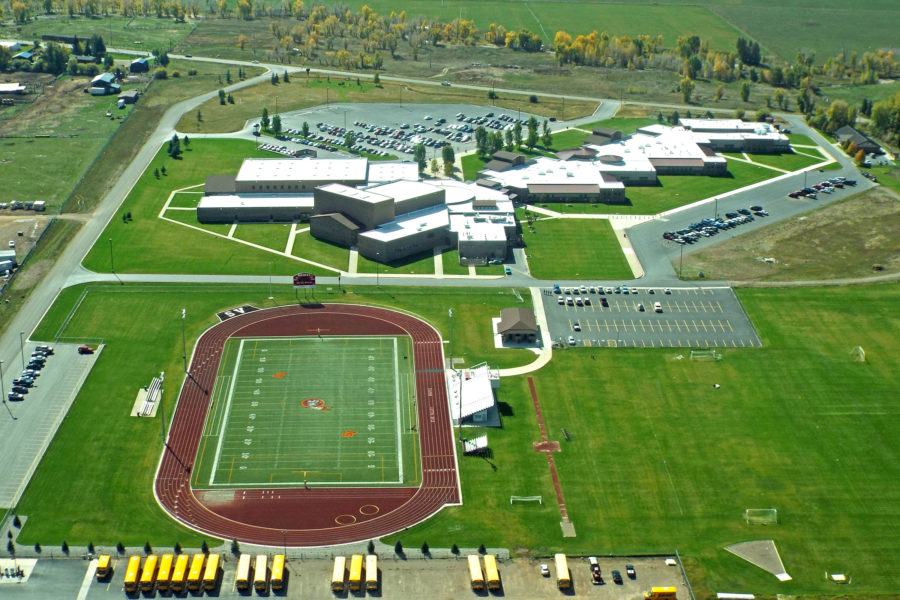
Polyurethanes are one of the most durable coatings on the market today and have found application in the corrosion and construction protection markets because they provide a unique combination of flexibility, weatherability, chemical, abrasion, and corrosion resistance. Photo courtesy of Covestro
For its first 20 years of operation, Fontainebleau High School used acrylic roof coatings to protect, preserve, and extend the life of its factory-coated metal roofs. In 2014 Tammany Parish School District asked architects from KVS Architecture and Sizeler Thompson Brown Architects to look into different options.
Knowing they were facing significant constraints on the project—a limited 60-day window for a 115,000-square-foot job, frequent afternoon thunderstorms, and dew in the mornings—the team reached out to NeoGard, a leader in urethane roof coating technologies. NeoGard recommended a high-performance aliphatic polyurethane coating. The single-component solution was easy to apply, an important consideration for the design team given the project’s demanding time constraints and moisture concerns.
Brazos Urethane used a biodegradable cleaner to prepare the metal substrate; seams were detailed with polyurethane and TieTex fabric and all fastener heads were detailed with polyurethane sealant. Primer was then applied, followed by a base coat of Elasta-Gard 70630 urethane. A reflective topcoat of Elasta-gard 7490 aliphatic urethane completed the system and adhesion tests were performed throughout the jobsite to confirm integrity of the coating application.
In the end, not only were the significant budget, time, and environmental concerns all met, the topcoat’s greater tensile strength proved more durable and weather resistant than previous coatings.
CHARLESTON LIBRARY SOCIETY, CHARLESTON, SC
The third oldest private library in the country, The Charleston Library Society was founded in 1748 as a community book collection. Its archives include rare books, maps, manuscripts, and letters from such luminaries as Alexander Hamilton, John Paul Jones, and George Washington. It survived a revolution, a civil war, fires, and earthquakes, but in 2018 it was nearly undone by the weather.
The building where the library is housed was constructed in 1914 thanks to a grant from Andrew Carnegie. In 2018, after hurricanes exposed a major leak that put the library’s collection at risk, it was clear something had to be done quickly to remediate the situation.
The main roof at the front of the building includes a parapet surrounding a slate hip-roof with a skylight along the ridge. The parapets required rehabilitation and waterproofing protection, especially at the roof transition. The copings were terra-cotta covered with a piecemeal conglomerate of aged coatings and reinforced membranes. A built-in gutter that extends from the face of the parapets to the eaves of the hip roof was also a concern. It contained layers of copper flashings and liquid-applied coatings installed over many decades. Another pressing issue for the design team was a low-slope roof at the back of the library covered with an acrylic single-ply membrane on top of many decades worth of archaic built-up roofing (BUR), with water trapped in the built-up layers.
After looking at various options, the engineers and architects settled on a cold-applied reinforced aliphatic polyurethane resin, a liquid-applied membrane from Kemper System. “It became a no-brainer because we wanted every area to have seamless monolithic protection,” says structural engineer Jason Gregorie. “We needed a versatile solution to address the varied substrates and surface profiles, the many contours, and the intersecting planes. The roof also had tight working spaces and difficult details. We knew the Kemper System could work well. It fully adheres, and the contractor could easily apply it to the different elements and transitions to achieve monolithic protection.”
The project also had to satisfy Charleston’s stringent landmarking requirements. “Since the library is architecturally significant in Charleston, we weren’t allowed to make any aesthetic changes that could be visible from the street,” Gregorie explains. Thankfully, unlike sheet products that use termination bars, the Kemperol membrane was able to self-terminate at the top outer edge of the parapet copings.
The final challenge to finishing the project was the threat of hurricanes. Hurricane Irma flooded Charleston that year and Maria came close. On a day with no rain in the forecast, the construction crew applied the Kemperol Reflect 2K FR aliphatic polyurethane system, which has an open time of about 30 minutes. The reinforced membrane system, applied a section at a time, dries to a monolithic surface that is water-resistant after about two hours. And Charleston’s history stayed safe and dry.