Story at a glance:
- APV ensures your engineered coating job is done right through proper building preparation.
- Depending on what coating suits a particular structure, APV offers three complementary primer systems.
- NeverFade’s resin system, Kynar Aquatec, outlasts high-performance 100% acrylic products.
The process of applying a protective coating to a building’s exterior is more complicated than it might seem—if it’s done right. Simply pressure-washing the facade and then painting it isn’t nearly enough. Experts say pre-coating preparation is the key to achieving high-quality, long-lasting results.
“Every job is unique,” says Erin Brown-Neff, the director of marketing and business development for APV Engineered Coatings. “Depending on where the location is—whether it’s Florida, California, the Midwest, the Caribbean, or Canada—the climate conditions can vary considerably. The surface condition of the building can also vary—all those things can impact how a coating will perform. There’s really no ‘one size fits all’ coating system.”
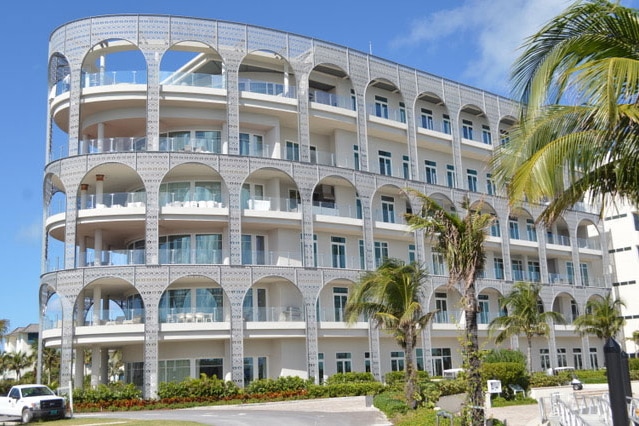
This condo property in the Bahamas keeps its exterior looking bright with W-1650 Bonding Primer and a custom Silver Birch Mica color of NeverFade Metal Topcoat. Photo by Stuart Dean Company
That’s why APV, working in concert with carefully chosen certified contractors like Stuart Dean Company, is so strict about surface preparation. “According to NACE International, 75% of all premature coating failures are caused by improper surface preparation,” Brown-Neff says.
1. Careful pre-inspection makes a big difference.
Those failures are often caused by improper initial assessments. Perhaps more crucially, contractors fail to involve the coating manufacturer from the outset. Whether a structure is old or new, in need of repairs for problems like blistering, peeling, or pinholing, or receiving its first coating, APV is always involved. “Together with our certified contractor, we act as inspectors on the job,” Brown-Neff says. “We go to the job site, see the unique situation on the project, and use NACE, SSPC, or ASTM Standards to specify how the surface should be prepped.”
Rex Dean, global director of facade restoration at Stuart Dean, says they first determine the type of substrate that needs coating and the existing coating system—if there is one. They then test the surface for adhesion to see if a new field-applied coating system will anchor to the current coating.
When that’s done, surfaces are tested for environmental contaminants like chlorides, sulfates, and nitrates—which are removed if they’re present. Next up: the creation of an “anchor/surface profile.” That can be achieved by hand abrasion, mechanical tool abrasion, and blast abrasion.
2. Consider environmental factors.
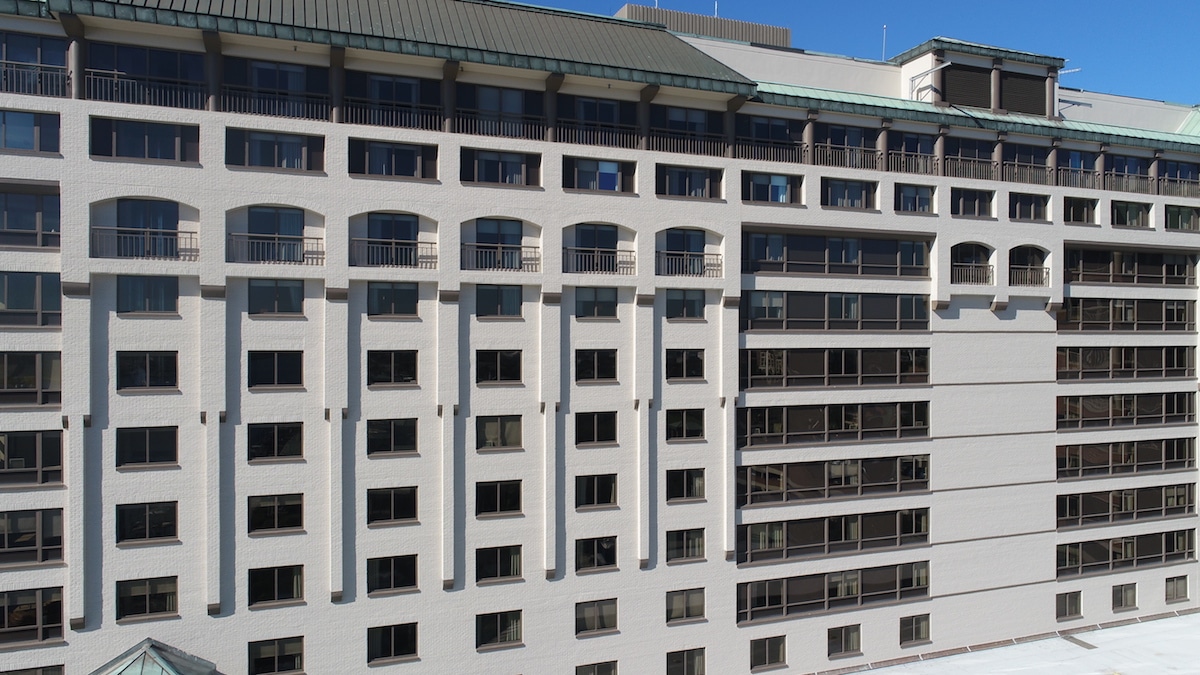
A detailed assessment of the surface in question, as well as the environment in which it exists, is crucial to the success of every project. Photo courtesy of APV Engineered Coatings
Prior to applying APV’s NeverFade, Dean says it’s also critical to conduct environmental monitoring that measures and records climate conditions like relative humidity, air temperature, surface temperature, dew point temperature, and the difference between surface and dew point temperatures. Those conditions dictate whether a NeverFade coating can be applied.
“Coatings applied in poor conditions can risk the performance of the coating installation,” Dean says. “Dry film thickness (DFT) or coating thickness is arguably the single most important measurement made during the application and inspection of protective coatings,” which are “designed to perform their intended function when applied within a tight DFT range as specified by the manufacturer.”
3. Make sure the primer complements the coating.
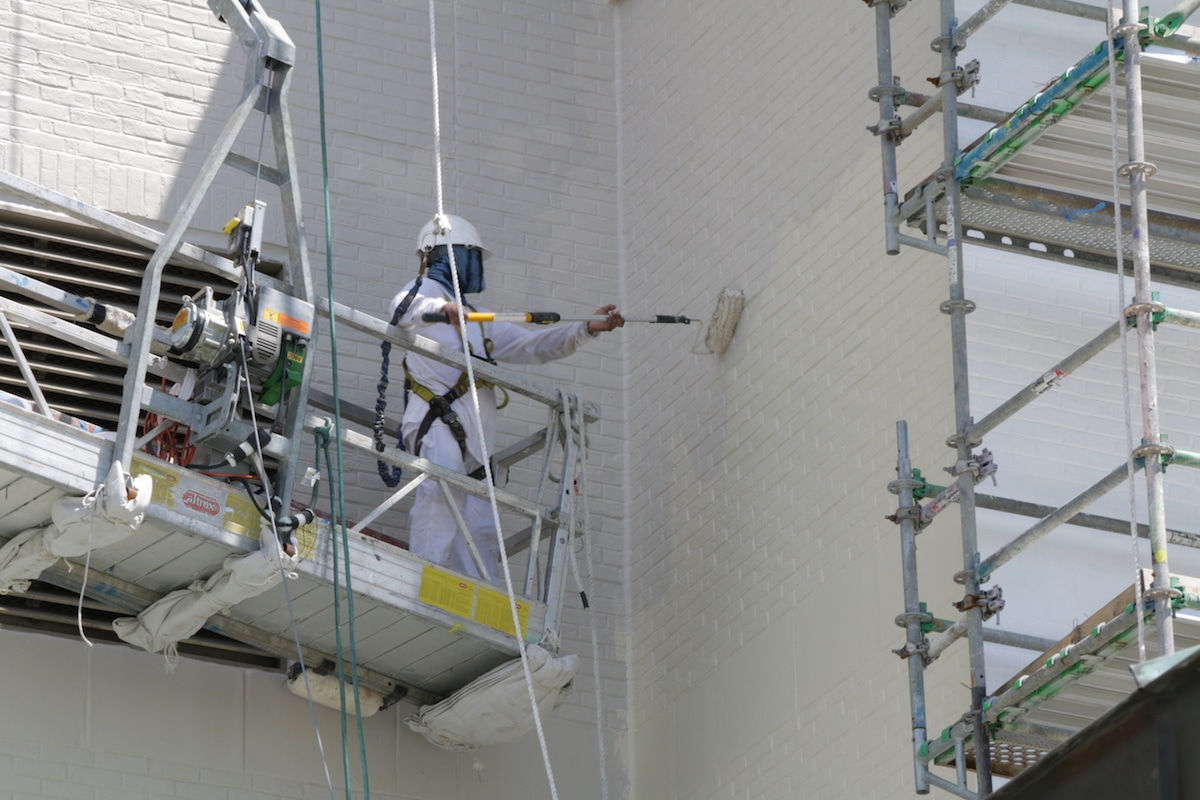
APV Engineered Coatings is involved in assessments every step of the way to ensure the process runs smoothly. Photo courtesy of APV Engineered Coatings
Depending on what coating suits a particular structure, APV offers three complementary primer systems—a universal primer (W1500), a bonding primer intended for coated surfaces such as factory coatings and Kynar (W1650), and a top-shelf two-component epoxy for use in areas—like the Gulf Coast of Florida—that experience high corrosion.
APV’s NeverFade coatings come in two main topcoat formulations that incorporate Kynar, the PVDF polymer engineered by Arkema. NeverFade Original is for wood, masonry, stucco, fiber cement, and concrete. The other, NeverFade Metal Restoration, is used on all types of ferrous and non-ferrous metals. Both are dispersed in water, which keeps VOCs low and air quality high.
4. Look for this when the job is done.
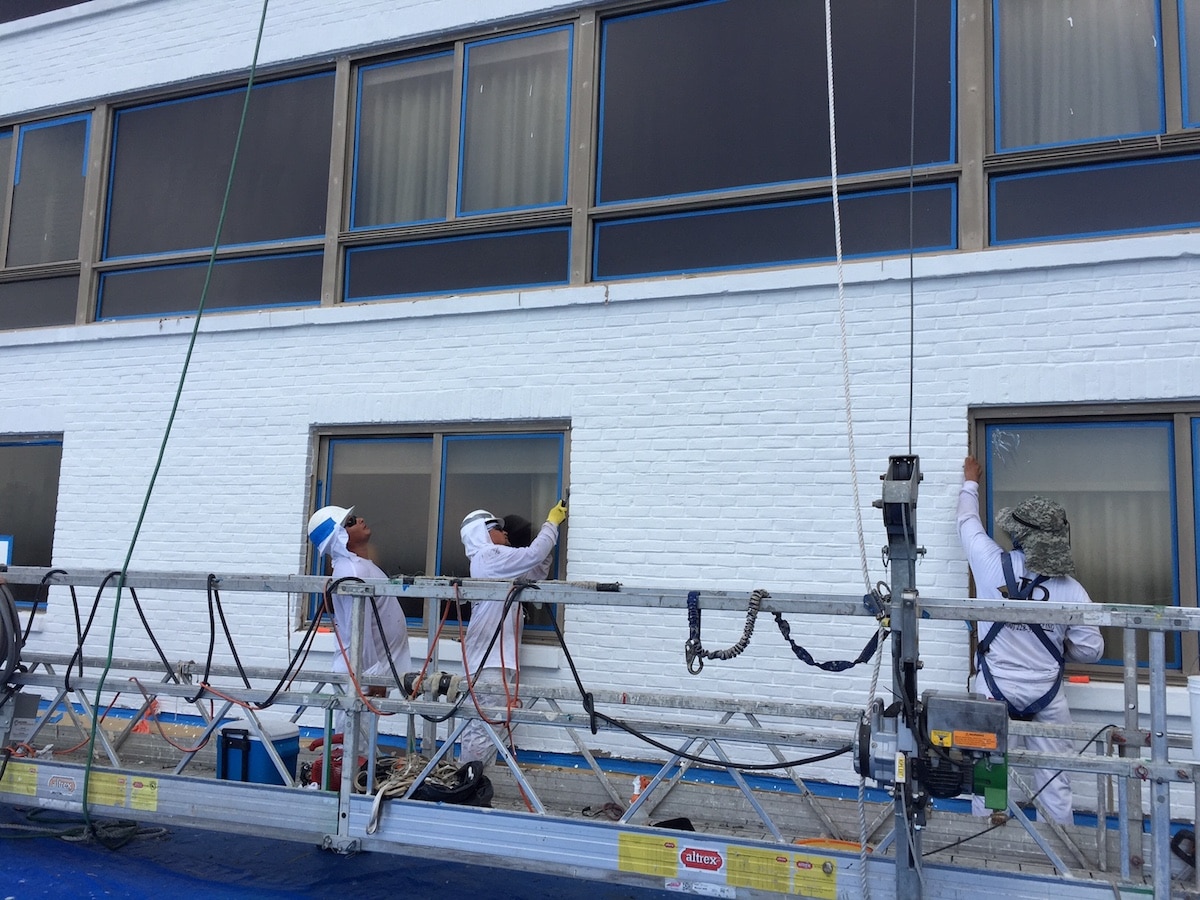
Photo courtesy of APV Engineered Coatings
“When you apply the coating system, you may see some initial variance in the finish, such as roller or brush markings,” Brown-Neff says. “But the coating actually levels out over a couple of hours, and you’ll notice those markings will fill out as the product cures. This self leveling effect allows NeverFade to be brushed and rolled onto surfaces without sacrificing aesthetics.
Ultimately, if you’ve done a thorough pre-job assessment and selected a knowledgeable contractor that works directly with the coating manufacturer, issues should be minimal-to-nonexistent. “The greatest feature of NeverFade is its resin system, Kynar Aquatec. It outlasts high-performance 100% acrylic products and even two-component urethanes,” Brown-Neff says. “When a customer is incorporating NeverFade into the spec, they’re sourcing a product that is going to increase the life cycle of the facade, so we want to make sure they’re getting what they’ve asked for.”