Story at a glance:
- Lester Building Systems’ offer engineered wood frames for flexible, sustainable, and durable design.
- Post-frame buildings go up approximately 30% faster and are less expensive than traditional construction methods.
- The uses for Lester Building’s systems includes commercial, residential, and even light industrial buildings.
Engineered wood frame buildings have been around for decades, yet their popularity continues to gain momentum within the industry as builders and customers alike take note of their many benefits. The post-frame construction method provides an elevated level of flexibility, durability, and energy efficiency, making it ideal for customers looking for a customized solution, whether it be for personal or commercial use. “Every building starts with a dream in the customer’s mind,” says Paul Boor, vice president of product development at Lester Building Systems, a leading manufacturer of engineered wood frame systems. “We’re able to take that dream and turn it into reality.”
Unlike traditional construction methods, post-frame construction puts the customer in charge. Lester Buildings is able to take specific inputs from a client—including local snow and wind load conditions, colors, materials, and geometric constraints—and create a drawing with cost estimates included. “They are able to get granular data and a visualization of their dream on their first visit,” Boor says. Many of Lester Buildings’ dealers act as general contractors while others can often recommend subcontractors as needed.
The Minnesota-based company manufactures its engineered systems at three US plants, selling both factory-direct and through a network of independent dealers across 35 states. Lester Buildings was founded in 1947 and began making wood-frame buildings in 1954 under the direction of Art Schwichtenberg. The company has since grown into one of the top three manufacturers of engineered wood frame buildings in the country. “People refer to our buildings as pre-engineered, but we don’t pre-engineer anything,” Boor says. “We like to say it’s engineered on the fly. It’s a truly custom solution.”
Post-Frame Goes Up Fast
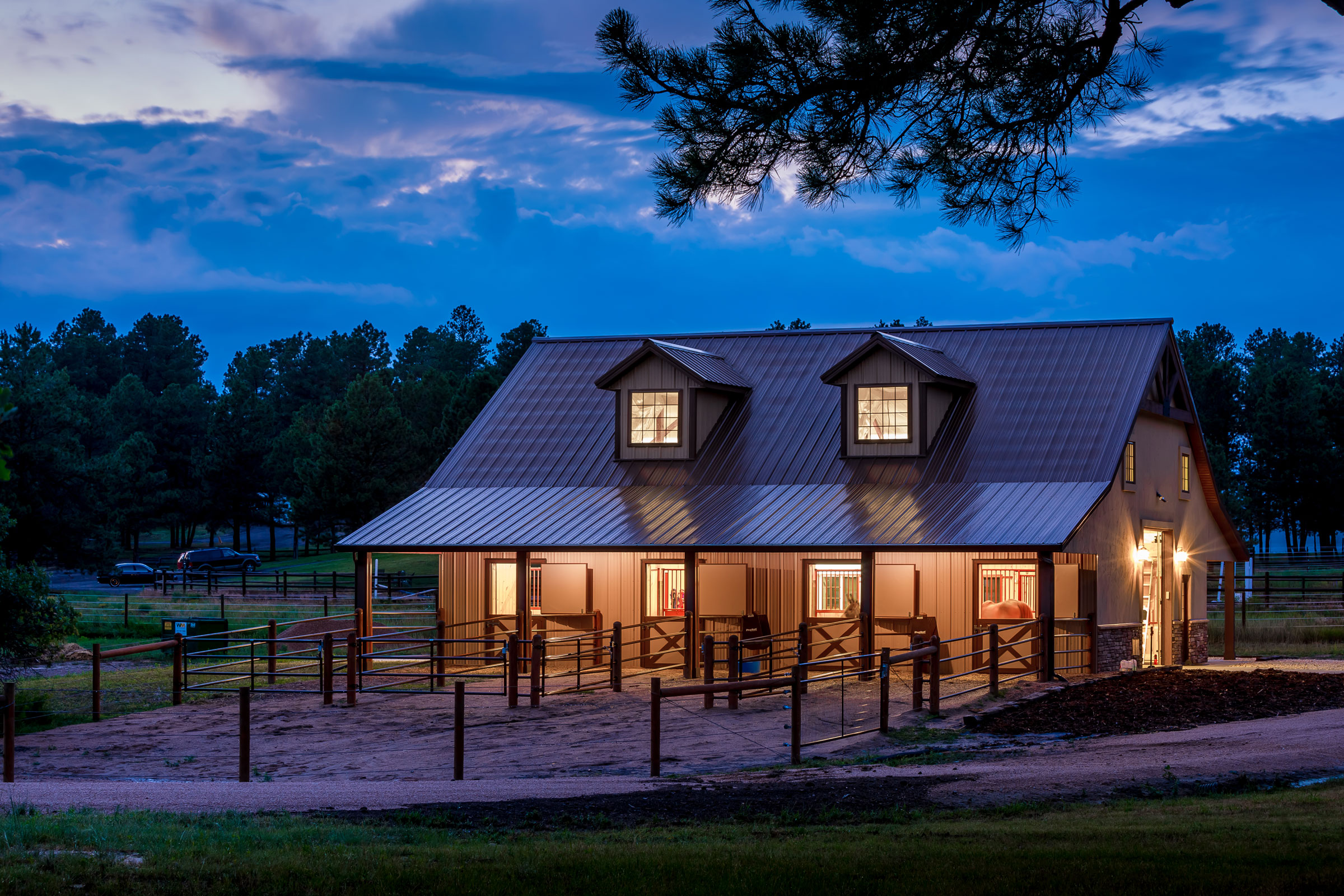
Post-frame buildings go up approximately 30% faster and are less expensive than traditional construction methods, according to the experts at Lester Buildings. Courtesy of Lester Buildings
Boor says engineered wood-frame systems are one of the fastest growing construction methods in the industry today. So what are the main benefits of a post-frame structure, and when should customers consider this option? “Any project of considerable size or complexity, and anything that’s not directly covered by a prescriptive code like the Residential Building Code, is a great candidate for engineered post-frame construction,” Boor says.
That includes commercial, residential, and even light industrial uses. There are a couple of reasons for this. For starters, Lester Buildings guarantees the structural integrity and durability of its engineered systems—something the local contractor building onsite cannot. Post-frame buildings also go up approximately 30% faster and are less expensive than traditional construction methods. Owners who want a quicker return on investment cite this as a key benefit.
Designs are Flexible
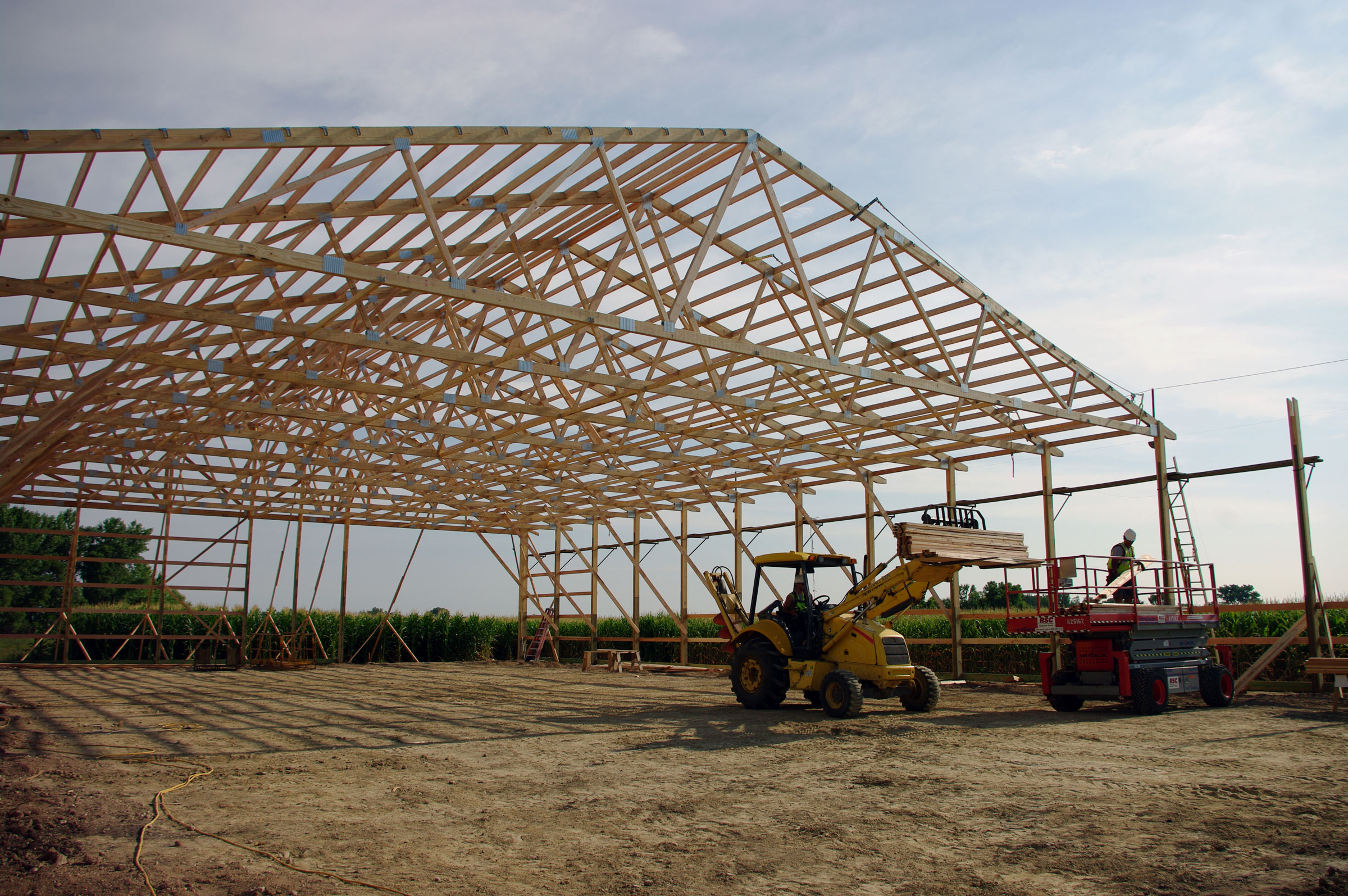
Using a double-press system, Lester BUILDINGS manufactures their trusses per order. The truss saw is programmed to cut the boards to the exact length needed to ensure accuracy and reduce construction time. Courtesy of Lester Buildings
Due to their durability and versatility, post-frame buildings can be adopted for just about anything. “Our customers are extremely varied,” Boor says. Agricultural uses like farm buildings, equine stables, and livestock barns are in high demand given that post-frame systems provide open floor plans and taller ceilings. Hobby buildings like garages and workshops are also a sizable portion of their business.
With the increased popularity of engineered post-frame buildings, Lester Buildings has worked with clients on everything from wedding venues and wineries to places of worship. “And because they can be heated and fitted with electricity and running water, they can be used for housing and retail as well,” Boor says. In fact, one of Lester Buildings’ fastest growing segment is post-frame homes.
These are Built to Last
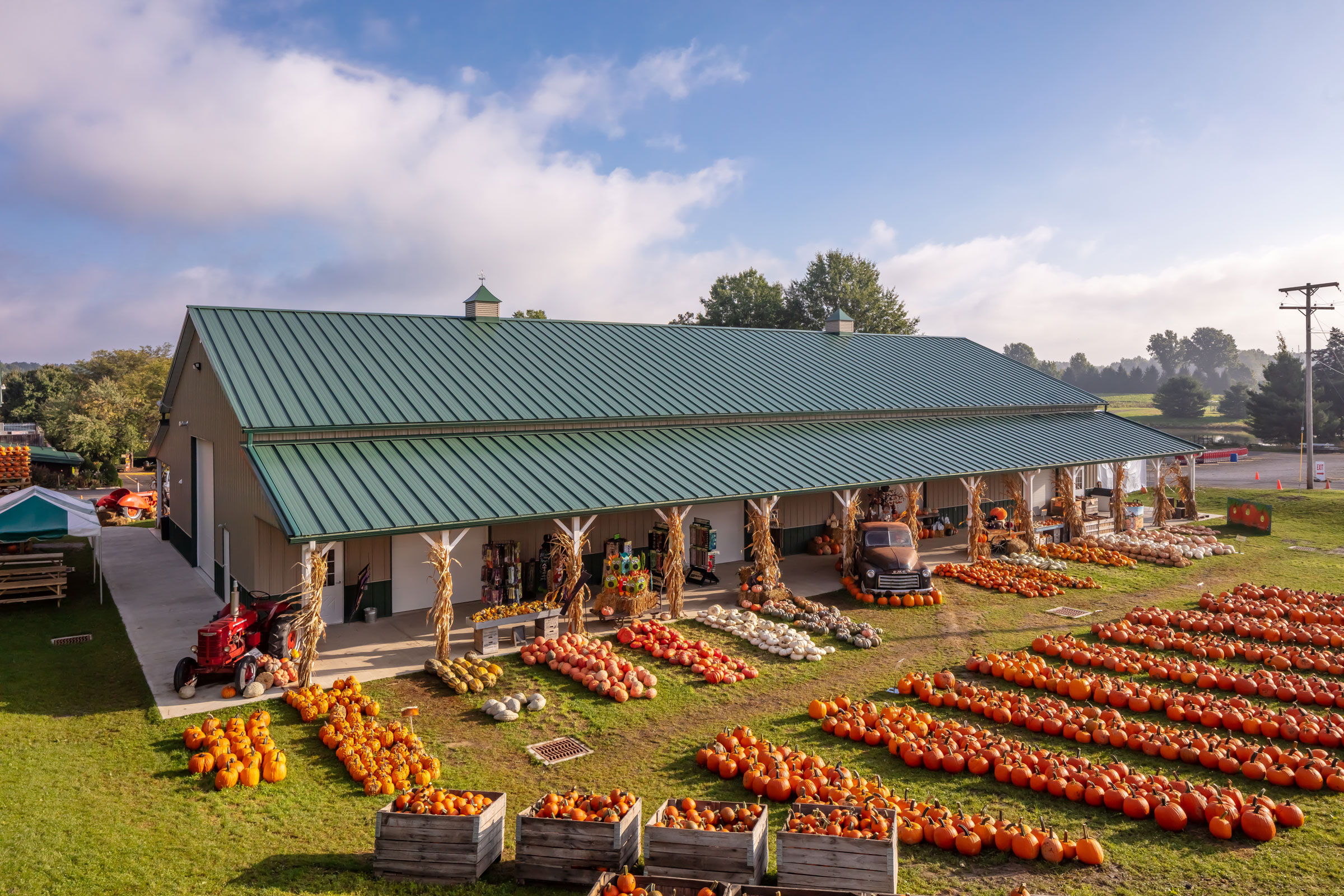
The White House Fruit Farm in Ohio turned to Lester Buildings when they needed a bigger building for their successful business. Courtesy of Lester Buildings
Concerned about the durability of engineered wood frame systems? “Durability is one of the strongest selling points” for post-frame buildings, Boor says. “The problem with non-engineered buildings is there’s probably a weak spot no one thought of. And you won’t find out until it’s too late.”
Engineered trusses and precision-made connection points are key to the durability of Lester Buildings’ systems. The company performs all structural design in-house, where its engineers take inputs like average snow and wind in a given location to determine design loads for a specific project. Once those loads are known, a design to safely absorb those forces is created. And it backs all of that up with a lifetime structural warranty on its buildings. Boor adds that, after this summer’s derecho storm that ravaged parts of Iowa and Illinois, one of the company’s dealers called to say that many buildings were lost or damaged in the area, while Lester buildings were still standing.
Post-Frame is Green
Wood is by far the most sustainable building material, as it is fully renewable and has the lowest embodied energy compared to steel or concrete—which require far more energy to produce and transport. “Timber is also what we call a ‘carbon sink,’ because it captures carbon from the air and sequesters it,” Boor says. “I want to ask Jeff Bezos, ‘Why aren’t you building your [Amazon] warehouses out of wood? You could sequester so much carbon.’”
And because Lester Buildings customizes its projects and performs all of the framing and sizing at its factories, far less material is wasted than a traditional structure built onsite. Boor sees net zero energy building codes as a particular area of opportunity for the company in the future. “Regulations on energy efficiency will continue to increase and post-frame buildings will be well positioned to meet those demands,” he says.
Get the Look You Want
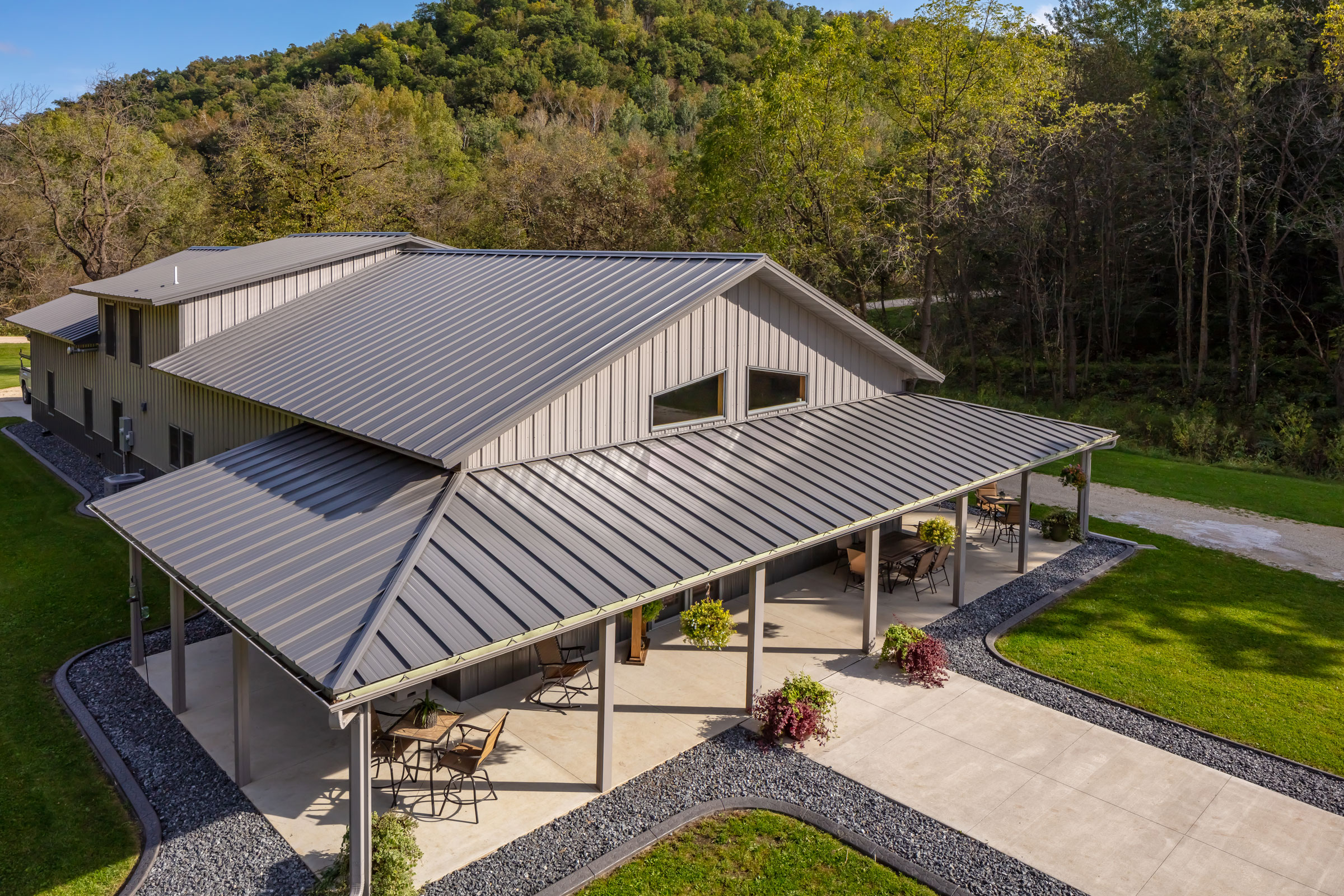
Any interior or exterior design element that is found in a traditional home can be included in a Lester Buildings pole barn home. Courtesy of Lester Buildings
There’s a common misconception that while post-frame buildings are durable and cost-effective, this comes at the expense of aesthetic design. Yet this couldn’t be further from the truth. “Since we customize everything, we can design almost anything you’d like,” Boor says. That includes custom entryways, dormers, porches, and other accessories. Lester is very proud to have designed and built many truly beautiful buildings.
Lester Buildings’ newly patented Eclipse Roof System® is a great alternative to a standing seam roof. With unmatched curb appeal, The Eclipse Roof System combines the structural integrity of a through-fastened roof with the weathertight, sleek appearance of a standing seam metal roof at a lower cost. An attractive roof batten snaps over the ribs, concealing the panel fasteners and creating bold clean lines.
“These are not cookie-cutter buildings,” Boor says. “We have nothing premade in our yard. We’re always encouraging customers to have it their way.”