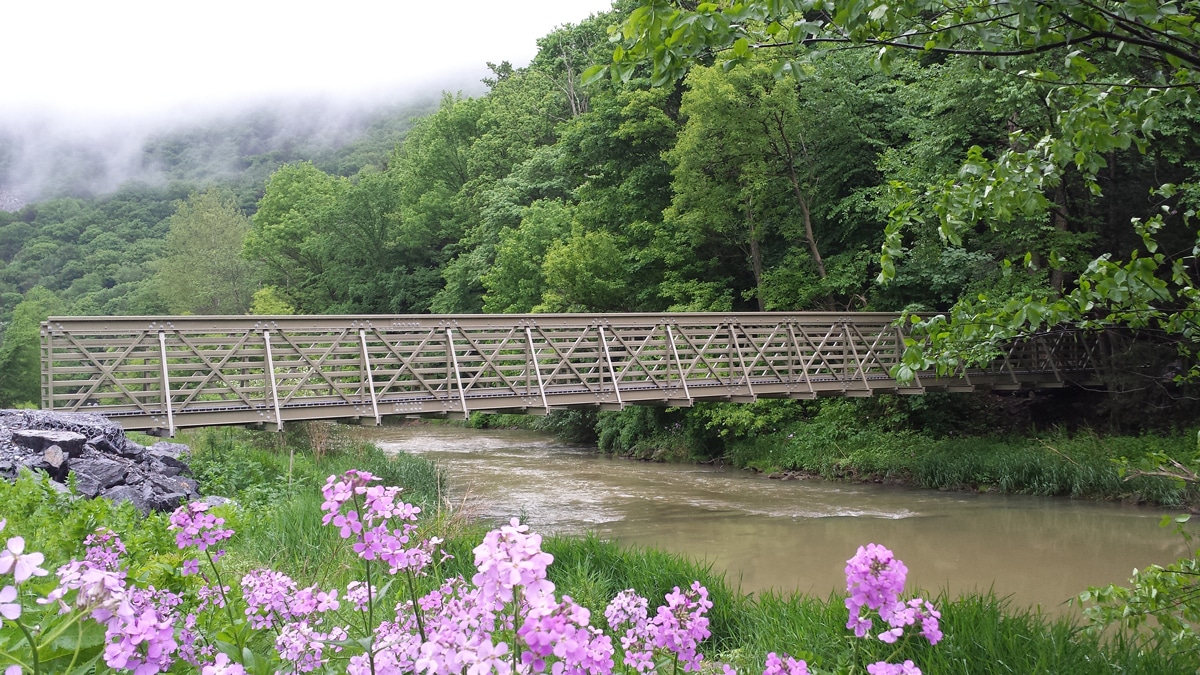
E.T. Techtonics’ bridges have classic lines and blend in seamlessly with their natural surroundings. [Photo: Courtesy of E.T Techtonics]
E.T. Techtonics is a leader in sustainable bridges to meet any need.
It’s likely, while wandering through one of your local state parks or a vast city green space, that you’ve passed through woodlands, above ravines, or over tumbling rivers with both ease and little thought for the structures that allow your aimless wandering. Paths meander smoothly onto bridges and boardwalks that allow you to traverse obstacles without feeling at all obstructed.
Creative Pultrusions has designed and manufactured custom bridges and walkways such as these for a combined 30 years under the product line—and former manufacturing name—of E.T. Techtonics. The company’s fiberglass bicycle, equestrian, light vehicle, and pedestrian bridges offer environmentally sensitive and aesthetic solutions for demanding requirements in any environment.
Founded in 1987, E.T. Techtonics sat at the forefront of design and construction for fiber-reinforced polymer bridge systems, partnering extensively with Creative Pultrusions for manufacturing needs. In 2016, Creative Pultrusions acquired the company and retained its name for its premier line of bridges and walking structures. Since the line’s founding, more than 1,000 E.T. Techtonics fiberglass pedestrian bridges and walkway systems have been installed throughout North America’s most popular recreation destinations.
FROM OUR JAN+FEB 2019 ISSUE
The preferred publication of leading green professionals.
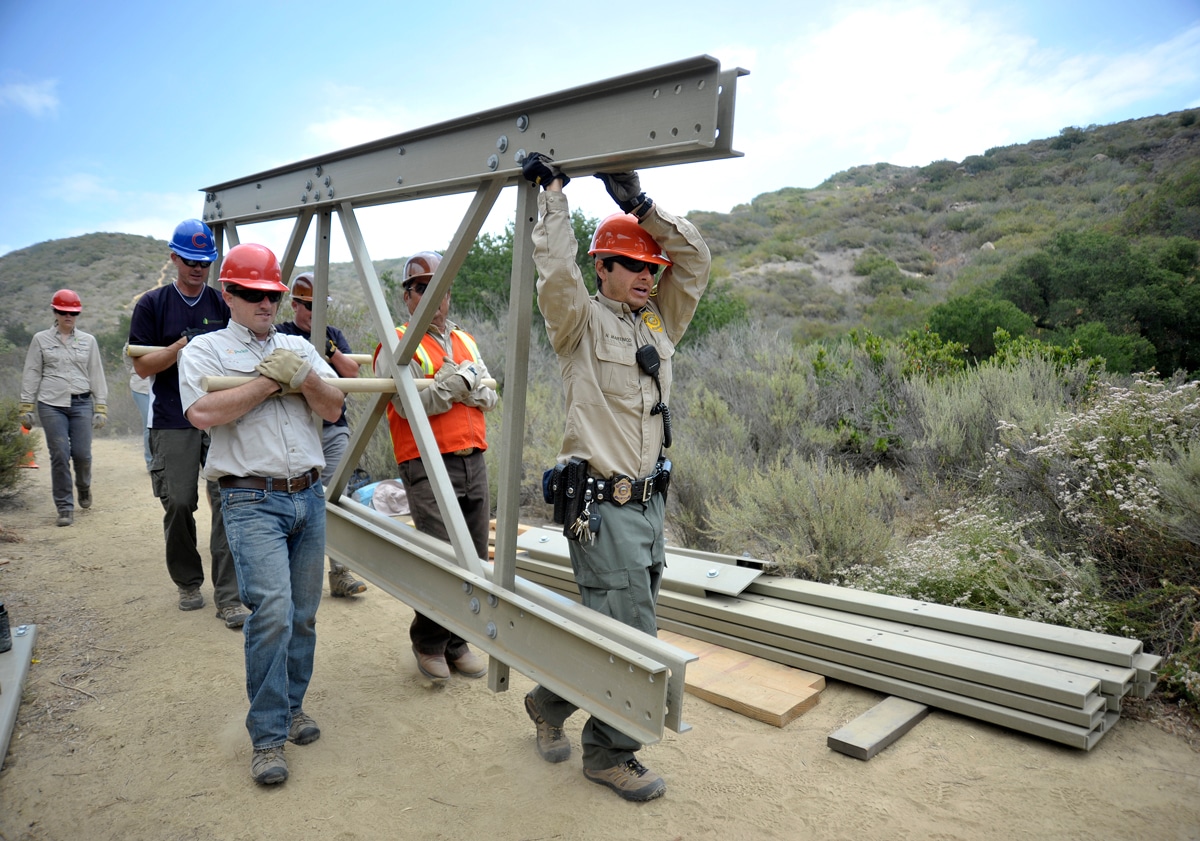
E.T. Techtonics’ bridges are lightweight and easy to install, as they’re custom-designed and prefabricated before they’re shipped. [Photo: Courtesy of E.T Techtonics]
Material
The bridge and walkways are constructed using fiberglass reinforced polymers. Resin and glass fiber reinforcements are combined through a heat-curing process and pulled through a die. Shapes and forms depend on the needs of a project.
The fiber reinforced polymer (FRP) composite offers a high tensile strength ranging between 30,000 psi and 100,000 psi, and yet it’s 80% lighter than steel, enabling easy installation in the most difficult of locations. FRP excels in harsh environments—water, saltwater, termite- and pest-prone—that can quickly degrade more traditional building materials.
Aesthetics
Strength and durability are one thing, but a major selling point for fiberglass bridges is their ability to meld seamlessly with their environments. E.T. Techtonics bridges are known for clean, classic lines that meld easily with natural surroundings. “We can color our resin, giving us options like olive greens and browns that match very well in the environments of a trail or a forest,” says Ted Harris, manager of the E.T. product line. His product lends itself easily to natural colors, but it can also provide a bit of flair if wanted to a local park or city installation with bright colors.
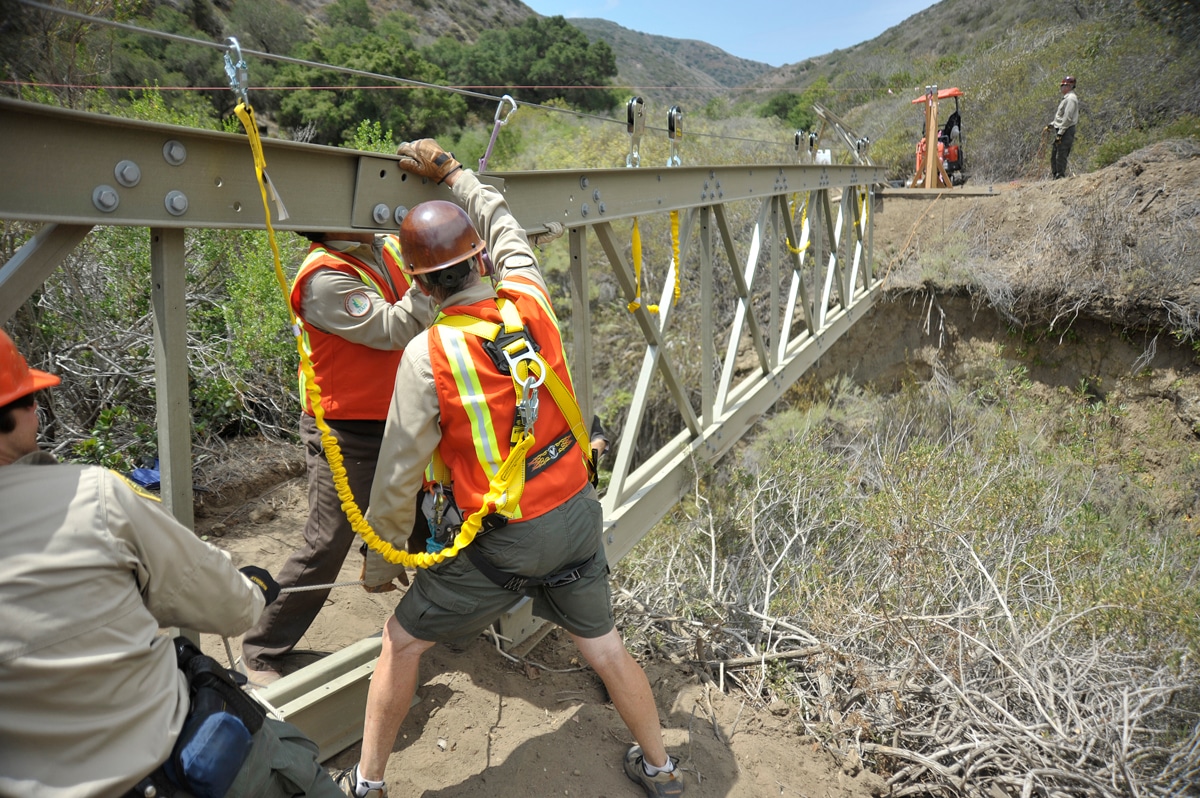
[Photo: Courtesy of E.T Techtonics]
Lightweight
High strength fiberglass polymer is light enough to transport easily and quickly into difficult-to-reach locations. “The heaviest component of our bridges is approximately 90 pounds, making it easily carried by just one or two individuals,” says Dustin Troutman, director of marketing and product development for Creative Pultrusions. “No matter where the bridge is located, our engineering team can custom design the structure based on the client’s installation capabilities.”
His team has developed bridges for trails that require install teams to hike single file across rugged terrain and for remote locations requiring helicopter access. Install is as easy as delivery. “My first impression of these bridges was they’re light and they’re in pieces we can carry in by hand or with small equipment,” says Cam Lockwood, who has spent more than 40 years managing and installing trails for the nation’s public lands.
Easy Setup
E.T. Techtonics bridges are custom-designed and prefabricated before they’re shipped, making setup in difficult locations as easy as access to those locations. “The quality control is outstanding,” Lockwood says. Of all the 30-plus E.T. Techtonics bridges he has installed, only one bridge needed a replacement piece during install. “That was the only bridge we asked them not to preassemble,” he says. “If we had pre-assembly, it wouldn’t have been a problem.”
Lockwood is currently building two of E.T. Techtonics bridges, a 35-footer and a 50-footer, as a private contractor on national forest land. “They’ve been innovative,” he says of E.T. Techtonics engineers. “We’ve come up with several different abutment designs that people just hadn’t thought about, and they were very helpful in doing the engineering design work.”
Long Life
Once installed, the bridges are there to stay. The resin, engineered just so, lasts decades where other building materials are hampered by chemical leaching and erosion. “It’s an ideal material,” Troutman says. “It will stand the test of time.”
Lockwood installed his first fiberglass bridge in Tahoe National Forest in the 1980s, and since then he’s installed bridges across the U.S., from Alaska to Texas. “These bridges will be around longer than me. They’ve needed some cleaning and servicing, but none have deteriorated.” His oldest has been carrying trail-goers for nearly 40 years and counting.
Why This Matters
The development of fiberglass bridges speaks to a major turning point in national park and trail system development. In the earlier days of Cam Lockwood’s bridge building, he and his teams were hauling logs up trails to build access points. “That takes a huge amount of energy. As we got more stringent with engineering requirements, we had to have more verifiable pieces of timber or steel, which requires cranes,” he says.
In places with trail systems that couldn’t accommodate the equipment to haul in building materials, Lockwood and his teams had to build access roads, significantly increasing the footprint of the trail system buildout and, in some ways, marring the reason many come to enjoy these trails: remote wilderness. “E.T. Techtonics bridges meet all of the strength requirements for pounds per square foot, but two of us can haul a bridge piece by piece,” Lockwood says.