Story at a glance:
- The building industry’s shift toward sustainability is driving demand for precast concrete given its advantages of cost, resiliency, aesthetic flexibility, and durability across a structure’s life cycle.
- While building industries are responsible for up to 50% of greenhouse gas emissions, precast concrete can reduce embodied carbon by up to 40% compared to traditional methods.
- Corgan’s BRIT was an early example of highly energy efficient buildings, demonstrating precast concrete’s role in minimizing environmental impact, alongside innovative structural solutions.
Globally the architecture and construction industries are responsible for approximately 50% of greenhouse gas emissions and nearly 45% of global resource consumption. While much progress is yet to be made, practitioners are increasingly recognizing the built environment’s potential as a key driver for change in the push toward greener practices.
Historically efforts of the building sectors have largely targeted reducing operational carbon emissions. In recent years methods have shifted to a more holistic approach that begins planning with considerations of embodied carbon across a building’s entire life cycle.
As industries grapple with evolving demands for sustainability and efficiency, precast concrete has proven to be a viable solution addressing several challenges—from logistics and performance to aesthetics and reusability—while accounting for many innovative construction solutions. While precast concrete has its benefits throughout the life cycle of a building, it is during the use stage when these systems truly shine. By prioritizing sustainability from a life cycle perspective in the design phase rather than focusing on first cost, architects, builders, and owners can make a positive impact on the environment and contribute to a more sustainable built environment.
Greener Practices
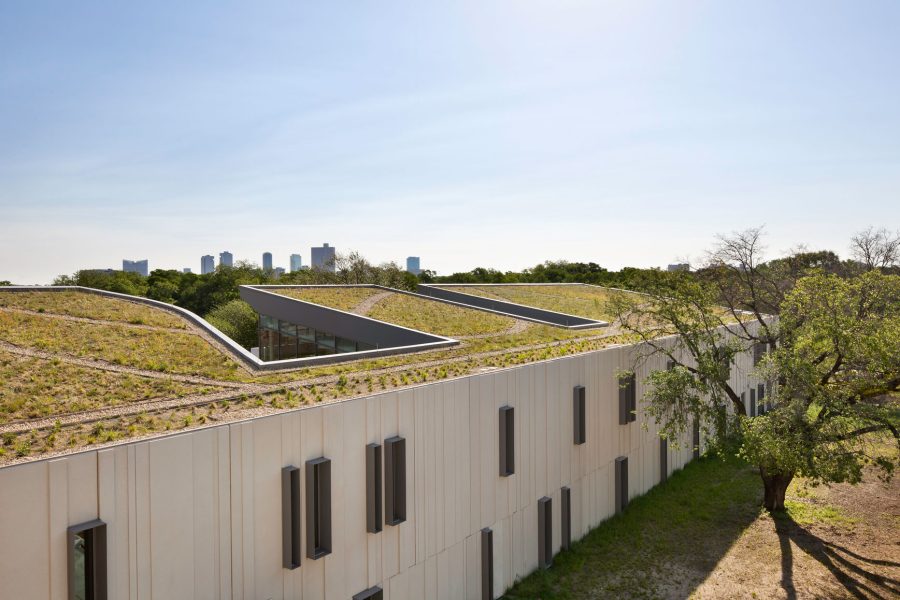
Corgan’s Botanical Research Institute of Texas (BRIT) integrates various innovative sustainability measures. Photo courtesy of Corgan
The understanding of sustainability gained new focus in the building industry in the early 2000s, in part accelerated by the expansion of the USGBC’s environmental initiatives and regulations. Around this time global architecture firm Corgan began questioning how buildings could be designed in a way that they are no longer a detriment to the environment, but rather active contributors to restoring ecological balance.
Corgan’s Botanical Research Institute of Texas (BRIT) integrates various innovative (and unconventional for their time) sustainability measures—including the implementation of both structural and aesthetic concrete components. The decision was initially driven by cost restrictions and the need for construction efficiency in developing the LEED Platinum facility. “The concrete becomes both your envelope and your structure, meaning you don’t have duplicative columns or foundations,” says Matt McDonald, commercial sector leader and principal at Corgan.
Design Flexibility
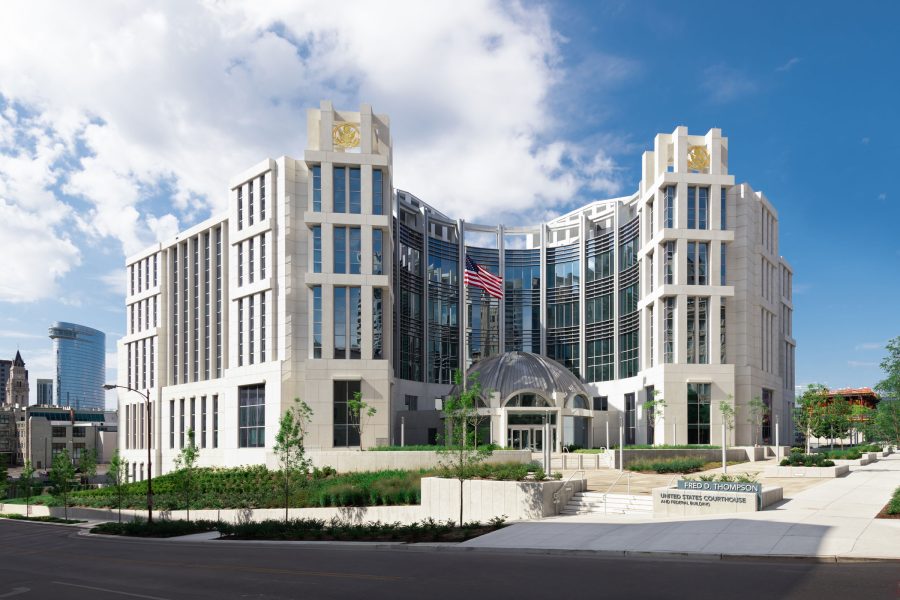
This courthouse was designed to LEED Gold BD+C standards and showcases precast concrete’s sustainability, inherent durability, and low maintenance requirement. Photo by Gabe Ford
The use of precast at BRIT was also an aesthetic choice, affording a cleaner, more uniform facade design. The undulating panels were fabricated offsite, allowing for a degree of precision and quality control that would have been difficult to achieve with traditional onsite methods. How the precast panels were colored and treated with a natural finish eliminated the need for exterior paint, simplifying the building envelope while significantly reducing maintenance concerns like peeling and weathering.
A blade connection for scaffolding was specially fabricated to ensure the bracing system did not interfere with the exterior appearance of the panels, according to Regina Stamatiou, project manager and vice president at Corgan. Developed by US-based building products manufacturer Gate Precast, this element keeps aesthetic intent intact while removing the need for additional patchwork in the future, minimizing interventions and resources for repairs. In July 2024 Gate Precast joined Wells, expanding to a national footprint.
Architectural precast allows for various aesthetic expressions and more design flexibility than ever—with virtually unlimited shapes, textures, and finishes that can be adapted to suit different design requirements and ensure long-term sustainability, says Brian Griffis, Gate Precast’s vice president of sales. “By emulating materials like natural stone through our GateStone finish, we also reduce the need to quarry additional materials.”
Endurance and Efficiency
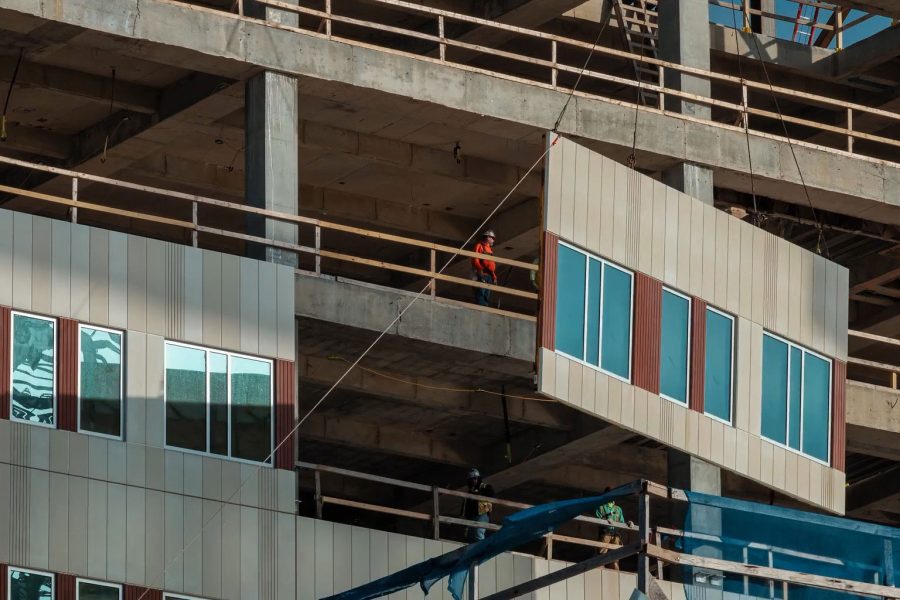
Lightweight GateLite panels helped to accelerate construction on the Baptist Hospital Campus in Pensacola by five months. Photo courtesy of Gate Precast
Beyond aesthetics, precast concrete’s inherent durability and low maintenance requirements are pivotal in reducing the environmental footprint over a building’s life cycle. “It’s a timeless material that doesn’t weather. It holds up to the elements and is very sustainable in its fabrication and longevity,” McDonald says.
Broadly, precast concrete can contribute to a reduction of up to 40% of embodied carbon compared to traditional cast-in-place methods, according to UKGBC. Griffis says innovations in precast concrete—like GateLite, with thinner, fully insulated panels—further reduce embodied carbon while maintaining high-performance standards, exponentially aligning with the industry’s sustainability initiatives. “You’re also getting that continuous insulation and encouraging industry advancements such as admixtures, cement substitutes, and Type 1L cement to lower cement content,” he says.
Evolving Demands
- Precast concrete panels are prefabricated offsite with glass and insulation. Photo courtesy of Gate Precast
- The Nordstrom NYC Flagship project uses the GateStone finish to emulate natural stone. Photo courtesy of Gate Precast
As impacts upon and demands of the building industry continue to evolve, so too does the impact of precast concrete. Notably industries like data centers, health care, and cultural institutions are embracing its advantages, some even seeking to adopt total precast systems for their unparalleled benefits. Griffis says “clients are looking for cost control, speed to market, improved quality, and minimal project risk.” Gate Precast has been increasingly working with more lightweight, unitized precast solutions prefabricated offsite with glass and insulation that allow for faster installation, minimized onsite labor, and higher quality.
Applications are diverse and also site-specific, integrating means for resiliency, including hurricane-resistant designs in the Gulf and wind load-resistant panels for tornados in the Midwest. “A lot of it is designed around the need for 100-year buildings,” he says.
Sustainable Vision
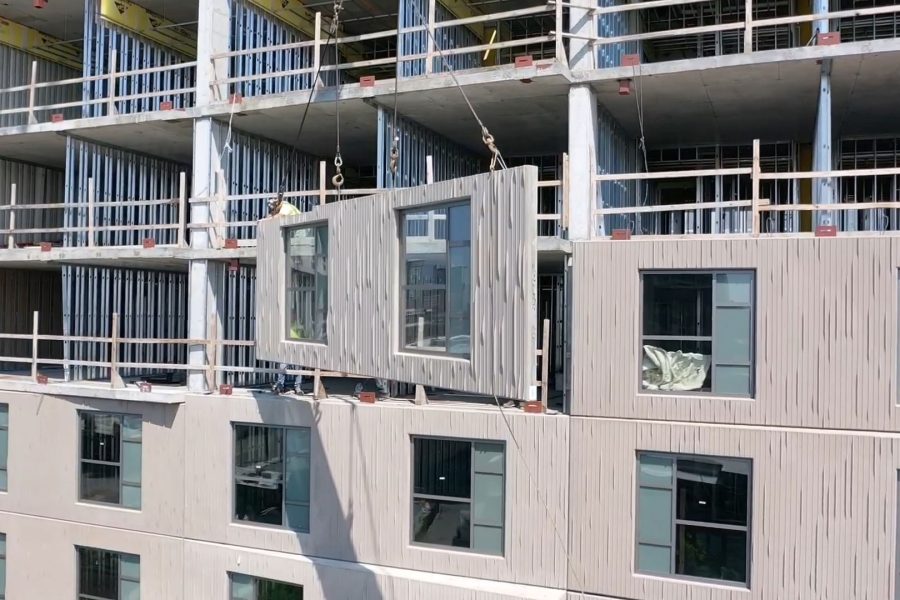
The Printing House Hotel, part of the Tapestry Collection by Hilton, in Nashville, uses Gate Precast’s unitized precast solutions. Photo by Chad Baumer Photography
Thirteen years on from the completion of BRIT, Corgan, too, continues its commitment to sustainable construction as it seeks to achieve carbon neutrality by 2025. Their ongoing project is a net-positive corporate campus for Wells Fargo in Irving, Texas, employing a faceted precast concrete facade that speaks to the growing demands to meet environmental goals within the industry.