Think concrete is ho-hum gray? Think again. Fabcon’s products offer warmth, texture, and a sense of place combined with being load-bearing, low maintenance, and energy-efficient.
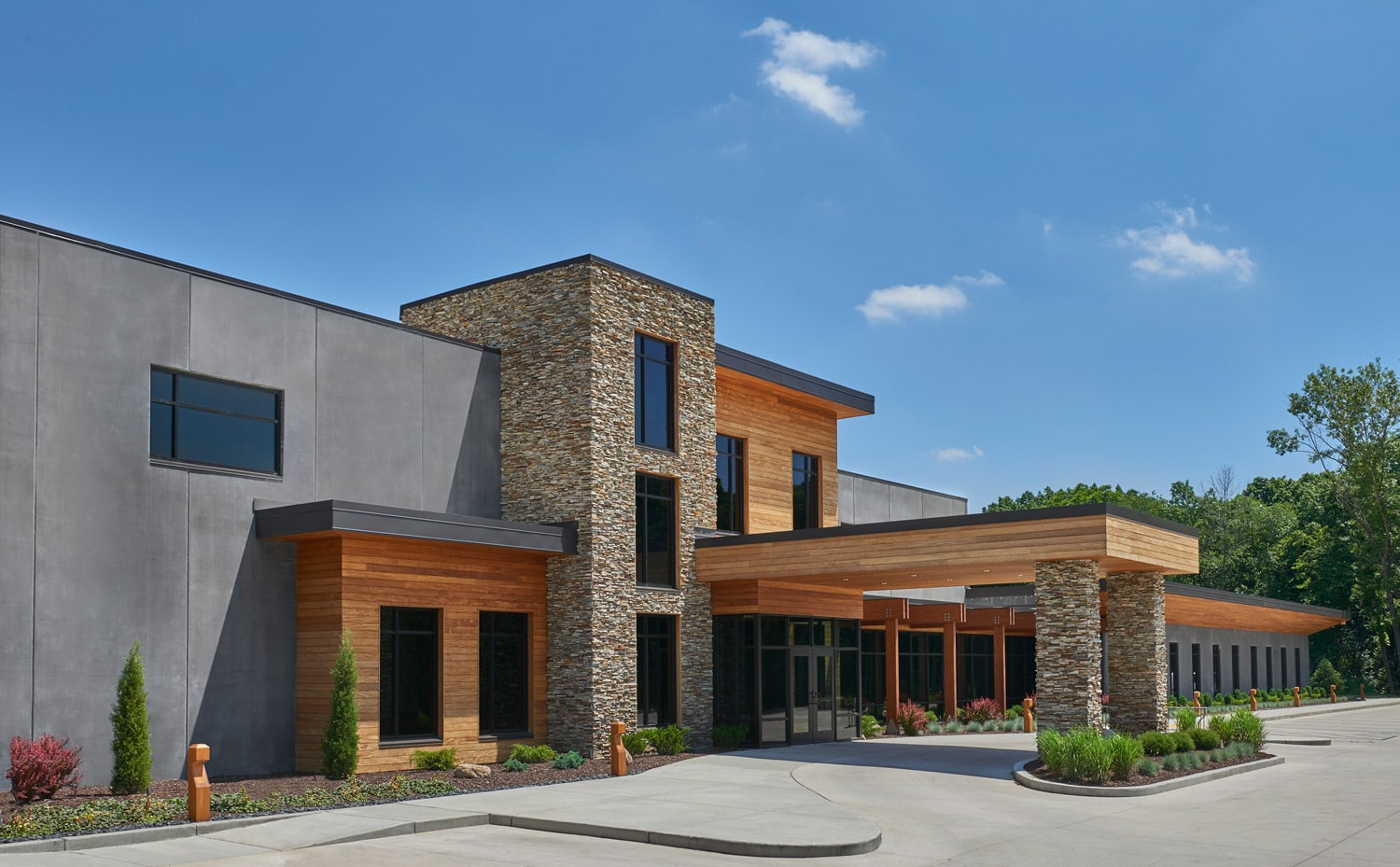
[Photo: Courtesy of Fabcon]
Fabcon’s precast concrete panels are known in the industry for being quick to install, resilient to weather conditions, and a sustainable choice for any budget. Fabcon’s VersaCore+ Green panels increase R-values by 30%, reducing energy costs for building owners.
But there’s more to great design than engineering—color, texture, and visual appeal are needed to differentiate in a saturated skyline. Luckily, Fabcon’s precast concrete panels are far from staid, achieving rich pigment and highly textured contrast effects to elevate any architectural project. Indeed, Fabcon describes its approach as having “functional aesthetics,” proving appearance doesn’t have to be sacrificed for performance.
Fabcon projects all over the U.S. make good on that promise, featuring some of the company’s most exciting finishes, techniques, and aggregates, all supported by the stellar performance and efficiency precast concrete panels are renowned for.
Creating Color
“We can create practically endless colors through the combination of materials we use,” says Rich Mantel, Fabcon’s materials engineer, of their extensive array of custom-mixed aggregates and pigments, which can range in hue from warm reds, yellows, whites, and off-whites to buffs/neutrals and many shades of gray. “We can combine four different ‘primary’ colors of pigments (light red, dark red, yellow, and black) in any ratio to create many different matrix colors,” Mantel says. “Aggregates (stone and sand) can be found from around the country to meet the customer’s desired look.”
Cody C. Lang, also a materials engineer at Fabcon, compares the process of adjusting the four components of the panels (cement, aggregate, tinted pigments, and matrix) to blending red, blue, and green light in a TV to produce a multi-hued projection. “Each of those components has its own color properties,” he says. “By changing and adjusting them, we can create a wide selection of possibilities.”
Amazing Aggregates
One way Fabcon goes above and beyond the standard look of concrete is by folding regional sediment into its aggregates, lending projects across the U.S. a distinctive result with a touch of local character and color. “Say you were to grab some quartz from the ground in Minnesota versus quartz from Pennsylvania,” Lang says. “Each type of quartz would have its own history, with characteristics that are unique to the original location. Think of rose quartz, blue quartz, smoky quartz, milky quartz, et cetera.”
SEE ALSO: Fabcon Asks Tough Questions to Get the Job Done
The number of different stones available in the rich diversity of the country’s geography makes for a generous range of client options. “We can utilize a combination of two colors of cement, gray, or white in the concrete mix, and over 50 different limestones, quartzes, and granites for stones and sands to create different colors and looks,” Mantel says.
Using local aggregates has another advantage for the customer—it greatly reduces costs. “The shipping cost from the quarry to our plant is the bulk of the cost for aggregate,” Mantel says. “The more that local aggregates are used, the lower the cost is for our customers.”
FROM OUR MAY+JUNE 2018 ISSUE
The preferred publication of leading green professionals.
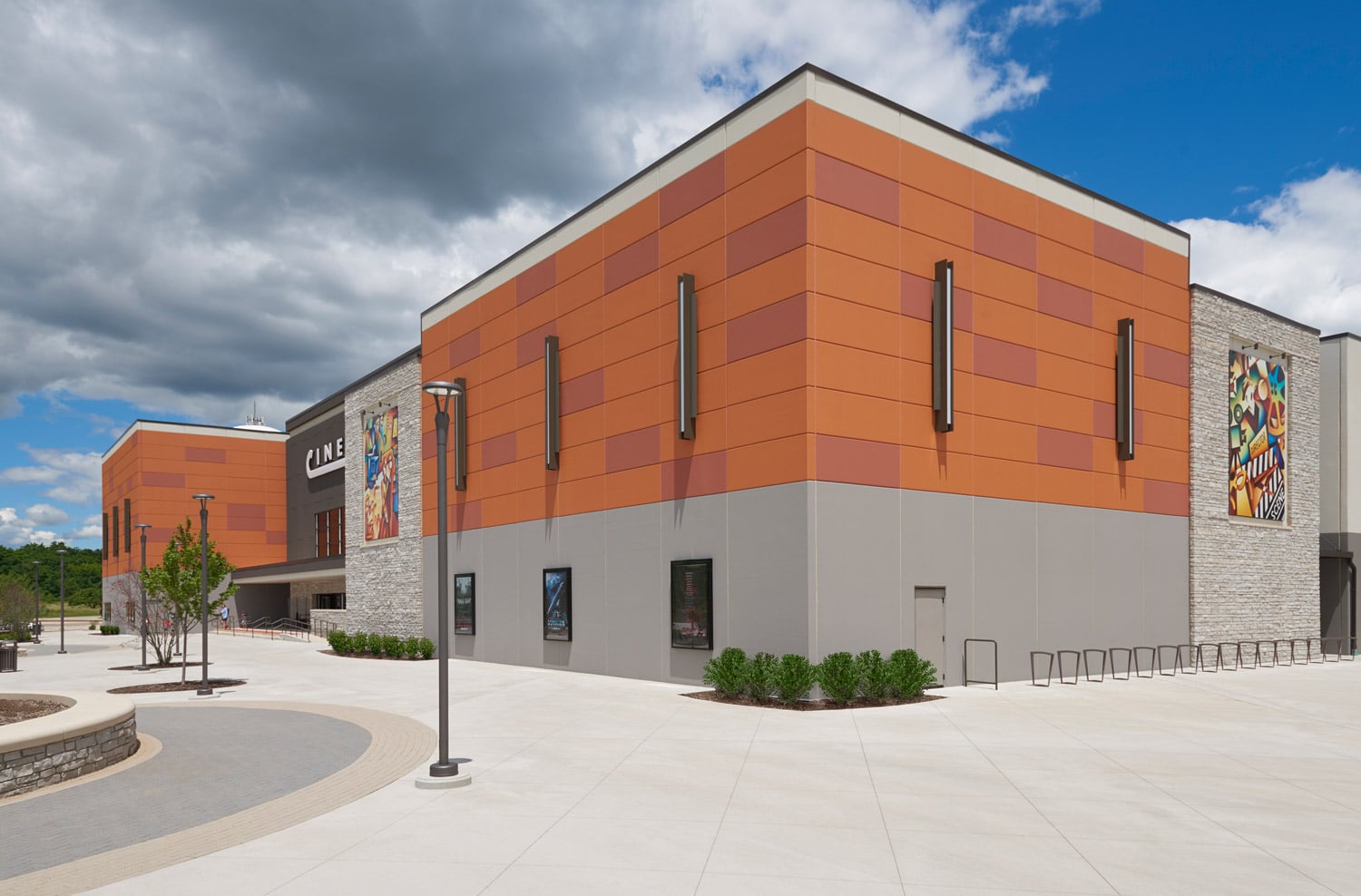
[Photo: Courtesy of Fabcon]
Cinemark Theaters
West Dundee, Illinois, 2016
Fabcon’s easy approach to helping customers “land and expand” has been integral to Cinemark Theaters’ growth. The ability to produce the tallest load-bearing concrete wall panels in the U.S. combined with high sound attenuation ratings ensures both the form and function of theater buildings are achieved. Using a warm paint palette of reds and neutrals and a sweeping command of space, Cinemark creates a cinematic experience by making good use of Fabcon’s steel form finish in some of its more than 300 U.S. locations.

[Photo: Courtesy of Fabcon]
Shutterfly
Shakopee, Minnesota, 2014
When revolutionary photo company Shutterfly needed a customer care and design production facility consistent with its creative and highly personalized style, they turned to Fabcon. An eye-popping tomato-red paint to complement the brand’s logo was applied after Fabcon installed the 80,489 square feet of wall panels just a few miles from their manufacturing facility.
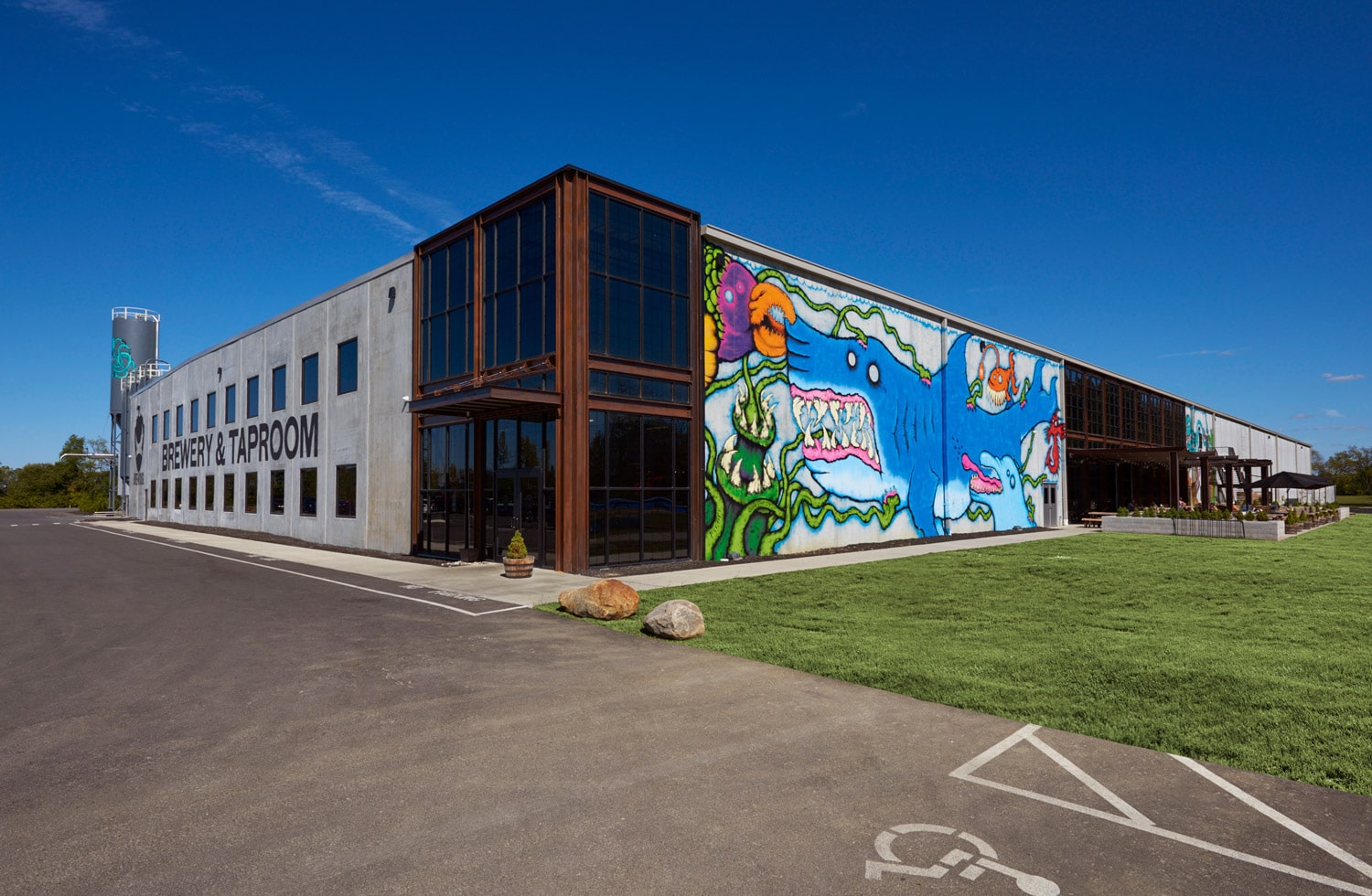
[Photo: Courtesy of Fabcon]
BrewDog
Canal Winchester, Ohio, 2016
When this Scottish brewing company descended upon the U.S., they made the deliberate choice to use Fabcon’s steel form finish in its natural state (a rich, deep gray) to get the industrial look associated with their brand. It proved to be the ideal backdrop for colorful murals both inside and on the exterior walls of Brew Dog’s first U.S. production and distribution facility, restaurant, and taproom.
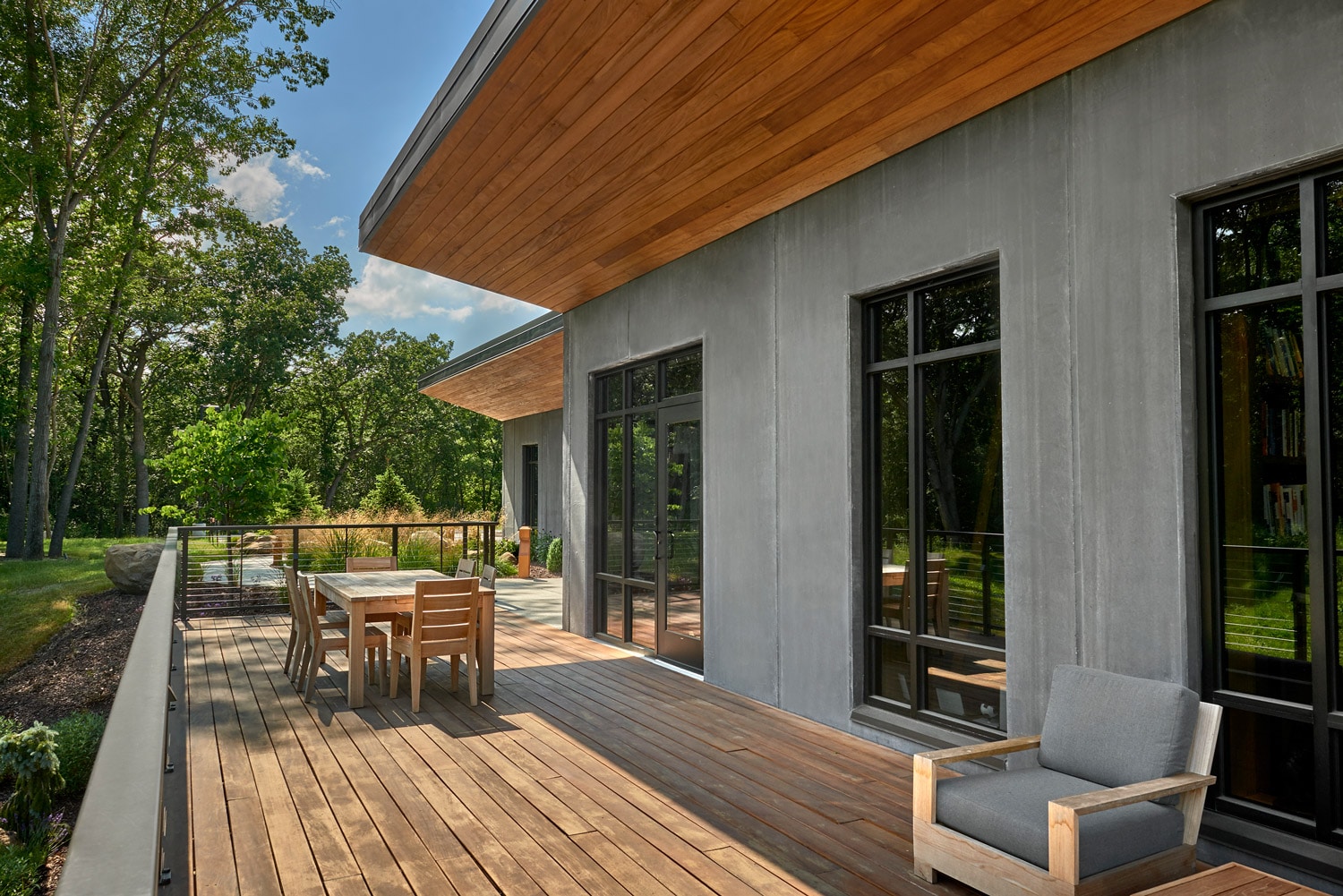
[Photo: Courtesy of Fabcon]
Wisconsin Vision Associates
Burlington, Wisconsin, 2014
Precast concrete made a lot of sense for Wisconsin Vision, a lens and contact lens distributor, when they built their new 63,000-square-foot corporate headquarters and warehouse. A portion of the project was buried in the ground, according to Eric Halbur at Abacus Architects, who designed the project, so precast’s durability and low maintenance was key. “You’re not going to have to update or maintain it,” he says. “It really does reflect Fabcon’s commitment to building something solid.”
The project’s harmony with Fabcon’s precast panels went beyond weather resistance (crucial for the Midwest’s fierce winters). The client wanted a smooth paneled look in a very specific gray that Halbur says a lot of manufacturers were reluctant to commit to, fearing inconsistency in coloring or texture would be ultra-apparent on a non-textured surface. Fabcon worked to provide the client with a sample of a tinted pigment and aggregate blend to achieve the charcoal steel form finish, which they enthusiastically signed off on. The result is a perfectly smooth surface in a custom shade of gray that complements the warm wood and natural stone elements of the warehouse.
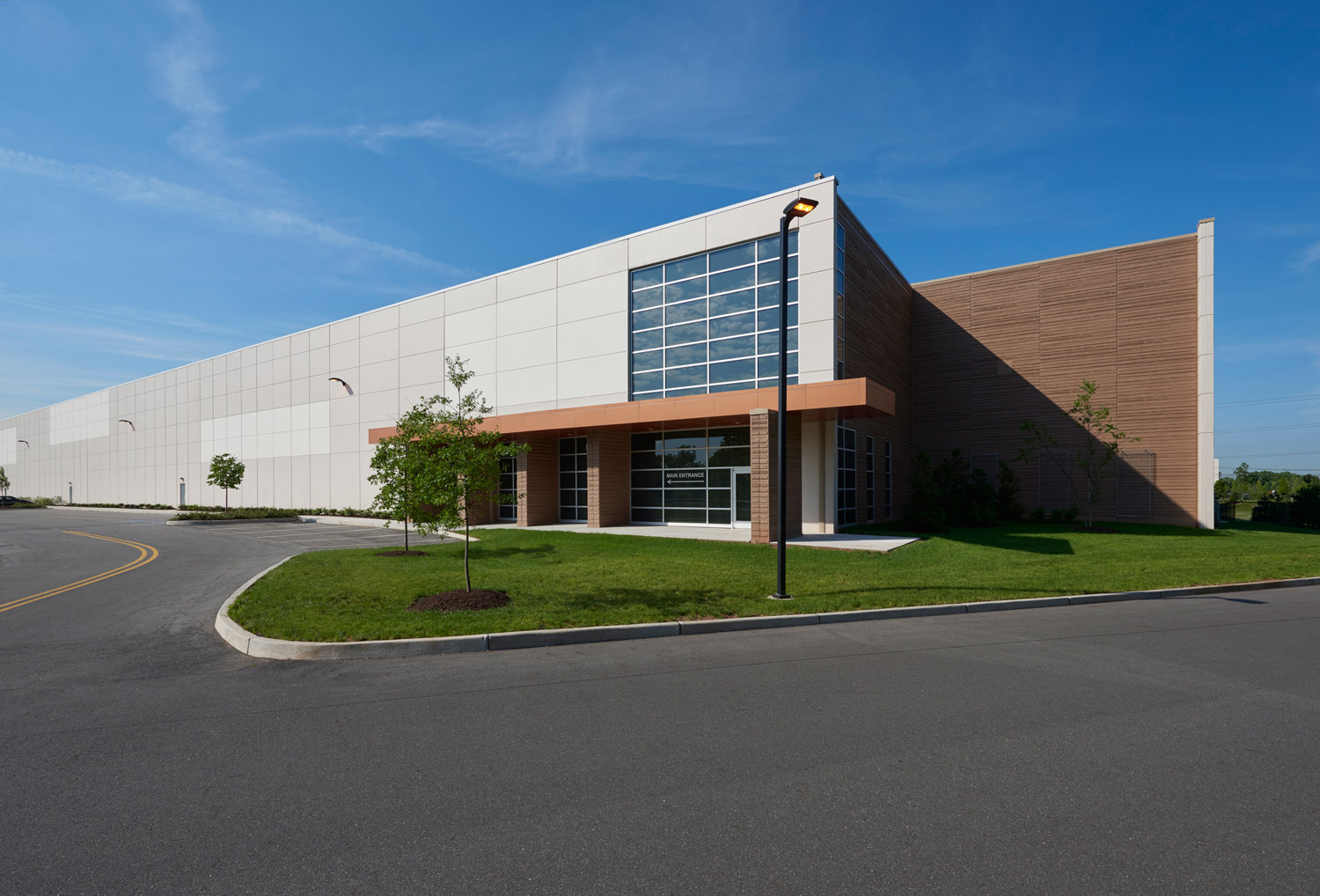
[Photo: Courtesy of Fabcon]
South Washington Park
Piscataway, New Jersey, 2013
To achieve the striated texture on South Washington Park buildings 1 and 2, Fabcon supplied a custom finish by utilizing a horizontal wood plank formliner, which created a textured wood grain appearance with plenty of depth. Formliners are similar to a popsicle mold, wherein concrete is poured into a mold or form to get it to display very specific textures.
It’s possible to get the look of masonry, for example, while still enjoying the low maintenance and durability of precast concrete. To contrast the warmer looking material, a steel form finish made of a cool white contrasted nicely. The total square footage of the buildings is 532,793 square feet. Fabcon provided 209,625 square feet of precast wall panels.
SEE ALSO: This is Why More Builders are Turning to Precast Wall Panels
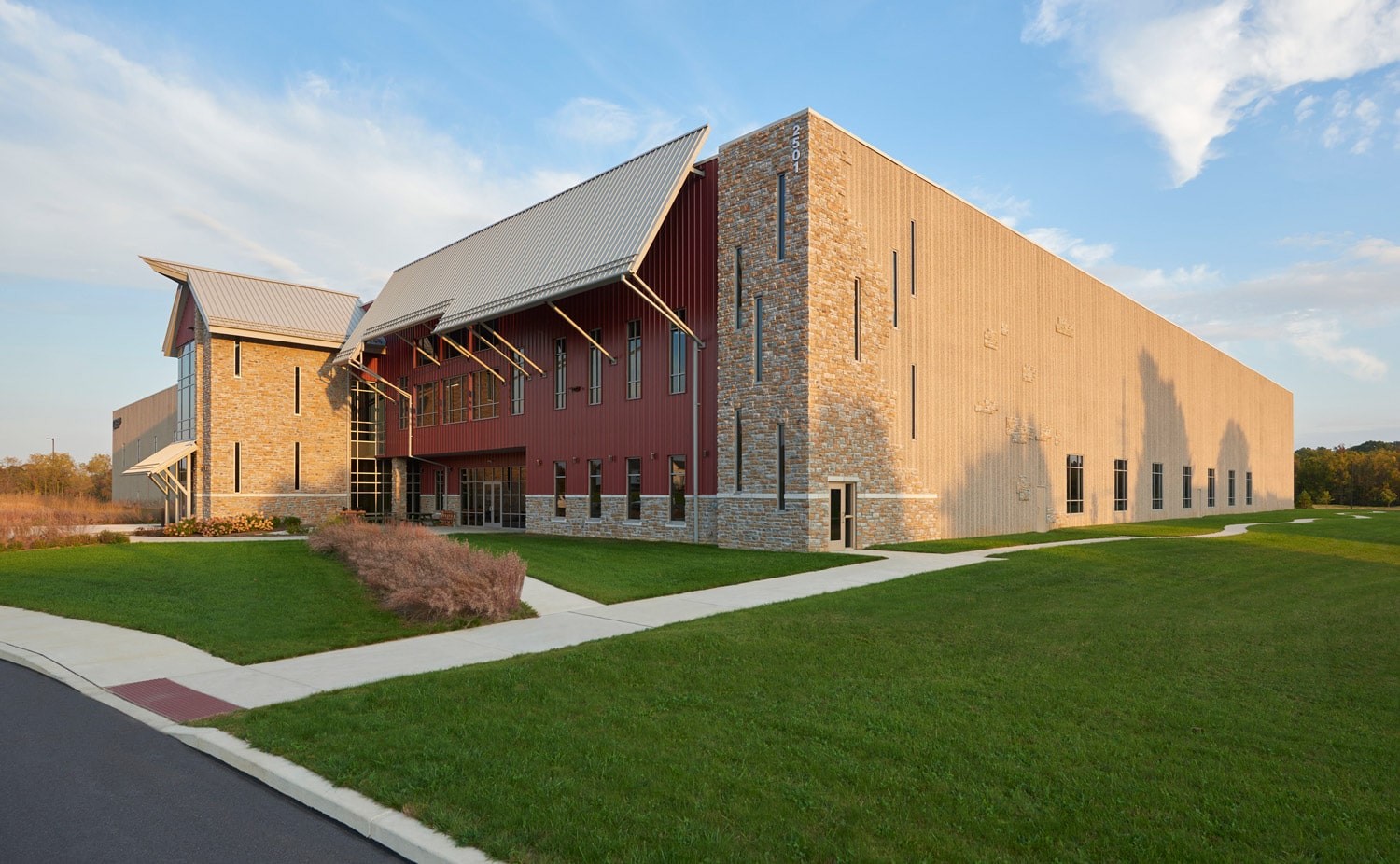
[Photo: Courtesy of Fabcon]
Quality Bicycle Products
Lancaster, Pennsylvania, 2014
Quality Bicycle Products’ east region facility was designed around their philosophy that partnering with other companies is about much more than buying and selling stuff. It’s about sharing a common vision and values. Considering the company’s passion to make the world a better place, it was important to them to build an energy-efficient, sustainable building.
It was also important to the owners that the building’s aesthetic fit the environment and modest community around them. The random rake, exposed Aggregate finish they chose reflects a natural landscape, echoed in their surroundings, and plays nicely with the field-applied cultured stone.