Precast wall pioneer Fabcon has revolutionized the way buildings of all sizes are built.
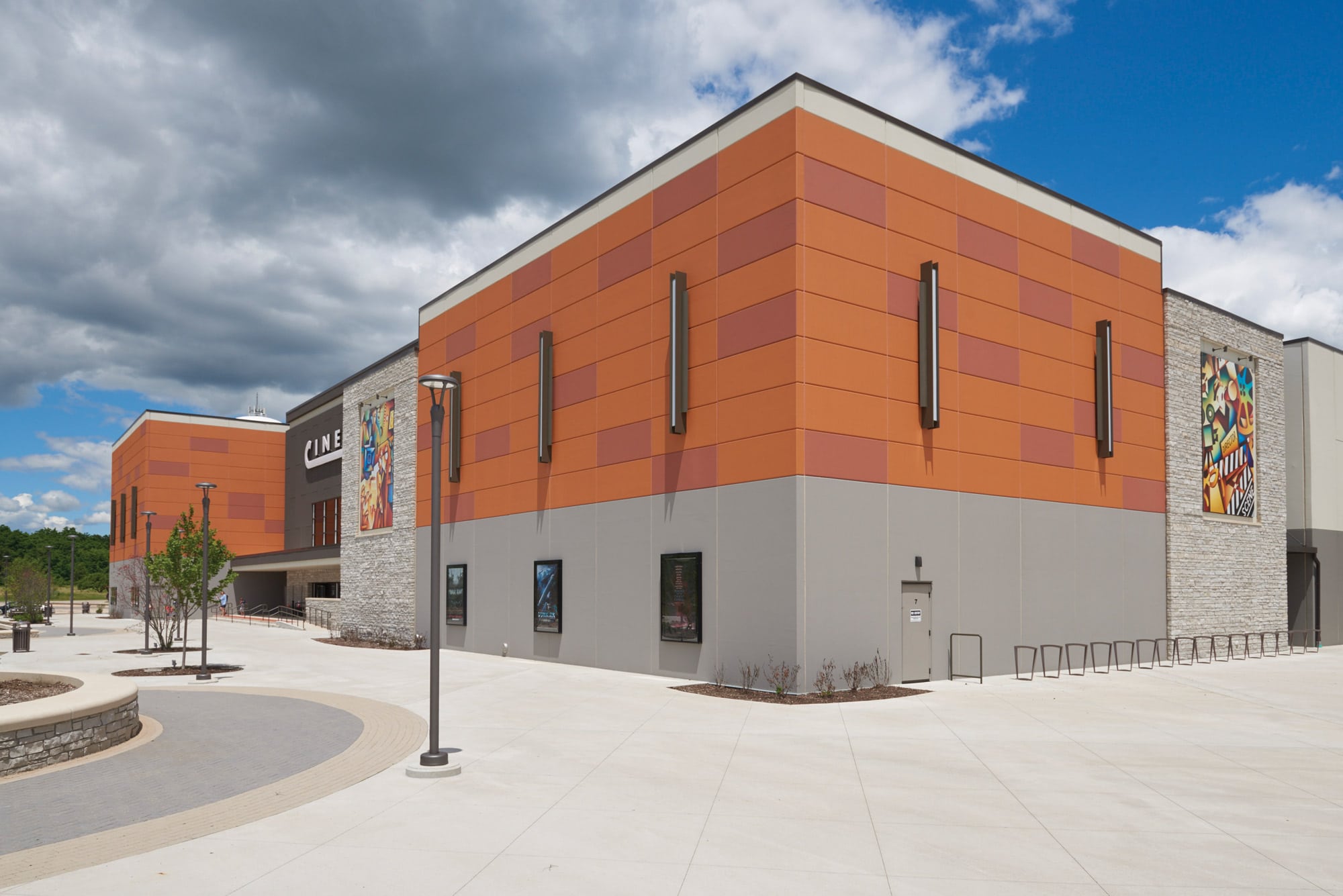
Fabcon’s precast wall panels go up quickly—with up to 250 lineal feet of wall per day installed. [Photo: Courtesy of Fabcon]
How do you build a 1-million-square-foot warehouse in just three weeks? With precast wall panels and an entire team, from design to installation, willing to do whatever it takes to get the job done.
That’s the spirit at Fabcon, which has been refining its approach to precast walls for more than 45 years. Well before Amazon was building a warehouse on seemingly every corner, Fabcon was finding ways to build efficiently and sustainably. That efficiency stems from Fabcon’s approach.
How They Do It
“We do everything in-house, start to finish in the process,” says Joe Dammann, a sales engineer who’s been with the company for 20 years. Unlike other manufacturers that outsource various elements of the process, Fabcon does it all. For customers, this means they have one point person who works with them from design to fabrication to installation.
Dammann says Fabcon has also taken the design process to the next level with a custom version of CAD they developed internally. The software transmits the design to the automated equipment in the plant, projecting an image of the design directly onto the panel. This reduces the amount of measuring done manually, enhancing accuracy and speeding up production. “The more accurate the panels are coming out of the plant, the quicker we can erect them in the field,” he says.
Thanks to the all-Fabcon team, customers are never stuck waiting for a sub-contractor to finish one element of the project before things can move along, Dammann says. In addition, any tweaks can be easily accommodated. “We’re extremely flexible in being able to make changes along the process,” he says. “If somebody has a plan change within days of the panel going into fabrication, we’re able to incorporate the change—often without negatively impacting the schedule.”
FROM OUR NOVEMBER+DECEMBER 2017 ISSUE
The preferred publication of leading green professionals.
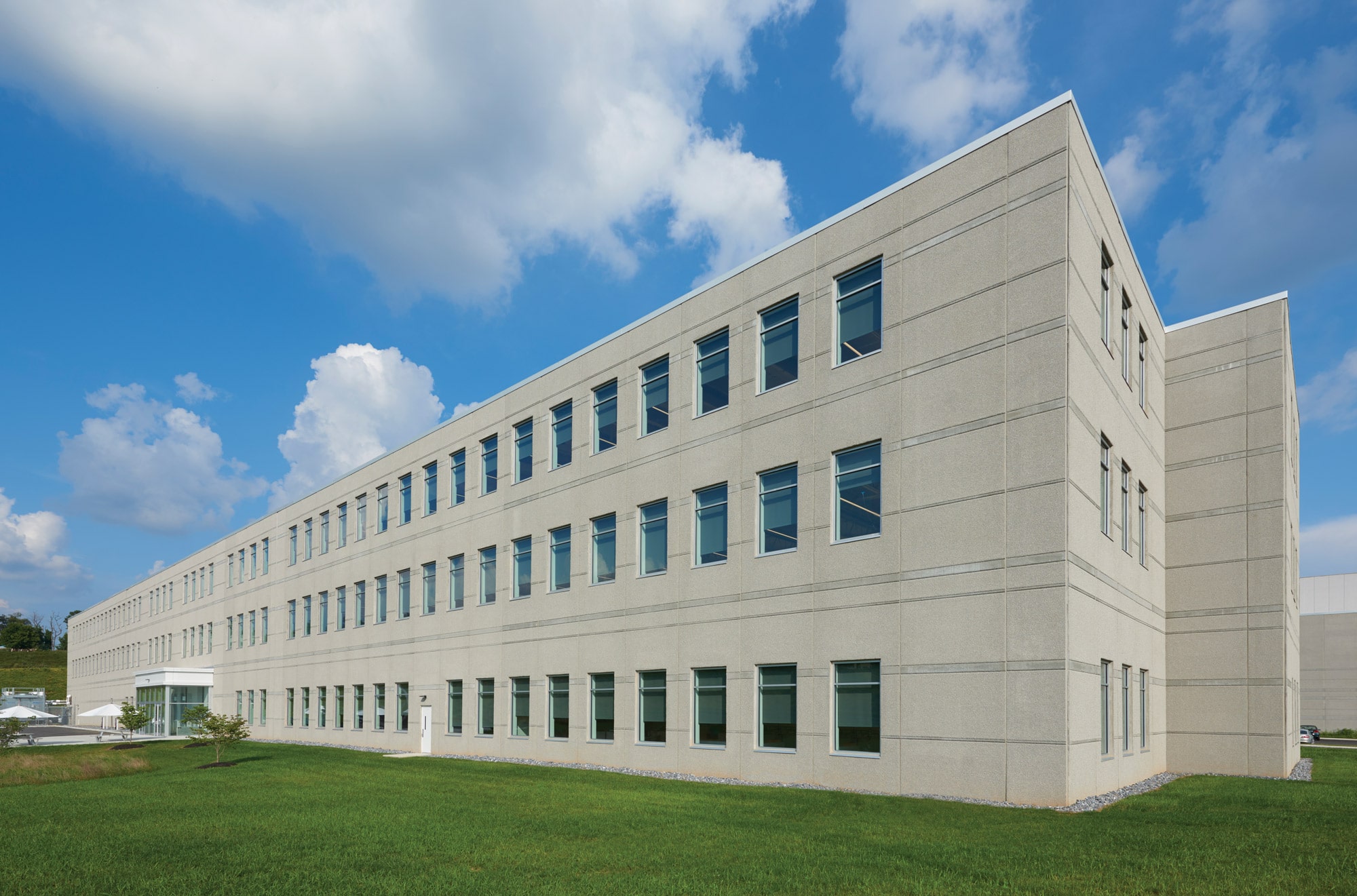
Johnson Controls, New Freedom, PA. [Photo: Courtesy of Fabcon]
Fabcon’s highly insulated walls are built in the controlled environment of a factory, so weather doesn’t pose an issue. Whether it’s below zero or 85 and sunny, construction can continue on schedule, Dammann says. Once the walls are built, they’re quickly installed in the field, with crews able to put up an average 250 lineal feet of wall per day, he says.
Fabcon’s flexibility and affordability stems from a sophisticated supply chain that serves its large volume of production. The company has plants in Minnesota, Ohio, Pennsylvania, and Kansas. Depending on the day, some 35 to 50 truckloads of precast panels are transported from those facilities to job sites, says Paul Schreifels, manager of supply chain at Fabcon. Schreifels has spent the last eight years working with suppliers to meet the constant need for materials within those plants.
The Materials They Use
Fabcon has always been on the cutting edge of the precast market, Schreifels notes, but it renewed its focus on cost containment and efficiency during the recession. Material sourcing was an important part of that effort.
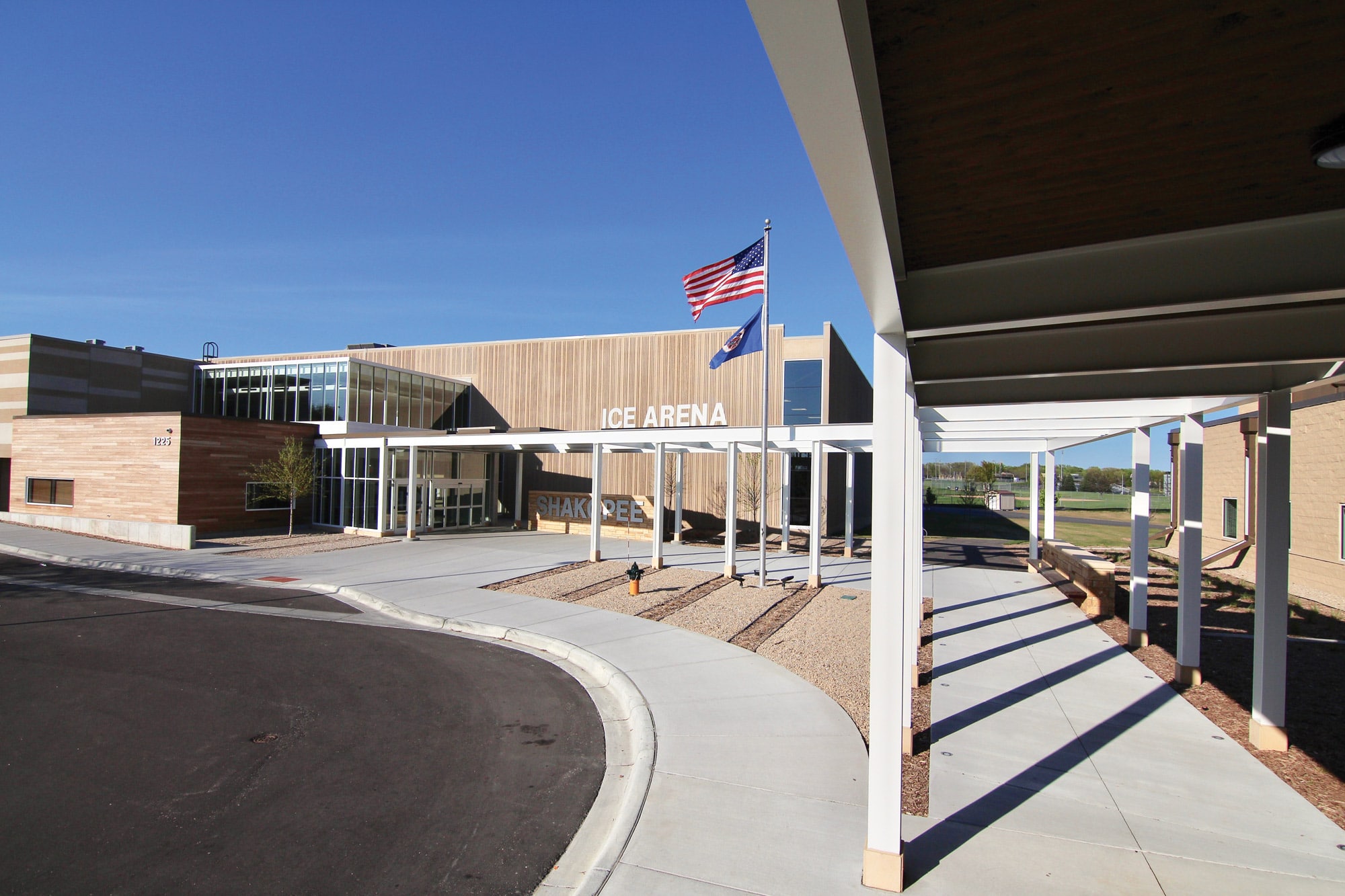
Shakopee Community Center, Shakopee, MN. [Photo: Courtesy of Fabcon]
Steel makes up about half of Fabcon’s total material cost, Schreifels says, with cement and aggregates making up the balance. Fabcon uses from 20 to 100% recycled foam within its products, which boosts its sustainability. And the walls are built to last: Schreifels says longevity is always a top concern when selecting materials. That means finishes are suited to the climate where they’ll be installed. In Minnesota, for instance, exposed aggregate finishes are often used, which never have to be painted—a boon for a state with harsh winters.
Fabcon patented its VersaCore+Green™ solution in 2007 to offer a highly sustainable product with a range of R values (up to R 28.2) depending on the thickness of the panels. The thermal value, combined with the quantity of recycled materials, gives customers the opportunity to gain LEED points as well as tax credits and incentives depending on the project location.
“Customers who may have been exclusively using concrete block or metal panels in the past are turning to precast walls because of the R-value they offer.”
In addition to assessing the company’s material sourcing, Schreifels and his team have also pursued ways to reduce their water use. Thanks to a conservation initiative at their Minnesota plant, they now recycle basically all of the water that goes into the facility—with much of it being used multiple times, he says.
Fabcon has invested significant time and energy into developing new finishes for its products, from sandblasted styles to exposed aggregate, all in an infinite variety of colors. This allows them to meet a dizzying array of needs, from a 20,000-square-foot church to a 2-million-square-foot data center, Schreifels says. And all of those customers receive the highest levels of service, efficiency, and quality.
“Fabcon’s ability to economically produce our walls in our precast plants is what starts to set us apart,” Schreifels says. “The sheer volume of product we can produce in our plants is impressive. Even to me today. We’re installing a building in a matter of days.”
Read more about Fabcon and catch up on more of their gb&d stories.