Sika Sarnafil is bringing green space back to the city with green roofs.
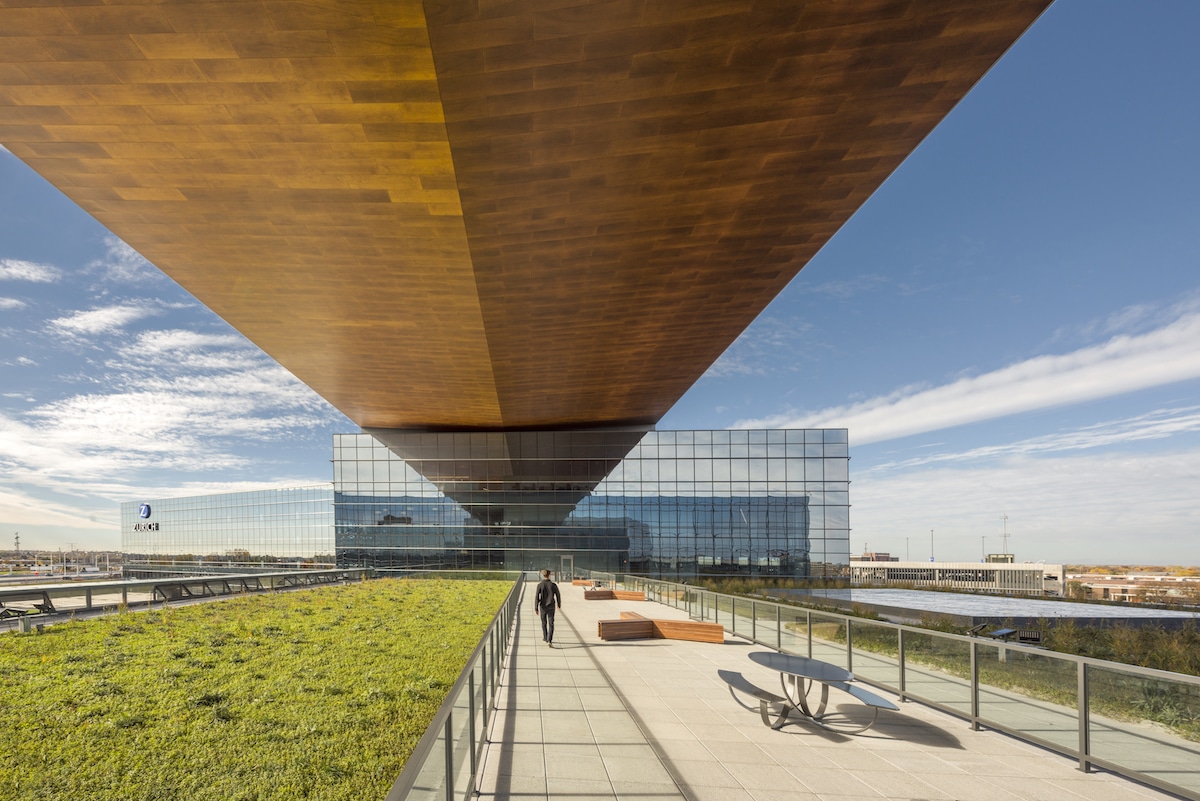
[Photo: Courtesy of Sika Sarnafil]
From a sustainability perspective, installing a green roof seems like a no-brainer. Vegetative roof coverings offer a host of benefits. They cut down on pollution, reduce heating and cooling costs, improve acoustics, extend a roof’s life, and offer an aesthetically pleasing way to bring nature back to urban living. “There are not many applications you can do on a building that have as many benefits as a green roof,” says Bill Bellico, director of marketing and inside sales for commercial roofing and waterproofing company Sika Sarnafil’s U.S. based operations.
The green roofing trend—which dates back thousands of years, to even the Hanging Gardens of Babylon, for instance—took off in Europe with sod coverings. The trend later developed into more comprehensive systems—the ones we use today—in the 1960s in Germany. The systems started to emerge in the U.S. about 20 years ago, Bellico says, with one of the earliest and most visible applications being Chicago City Hall in 2000.
Vegetative roof coverings have become popular in all types of environments, from office buildings to health care facilities, where they are being used as an oasis for patients and their families. “Everybody seems to be fascinated by green roofs, whether they’re involved in the construction and design industry or not,” Bellico says. “They instantly appeal to human nature. The benefits are getting more widely understood
and appreciated.”
Sika Sarnafil has been at the forefront of the green roofing business—installing their first green roof in 1969 in Bad Zurzach, Switzerland, which is still growing strong today. But it hasn’t been all fun and games; the company—and its host of experts—has learned many lessons along the way. Two of those experts recently sat down with gb&d to share some of what they have learned and offer advice to anyone looking to go the green route.
Field Support Services Manager Jon Jensen and Education, Waterproofing, and Healthcare Facilities Specialist John Robinson, who is also a certified green roof professional, together have more than 50 years of experience in the industry. They recently shared green roof advice with gb&d.
FROM OUR MAY+JUNE 2018 ISSUE
The preferred publication of leading green professionals.
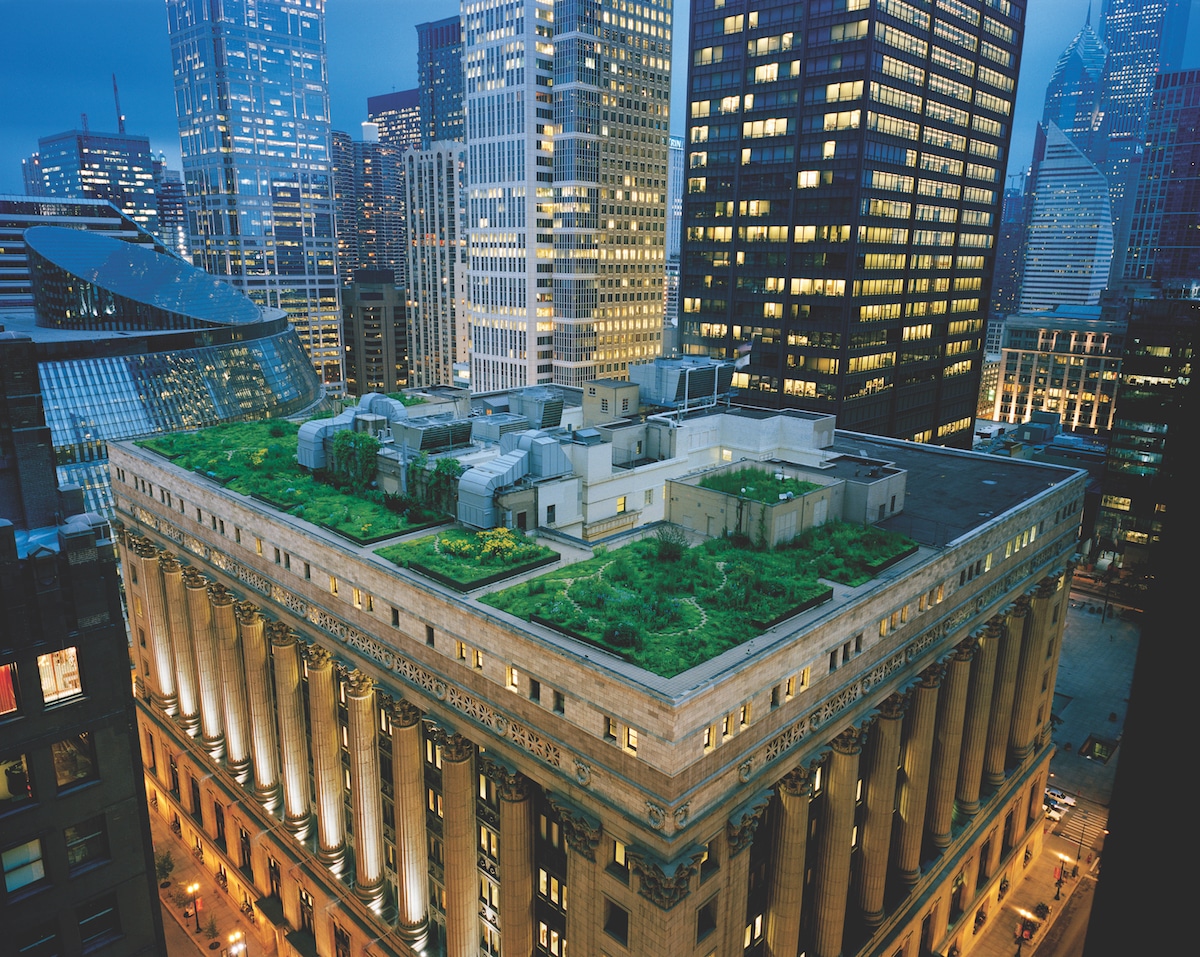
Sika Sarnafil installed a green roof on Chicago’s City Hall in 2000. [Photo: Courtesy of Sika Sarnafil]
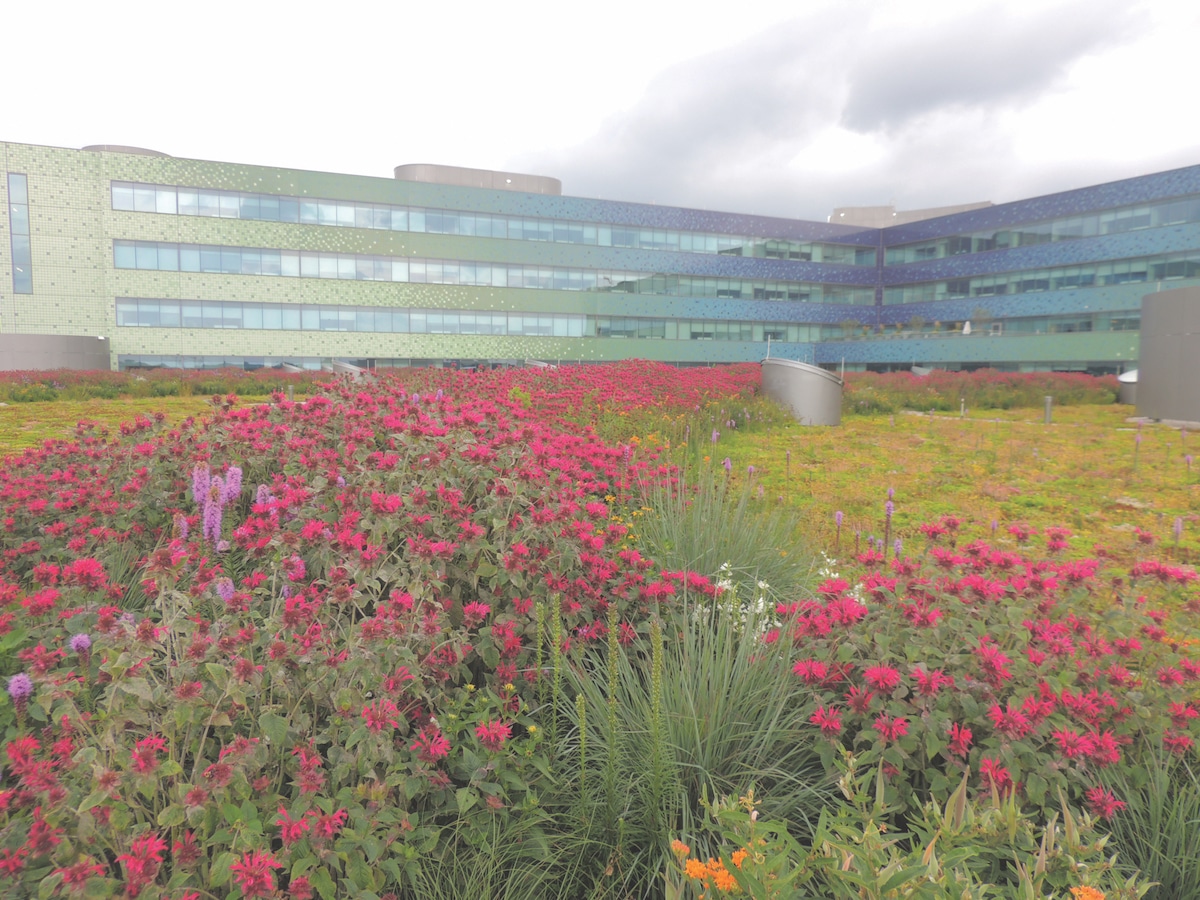
The green roof on the Mercy Health-West Hospital in Cincinnati is beneficial to patients, families, and the hospital’s staff. [Photo: Courtesy of Sika Sarnafil]
gb&d: How have you seen green roofs evolve?
Jensen: The basics have generally remained the same, but the creativity that goes into the designs has evolved. Other features have been added—patterns, colors, landforms that create interesting and unique aesthetics. The use of green roofs has definitely grown, no pun intended, but the waterproofing has stayed the same.
Robinson: Green roofs have been utilized for centuries in many civilizations. We have been designing and constructing plaza decks and rooftop spaces that incorporate green areas for decades. The European model of more lightweight, shallow soil, easier to maintain extensive systems have been gaining popularity in the U.S. in the past decade due to cost and design advantages.
gb&d: What misconceptions do people have about green roofs?
Robinson: There are many fallacies surrounding green roofs. Some of the more common misconceptions include thinking all types of green roofs are too expensive to construct, they are difficult to maintain, they all leak, they are difficult to repair, and they do not offer the intended environmental benefits. As we install more green roofs, we look at proven systems, the design application, and performance and get more data that validates the benefits. We are installing systems that are easy to maintain, that don’t leak, and are easy to repair if needed.
Jensen: A properly designed, quality roof system underneath a properly maintained vegetative cover means years of worry-free service. Installing a green roof over a traditional low-slope roof can alleviate the issues of storm water runoff and the urban heat island effect, while increasing overall aesthetics. Also, by installing a vegetative cover over your roof, you are increasing the life of the roof by minimizing UV exposure.
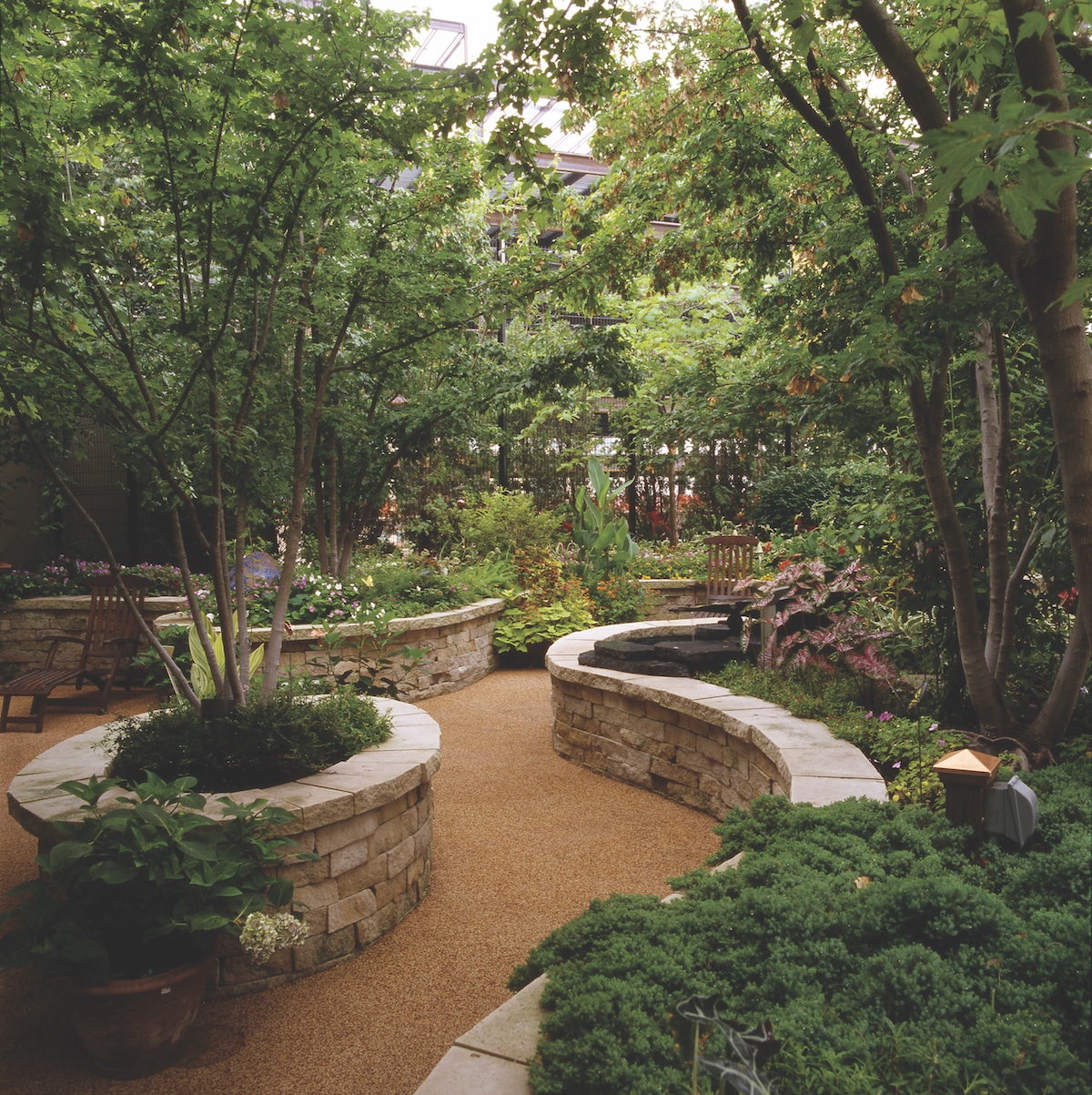
Sika Sarnafil beautified this outdoor space at the St. Louis Children’s Hospital. [Photo: Courtesy of Sika Sarnafil]
gb&d: What challenges do green roofs pose?
Jensen: The big thing is making sure the design and details are correct. All entities involved need to be up-to-speed on green roofs. It is not an exposed roof that you can look at any time. You want to do it right the first time to avoid costly repairs later.
Robinson: The biggest challenge I see is dealing with upfront cost and thinking about the roof in terms of total cost across its life cycle. While the initial cost of a vegetative roof can sometimes be two to three times the cost per square foot of a traditional roof system, there is a wide range of application options that can work for different budgets. In addition, people typically focus on upfront cost instead of considering the total life cycle of the roof. A traditional exposed roof might only last 15 to 20 years, whereas a protected, covered, vegetative system could last in excess of 50 years. It is important that you have policy and code officials that are educated on green roof systems and any storm water credits or other grants that may be available to someone constructing a green roof.
gb&d: What is the most common mistake people make?
Jensen: From my perspective, tradespeople—landscapers, HVAC technicians, et cetera—can accidentally, and oftentimes unknowingly, damage the waterproofing membrane. Everybody involved with roof maintenance needs to be made aware of the watertight membrane below the green roof and certain precautions need to be taken to keep it that way. For example, we had a landscaper put spikes in to hold irrigation in place and it went right through the membrane. It caused leaking into the building and was difficult to figure out what was going on.
Robinson: Not receiving an accurate quote for the specific green roof needed, poor design, construction and maintenance, and use of substandard materials are the big ones. When the roof is not properly designed or maintained—the plants get too much water, or not enough, vegetation is covered in weeds, draining is impeded—that leads to premature failure of the system. All of these things are critical to the success of the system.
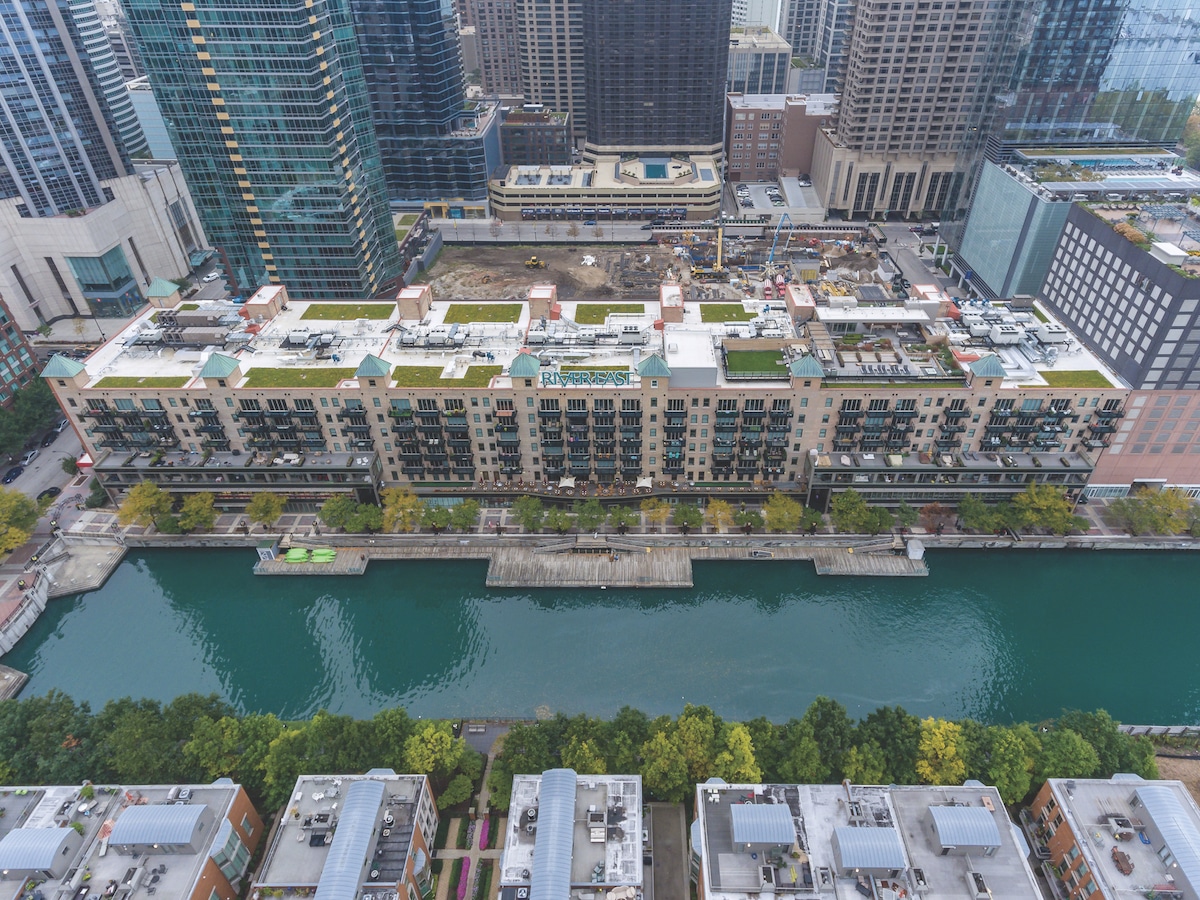
[Photo: Courtesy of Sika Sarnafil]
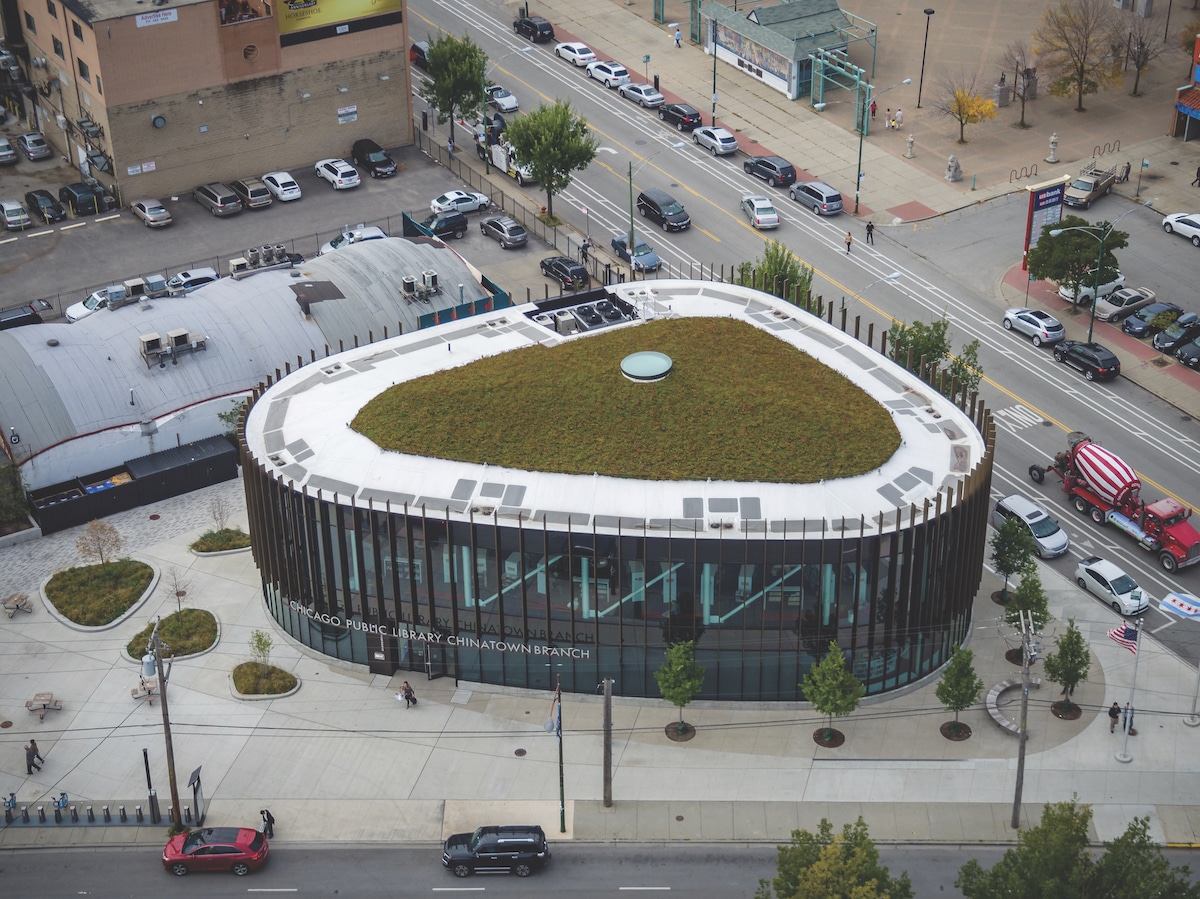
Sika Sarnafil has worked on many large projects, including Chicago’s Chinatown public library. [Photo: Courtesy of Sika Sarnafil]
gb&d: What is the biggest lesson you have learned?
Jensen: Quality assurance needs to be maintained through inspections and testing. Monitoring the work of other trades is paramount. Locating a leak in a green roof can prove to be a difficult and costly endeavor. It is time-consuming, expensive, and a large disruption to the system. It’s also vital to have a chain-of-custody plan in place; once the roof is tested and deemed watertight, all potential workers on the roof must be educated and mindful of the waterproofing membrane. It is also important to take weight into consideration and know how much the structure can handle.
Robinson: Green roof construction is still not common, and it requires both a contractor and waterproofing manufacturer with documented experience in these systems. Also, the project should require a single source warranty that includes the waterproofing and green overburden under a single responsible party. Coordination of trades is crucial. All parties must know their responsibilities.
gb&d: The commercial roofing industry has relied on Sika Sarnafil’s thermoplastic single-ply membranes for more than 50 years. How are these used in green roofs?
Jensen: The membrane is the primary waterproofing for the roof. When using a thermoplastic single-ply membrane, the seams can be hot-air welded creating a water tight monolithic sheet. And the seams are good for the life of the system, unlike other systems that use glues to bond their seams. The sheet also acts as a natural root barrier eliminating the need to add another layer of protection.
Robinson: The advantages include a long life cycle, root and rot resistance, chemical resistance, sustainability, and design flexibility.
AS SEEN IN
Chicago City Hall
Chicago Public Library’s Chinatown Branch
St. Louis Children’s Hospital
Target Center
The Pulitzer Foundation for the Arts