Story at a glance:
- Greenfiber® SANCTUARY cellulose insulation differs from other forms of insulation in that the raw product, trees, creates a carbon sink.
- In addition to competitive and superior insulation properties, SANCTUARY blocks sound, odors, and fire.
- Able to earn LEED points, the product has undergone a Life Cycle Assessment and is gaining market share with increasing awareness of its ease of installation.
At this point in the journey to make buildings more sustainable, one truism is fairly well understood. Before investing in renewable energy systems, energy-efficient windows, programmable thermostats, recycled steel, sustainable wood, and energy-efficient lighting, one feature is essential—a tight building envelope with high-performing insulation.
Most of the traditional materials—fiberglass, mineral wool, polyurethane-spray foam, polystyrene foam board, and polyisocyanurate—found in insulation require the extraction and use of fossil-based ingredients. Even worse, the manufacturing processes for these materials have a high carbon footprint. A study of 503 newly built homes in the Toronto region found that insulation is the second largest source (second to concrete) of material-related carbon emissions. More than 25% of the buildings’ embodied carbon was in those homes’ insulation materials.
One insulation material stands apart from the others, though, and that is cellulose.
Why Cellulose?
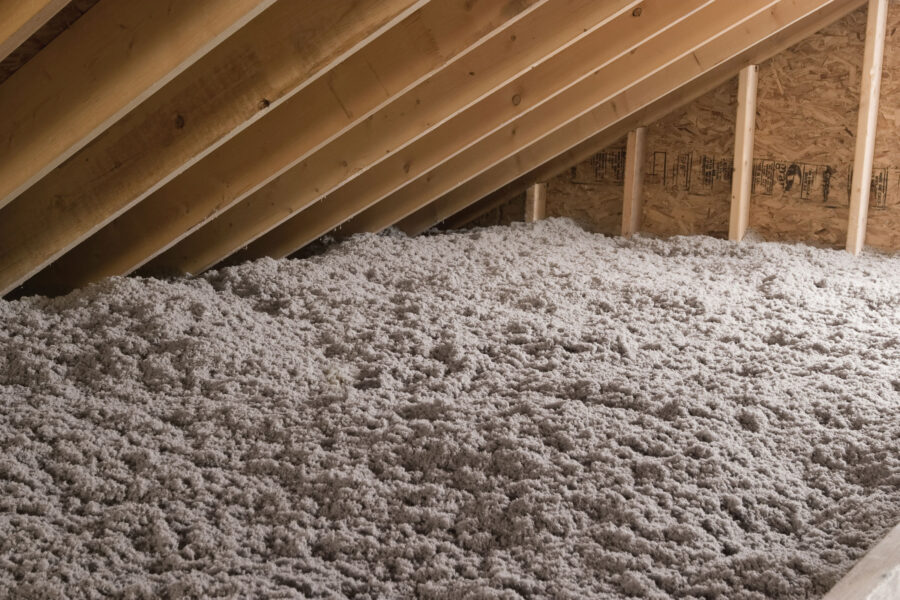
Photo courtesy of Greenfiber
One reason cellulose insulation differs is that cellulosic material is plant-derived, typically from trees. That means the original source of these materials captures atmospheric carbon over the years before the trees are harvested. Even better, cellulose-based insulation is largely derived from post-consumer recycled paper, which is made from those trees.
A tree otherwise left to rot or burn would return the carbon to the environment, but when processed into paper and later building insulation, it continues to hold that carbon for at least the life of the structure.
The second reason cellulose insulation carries less embodied energy is that the manufacturing process of turning this recycled paper into building insulation itself has a low carbon footprint.
According to a study conducted in 2022 by the Builders for Climate Action—using BEAM (Building Emissions Accounting for Materials) software—11 types of cavity fill insulation products were measured for their Global Warming Potential, or GWP, all with R-10 insulation values applied over 100 square feet. The types ranged from closed cell polyurethane spray foam HFC (with the highest GWP) to cellulose dense packed (the lowest GWP). The second and third lowest-GWP ratings were cellulose dense packed and cellulose loose fill, respectively. The two highest performing products are manufactured by Greenfiber, all of which benefit from biogenic carbon storage because those products derive from trees, not petroleum.
Other types of insulation that had poorer GWP performance than cellulose fibers were mineral wool batt, mineral wool loose fill, fiberglass loose fill, fiberglass batt, and hemp wool batt.
From Post-Use Paper and Cardboard to Insulation
Greenfiber, which manufactures cellulose-based insulation, sources recycled paper at its 13 plants in the US and Canada from primarily industrial sources.
“Initially we received post-consumer newspapers from curbside recycling programs,” explains Steve Gerber, the company’s vice president of business development. But with the demise of printed newspapers the company has shifted its sourcing and operations in the past five years to using corrugated boxes and other fiber sources from mostly commercial and industrial operations.
“We had to change our equipment to adapt to these fibers,” he says. Examples of those sources are overruns, misprinted packaging, and post-use cardboard. It arrives in a mostly shredded form at their plants, with no moisture or other contamination on the material accepted.
When received, Greenfiber’s operations include removing plastics and metals from the material. From there the operation includes shredding to about a quarter-inch size, which achieves optimal density (“fluffiness”) for the end product. Fire retardant chemicals that meet standards established by the Consumer Products Safety Commission are applied.
Temperature, Sound, Odor, and Fire
To the building owner or occupant, the first expectation of an insulation material is temperature control—keeping the heat out or in, depending on the season. That typically is measured in R-values. But that’s not the whole story when it comes to how Greenfiber’s Sanctuary cellulose insulation performs.
In raw R-values SANCTUARY provides between 3.7 and 3.8 per inch of thickness. At thicker installations, say a 2-by-4-inch wall cavity, that value is an R-13. In attic applications about a 10-inch provides an R-38. On average the material reduces heating and cooling bills by about 25% or more.
Whether blown in, spray-applied, or dense-packed, the characteristics of the SANCTUARY product are it fills tiny joints, crevices, and gaps, creating a denser barrier that not only provides thermal blocking but also muffles sounds and reduces pollution infiltration (i.e., odor transfer).
Another feature of walls is they do, or should, block the spread of fire. This is a particularly important feature with town homes that share walls; your neighbor’s fire should not burn your home, too. Greenfiber provides a fire-rated material, Greenfiber FRM Insulation for the SANCTUARY Two-Hour Firewall Assembly, that provides a two-hour firewall and blocks sound with an STC of 56 or greater.
Where Cellulose Insulation is Used
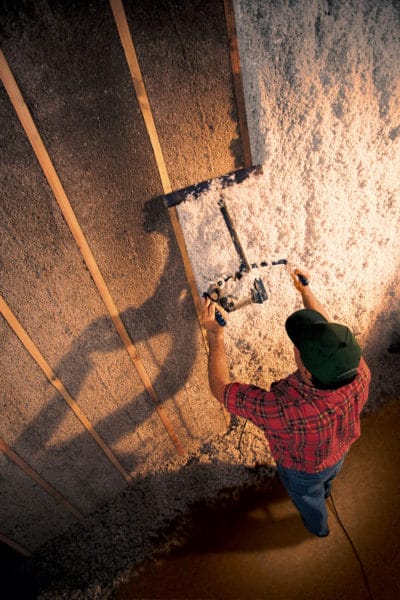
Greenfiber’s wall insulation starts as a plant material, is made into paper, and reused as insulation. Photo courtesy of Greenfiber
Higher-performing cellulosic insulation is used in residential and commercial structures. About half of what Greenfiber sells is applied to new construction and the other half to existing buildings.
“Builders and owners like the sustainability features of Greenfiber,” says Laura Woodford, the company’s vice president of marketing. “Contractors are more focused on a defect-free installation process. If there are no defects, they don’t get called back to redo something. Greenfiber SANCTUARY satisfies both.”
That said, these plant-derived products currently hold a smaller market share relative to fiberglass, mineral wool, and polyisocyanurate. One reason is a lack of familiarity with the installation process, which can be accomplished by non-professionals. Others are perceptions about moisture sensitivity, settling, product availability, and upfront costs.
But moisture issues are addressed in a variety of ways for all kinds of reasons, not just insulation. Settling is offset by anticipating it in the installation process. Availability is increasing all the time, and the upfront costs—not really an issue, as it prices on a par with fiberglass and lower than foam-types of insulation—are soon offset by energy savings in a project.
Thoroughly Tested and Evaluated
To meet both municipal building codes and the sustainability demands of builders and occupants, Greenfiber SANCTUARY has undergone evaluations by Underwriter’s Laboratories and complies with all the requirements of the Consumer Products Safety Commission, in addition to being rated by the LEED program.
The company has also engaged Sustainable Minds to conduct a life cycle assessment (LCA) to evaluate the product in all life cycle stages—from raw material sourcing to manufacturing in six of its plants to end of use. A 41-page report is available from the company that provides detailed LCA data.