Story at a glance:
- Understanding the need and proper use of vapor barriers and retarders is crucial when it comes to moisture control.
- A properly selected and installed under-slab vapor retarder is the first line of defense against water vapor and soil gas migration.
- Unprotected slabs without the proper moisture-barrier can compromise the home’s interior by allowing pathways for water vapor and soil gas to travel through.
Across much of the US, having the right vapor barrier or vapor retarder is crucial to controlling moisture in the home. A vapor retarder is defined as a material that reduces the rate at which water vapor can move through a material, according to the US Department of Energy.
Vapor barriers can help control moisture in everything from basements and crawl spaces to ceilings and walls. The best moisture control must also have air-sealing gaps. It’s critical to use vapor barriers correctly, as incorrect use leads to more moisture related problems, according to the Building Science Corporation.
“Vapor barriers were originally intended to prevent assemblies from getting wet. However, they often prevent assemblies from drying,” writes Joseph Lstiburek in this in-depth piece on understanding vapor barriers. “Vapor barriers installed on the interior of assemblies prevent assemblies from drying inward. This can be a problem in any air-conditioned enclosure. This can be a problem in any below grade space. This can be a problem when there is also a vapor barrier on the exterior. This can be a problem where brick is installed over building paper and vapor permeable sheathing.”
What are the Types of Vapor Barrier?
Vapor retarders are typically available as membranes or coatings, according to the Department of Energy. Membranes are generally thin, flexible materials but also include thicker sheet materials sometimes called structural vapor retarders. Materials like rigid foam insulation, reinforced plastics, aluminum, and stainless steel are relatively resistant to water vapor diffusion. These types of vapor retarders are usually mechanically fastened and sealed at the joints.
Thinner membrane types come in rolls or as integral parts of building materials. Common examples include polyethylene sheeting and aluminum- or paper-faced fiberglass roll insulation. Another type is foil-backed wallboard. Most paint-like coatings also retard vapor diffusion.
There are also what’s called water resistive barriers, which attempt to accomplish water vapor diffusion and air movement control with one material. This is said to be best in southern climates, where keeping humid outdoor air from entering the building cavities is critical during the cooling season.
In many cases, such water resistive barriers consist of one or a combination of polyethylene plastic sheets, builder’s foil, foam board insulation, and other exterior sheathings.
Vapor Barriers and Retarders in Action
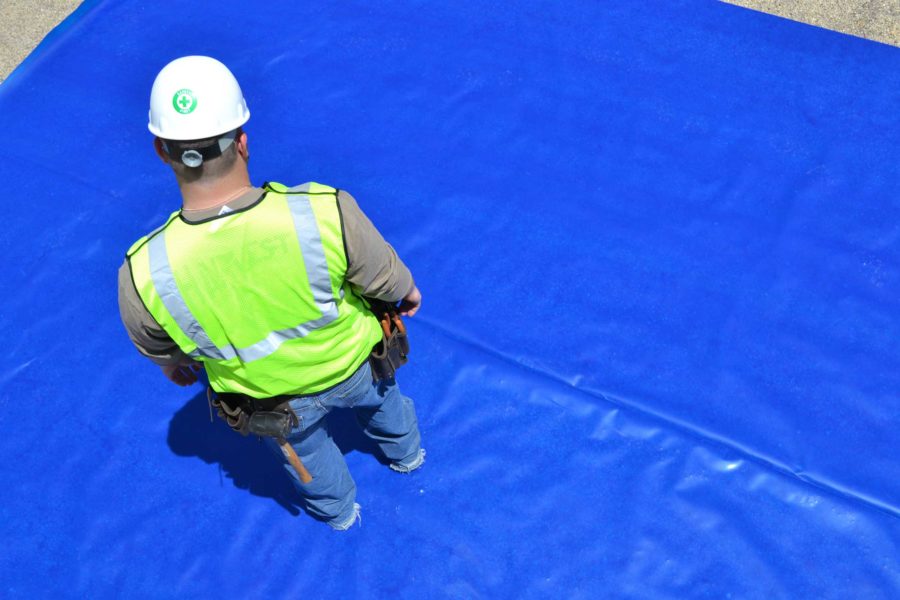
Updates to the International Residential Code (IRC) increase the required performance specs for under-slab vapor retarders. Photo courtesy of ISI Building Products
You can properly protect your investment from the ground up with a high-performance under-slab vapor barrier system.
“Below slab water vapor remediation after-the-fact is a complicated and costly fix,” writes Dario Lamberti in a previous article for gb&dPRO. “The small, upfront savings when choosing a minimal protection moisture barrier can be appealing, but the result often turns into a long-term problem.”
Lamberti points to how proper planning and design averts potential headaches and expenses. He says there are a few key points to consider before choosing a moisture barrier.
Choosing a Below Slab Vapor Barrier
Lamberti says advancements in plastic film manufacturing means higher performing materials are becoming the norm. “It is important to look for moisture barrier products manufactured from 100% virgin resin,” he says. “They are also typically manufactured in a multi-layer or co-extruded fashion. Co-extruded films are in high demand as they incorporate the best properties of different resins and link them all together into one film structure.”
High-performance vapor retarders and barriers are commonly available in 8-mil, 10-mil, 15-mil, and 20-mil thicknesses, but increased thickness does not always translate into better performance, Lamberti emphasizes. “Avoid single extruded products made from recycled content. For example, a 10-mil single layer extruded film made from recycled content will not carry near the performance of a thinner 8-mil co-extruded film manufactured from virgin resin. When evaluating vapor retarder and barrier products, it is key to make sure they are made from virgin resin and are co-extruded films.”
The Future of Vapor Barriers
A new change in the 2021 International Residential Code (IRC) requires better performing vapor barriers under the concrete slabs, Lamberti says. He says the change means better protection against moisture-related flooring failures, healthier indoor air quality, and increased structural longevity.
Although concrete is long-lasting and durable, it’s also porous. “Unprotected slabs without the proper moisture barrier can compromise the home’s interior by allowing pathways for water vapor and soil gas to travel through concrete,” Lamberti told gb&d previously. “Water vapor migration can cause flooring failures, high relative humidity, mold, mildew, and degradation of the concrete slab and its components. Soil gasses like radon and methane can also readily move from the soil to the indoor environment—negatively affecting occupant health and safety.”
Previous residential building code required a 6-mil vapor retarder to be used under concrete slabs. The 2021 IRC requires a 10-mil vapor retarder, conforming to the industry recognized ASTM E 1745 Class A standard for under-slab vapor retarders.
What are the Classes of Vapor Barrier?
There are three classes of water vapor retarders (or vapor barriers).
Class 1:
Glass
Sheet metal
Polyethylene sheet
Rubber membrane
Class 2:
Unfaced expanded or extruded polystyrene
30 pound asphalt coated paper
Plywood
Bitumen coated kraft paper
Class 3:
Gypsum board
Fiberglass insulation (unfaced)
Cellulose insulation
Board lumber
Concrete block
Brick
15-pound asphalt coated paper
House wrap
ASTM E 1745 classifies materials as A, B, or C based on the product’s puncture resistance, tensile strength, and water vapor permeance. Lamberti says Class A vapor retarders and barriers carry the highest puncture resistance and tensile strength, with Class C being on the lower end of the scale.
“The primary reason the new code specifies a Class A vapor retarder is to ensure the integrity of the membrane during installation,” Lamberti says. “To provide the highest level of protection, a vapor retarder should be continuous (without gaps or tears). Class A vapor retarders provide robust protection against degradation from construction foot traffic prior to the pour.”
Lamberti also stresses the importance of understanding the difference between a vapor retarder and a vapor barrier. He says the industry recognizes a vapor retarder as having a water vapor permeance rating between 0.1 perms and greater than 0.01 perms. Vapor barrier materials are considered to have a water vapor permeance rating below 0.01 perms. “The lower the water vapor permeance, the higher the quality of the vapor retarder,” he says.