Story at a glance:
- Delta Millworks’ wood is stable and sustainable.
- All wood needs to be acclimatized to its environment.
- Proper installation is as important as high-quality wood.
Delta Millworks knows wood and then some. Founded in 1985, the Austin, Texas–based company has expanded greatly over the years to become an internationally respected purveyor of high-quality wood for everything from exterior and interior cladding and ceilings to flooring and decking.
From thermally modified and acetylated woods to those treated with an innovative Japanese charring process called shou-sugi-ban, the company’s products consistently set the industry standard for stability and sustainability.
Delta CEO Robbie Davis, who took over the company from his founding father Bob, is closely involved with every aspect of operations— from where Delta sources wood to how that wood is tested and treated to final installation and proper maintenance. He recently shared some of his expert insights.
Exterior Cladding
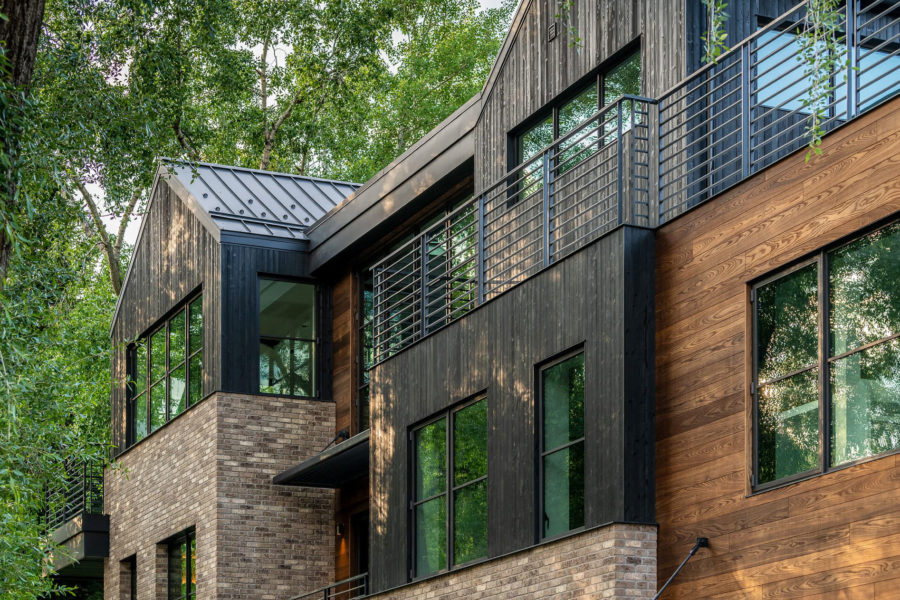
Photo courtesy of Delta Millworks
First and foremost, Davis says, it’s important to use woods that are “stable.” That means they maintain their straightness and flatness when there are changes in temperature, humidity, and exposure to the elements (sun, rain, hail, etc.).
The dryness of high altitudes can be detrimental as well. Protecting those woods with a high-performance finish is also vital. “You can have the most stable wood on earth,” Davis says, “but if the finish fades in 12 months and you have to spend a good chunk of money to bring it back to new, that’s a quality issue. Whether it’s oil, water, or water-borne, you need a finish that penetrates the wood and doesn’t peel or flake off. It should also have good UV blocking properties. At the end of the day, ultraviolet light is harsher on wood than any other outdoor element.”
Davis also notes that Delta’s exterior woods—including its specially modified products like Accoya and Kebony, its shou-sugi-ban line that involves a Japanese charring process, cedar, and its newest thermally modified Mojave collection (available in oak, hemlock, radiata, and Ponderosa pine)—are far superior in quality to those typically sold at home centers. You’ll spend a bit more upfront, Davis says, but it will save you significant money, time, and headaches down the line.
Interior Paneling
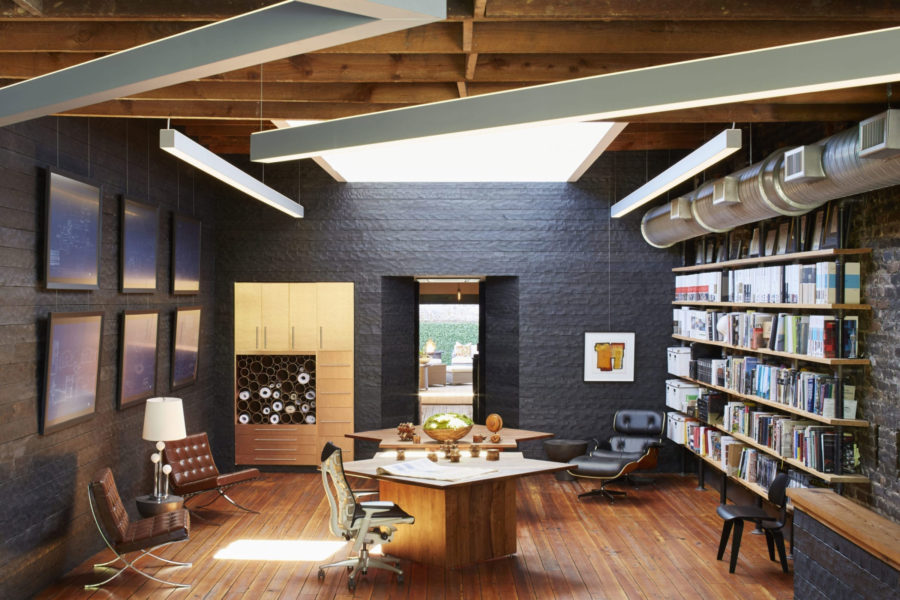
The Cevian Design Lab chose Accoya interior paneling. Photo courtesy of Delta Millworks
When it comes to interior applications, Davis says, there’s more leeway in the types of woods that can be used—including more affordable options like cypress or yellow pine. Regardless of the type, however, every wood product should be kiln-dried to enhance its stability and longevity. “Every type of wood is hygroscopic, meaning it absorbs and releases moisture based on its environment,” Davis says.
That’s why all wood should also be pre-acclimated prior to installation. If a home is usually air-conditioned or its windows are often open, air-stack the wood in those conditions and monitor its moisture content, Davis says. “You can use the highest quality wood in the world, but if it’s not acclimated, it’s not going to perform like it should.”
Flooring
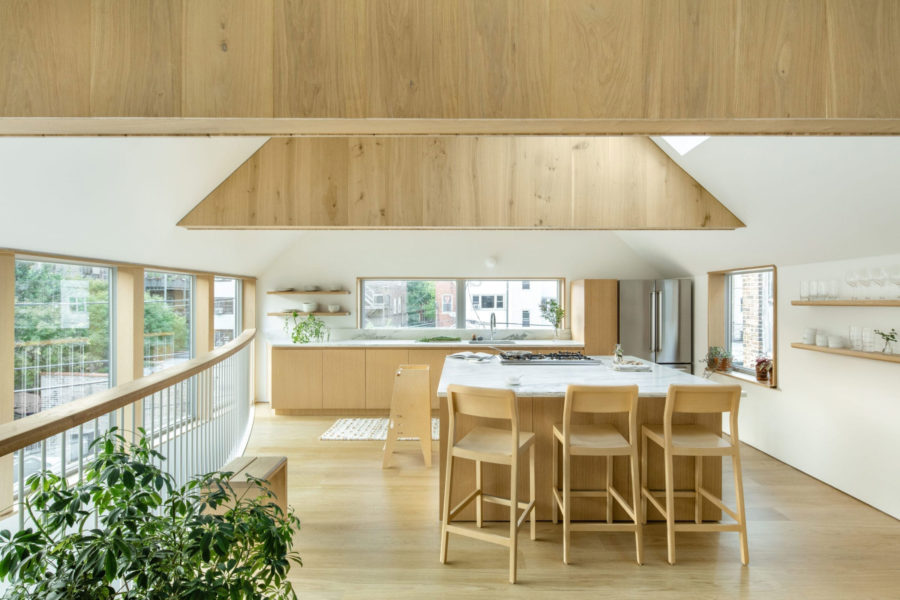
The Ardmore House in Chicago. Photo courtesy of Delta Millworks
Wood floors take a lot of abuse from shoes, toys, pets, furniture, and other things—including radiant heat, which draws out a lot of moisture. So in addition to stability, you want a dense wood like domestic or European oak—properly installed, of course. “We can’t stress that enough,” Davis says. “All woods will expand and contract at least a bit, and how quality wood performs is dependent on quality installation—even something like our Accoya product, which has a 50-year warranty.”
Any time a floor fails structurally, he adds, it’s a big undertaking to replace the materials. Many of the issues we deal with from a quality or structural perspective involve incorrect installation, so we really try to stay on top of that to the extent possible by making sure our clients are educated about stuff like acclimatization, using the correct fasteners, and sealing cut-ins on the exterior siding so water isn’t absorbed through the ends of the boards.
Decking
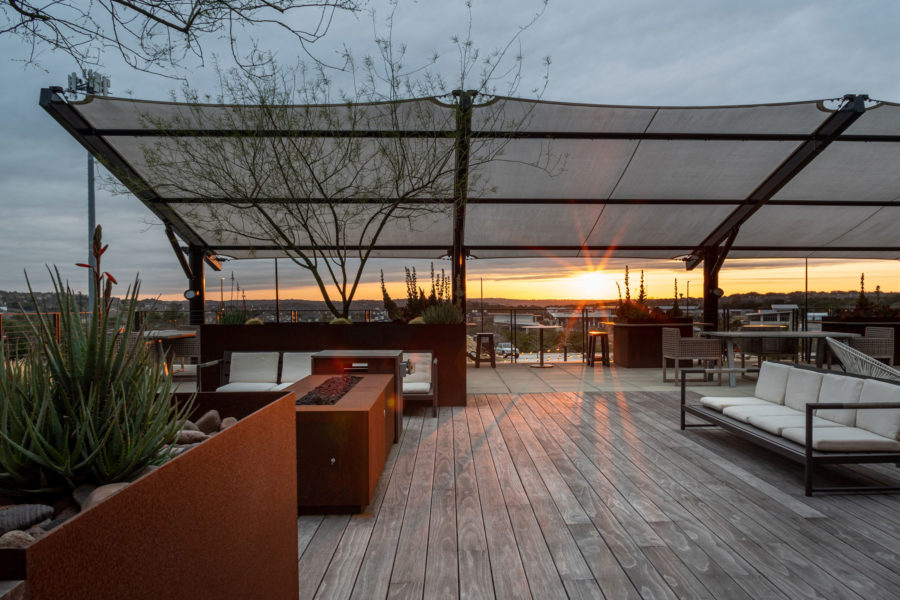
Delta Millworks’ Kebony is used outside at the Yeti headquarters. Photo by Fine Focus Photography
“You can stain or put a coating on decking, but a lot of our clients prefer to leave the wood unfinished and let it gray out naturally,” Davis says.
And because horizontal decks are far more exposed to the elements than exterior siding, he explains, they age twice as fast. As a result, Delta’s top go-to woods are Kebony, Accoya, thermally modified oak, and thermally modified radiata pine. These sustainable products typically don’t need to be treated with anything to maintain their structural performance during an extended life cycle, which gives clients peace of mind, saves them money in the long run, and allows them to show off the naturally aged wood.
Soffits
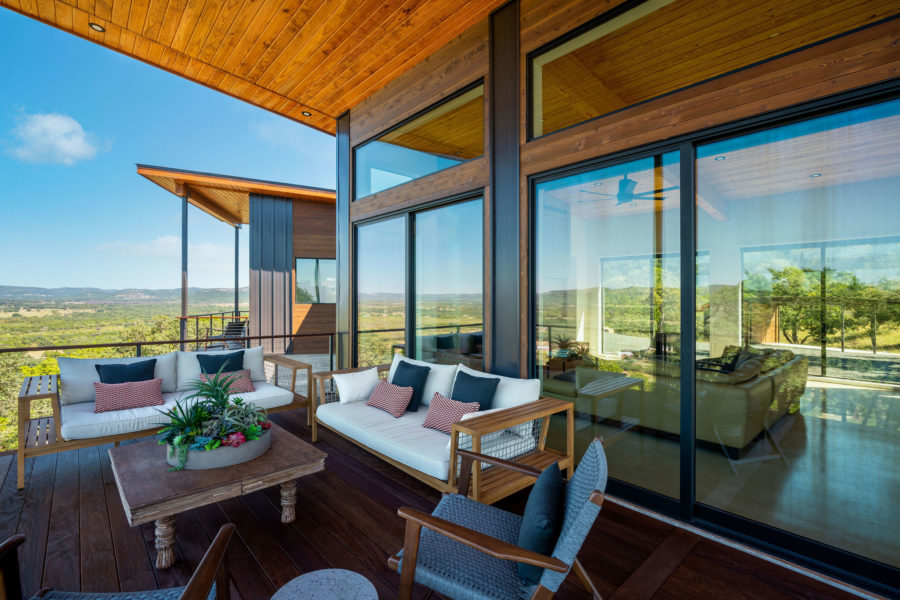
Soffits seen on the Frio Residence in Leakey, Texas. Photo courtesy of Delta Millworks
Because they’re not walked on or exposed to harsh weather, wood options abound when it comes to soffits. Whichever wood you choose, though, should be kiln-dried and acclimated to its environment. And while soffits don’t have to match interior ceiling wood, Davis says, that’s certainly possible if the ceiling wood is also appropriate for exteriors.
“The basic rule of thumb is if it can be used for exterior, it can always be used for interior. The trend these days is interior ceilings that lead out to either an exterior ceiling or a soffit, and nine times out of 10 we’re using the same wood—usually vertical-grain hemlock.” Not only is hemlock clean, consistent, and beautiful, Davis says, it’s stable and high-performance enough for exterior soffits that aren’t nearly as exposed to the elements as siding.
Other Delta Advantages
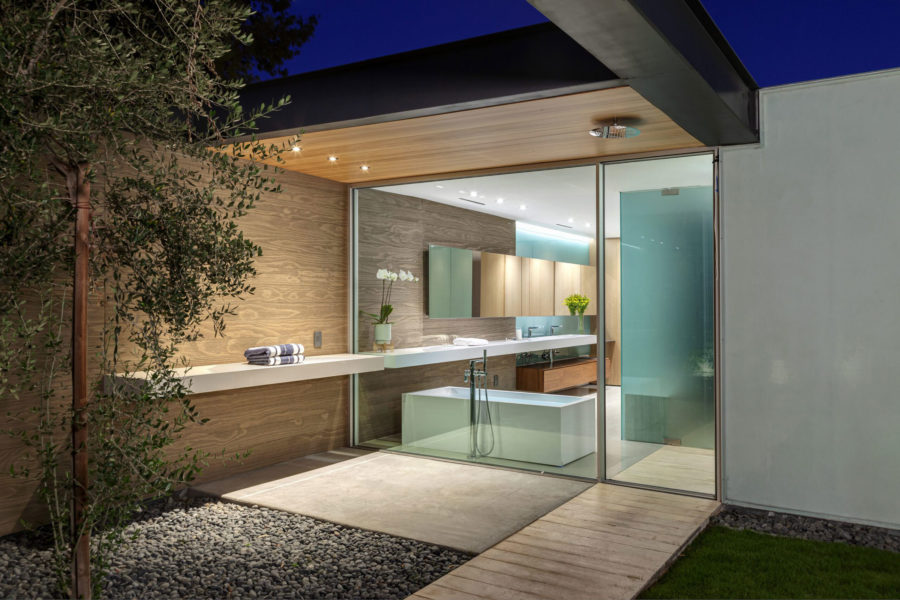
Accoya, seen here at a residence in Joshua Tree, has a 50-year warranty. Photo courtesy of Delta Millworks
All of Delta’s wood is sustainably sourced, and a good portion of its domestic product comes from tree farms in British Columbia. That means there’s no clear-cutting involved, less long-distance shipping, and a smaller carbon footprint than those produced by many other wood harvesters in America and abroad.
Testing, too, is a vitally important part of the Delta process. Each product is subjected to artificially emulated extremes—high up in the dry mountains of Colorado, for example, or near the humid coast of California—with an accelerated weathering machine to make sure treated wood and coatings can easily endure the harshest real-world conditions. That way, there are no surprises once it’s installed, and clients can be assured of its future performance.