Story at a glance:
- Insulated concrete forms (ICFs) are driving a sustainable path to net zero energy.
- Less than 1% of all commercial buildings are net zero-verified.
- Beyond energy efficiency, ICF comes with a host of other building benefits.
When it comes to commercial buildings, net zero energy is far from the norm. In fact less than 1% of all commercial buildings are net zero–verified, according to the World Green Building Council.
The good news is that number is growing as much as 50% every two years. And though the path to net zero can vary, one building method sets the standard for energy-efficient commercial spaces that’s almost too good to be true—insulated concrete forms.
Insulated Concrete Forms and Net Zero
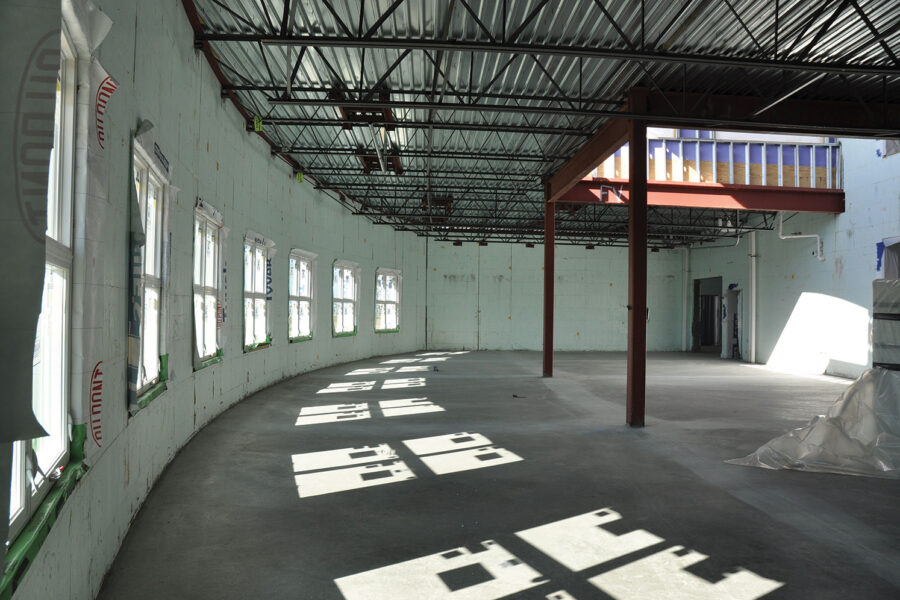
Richardsville Elementary School, built with Nudura ICFs, was the first net zero school in the US. Photo courtesy of Tremco CPG Inc.
Insulated concrete forms, or ICFs, are a forming system that remains in the structure of a building after the concrete has cured. The solid mass of the monolithic concrete, layered between two continuous panels of EPS foam, significantly reduces the flow of heat through the wall, minimizing thermal bridging and creating an energy-efficient building envelope.
Although insulation is not the sole contributor to net zero buildings, together with other green building strategies, ICFs work toward conserving energy and achieving net zero and, in some cases, even net-positive buildings.
“It’s much easier to build a net zero job or system with ICF,” says Cameron Ware, western division key account executive for Tremco CPG Inc.’s Nudura® ICF brand.
Ware has worked with ICFs for almost 20 years and has spent the past five training architects, engineers, and installation crews on Nudura ICFs, part of the Tremco CPG family of brands. To date he’s been involved with the construction of several million square feet of ICF walls, including one of the first net zero schools in the US—an achievement many architects thought was impossible.
Over his career Ware has seen many approaches to net zero. What he’s learned is that to build a successful net zero commercial building, there is a correct order of sustainable, energy-efficient strategies to employ. “I call it the hierarchy of green. If you get it in the wrong order, you screw it all up,” he says.
Ware’s path to net zero begins with the building envelope, and that’s where ICF comes in. “You start with the envelope to reduce air infiltration. Air infiltration is a huge piece of net zero, and ICF virtually eliminates it completely,” he says. “Whereas in regular construction, there’s an awful lot of caulking required to make wood or steel have zero air infiltration.”
With a net zero structure built with ICF architects have an easier path forward to achieve their energy goals.
The Benefits of ICF Beyond Energy Efficiency
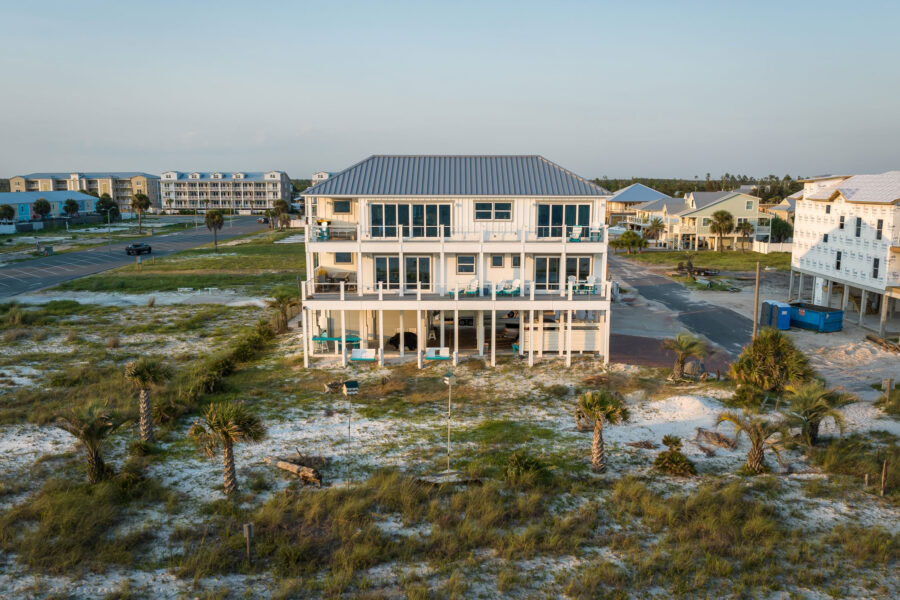
This home is one of the few houses left standing after Hurricane Michael. It was built using ICFs. Photo courtesy of Tremco CPG Inc.
Other than helping architects and engineers achieve net zero, ICFs come with advantages that aid both buildings and their construction.
1. Durability
A key tenet of green building is developing structures that last. Using ICF can help ensure that a building will remain standing for centuries.
Not only does concrete stabilize and strengthen a building, but ICFs also offer maximum safety with a fire protection rating of up to four hours and the ability to withstand winds up to 250 mph, moving far beyond the strict 195 mph standard of Miami-Dade certification.
In 2018, Category 5 Hurricane Michael destroyed many buildings as it struck the Florida panhandle. The sole home standing on the coast of Mexico Beach was built with ICF to endure the extreme forces from the storm.
2. Sustainability
When it comes to sustainability, the insulation value of ICF walls lessens the heating and cooling load during extremely hot or cold periods.
“When you walk into a cave, for example, if it’s really cold out, it’ll feel warm in the cave. If it’s really hot out, it’ll feel cool in the cave. Earth is radiating the average temperature over the last month or so in that cave. You’re feeling the energy coming from the earth that feels cool or warm, and it’s stable. You get that same effect with ICF,” Ware says.
Because of the amount of concrete in an ICF building, the building’s mass is larger. “The building has so much mass, it takes a while for it to know that it’s gotten colder or warmer outside,” he says. “This experience causes a reduction in peak loads for AC or geothermal equipment, so you can buy less equipment to satisfy that demand for that building.”
3. Better Sound Attenuation
Every building has a sound transmission class (STC) rating that measures a building’s walls, ceilings, and windows based on their ability to reduce sound coming through. The higher the STC rating, the less noise coming through.
“Your typical house is in the 40s or so, or even a little lower, which means you’re going to hear the guy across the street mowing his yard. You’re going to hear kids playing outside,” Ware says. “An ICF house has an STC of over 50, which means you can’t hear through it very well.” This sound dampening benefit results in a much quieter interior, free from outside distractions.
4. Speed of Construction
ICF construction could be categorized as masonry or stone construction, but it moves much faster. “Masonry work is very, very hard work. It’s easier and faster production-wise to put up ICF because the product only weighs about one pound per square foot, compared to 30 to 40 pounds per rock or CMU.”
On top of that ICF can be installed in any weather condition since it won’t absorb moisture like wood. Crews can work through the winter to minimize construction downtime and expedite when interior work can begin, and with it, building occupancy.
5. Cost Savings
From the speed of construction to the energy efficiency in the final structure ICFs bring big cost savings at every stage of building.
The lightweight nature of ICF eliminates the need for cranes and other equipment for installation, plus less freight cost and easier shipping, especially with ICF systems that can be folded and shipped flat. Greater insulation means less pressure on a building’s heating, cooling, and other mechanical systems, reducing long-term operational costs and the need for maintenance. Not to mention less energy consumption overall will lower a building’s energy bill.
When ICFs are used alongside other green building strategies to achieve net zero, building owners may be able to make money from their utility companies for the additional energy the structure produces. The first net zero school Ware worked on in tornado-prone Kentucky, for instance, earns more than $45,000 a year from producing excess solar power.
Although 100% net zero-verified buildings may seem like a scene from a distant future, ICF technology is an easier, more sustainable, and cost-effective way to bring that dream to reality. All it takes are architects, engineers, and building owners who are ready to take it on to lead the industry to a better, greener future.