Story at a glance:
- Hurricane Andrew in 1992 caused South Florida to rethink its building code.
- Impact glass needs to endure flying debris in tough coastal environments.
- Flying debris and sudden shifts in pressurization cause significant damage to homes during hurricanes.
In 1992, five years after Mike Wothe began working in the glass industry, Hurricane Andrew obliterated South Florida. The Category 5 superstorm caused 65 fatalities in the US and the Bahamas and did more than $27 billion in damage. Back then so-called “impact glass” in windows and doors wasn’t part of the state’s building code. That changed in early 2002, when the Florida Building Code mandated it for significant remodels and new construction in the state’s most hurricane-prone areas. Other states along the Atlantic and Gulf coasts have adopted similar measures.
Wothe and PGT Innovations (PGTI), where Wothe is executive vice president of operations, have long been in the business of improving impact glass technically and expanding its ubiquity geographically. He recently offered some expert insights on why it matters, how it’s evolving, and where it’s most in demand.
What is impact glass, and how is it evolving?
- Photo courtesy of PGT Innovations
- Photo courtesy of Corning Incorporated
Impact glass is more than just “laminated glass” like you’d find in a car windshield. What makes a good windshield, doesn’t make a good hurricane window. True impact glass is built to withstand hurricane-force winds of 110 miles per hour or greater as well as flying debris and dramatic pressure shifts. We have tests—one involving a 9-pound two-by-four shot out of a canon at 50 feet per second—that emulate these strong storms. Over the years it’s evolved around strength first and then durability—the ability to last in a tough coastal environment.
The newest innovations in impact glass from PGT Innovations, achieved in collaboration with Corning Incorporated, are around weight. As the demand for larger windows and doors with more glass increases, the weight of those products increases with it. This creates significant challenges for window and door manufacturers to build the products and load them on delivery trucks, as well as challenges for building professionals to install and homeowners to operate the products. With the new thinner impact-resistant glass units from PGT Innovations and Corning, up to 45% of the weight is removed. This means it’s easier for manufacturing employees to maneuver the products while they’re being built, easier for building professionals to install, and easier for homeowners to open and close their windows and doors.
Why does impact glass matter?
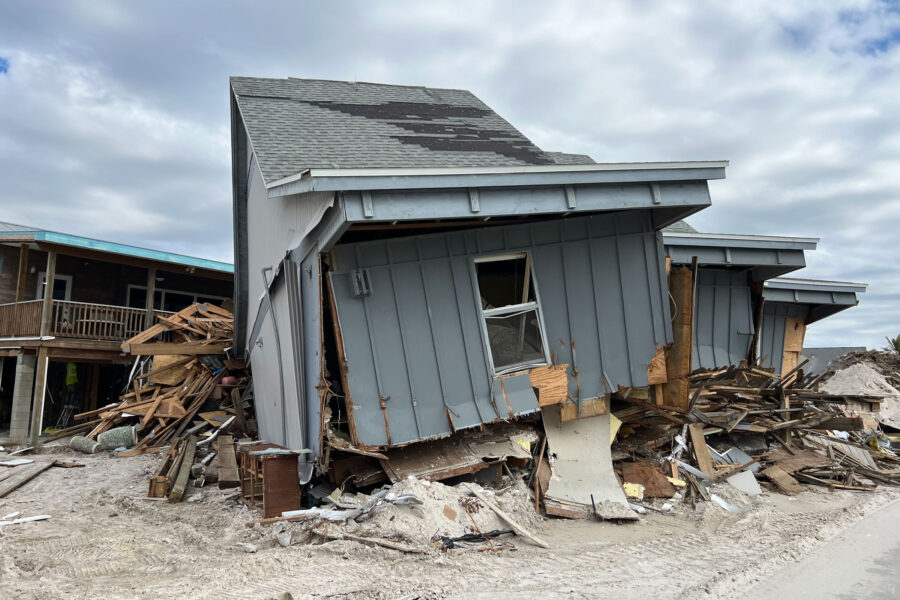
Photo courtesy of PGT Innovations
For houses with impact-resistant glass windows and doors, during storms with high-velocity winds, you’re keeping the outside out and the inside in. You’re safe inside your structure. In 1992 and before, Florida was the cheapest window market in the country, with non-thermally broken, aluminum-framed, single-pane windows. No energy efficiency, no insulation, no lamination. There was also no protection.
When a hurricane hits a house, there are positive and negative air pressures pushing and pulling on every “opening” of your home—windows, doors, and garage doors. If the glass in a window or door breaks, or if an opening is somehow otherwise breached, winds can rush into a home, pressurize the inside, and literally lift the roof off and blow the walls out. So in addition to flying debris damaging a home during a storm, pressurization of the home can blow it apart. Impact glass is a vital component of a whole-system approach to home hardening.
Where is the highest demand?
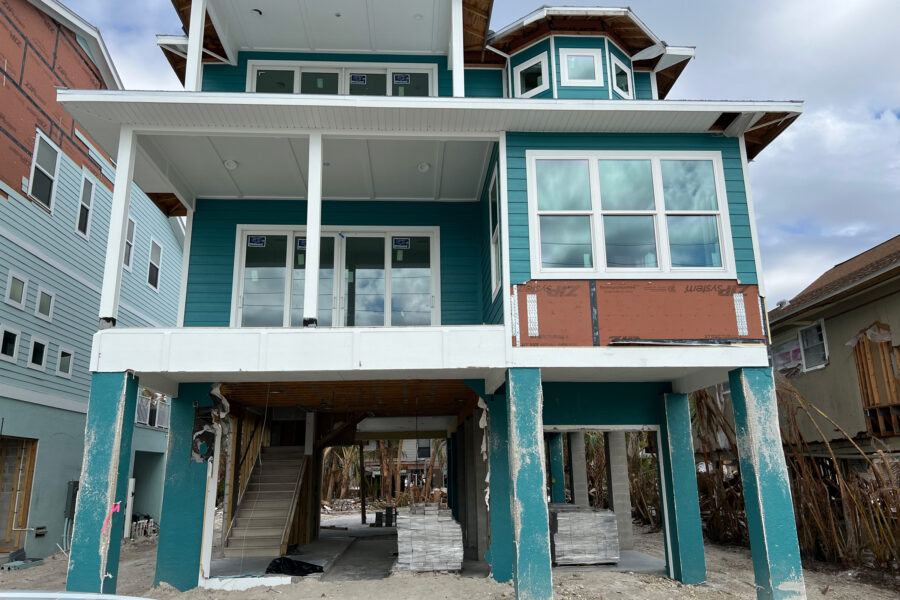
Photo courtesy of PGT Innovations
Hurricane-rated windows are primarily used in hurricane zones and coastal zones. The product also has value in sound control and residential security. As for residential versus commercial projects, they both need to meet the code, so there’s plenty of work doing retrofits for both. As storms hit land and people realize they need more protection, Florida continues to drive conversion as it attracts a population that has the money to upgrade and wants safer homes.