Story at a glance:
- CannonDesign turned to Kingspan for its QuadCore Optimo as part of an emergency room renovation project in Cincinnati.
- Planet Passionate is a 10-year sustainable program from Kingspan, focused on climate change, circularity, and protecting the natural world.
Sustainability has long been the focus of Kingspan Insulated Panels, a leading manufacturer of insulated metal panels and innovative facade solutions. “Given that we are an insulation manufacturer, energy efficiency has always been a driver for us,” says Brent Trenga, director of sustainability for Kingspan Insulated Panels, North America.
Kingspan Insulated Panels is part of the larger Kingspan global business, which also includes Insulation; Data + Flooring; Light, Air + Water; and Roofing + Waterproofing. As part of Kingspan’s Planet Passionate sustainability initiative, the building products producer aims to achieve net-zero carbon in its manufacturing operations and is committed to a 90% reduction in scope 1 and 2 greenhouse gas (GHG) emissions by 2030. The program is a massive undertaking when considering the size of Kingspan, which operates across 80 countries with more than 22,500 employees.
The company reduced emissions of its Ireland headquarters by 40% in 2023 compared to the previous year. Kingspan’s forklift fleet is 40% electric, and last year the company invested nearly $62 million in research and development—to name just a few of the visible examples of its commitment to sustainability. “It’s about us leaving the people and planet a better place than we found it,” Trenga says.
A Growing Need
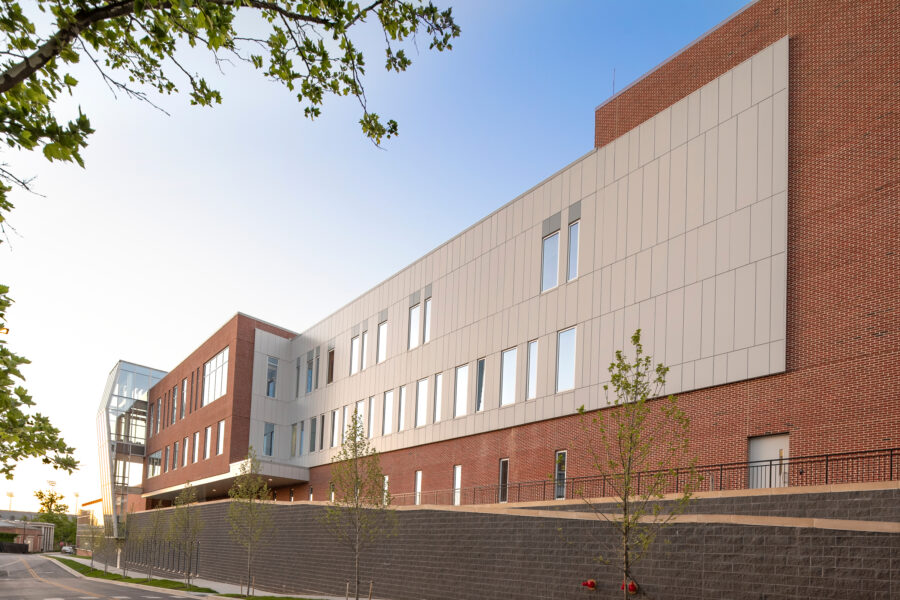
Jones-Hill House at the University of Maryland. Photo courtesy of Kingspan Insulated Panels
Trenga says infrastructure construction continues to drive sales at Kingspan, which is also a second generation family-run business. This includes massive data centers, automotive plants, and auto electric battery manufacturing facilities. Kingspan’s insulated panel customers include some of the biggest companies out there—like Tesla, Ford, General Motors, Google, and LG.
CannonDesign has worked with Kingspan on a number of projects, including data centers and industrial buildings. “Then we realized these systems can be used for all types of buildings,” says Eric Corey Freed, director of sustainability at CannonDesign.
The architecture firm with offices all over the US has also worked with Kingspan on institutional, commercial, health care, and university projects. “It’s a higher performing envelope and gives us a pathway toward net zero energy for a high-performance building,” Freed says.
What we are really building are 100-year buildings.
Insulated metal panels, or IMPs, helped a medical center renovation at the University of Cincinnati go more quickly when CannonDesign chose them as the building envelope for the expansion. The project was completed in December 2022. Quick installation of IMPs provided a weathertight envelope in reduced time, drying in the emergency room faster and allowing for inside finish work to begin sooner, according to Kingspan. “Creating a nice tight envelope—insulated metal panels give me an opportunity to do that,” Freed says.
In general he says working with clients like these—from Kingspan to the University of Cincinnati—is exciting. “We get to use work with the most amazing clients who are looking to solve emission problems in health care, education, and science.”
He says continued innovations in the industry have also improved with regard to the life cycle cost of buildings and more durable solutions, as most see the value of building projects that won’t soon be torn down. “What we are really building are 100-year buildings.” Kingspan’s IMPs offer another step toward building better, longer-lasting projects. And that’s important, considering about half of carbon emissions come from the design and construction of the building.
The Road to Sustainability
- Jones-Hill House at the University of Maryland. Photo courtesy of Kingspan Insulated Panels
- Jones-Hill House at the University of Maryland. Photo courtesy of Kingspan Insulated Panels
Kingspan’s Planet Passionate initiative means accelerating net zero emissions. The company formally set sustainability targets in 2011, achieved its initial net zero goals, and then released the Planet Passionate plan in 2020.
“We have made incredible progress against every target we have set,” Trenga says. “We knew it was a challenge, and we are excited about the challenge and the opportunity.”
Kingspan’s insulated panels continue to help the company achieve its Planet Passionate goals. Manufactured offsite, the panels are a single component providing cost savings and thermal value while being produced with high recycled content. Because they are constructed in a controlled environment, IMPs are produced with little waste. Ease of installation on the job site also cuts down on time and provides labor savings.
Trenga says both the foam and steel used in the panels are low carbon materials that can be taken back and recycled for end-of-life solutions. “The panels are manufactured with a target of zero waste heading to a landfill.”
When it comes to the building envelope, the panels provide the proper air, thermal, water, and vapor barriers for structures, Trenga says. IMPs are available as wall systems, roof systems, and cladding accessories and components. And Kingspan’s QuadCore® Technology offers one of the most thermally efficient insulation cores on the market. This next generation of self-blended hybrid insulation has cores available in a range of thickness widths, with superior fire protection, health and wellness certifications, and a 30-year thermal warranty. “We continue to improve the products we manufacture and bring to market,” Trenga says.
Kingspan’s BENCHMARK Architectural Wall Panels also provide superior thermal properties as well as offer up a wealth of aesthetic capabilities with more styles and colors for creative freedom. These architectural insulated wall panels are exterior wall panels with steel skins and feature an insulating foam core.
Kingspan has set the bar high with its own facilities, too. Ultimately they not only measure the performance and targets of their own products and operations but also what each product is made with, how materials are sourced, and what happens after production. Many of its plants use renewable power onsite, and every site has a “zero waste to landfill” goal. Trenga says they hold themselves accountable while continuing to push others in the industry. “It’s not just about construction products. It’s how everyone runs their business.”