Story at a glance:
- LinkedIn adds three new buildings and two new parking structures to their campus in Mountain View.
- Designed by STUDIOS Architecture, the project emphasizes the connection between indoor and outdoor spaces.
- This project is one of the first to use low-carbon concrete and is LEED Platinum–certified.
Arrive at Building One of LinkedIn’s Middlefield campus in Mountain View, California and you’ll be greeted by orange stairs. You can walk through the lobby and take them all the way up to the sixth floor, but if you don’t want to go inside, you can also take the outside stairs to the third floor terrace deck.
From the onset the team behind the project was interested in creating connections between indoor and outdoor spaces. “Early on we didn’t really have the ins and outs of everything, but we had this idea of creating a meaningful outdoor space and physically connecting them,” says Jeong Choi, a principal at STUDIOS Architecture.
To accentuate this they used orange blocks to represent the stairs in a physical model. As they communicated with city officials and others about the project, they also fell in love with the character of the stairs. “We talked about how nice it is to have features that differentiate the building rather than having random glass boxes everywhere.” It set the expectation for the design quality for the rest of the campus—and for the city as a whole.
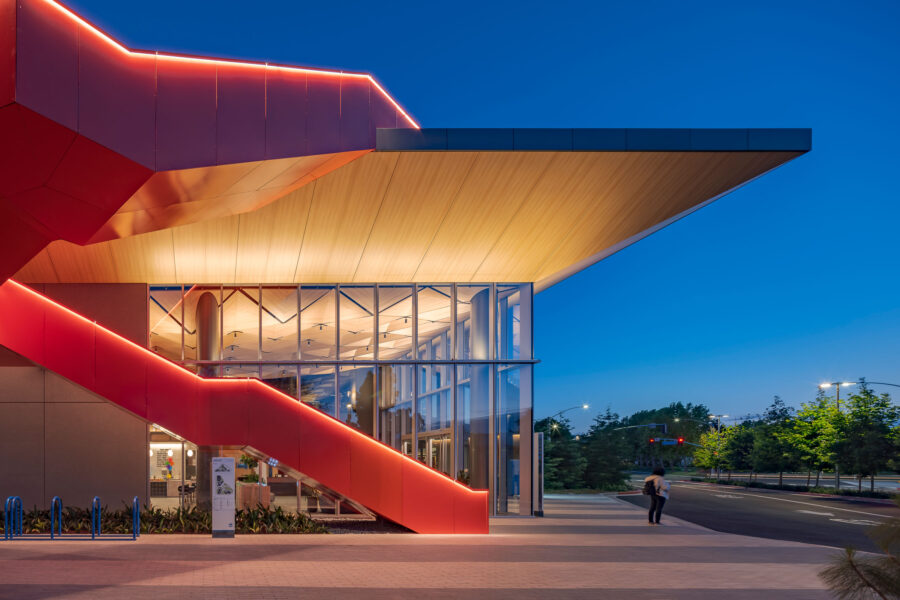
More than 20% of the total annual energy cost of the LinkedIn Middlefield project is offset by renewable site-generated energy when the building is running at its full capacity. Photo by Kyle Jeffers
STUDIOS has been working on various projects with LinkedIn since 2013. This recent long journey to find LinkedIn a new home included a land swap with Google and a global pandemic. LinkedIn inherited three 1980s-era buildings from Google. After some deliberation they decided to not tear them down, but that limited their buildable land drastically. “The limits gave us the opportunity to be more creative. It became our driving force to create a better performing building that blend well with the existing buildings,” Choi says.
In the end the team added three new buildings and two new parking structures to the three existing buildings to create a one-million-square-foot campus earning LEED Platinum certification.
Massing
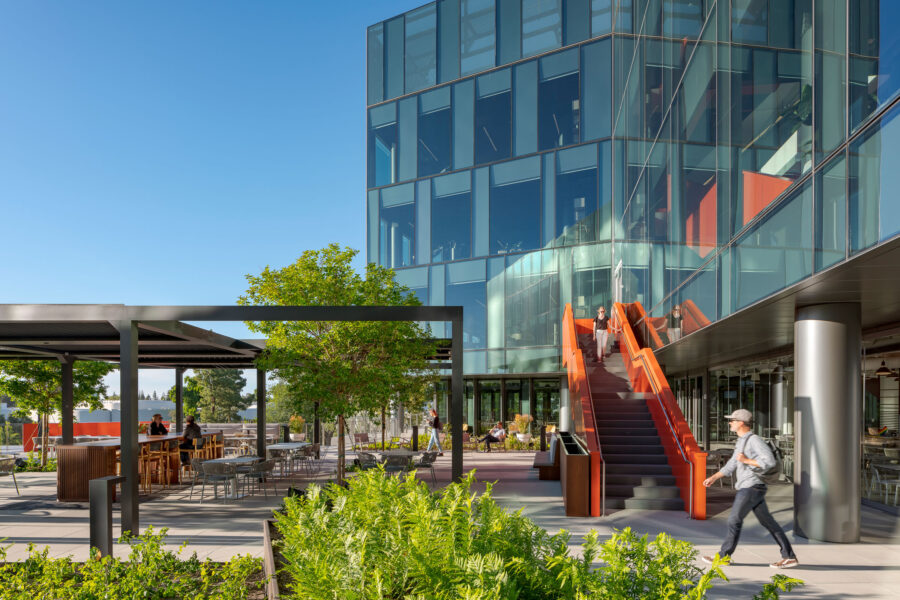
The third-floor terrace deck provides a secure outdoor space that maintains its connection with the ground level. People on the upper floors almost always have immediate access to outdoor decks designed to support many activities. Photo by Kyle Jeffers
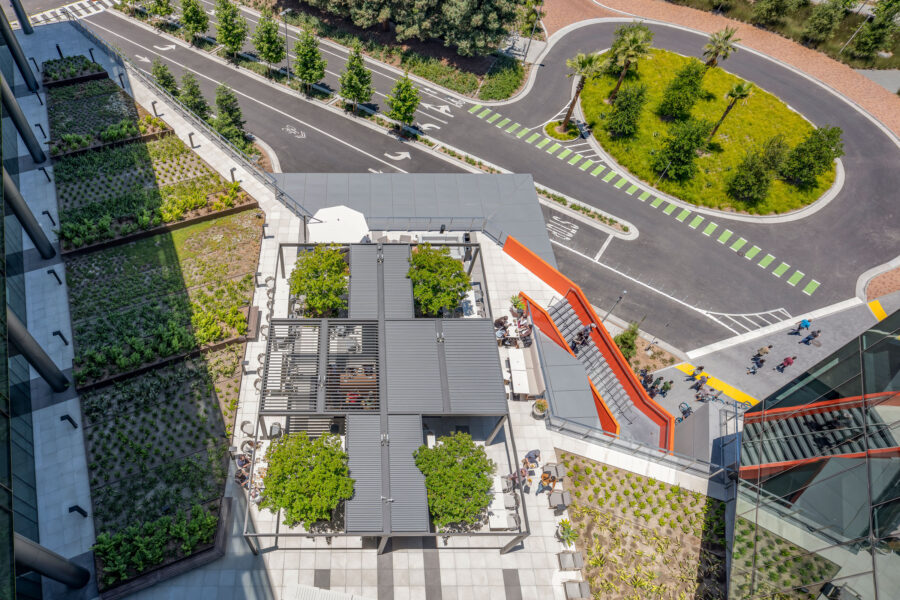
The new LinkedIn campus is surrounded by native tree canopies, while gardens across the site collect and treat stormwater. The landscaping and irrigation systems of the project reduced potable water consumption for irrigation by 90%. Photo by Kyle Jeffers
Working within the confines of the site, a typical 120-by-300-foot office building was out of the question. In contrast, the new buildings on the LinkedIn campus are as narrow as 65 feet. “As a result we worked with the structural engineer to be more efficient about the structural layout and without sacrificing usable space,” Choi says.
The design team optimized load paths to reduce the number of columns and create more open space. They also pushed the stairs outside and created the overhangs that ultimately became distinctive features of the project.
Performance
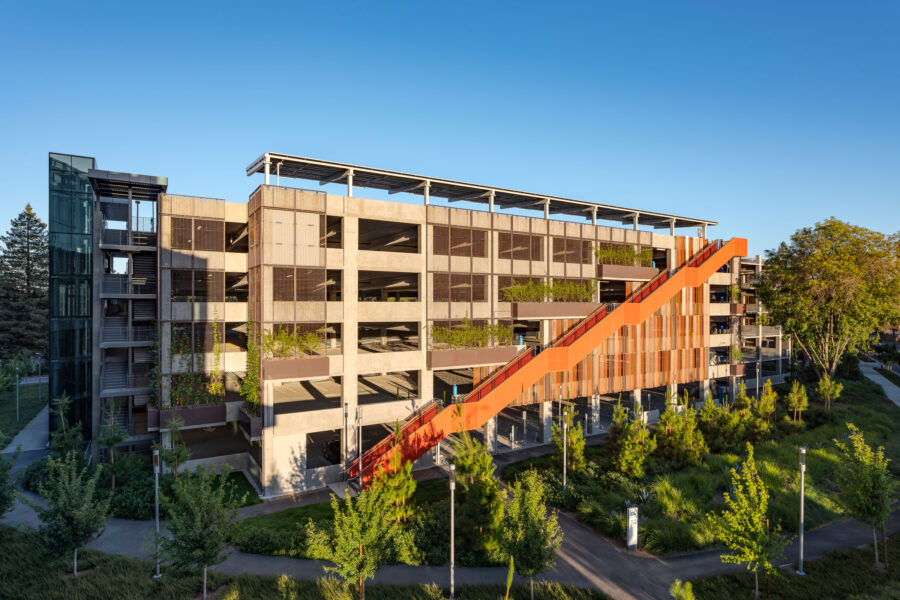
The parking structure features an illuminated orange staircase. Perforated metal panels are folded in three ways and have slightly different colors to mimic tree bark. Photo by Kyle Jeffers
“The design of the building is really performance-driven. By designing a better performing building, it uses less energy to maintain,” Choi says.
The long and narrow buildings can bring in a lot of natural light, but too much light can lead to heat gain. Putting the information into physical and energy models, the team fine-tuned ways to optimize performance. They tweaked angles and directions, experimented with ways of breaking into the massing, and calculated the ratio of vision glass to opaque glass for each face of the building. “Those kinds of percentages are very carefully designed based on analysis that we have in a computer model.”
Low-Carbon Concrete
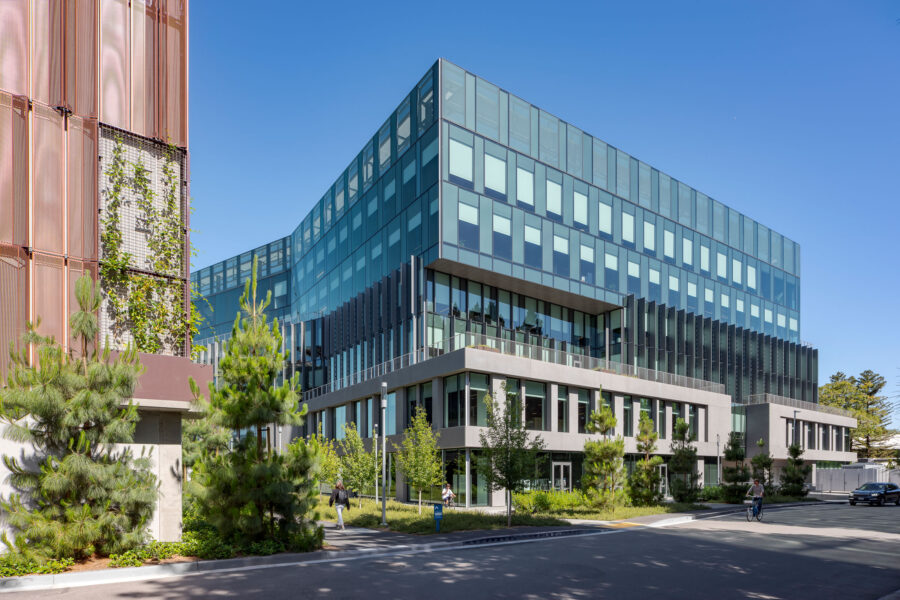
Precast concrete was chosen for the lower levels to create a sense of harmony with existing builds. Photo by Kyle Jeffers
When choosing building materials the design team wanted to ensure they wouldn’t alienate the existing buildings. As a result, they chose precast concrete.
Traditional concrete is often associated with high carbon emissions, and with LinkedIn’s goal to be carbon neutral by 2030, the team wanted to push the envelope for what could be done sustainably. Partnering with CarbonCure—a Canadian company working to reduce embodied carbon in concrete—the LinkedIn campus is one of the first developments to use a new technology. The project used two strategies to reduce carbon—replacing the cement in concrete with fly ash and slag (byproducts of coal and steel production, respectively), and using Carbon Cure technology that injects CO2 captured from large emitters into concrete during mixing. The combined strategy is estimated to reduce carbon emissions by 2,400 tons, a 30% reduction over business as usual, according to CarbonCure.
“Technology keeps evolving,” Choi says. The solution they thought was best five years ago is no longer the latest and greatest. Today the industry is working on carbon-negative concrete. “It’s a crazy concept. Building a new building could be more sustainable than not building.”
Project Details
Project: LinkedIn Middlefield
Architect: STUDIOS Architecture
Location: Mountain View, CA
Size: 700,000 square feet
Structural Engineer: Forell/Elsesser
Civil Engineer: BKF Engineers
General Contractor: Devcon Construction
Curtain Wall: Walters & Wolf
Landscape Architect: PWP Landscape Architecture
Certification: LEED Platinum
- The campus pavilion is a popular spot, hosting a coffee bar, happy hours, farmers’ markets, and other community events. At the center of the site STUDIOS and their client added a mass timber and steel structure to bring more energy to the space. Photo by Kyle Jeffers
- The folding geometry of the wood ceiling is utilized to conceal deep tree wells on the third-floor deck and also engineered to have micro-perforations that provide excellent noise reduction for the lobby. Photo by Kyle Jeffers
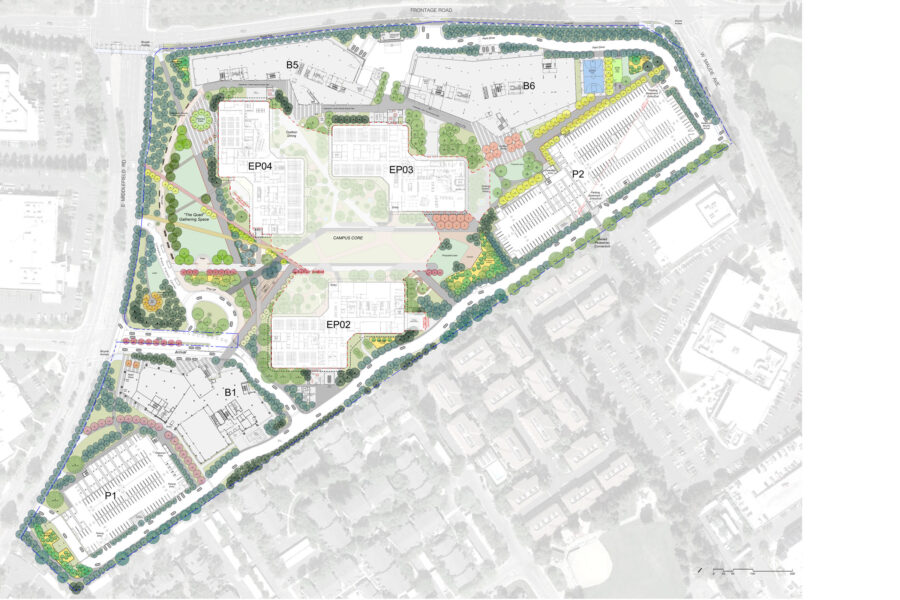
Full site plan. Image courtesy of STUDIOS Architecture