Story at a glance:
- Manufacturers are examining their raw material supply chains and transparency standards.
- Porcelain tile is especially well suited to engage with the Cradle to Cradle program.
- Porcelain tile is the preferred flooring choice when considering the impact in areas of IAQ, the circular economy, and climate change.
A fast-growing trend in sustainable and green design is the concept of material transparency, which is supported by a variety of certifications, declarations, or other standards. Recent events have shone a light on the health effects of the built space, and designers have responded by incorporating material content and potential occupant exposure into their design decisions.
Manufacturers have responded in varying degrees to the challenge by examining their raw material supply chains and obtaining a variety of transparency standards. Letās examine some of the more prominent transparency tools or standards as they relate to porcelain tile.
Health Product Declaration
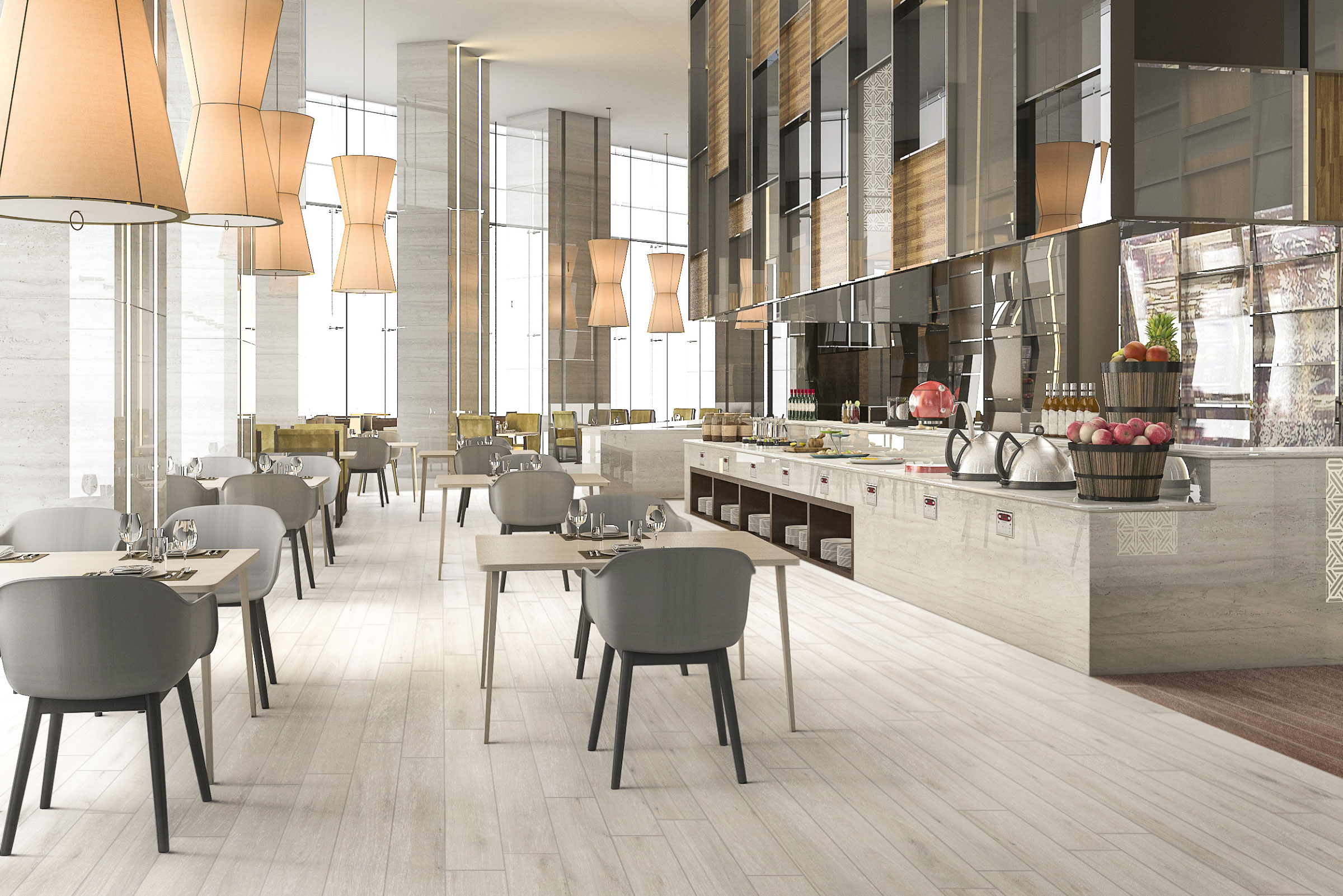
Native in Poplar and Teak. Photo courtesy of MILE®stone
Health Product Declarations (HPDs) provide a full disclosure of the potential chemicals of concern in products by comparing product ingredients to a set of priority āhazardā lists based on the GreenScreen for Safer Chemicals and additional lists from other government agencies.
There are two available levels of reportingā1,000 parts per million or 100 parts per million. HPDs are the output of the Health Product Declaration Collaborativeāa customer-led nonprofit member organization committed to the continuous improvement of the building industryās environmental and health performance through transparency and innovation. The HPD Collaborative created, supports, and advances the Health Product Declaration (HPD) Open Standard. It is freely available to all at hpd-collaborative.org.
To support HPDs and other transparency certifications, the Tile Council of North America (TCNA) developed the Material Ingredient Guide (MIG). It is a resource for ceramic tile, mortar, and grout manufacturers to use when providing the content and chemical makeup of their products or āmaterial ingredient transparency,ā using reporting formats like the HPD and other standards.
Material ingredient transparency is a fundamental step manufacturers take toward compliance with green and healthy building certification programs and developing brand trust with customers. The MIG provides information about the material ingredients used industry-wide by North American manufacturers references GreenScreen Assessments of the materials and provides insights into the industryās role in satisfying healthy building criteria. Use of the MIG in support of other transparency standards can contribute to green and healthy building optimization credits.
Environmental Product Declaration
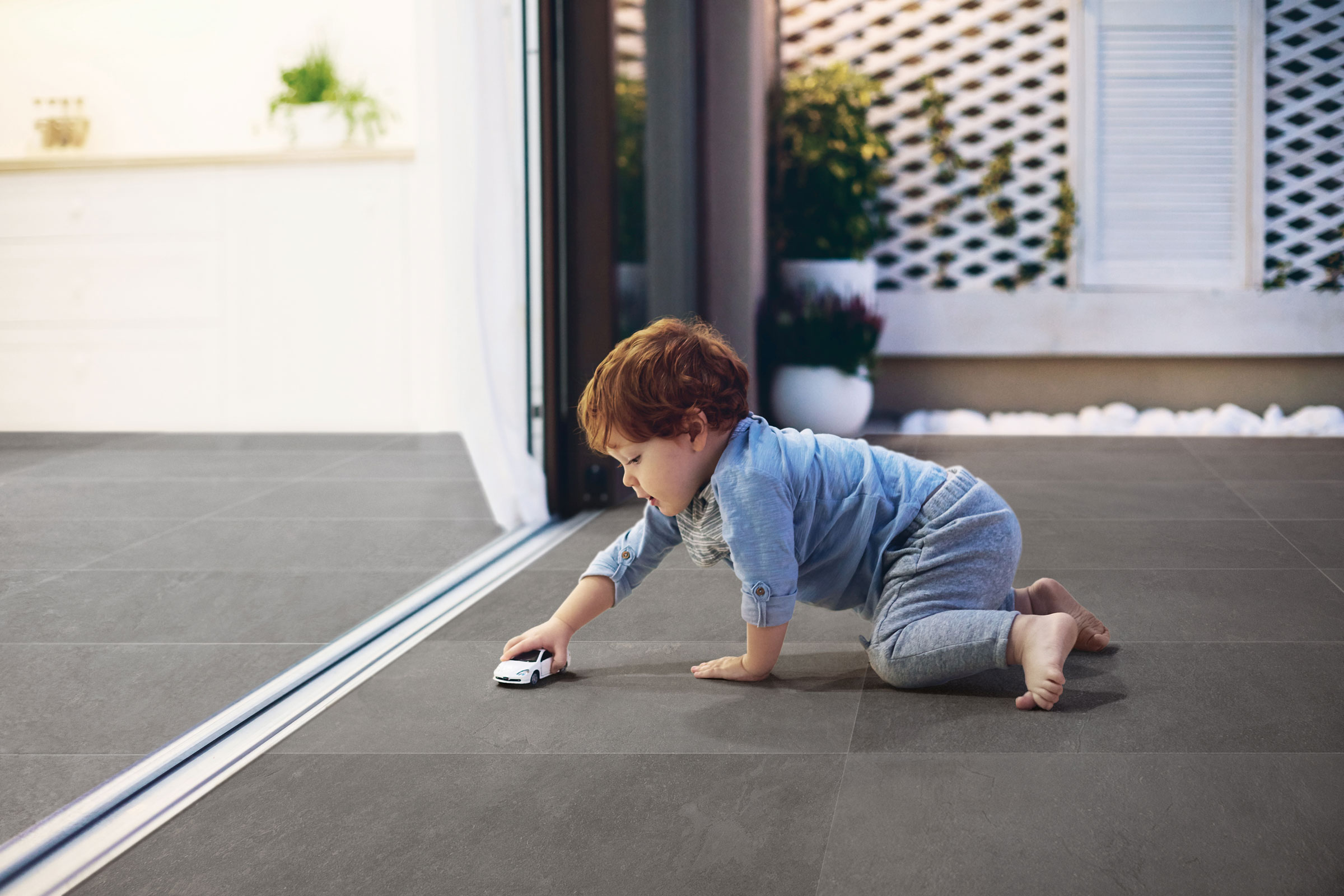
Lith in Heirloom. Photo courtesy of MILE®stone
An Environmental Product Declaration (EPD) is an independently verified and registered document that communicates transparent and comparable information about the life cycle environmental impact of products credibly. To ensure consistency across manufacturers, EPDs are prepared in accordance with ISO 14025-Environmental Labels and Declarations. Considerations in the EPD include greenhouse gas emissions, water quality effects, ozone depletion, rainwater acidification, and several others.
A Life Cycle Assessment (LCA) is a prerequisite for preparing an EPD. The LCA analyzes the environmental impact of the manufacture, use and end-of-life disposal of the product in question under the Product Category Rules (PCR). The PCR is a set of rules in place to ensure that LCAs and EPDs for similar materials perform to the same high standards.
A typical EPD for porcelain tile shows the lowest greenhouse gas contribution of any competing flooring type. This status is the culmination of several actions, including efficient use of energy in the manufacturing process, low energy demands for maintenance of the installed tile, and the exceptionally long life of porcelain tileāequal to the life of the building as per the PCR.
Declare Label and Red ListāFree
The International Living Future Institute (ILFI) is a non-governmental environmental organization committed to encouraging the transformation toward communities that are socially just, culturally rich, and ecologically restorative. ILFI is premised on the belief that providing a compelling vision for the future is a fundamental requirement for reconciling humanityās relationship with the natural world. It is a hub for many other forward-looking programs that support the transformation toward a living future.
Among these is the Declare labelāa platform to share and find healthy building products. Manufacturers voluntarily disclose product information on easy-to-read Declare labels, which are used by designers, real estate owners, and conscientious homeowners to specify products they can trust.
Declare can be likened to a nutrition label for building products. It is designed to help specifiers quickly identify products that meet their project requirements. Declare labels disclose all intentionally added ingredients and residuals at or above 100ppm (0.01%) present in the final product by weight. Each ingredient must be reported with a chemical name, CAS number, and percentage or range.
Manufacturers voluntarily disclose product information on these easy-to-read Declare labels that report all product ingredients and use a simple color-coded system to flag chemicals of concern. They provide further information on the productās final assembly locations, life expectancy, and end-of-life options. As for chemicals of concern, Declare screens a productās ingredients directly against their Red List, eliminating the requirement to manually vet chemicals. The LBC Red List contains the āworst in classā materials, chemicals, and elements known to pose serious risks to human health and the environment.
Recycled Content
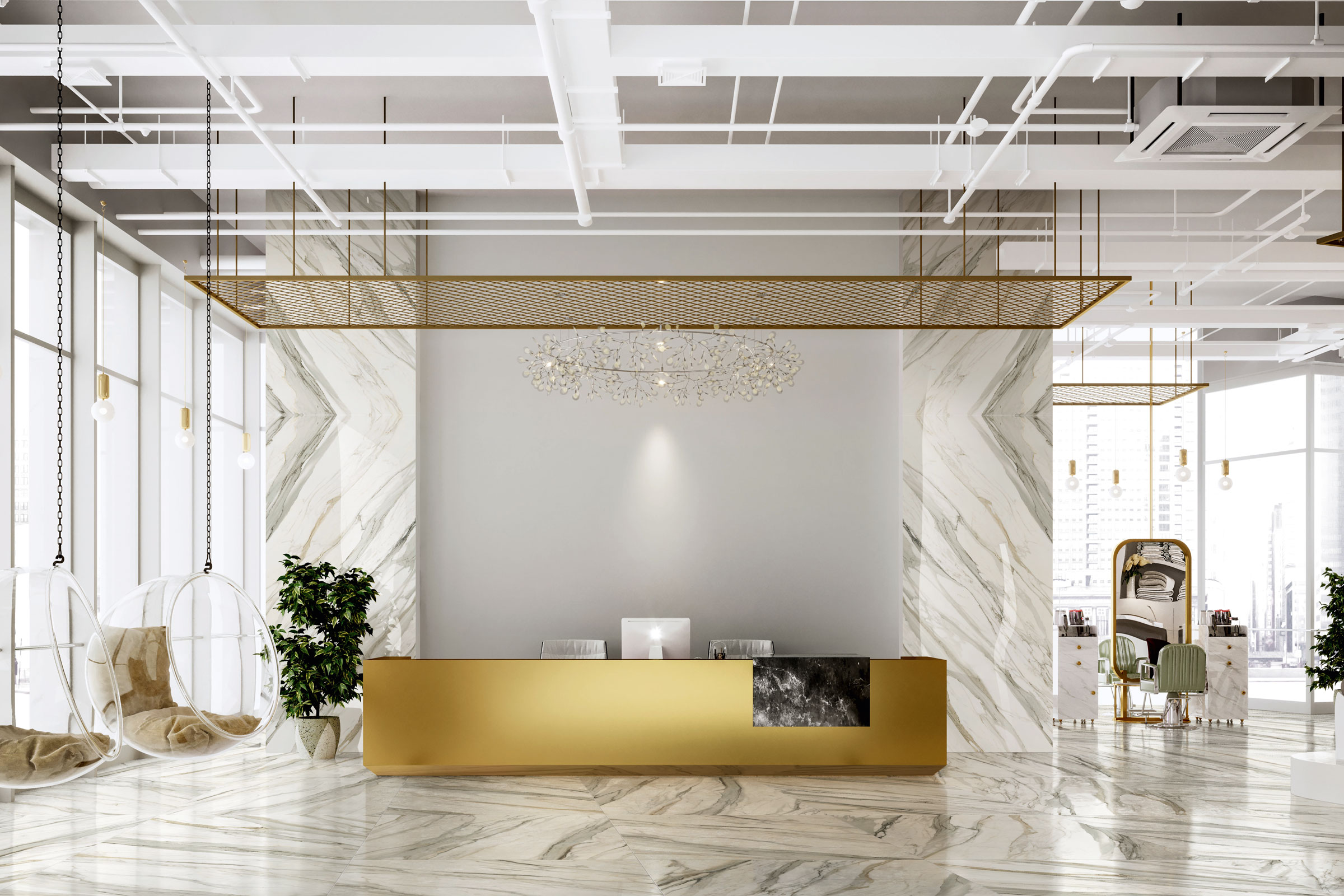
The JEM collection. Photo courtesy of MILE®stone
Recycling provides several environmental advantages, including reduced carbon footprint, reduced water consumption, and preservation of landfill space, among others. The circular economy is gaining prominence in the overall economy as viable in both the environmental and economic arenas. Porcelain tile is unique among flooring products because it is 100% recyclable at the manufacturing site, at end of life, and can utilize a wide range of post-industrial and post-consumer wastes as feedstock. To ensure accuracy and reliability of the recycled content designation, third party certification is a must.
Recycling of production scrap from all stages of production is an achievable goal for a modern porcelain tile factory. Well managed recycling of these materials can have a positive effect on the finished product, resulting in a superior product in terms of strength over the use of all virgin materials.
Many of the raw materials used in porcelain tile production can be supplemented or even replaced with recycled materials like mining wastes and post-consumer glass bottles. Recycling of porcelain tile at end of life presents certain challenges, but if the tile can be separated from other, nonceramic demolition waste it can be easily recycled. An additional advantage to porcelain tile at end of life is that it can be readily certified as āclean fillā and used in place of aggregate in roadbeds or under foundations.
Green Squared (ANSI A138.1)
Green Squared is the only multi-attribute sustainability standard and certification program specifically addressing tile and the associated products needed to install tile. The universe of included materials consists of ceramic and glass tiles, mortars, grouts, backer-boards, membranes, and other installation materials. Green Squared is a cradle-to-grave performance standard that minimizes the need to cross-evaluate single-attribute sustainability claims.
For a product to be Green Squaredācertified requires that it meet the American National Standard Specifications for Sustainable Ceramic Tiles, Glass Tiles, and Tile Installation Materials (ANSI A138.1). To be in conformance, products meet a broad array of demanding sustainability requirements and electives, as identified in the standard. The Green Squared framework for product evaluation and certification is in accordance with ISO Type 1 environmental labeling and declaration requirements (ISO 14024).
Developed by an ANSI-accredited committee of green building professionals, manufacturers, distributors, installers, and other stakeholders, the Green Squared standard, ANSI A138.1, contains an array of multi-attribute environmental and social criteria.
Environmental Product Characteristics
The first section of ANSI A138.1 standardizes product attributes like the amount of recycled content, level of volatile organic emissions, amount of indigenous raw materials, etc. Three levels of recycled content and reclaimed waste are defined in the standard. Level one is mandatory for conformance, and levels two and three are elective. Thresholds vary depending on product type.
There are also three standardized levels of indigenous raw material content. Recognizing the environmental burden from transportation, indigenous raw materials are those extracted within 500 miles of the manufacturing site. If transported by rail or sea, the limit is 2,000 miles. All three levels are elective.
There are five standard attributes for sustainable packaging. All five are elective, but it is mandatory that at least one be achieved:
⢠Minimal packaging (packaging cannot exceed a specified percentage of the product weight)
⢠Recyclable packaging (a specified percentage of the packaging is recyclable)
⢠On-site reusable packaging (100% reusable onsite)
⢠Biodegradable or compostable packaging (meets specific ASTM biodegradability criteria)
⢠Recycled content packaging (contains a specified percentage of recycled content)
A certified product must meet industry standards for durability and performance. For example, tile must comply with ANSI A137.1. Also mandatory for conformance, a product shall have low (for installation products) or no (for tile) volatile organic compound (VOC) emissions. Environmentally friendly maintenance instructions must also be available. Elective options for conformance to A138.1 include criteria for solar reflectance index (SRI), light reflectance value (LRV), and sound abatement. Also, electives for LCA and/or EPD are available.
With the plethora of green programs in the marketplace, Green Squared certification provides authenticity and conveys that the product certified can be trusted. The Green Squared framework for product evaluation and certification is in accordance with ISO Type 1 environmental labeling and declaration requirements (ISO 14024).
GREENGUARD
The majority of everyday chemical exposure in people occurs through the air we breathe in our homes, offices, schools, and other indoor environments. These airborne chemicals are commonly referred to as VOCs, which are used to manufacture and maintain many building materials, including many types of flooring. Studies by the EPA and other researchers have found that VOCs are common in indoor environments and that their levels are typically much higher than found outdoors.
There may be anywhere from 50 to hundreds of individual VOCs in the indoor air at any given time. Some may produce objectionable odors at low levels, while others have no noticeable smell. Many VOCs are irritants and can cause headaches, eye, nose and throat irritation, and dizziness. Long-term exposure to some VOCs may lead to chronic diseases or cancer. At high concentrations, some VOCs can be toxic.
The products that used to build and furnish our indoor environments can have a significant impact on indoor air pollution levels. Products that have achieved GREENGUARD certification are proven to meet rigorous, third-party chemical emissions standards, helping to reduce indoor air pollution and the risk of chemical exposure, while aiding in the creation of healthier indoor environments.
There are two tiers of certification: GREENGUARD certification and GREENGUARD Gold certification. All certified products are subject to a review of the manufacturing process and routine testing to help ensure minimal impact on the indoor environment. GREENGUARD Certification emissions limits were first used as purchasing specifications for the EPA and the state of Washington for furniture and commercial building products. GREENGUARD Certification criteria have been the basis for the LEED credit for low-emitting furniture since 2002.
The GREENGUARD Gold certification standard includes health-based criteria for additional chemicals and also requires lower total VOC emissions levels to help ensure products are acceptable for use in environments like schools and health care facilities. In addition to limiting emissions of more than 360 VOCs and total chemical emissions, GREENGUARD Goldācertified products must also comply with requirements of the state of Californiaās Department of Public Health (CDPH) āStandard Method for the Testing and Evaluation of Volatile Organic Chemical Emissions from Indoor Sources Using Environmental Chambers, Version 1.2 (2017),ā also known as California Section 01350.
Cradle to Cradle
The Cradle to Cradle Products Innovation Institute is dedicated to powering innovation for the circular economy through products that have a positive impact on people and planet. Through their Cradle to Cradleācertified Products Program, the Institute sets the standard for products that are safe, circular, and made responsibly. Cradle to Cradle certification is used by forward-focused designers, brands, retailers, and manufacturers across the value chain to innovate and optimize materials and products according to the most advanced science-based measures for material health, product circularity, renewable energy and climate, water and soil stewardship, and social fairness.
Cradle to Cradle certification is the global standard for products that are safe, circular and responsibly made. Leading brands, retailers, designers, and manufacturers across the value chain rely on the Cradle to Cradleācertified Product Standard to ensure the impact of their products on people and planet is a positive one. Cradle to Cradle assesses the safety, circularity, and responsibility of materials and products across five categories of sustainability performance:
⢠Material Health
⢠Product Circularity
⢠Clean Air and Climate Protection
⢠Water and Soil Stewardship
⢠Social Fairness
Porcelain tile is especially well suited to engage with the Cradle to Cradle program. Through the industryās extensive use of HPDs, EPDs, and other transparency initiatives, attributes associated with material health are positive and well understood and documented. The broad use of recycled content coupled with porcelain tileās end of life recyclability presents a strong circularity case.
The previously discussed GREENGUARD Gold certification, easily obtained by porcelain tile, supports clean air in the occupied space. As is typical to the porcelain tile industry, porcelain is manufactured without a wastewater discharge, supporting water stewardship. Among all competing flooring types, porcelain tile has the most straightforward compliance with the requirements of Cradle to Cradle Certification.
Floor Score
FloorScore is another indoor air quality certification standard for hard surface flooring materials, adhesives, and underlayments. Developed by SCS, a certifying body, with the Resilient Floor Covering Institute, an industry trade association of resilient flooring manufacturers and suppliers, it qualifies for many green building schemes including LEED v4.1, WELL, BREEAM, CHPS, and Green Globes. While initially developed for resilient flooring, FloorScore is compliant with Californiaās Department of Public Health (CDPH) āStandard Method for the Testing and Evaluation of Volatile Organic Chemical Emissions from Indoor Sources Using Environmental Chambers, Version 1.2 (2017)ā (also known as California Section 01350). It is an inclusive standard that can be used for porcelain tile.
Summary
As the design process increases its consideration of the impact of the built space on occupant health, transparency standards fill an ever-growing role. Forward-thinking manufacturers recognize this and are working to provide transparency standards for their products to support the design community in making responsible product choices. Porcelain tile is the preferred flooring choice when considering the impact on indoor air quality, its participation in the circular economy, or even its impact on climate change.