The experts at FiberTite share why their system works.
FiberTite® specializes in roofing membrane systems that last. Based in Wooster, Ohio, it is one of the leading roofing companies in the nation—constructing long-lasting roofs for more than 35 years.
“What sets us apart is our roofs’ chemical makeup, our fiber-knitting process, and the track record and history we have,” says Roy Ahrens, technical specialist at FiberTite.
Ahrens began working at FiberTite in 2015, but he knew about the company’s positive reputation for longevity and durability long before joining the team. He recognized and respected their work as a roofing consultant back in 2012. “You didn’t see many single-ply roofs that were still performing well after 30 years,” he says. “It piqued my interest when I found out the roofs that were lasting the longest were FiberTite roofs.”
Here are 10 ways the FiberTite roofing membrane proves to be the smartest method for building strong, durable roofs.
FROM OUR JANUARY+FEBRUARY 2018 ISSUE
The preferred publication of leading green professionals.
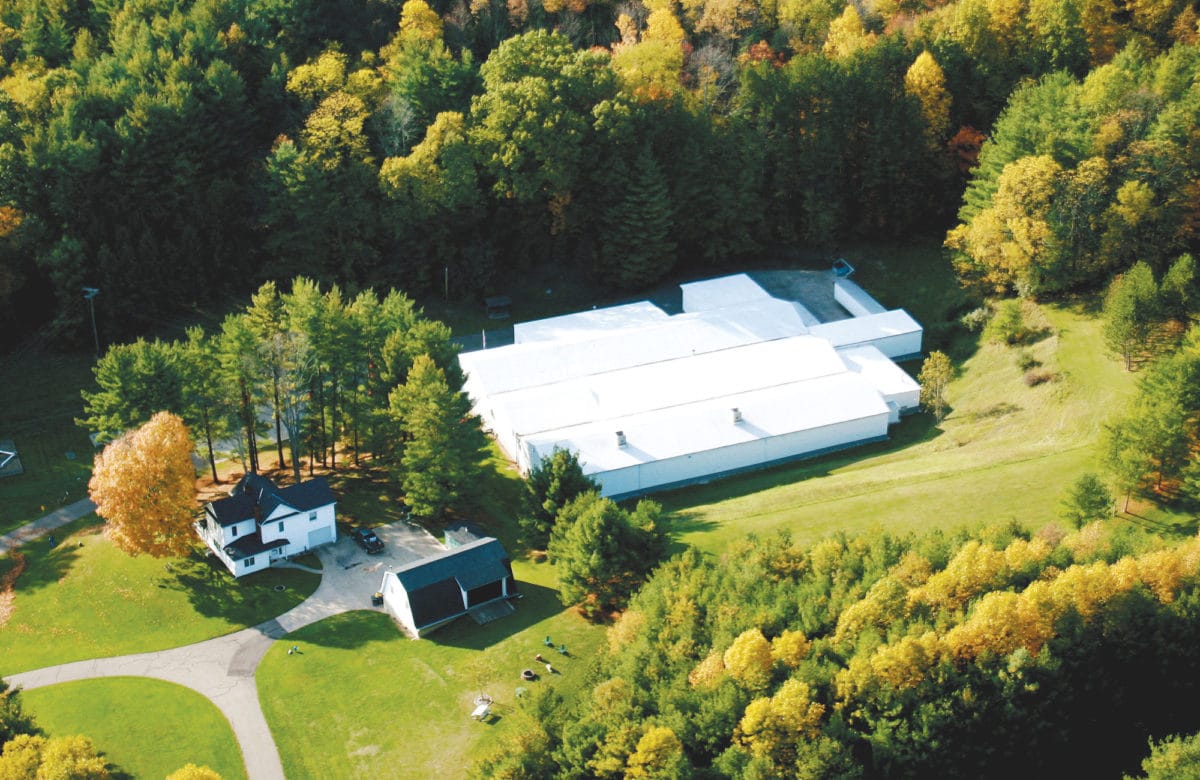
FiberTite roofs have proven to perform well even after 30 years. [Photo: Courtesy of FiberTite]
1. Product Formulation
FiberTite roofs outlast the rest because of their unique roofing membrane formula. In fact, the formula hasn’t changed since the start of the company in 1979—why fix something that isn’t broken?
The FiberTite roofing membrane utilizes Elvaloy® Ketone Ethylene Ester (KEE). In 1973, DuPont™ developed KEE with the hope of making better roofing materials. DuPont wanted to create a solid plasticizer with a high molecular weight that would not separate from a single-ply polyvinyl chloride (PVC) roof. “Before Elvaloy KEE was created, PVC roofs typically used liquid plasticizers. But liquid plasticizers migrate out of the system. This means the PVC would revert to being brittle and more prone to cracking or shattering,” Ahrens says.
Ahrens explains that a solid plasticizer, unlike liquid, bonds with PVC to create a new permanent compound, increasing the longevity and durability of the material. Elvaloy KEE resins also fight weathering and chemical breakdown to allow for more durable single-ply roofing systems.
In the ’70s, Seaman Corporation (FiberTite’s manufacturer) began line trials using Elvaloy with PVC to create a geomembrane. About two years later, the XR-5® geomembrane was developed, and it was ready for use by 1975. It’s the highest strength and most chemical resistant geomembrane on the market, and FiberTite was born of it.
Today, the FiberTite formula has a proven blend of KEE. The optimal amount of KEE not only makes the roof more resistant to UV rays and chemicals but also contributes to longevity, repair ability, and superior performance.
2. Building Security
Safety comes first, and critical facilities need increased protection when it comes to roofing. Hospitals, schools, data centers, and food processing plants cannot afford the risk of roofing damage or water leaks. “The Ohio Facilities Construction Commission deems roofing as one of the top critical components in a building,” Ahrens says. “If the roof were to fail, it would cause many safety issues.”
Single-ply FiberTite membrane roofing systems provide premium protection against chemicals, standing water, and other damages compared to conventional single-ply and multi-layer roofing systems. FiberTite also offers hybrid multi-ply roofing systems to increase roofing redundancy. This formula combines the FiberTite membrane as the cap sheet with FiberTite SBS Modified Bitumen base sheets for maximum protection. FiberTite utilized a hybrid multi-ply roofing system when working on the Good Samaritan Medical Center in Lafayette, Colorado.
3. Chemical Resistance
“Some people think, ‘Well, we don’t have jet fuel. We don’t have fats and oils like food processing plants, so I’m not worried about chemical contamination.’ But, the reality is, all roofs have chemical contamination, whether from normal pollution or standing water,” Ahrens says.
As previously mentioned, FiberTite was born of the XR-5 geomembrane, which was developed to contain and protect against acids, oils, methane, and alkalis. Across the world, XR-5 is used for pond liners, secondary containment, floating covers, and wastewater baffles. FiberTite’s product formulation makes it the most chemical resistant of all roofing membranes.
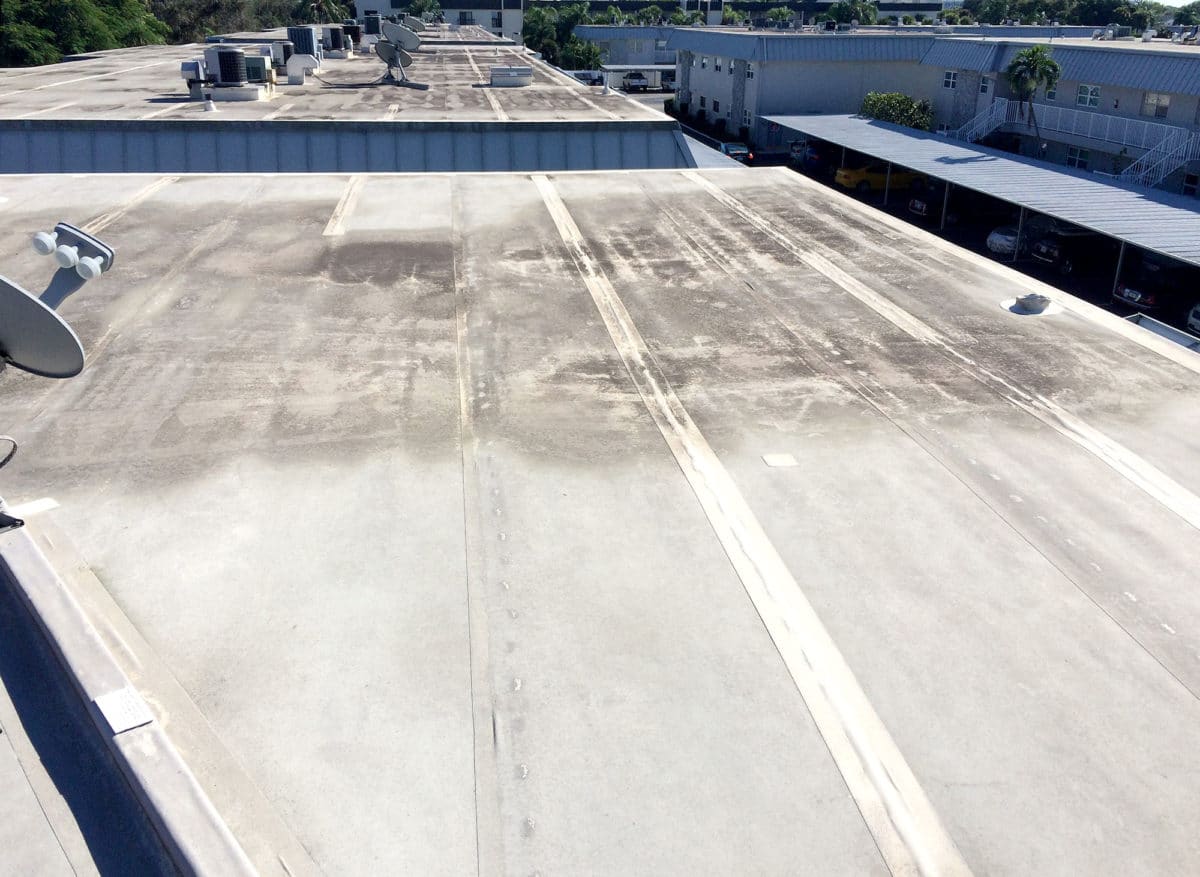
The FiberTite KEE membrane is self-extinguishing thanks to its chemical makeup. [Photo: Courtesy of FiberTite]
4. Puncture Resistance
“As you can tell from our name, fiber is the backbone of our roofs,” Ahrens says. “The roof’s puncture resistance has everything to do with the fabric.”
Contrary to popular belief, roof puncture resistance doesn’t depend on the thickness of membrane—the fabric is what makes the roof more puncture resistant. Using poor quality fabric with low fiber counts creates a flimsy, weak membrane.
Unlike other roofing membrane companies, FiberTite knits and weaves its own fabric at its weaving mill in Tennessee. From start to finish, the FiberTite team has complete control and customization over the fabric manufacturing process. FiberTite typically uses twice as many yarns within a one-by-one-inch square than other manufacturers, which makes its reinforcement fabrics stronger and more resilient.
5. Combustibility
The FiberTite KEE membrane is self-extinguishing thanks to its chemical makeup. The vinyl in the PVC includes a flame resistant chlorine component.
If you expose the FiberTite membrane to fire, you can see this chemical process in action. Once you remove the flame source, membranes other than the FiberTite membrane continue to burn, while FiberTite self-extinguishes once the flame source is removed.
6. Water Tightness
Waterproofing a roof starts with the fibers. FiberTite roof membranes are water resistant because the yarns are covered in a primer coat that encapsulates them and increases their water tightness. No other company in the industry takes this important step after the knitting and weaving process.
“Many roofing systems adhere their fibers using a heated strikethrough process where the top and back coat are sandwiched together with the scrim in between,” Ahrens says. “But at FiberTite, we encapsulate the yarns first and then fuse the top and back coat together separately, which fully waterproofs the roof.”
The prime reason for the top coat is for waterproofing and to protect the yarns from water damage. And there is no need for extra sealant because the custom-made yarns in the FiberTite membrane are already watertight.
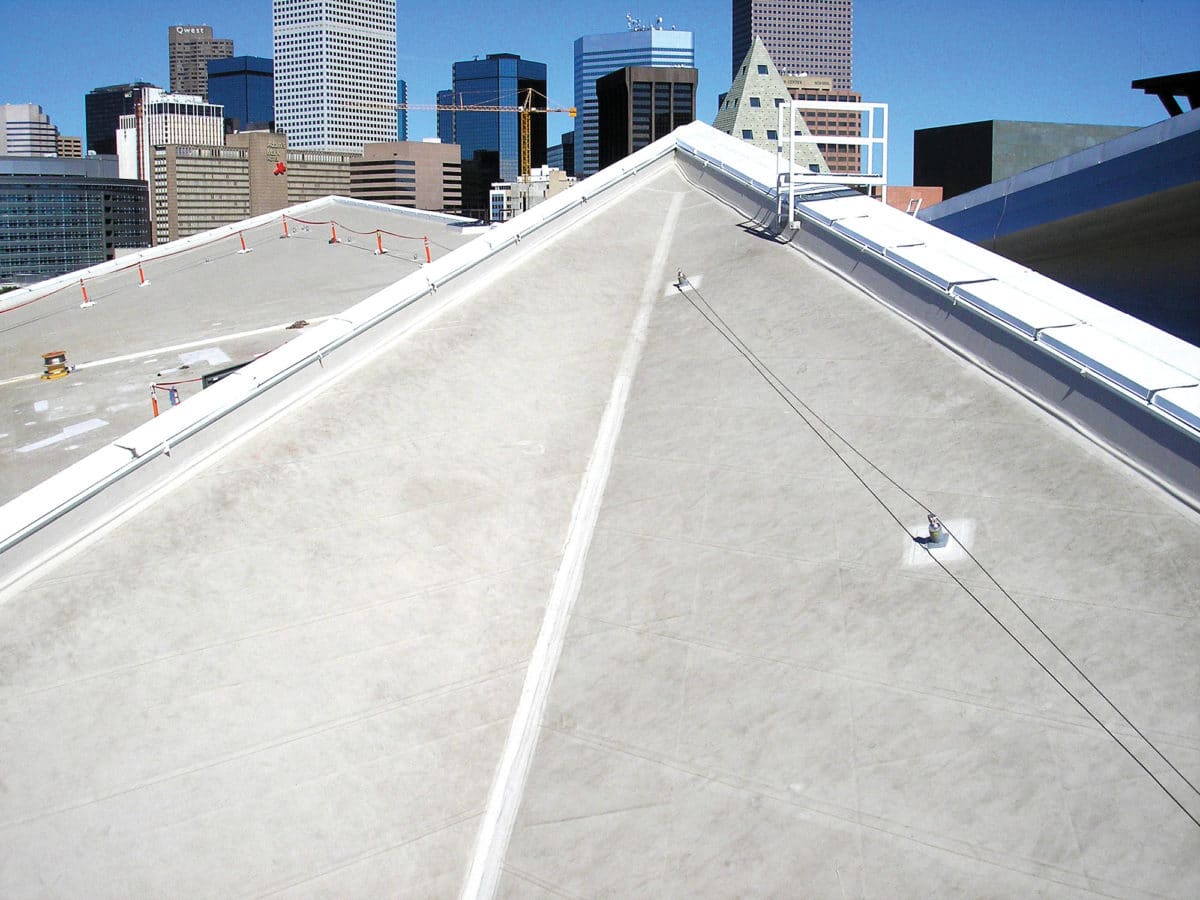
FiberTite’s strong, puncture resistant roofing system was the perfect choice for the Denver Art Museum. [Photo: Courtesy of FiberTite]
7. Sustainability
FiberTite is sustainable, efficient, and ecological. The company has one of the top scores from the Cool Roof Rating Council and was one of the first roofing membranes labeled under the ENERGY STAR roofing products program. FiberTite roofing membranes also exceed LEED requirements.
FiberTite also offers rooftop gardens, or green roofs, popular among environmentally conscious clients. These sustainable roofs provide many benefits, including energy efficiency, stormwater and flooding control, cleaner air, and a longer roof life span. Green roofs also add thermal insulation, which lowers utility costs.
FiberTite and its manufacturer, Seaman Corporation, are also founding members of the Vinyl Roofing Division of the Chemical Fabrics and Film Association, which helps educate architects, building owners, and contractors on the benefits of vinyl as a sustainable material for single-ply roofing systems.
8. Solar Reflectance
UV light inevitably damages materials over time. Since your roof can’t wear sunscreen, it’s important to install one with high solar reflectivity (SR) and infrared emittance (IE) to help your roof last longer and improve your building’s energy efficiency.
“UV is what breaks down and ages roofs,” Ahrens says. UV radiation alters the chemical composition of your roof; when oxygen molecules combine with hydrocarbons, materials begin to break down. As these molecular changes take place, your roof becomes more susceptible to cracking.
Ahrens says flat, built-up roofs were much more common when he started in the industry 30 years ago. “Roofs were not nearly as solar reflectant as they are now. If the roof wasn’t covered in gravel then it may have had a coating to increase its reflectance, but this ended up being a maintenance issue since the roof would lose its reflectance over time.”
The FiberTite roofing membrane has an acrylic coating to keep it cleaner and more reflective. High solar reflectance helps with cooling costs in summer and lengthens the roof’s life span. The FiberTite membrane also meets the SR and IE requirements of California Title 24 energy efficiency standards.
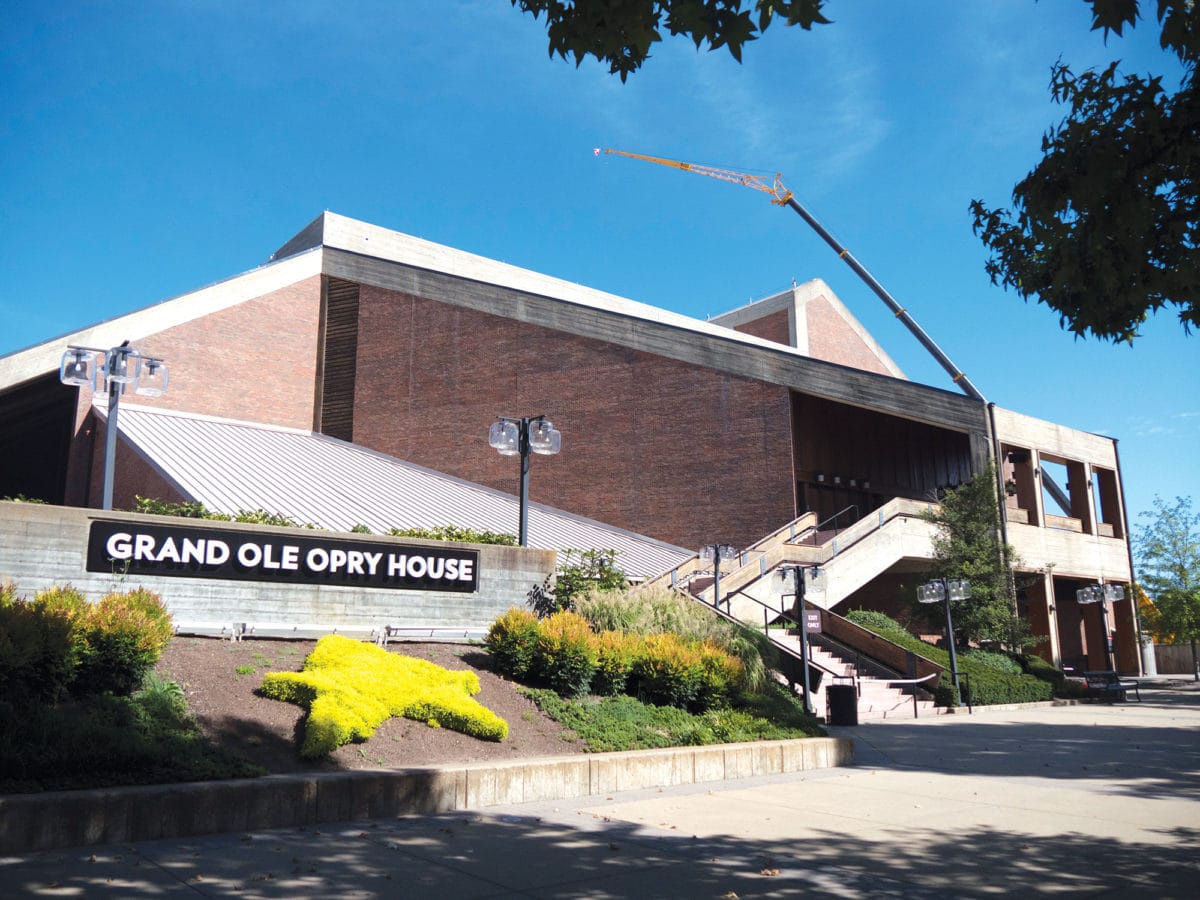
[Photo: Courtesy of FiberTite]
9. Durability
Durability and longevity go hand in hand. “Carl Cash, a roofing industry expert, suggests building owners consider the durability range as a better indication of a roof life span instead of a warranty,” Ahrens says.
Because of the solid plasticizer KEE in the FiberTite KEE membrane, FiberTite roofs are very strong and durable. “Everything will wear on the surface over time depending on different conditions, but our KEE membrane has the best durability and takes the longest to wear that surface away,” Ahrens says.
Depending on the environment, it takes several years for a FiberTite roof to lose just one thousandth of an inch (mil) off the surface.
10. Longevity
Roofs that last longer are more cost effective and better for the environment. FiberTite roofs can withstand harsh chemicals and perform well for decades. As a result, FiberTite’s carbon footprint is much lower than the industry average.
While initial roofing cost may be slightly higher for a FiberTite membrane, the investment pays off with a much lower life cycle cost. You won’t need to replace your roof as often as other membranes. Since its introduction in 1979, no FiberTite roof has experienced membrane failure—ever.
You’ll also find FiberTite’s work at:
- Bristol Motor Speedway
- Denver Art Museum
- Duke University Medical Center
- Georgia Aquarium
- Grand Ole Opry
- Houston Airport
- Rubbermaid, Inc.
- Spangler Candy Company
- Tyson Foods
- Universal Studios
- Yankee Stadium
Learn more about FiberTite and see related content about roofing.