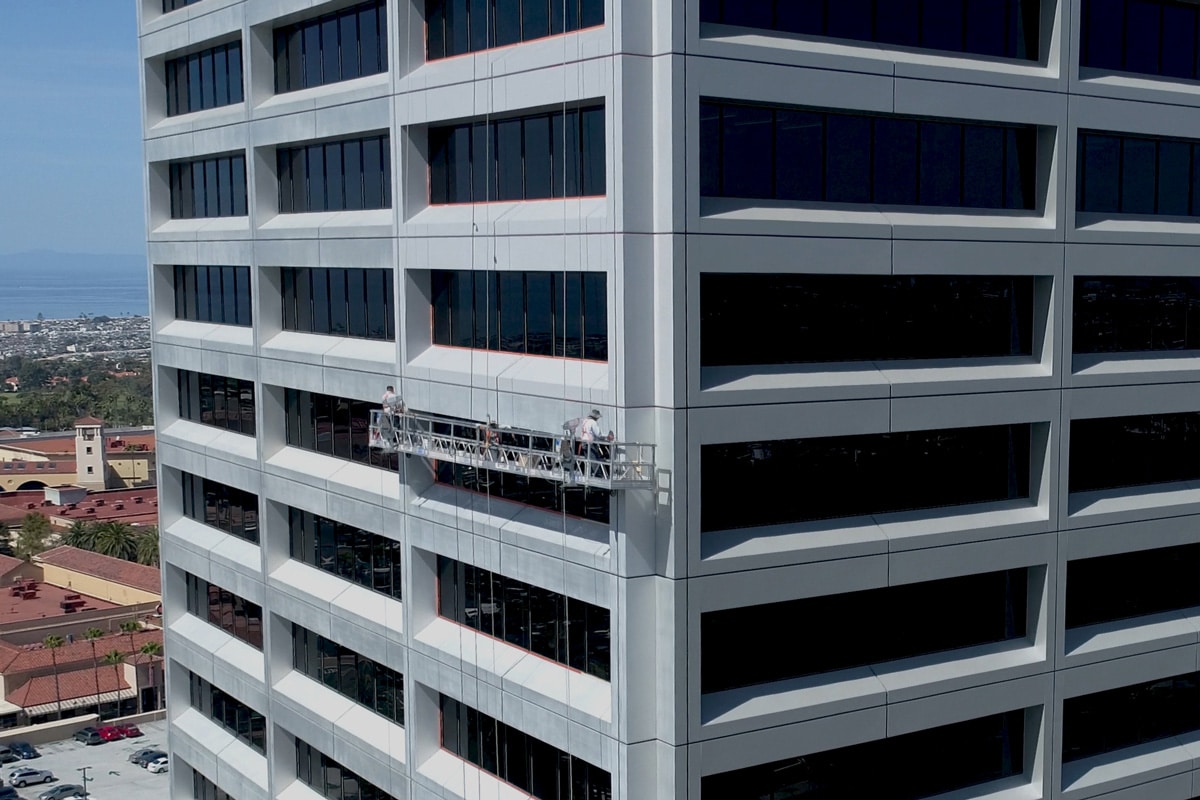
[Photo: Courtesy of APV Engineered Coatings]
About 75% of the U.S. population lives within 50 miles of a coast, and most of the metal structures in those regions are subject to coating degradation like chalking or fading caused by extreme ultraviolet or other types of harsh environmental exposure. For more than three decades, Rex Dean, of NeverFade® certified applicator Stuart Dean, has inspected and consulted on more than 4,000 facade projects around the world. As the company’s global director of facade restoration, he specializes in on-site metal restoration. Here, Dean notes major factors to consider in the metal coating process—from corrosion mitigation and surface preparation to final applications.
In coastal areas, we often see what’s called filiform corrosion on exterior coating systems of factory finishes and architectural aluminum. It looks like blisters and bubbles, and often those blisters break and you’ll see aluminum oxide as well as a buildup of chloride. But the solution isn’t to re-clad over the issues. Instead, it’s important to address the problems.
When filiform corrosion is present on architectural aluminum, you need to ensure all the corrosion is exposed. We mechanically abrade the finish to discover any hidden corrosion. Then we wash the surface with a Chlor-Rid® to remove salts. If you don’t remove the salts, you’ll ultimately sand those chlorides into the metals, causing failure at a later date.
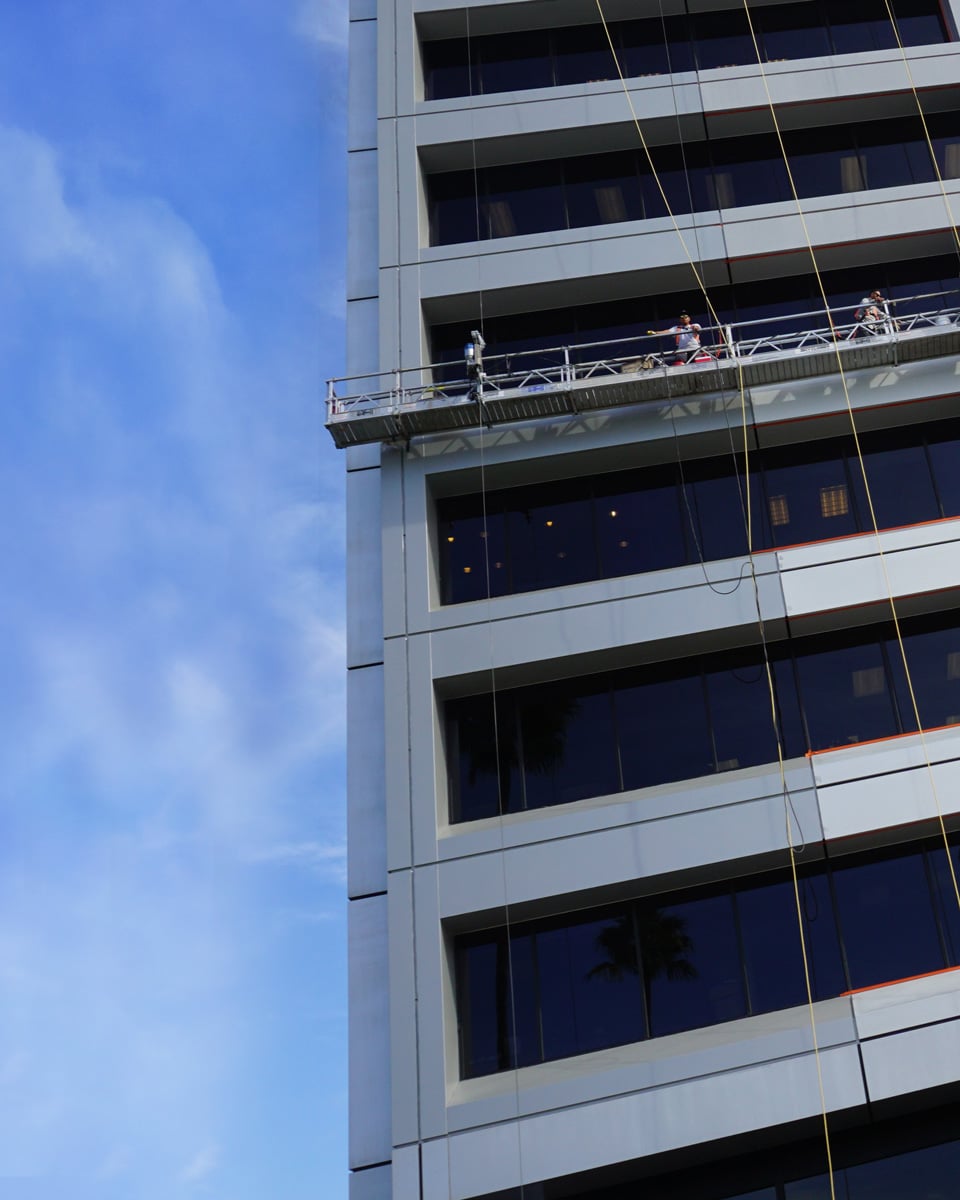
[Photo: Courtesy of APV Engineered Coatings]
Next, we micro-blast using a small handheld blaster and aluminum oxide to flush out the corrosion. We do this because the corrosion cell is below the surface, so you can’t wire brush or sand the contaminants from it—you have to reach the crevices. The mitigation done, we typically use a pre-treatment similar to something that would be applied in a factory in an AAMA 2605 specification, like a phosphate wash or a chrome pre-treat. Both of those substances are recognized as a step that retards and fights corrosion as well as creating adhesion, so when the primer coat is applied, it will properly adhere to the substrate.
When it comes to the coating application process, APV’s NeverFade is highly flexible. The Kynar Aquatec® polymer in NeverFade allows us to ensure the performance of an AAMA 2605 factory coating standard with a field-applied system. It can be sprayed, brushed, or rolled, depending on project needs.
Climate is also important. In the case of field-applied coatings, the substrate temperature should be 50 degrees Fahrenheit or greater, and the air temperature and relative humidity should be monitored in relation to the dew point. We monitor conditions throughout the project.