Story at a glance:
- Miller Hull designed Loom House off of the Pacific Coast to meet Living Building Challenge standards—and then some.
- The homeowner wanted the water treatment system to be available to the entire community.
- The landscape architect worked to remove invasive species, bring in natural species, and protect the watershed as part of the design.
When our team was introduced to the Loom House clients, we had an instant connection. Interior designer Charlie Hellstern had been working with them for many years, and when they mentioned to her that they were ready to build a new home and wanted it to be energy-efficient, she thought to introduce them to Miller Hull right away.
As we got to know about our new client’s lifelong work of environmental stewardship and social justice, we began to think of a more holistic way to plan their home. The owners have spent their lives running a foundation to foster a more equitable and environmentally responsible world by funding projects that find inventive ways to increase environmental justice. Their history led us to propose a green building certification that supports performance, human health, and equity: The Living Building Challenge (LBC).
Loom House is located in the Temperate Conifer Forest biome in the Puget Sound Lowland. Beginning with an existing home was important for the clients, as they wanted to reduce their environmental impact. The property they purchased for renovation consisted of two small buildings. While they were designed in the beautiful and classic Northwest modern style, the home contained chopped-up spaces that did not take advantage of the beautiful views nor the forested site. Our design goals were to maintain the home’s original character while upgrading the envelope and making the floor plans more functional.
The clients would live in one of the buildings and work in the other, making full use of their property day and night. The renovation surgically implements an envelope upgrade to meet the net positive energy performance of the Living Building Challenge. We carefully added a net positive water system to the property to provide rainwater collection and water treatment all without harming the existing, lush landscaping. This was all while maintaining the original design character of the home.
People often remark on the difficulty of the Living Building Challenge, but it is not that the LBC is too tough, it is that we must change the way we have all been designing and shift the business as usual of an entire design and construction industry to more equitably and sustainably design homes and buildings for people and our planet.
True to the Living Building Challenge, the project team began our work with a biophilia charrette led by Sonja Bochart. The entire design and construction team met onsite with the clients and took our time to understand the natural elements that shape the property. It was a powerful meeting where we all connected by sharing influential stories of nature from our childhood. This charette set the tone for the project as we bonded with each other and developed clarity for the project with inspiration on how to bring nature-based design solutions into this new home.
The Site
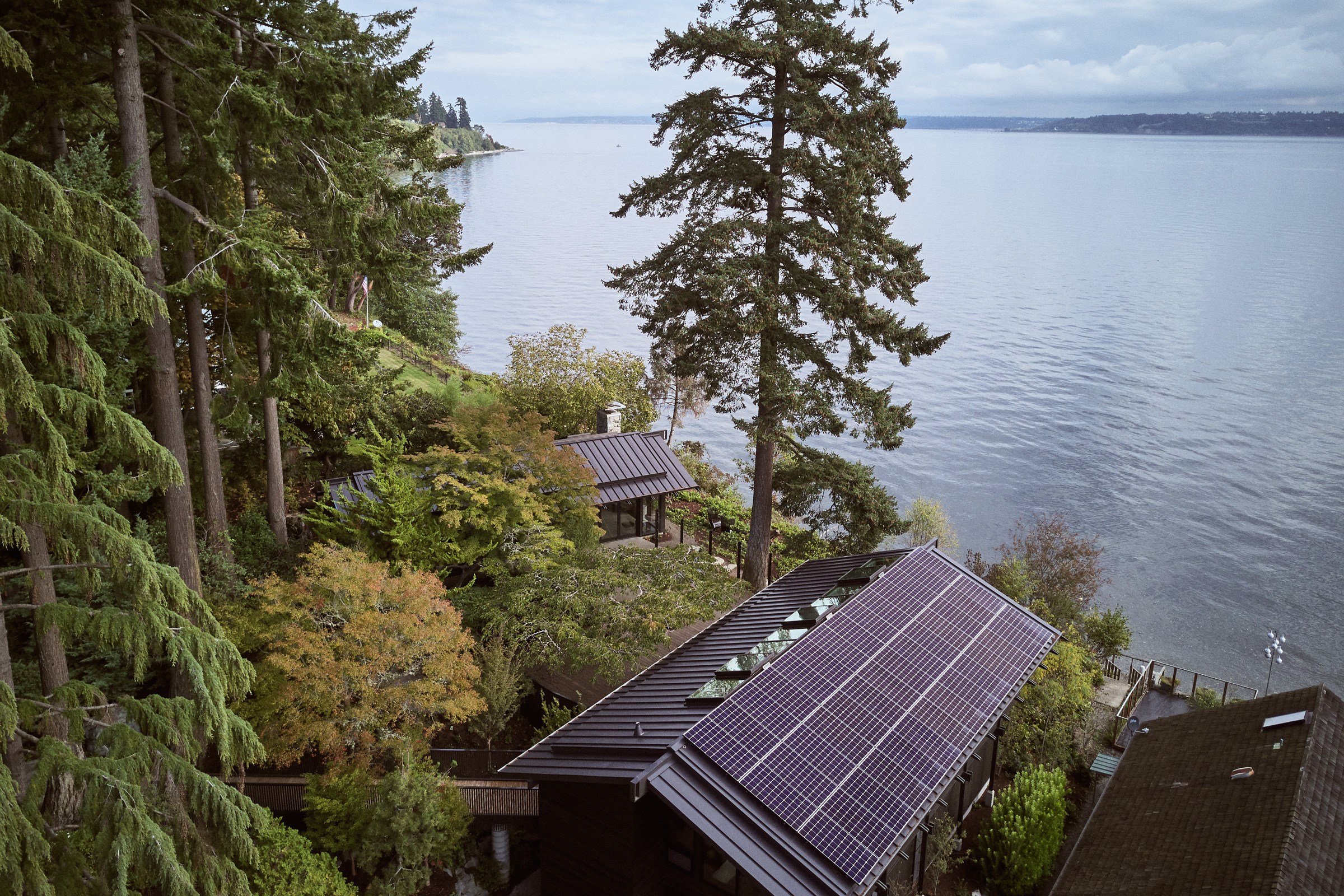
Loom House is located in the Temperate Conifer Forest biome in the Puget Sound Lowland off the Pacific Coast, and the homeowners wanted to reduce their environmental impact as well as give back to the community. Photo by Ben Schauland
From the outset, the team asked how Loom House could be an active steward of its watershed, protecting the ecological health of the landscape while helping it flourish. This became a major design tenant with Landscape Architect Anne James’ work as we transplanted existing trees, removed invasives, and brought in natural species. Habitats such as nurse logs and native plants are in place for birds and other pollinators, while the watershed and its keystone species are protected from harmful runoff.
With an abundance of beautiful plants and trees, including some 100-year-old conifers, the clients hired a world-renowned tree expert, plant pathologist and arborist Olaf Ribeiro, to review their conditions. He brought invaluable insight to help sustain the health of the property’s historic trees.
In redeveloping the property as a Living Building project, our team had to wrestle with how to transform a mature garden requiring intensive maintenance and high water use into a garden that would significantly reduce maintenance and irrigation demand. These challenges had to be met while also providing the agricultural component required to fulfill the LBC Petals.
To solve this, rainwater is captured, treated, used to grow fruits and vegetables as well as infiltrated back into the site to complete the hydrologic cycle. Native plants along with onsite urban agriculture, including a hazelnut grove and mycological foraging forest containing native species, provide food for the homeowners. A berry bramble, located near the community mailboxes to encourage neighborly sharing, includes a mix of native berries. The plants include nitrogen fixers, accumulators with deep taproots, and ones selected for pest control with the goal of creating a resilient, regenerative, and beautiful garden.
Water
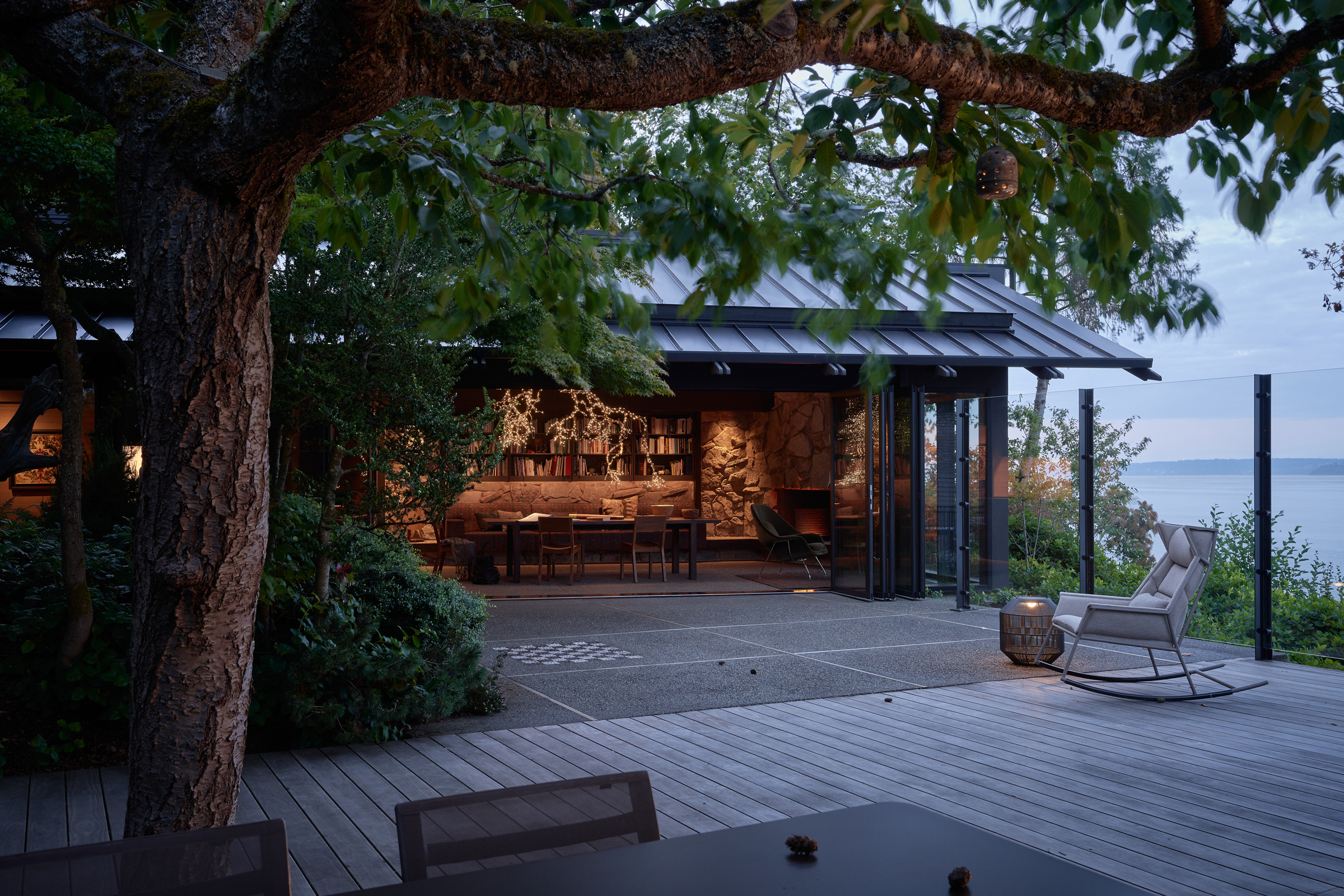
Loom House incorporated repurposed materials like salvaged steel from an old ship for the front door, once-overgrown wisteria branches transformed into a beautiful light fixture, and old concrete walks hand-laid into new site retaining walls. Photo by Kevin Scott
With its beach-front location, Loom House has a great responsibility to the health of its watershed. Now viewed as likely the most difficult Petal of the LBC, the Water Petal is on full display in the daily workings of the property.
All stormwater is treated onsite—rainwater is collected from roofs and fed into a 10,000-gallon, below-grade cistern before being treated to potable levels with a system of filters and UV disinfection before being pumped to efficient fixtures. All the home’s grey and black water is treated onsite through subgrade treatment boxes. The treated water is dispersed as subsurface irrigation and infiltrated back into the water table. The entire system, with the homeowner’s using only about 20 gallons per day, can function off-grid, which further supports the home’s resilience capability.
Loom House has always been about more than just a single building project for one family. One of the seven Petals of the Living Building Challenge is Equity. When our clients committed to building a Living Building home and office, they asked the design team to commit, too. They charged the team with making sure that every Petal of the Challenge was equitable. Like us, our clients know that while buildings like these can help advance sustainability in our industry, this progress will not be fast enough nor successful enough, if they are not made available to everyone.
Led by the homeowner’s commitment to making the water treatment system available to the entire community, the design team successfully worked with the city to allow the onsite treatment of water and subsurface dispersal. This year-long process was a partnership working with the city council, city engineers, and health department. This effort was designed to help the natural solutions of the Living Building Challenge scale to other properties and building types across the county. It even helps relieve the demand on the municipal water treatment plant, which is already overburdened. Now, Loom House’s legacy has created a pathway for countless others to follow in the name of water stewardship.
Energy
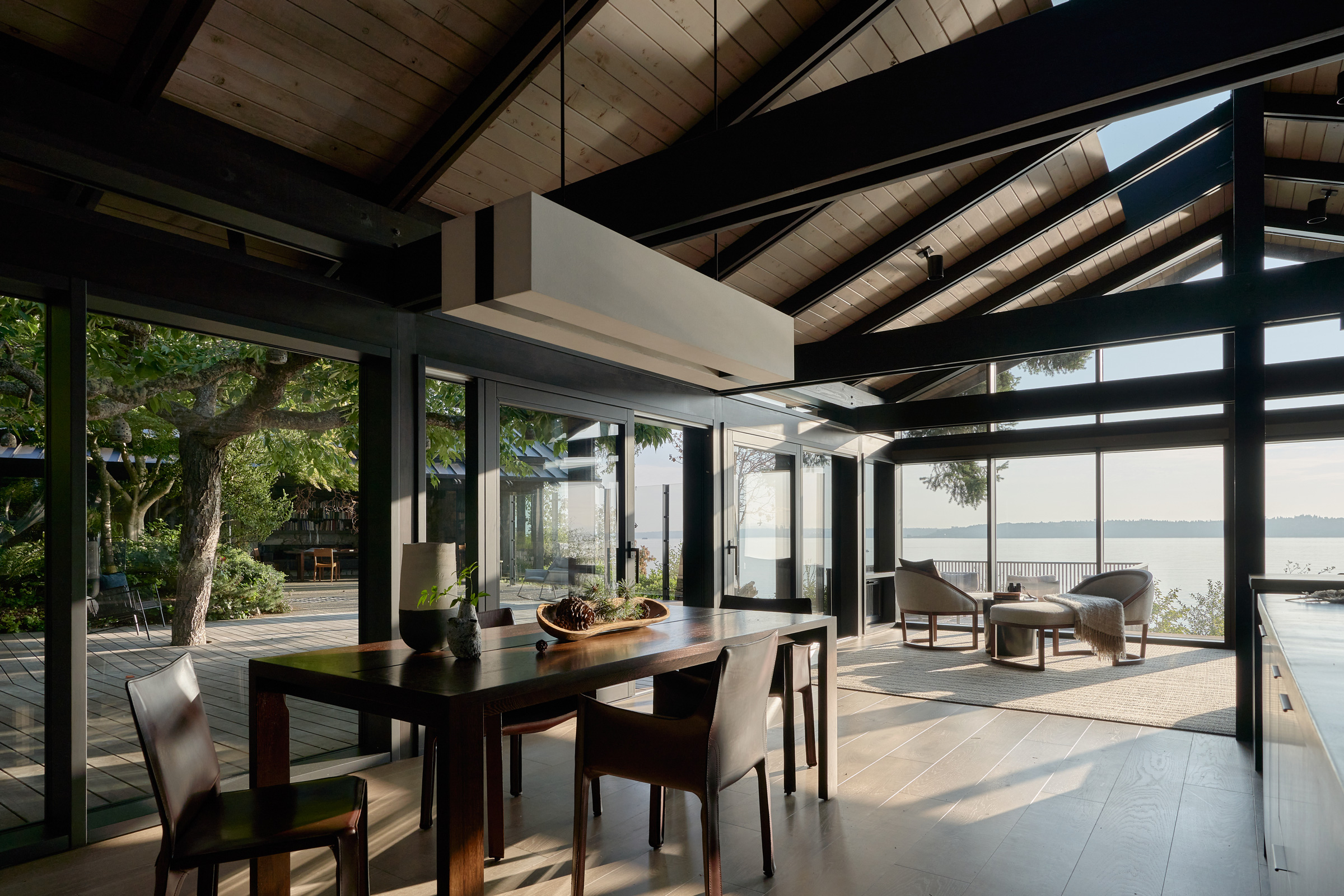
Photo by Kevin Scott
The all-electric Loom House performs at 105% net positive energy using approximately 16,800 kWh of electricity while generating 17,600 kWh from the onsite photovoltaic system. This makes the home’s operational emissions zero.
The Loom homeowners always wanted the material and land savings inherent in an existing home. Keeping the primary structure and reusing exterior cladding helped maintain the home’s original character and reduce the embodied carbon as well. Embodied carbon emissions were calculated at 43 metric tons of CO2. This is after our successful 39% global warming potential reduction from the home’s primary materials. The entire embodied carbon footprint was offset through a one-time purchase following results from a whole building LCA.
Loom House benefits from the mild-maritime Puget Sound climate, which provides the ability to cool with natural ventilation and use radiant systems for additional cooling and efficient heating. A substantial upgrade to the building envelope supports these efficient systems and provides thermal comfort. Working closely with our contractor, Clark Construction, the team preserved the home’s original character by carefully removing and restoring the exterior siding and then replacing it. Insulation was added to the walls and roof and triple-glazed windows and doors were installed throughout.
Some energy challenges included the 24/7/365 operation of this home serving both residential and office functions. Lighting control systems and residential-scale UPS to deal with the frequent island power outages contributed to some of the highest energy demands. To help offset these challenges, extremely efficient appliances, extensive daylighting, heat pump radiant floors, and heat recovery ventilators keep the home’s total energy use low.
One of the biggest challenges came from finding accurate, reliable energy monitoring systems that would provide enough information for the owners to track use and modify behavior. After trying three manufacturers and testing their systems, we found that this type of residential-scale feedback system may not yet exist in the market.
Another challenge came during the effort to decarbonize the home. In an effort to remove all combustion sources from home to meet the net positive energy goals, the existing fireplace was decommissioned. The team was left with an existing fireplace and chimney, which was repurposed into a glowing LED art piece mimicking a flame. The final piece evokes a hygge quality, reminiscent of a warm hearth. Rather than demolishing the leaky stone chimney, efforts were taken to seal the building envelope around it to help reduce infiltration.
Materials
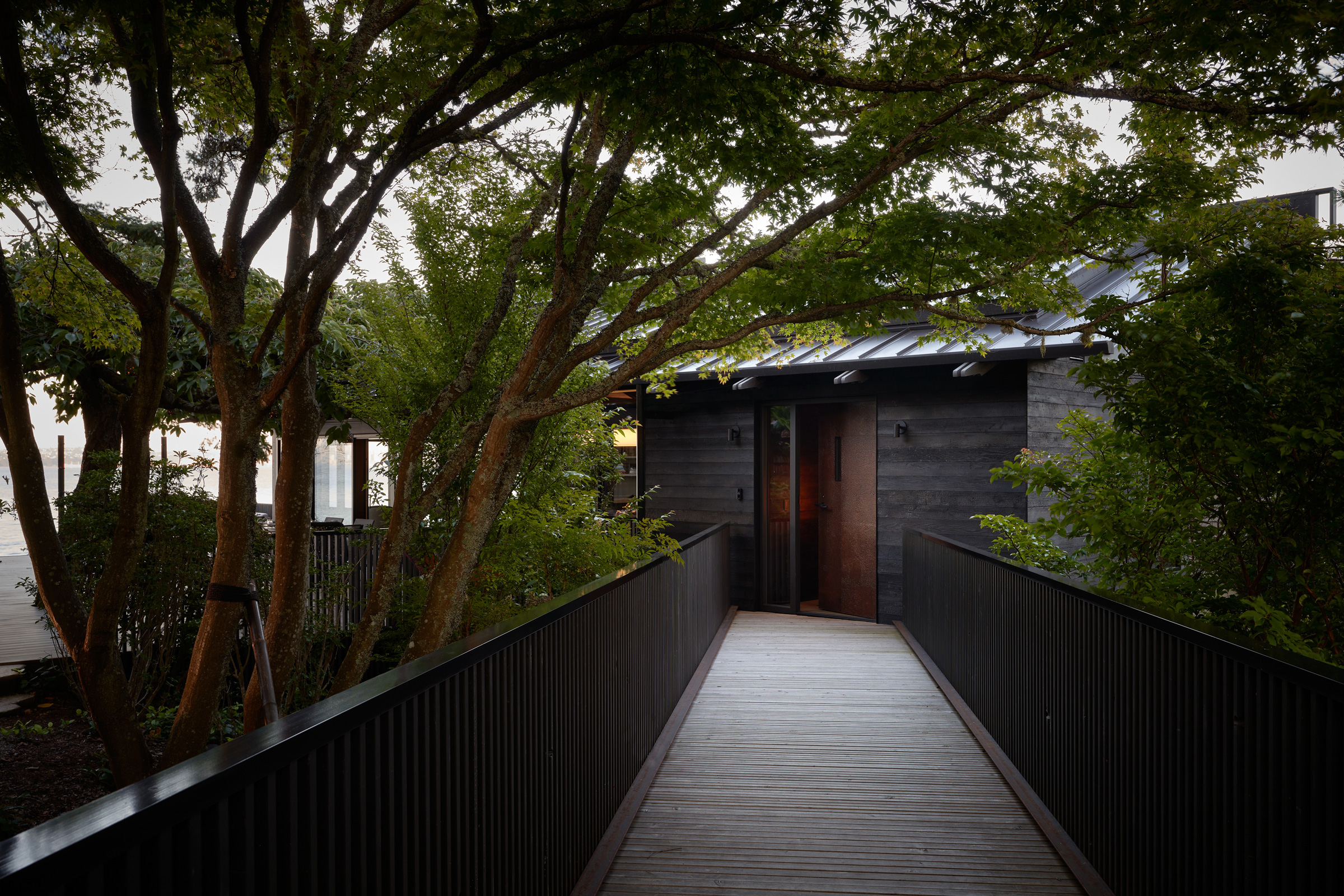
Photo by Kevin Scott
Creative solutions to incorporate repurposed materials like salvaged steel from an old ship for the front door, once-overgrown wisteria branches transformed into a beautiful light fixture, and old concrete walks hand-laid into new site retaining walls all help reduce the need for new materials. Thirty-nine percent of all construction materials came from within 300 miles of the home and 98% of all project waste was diverted from landfills or salvaged.
Focusing on occupant health as a major driver of the project, the team wanted to go beyond the already strict requirements of the Living Building Challenge and ensure that all furniture and furnishings in the home were free of the harmful Red List chemicals like the rest of the project.
Hellstern worked closely with her artisans and furniture makers to identify safer alternatives to common furniture materials that often contain Red List chemicals. These materials included wool, organic latex, cotton, and organic down feathers instead of typical petroleum-based products.
In addition to reusing furnishings the homeowners already had, all new pieces of indoor and outdoor furniture were composed of all-natural materials and help contribute to good indoor air quality. Compliance with California Department of Public Health standards for emissions ensures the home has reduced TVOC’s and other PM contaminants.
Conclusion
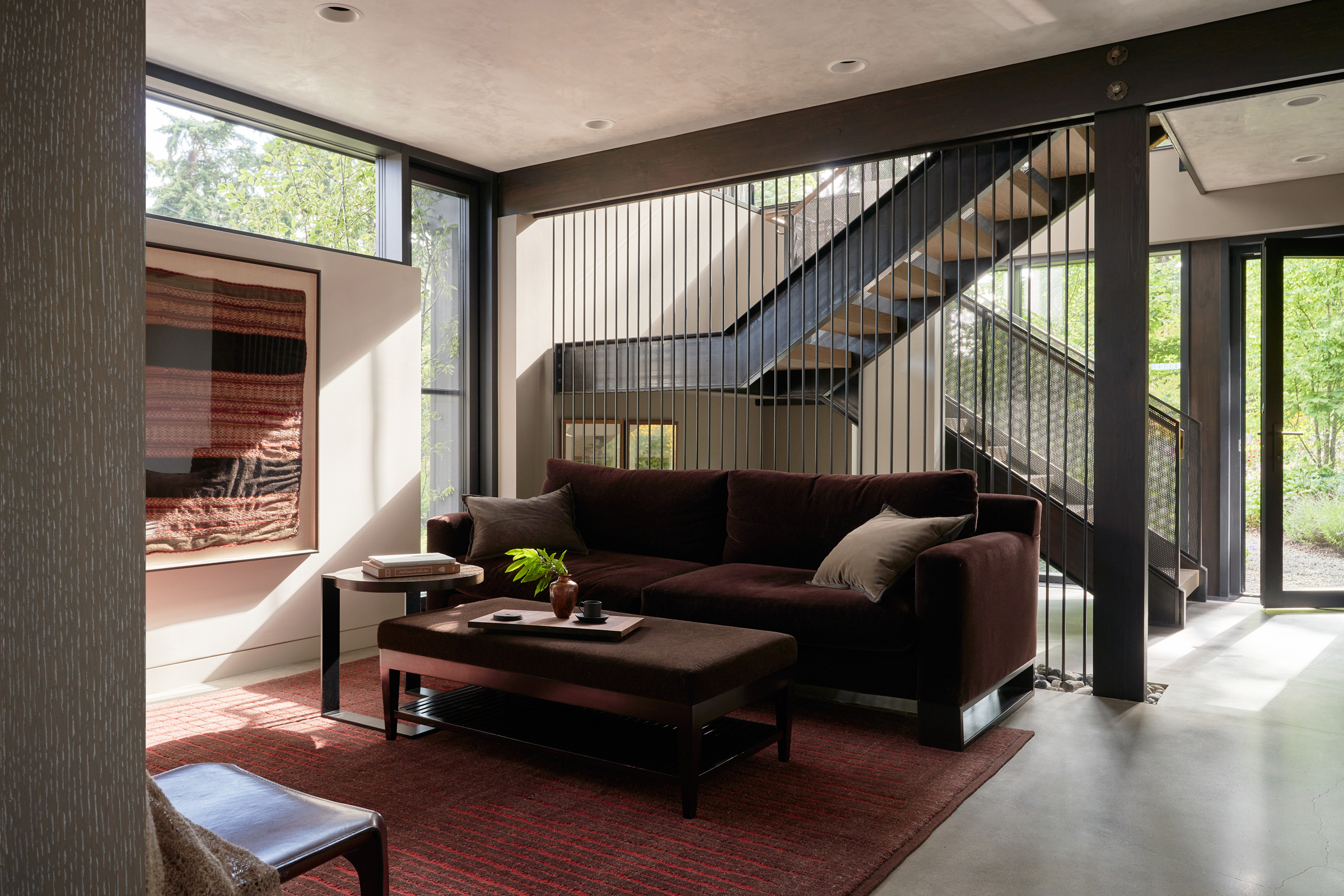
Photo by Kevin Scott
Loom House is only the fourth home in the world to achieve Living Building certification and the first residential renovation to do so. The homeowners tell us it costs less to operate their property each month than their cell phone bills; Living Building homes are possible now. They make sense financially and they certainly make sense in support of human and environmental health. Our message to both homeowners and design teams considering this level of meaningful sustainability is that you can do it and it is worth it. Our planet and our communities need you.
While Loom House has been successful for our clients, it also had broader community benefits. With the clients’ commitment to equity in their transformational home renovation, this project has changed city building code to allow other homes to treat their water on-site, opened a portion of their garden to the neighborhood, provided work for countless artists and craftspeople in the region and also provided water treatment systems for dozens of other homes through the Living Building Challenge’s Handprinting opportunity.
The legacy of Loom House is not just in how it performs, but it is also the opportunities the project creates for other homes to be good stewards to their environment as well.