Story at a glance:
- Skanska is working to be net-zero by 2045. They’re also working to reach a 70% reduction in Scope 1 and 2 emissions by 2030.
- Radiant heating and cooling is an effective way to lower energy demand and gain energy efficiency while providing more designable space.
- Uponor is working to produce 90% of its product portfolio with Environmental Product Declarations.
With federal commitments to reduce net greenhouse gas (GHG) emissions by 50% in 2030 and reach net zero by 2050, many industries are carving new paths to sustainability. All eyes are largely on the architecture, engineering, and construction industries, as buildings account for more than 40% of annual global CO2 emissions.
One of the largest construction and development companies in the US, Skanska, has even more ambitious goals, with a climate plan for net-zero by 2045. They’re also working to reach a 70% reduction in Scope 1 and 2 emissions by 2030, and in 2022 they achieved a 55% reduction. Part of how they accomplish that is by working with equally committed partners. “The building material supply chain is hugely important, and getting that supply chain decarbonized,” says Heidi Creighton, former national head of sustainability for Skanska USA Commercial Development, now principal of Creighton Sustainability Advisors. “We really need all of those pieces to fall in place so we can all get to our zero commitments.”
Defining Sustainability
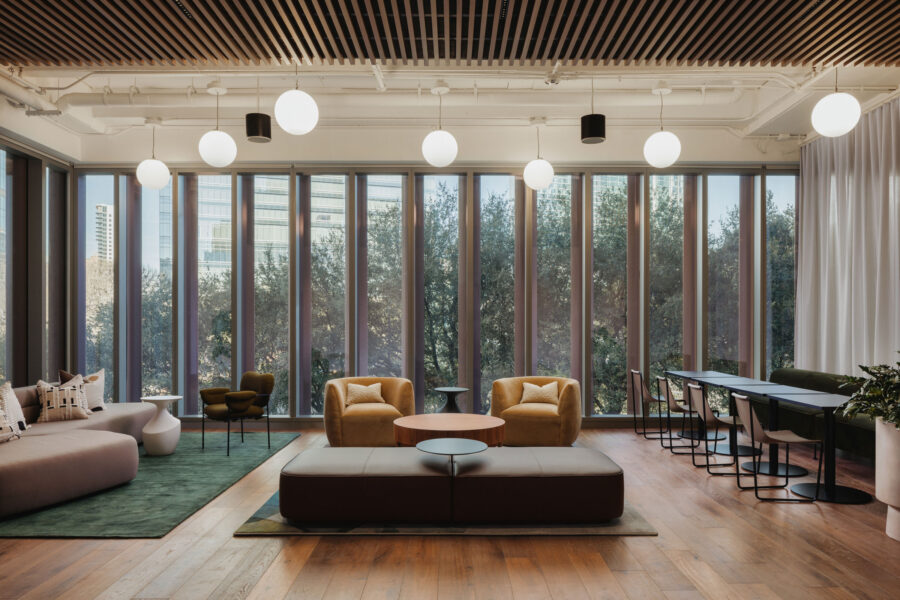
Inside 1550 on the Green in Houston. Photo courtesy of Skanska
Creighton, who recently joined USGBC California as a senior advisor for decarbonization, says people can sometimes be confused about what net zero means, as different definitions exist. “The Federal Government is working on a definition so the whole industry can get around it,” she says. “Because when somebody makes a claim like that, you really need to drill in and understand. Educating the market is hugely important, and understanding what Scope 1, Scope 2, and Scope 3 are is also important.”
The EPA defines Scope 1 emissions as direct GHG emissions that occur from sources controlled or owned by an organization (in other words, emissions associated with fuel combustion in boilers, furnaces, vehicles). Scope 2 emissions are indirect GHG emissions associated with the purchase of electricity, steam, heat, or cooling. While Scope 2 emissions physically occur at the facility where they are generated, they are accounted for in an organization’s GHG inventory because they are a result of the organization’s energy use, the EPA says. Scope 3 emissions include all sources not within an organization’s scope 1 and 2 boundary.
“Education within our industry and also outside of our industry and to our customers is super important,” Creighton says. “I think when people don’t understand something they’re not as engaged, or maybe they feel like it’s a little bit too abstract or like what they’re doing wouldn’t impact the end result, but that’s not true at all. We all need to band together and work toward these goals for a healthy, sustainable, regenerative built environment.”
Skanska works to set aggressive sustainability goals early in each project. “We set a target for all of our projects and do everything we can to indicate to the market that this is a key priority for us—and that we’re going to focus on low carbon materials because I think it’s so important for the supply chain to see those signals that the large buyers really want this.”
And that is true of every Skanska project. “We need everybody to be doing this, and we are able to say that 100% of our commercial development portfolio in the US is LEED-certified or pursuing certification. LEED Gold is the minimum target—and we get to Gold or Platinum on all of our projects. We love our third-party certifications,” Creighton says, pointing also to WELL, Fitwel, Salmon-Safe, and others.
Skanska also considers aspects like water usage, stormwater collection, and heating and cooling as part of its efforts to reach net zero. “Carbon is super important, but we also can’t lose sight of other really important aspects around sustainability. For example, water scarcity is becoming more and more important,” Creighton says. “And storms are becoming more frequent and more intense.”
Sustainable Solutions: Water
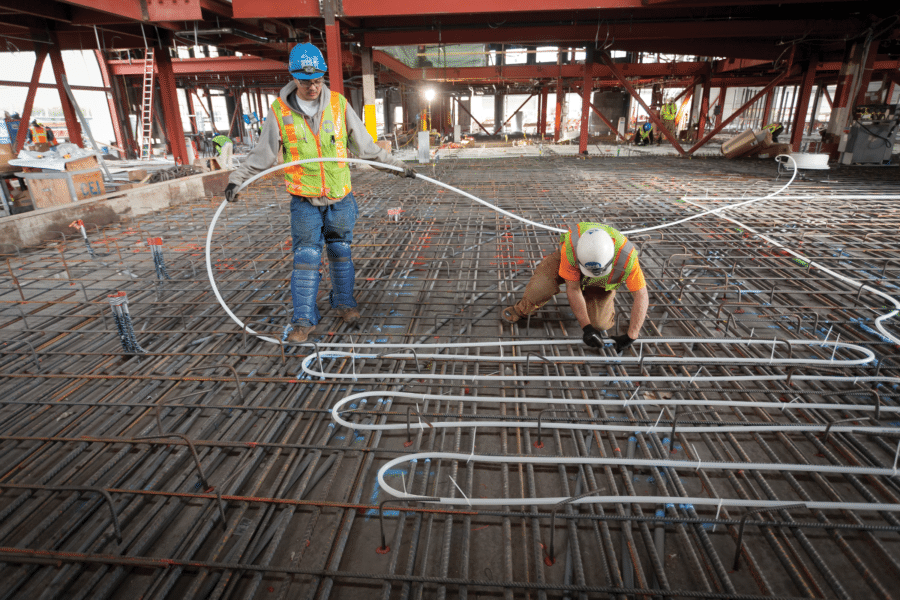
The Pier 15 Exploratorium project in San Francisco uses PEX embedded in a concrete slab to circulate water from the San Francisco Bay as a heat sink and source for chilled water. Photo courtesy of Uponor
Some manufacturers, too, have been focused on developing greener solutions since before it became trendy. “Sustainability is a part of Uponor culture. It’s really been a part of what we do for a long time,” says Chrissie Walsh, sustainability manager at Uponor, a global leader in plumbing innovations.
Uponor is now shining a light on their work and sharing data from what they’ve learned with the industry, helping customers to reach their own sustainability goals. Solutions like their AquaPort are one way Uponor is making projects more sustainable, as it decentralizes domestic hot water in commercial settings. The AquaPort is a new technology focused on generating domestic hot water that is both more hygienic and delivered more efficiently. It’s an ideal solution for owner-occupied spaces with high unit density, says Hailey Mick, business development manager for engineering services at Uponor. She points to patient towers in health care, student housing and higher education, and high-end hotel rooms as great examples.
“It’s a self-contained unit that uses the energy from a building’s hydronic HVAC heating system to create domestic water locally on demand in the unit,” Mick says. “By doing that, we’re eliminating the central domestic hot water system, which results in a 40% reduction in the piping in the building. So every pipe is basically a heat exchanger.” That also means a 50% reduction in the volume of domestic hot water in the plant.
Installing AquaPorts gives design teams more designable space, delivers hot water faster, and requires less chemicals. “We can lower the amount of water in the plant, and we can lower the energy it takes to deliver hot water to the faucet,” Mick says. “It’s a huge savings for both energy and water, and then look at the elimination of all the additional piping you would need.”
She says it’s sometimes difficult for owners to choose high-efficiency solutions if the payback is 10 years or more, but the AquaPort aims to address domestic hot water issues without driving up the initial cost for the building owner.
Small Changes Add Up
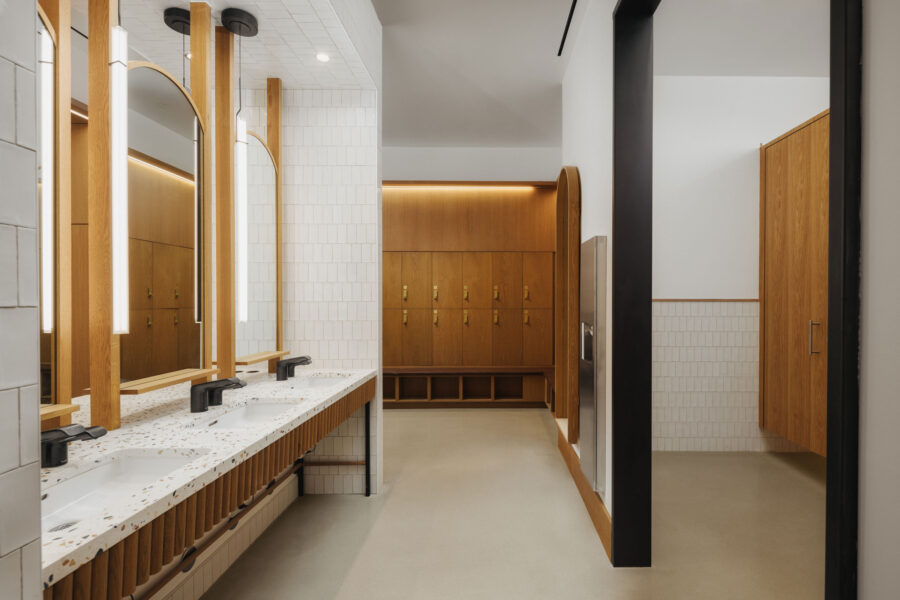
A bathroom space inside 1550 on the Green in Houston, designed by Bjarke Ingels Group and built by Skanska. Photo courtesy of Skanska
“We at Uponor may not be a huge part of the volume of your total build, but we can have a substantial impact on how you’re going to approach building better and how you’re going to start the conversation around decarbonization,” Walsh says.
A new Uponor program called Kitting Services is all about speeding up installation and reducing labor, material costs, and jobsite waste, making the entire construction project smoother from start to finish. “Because at the same time that we’re trying to create these super-efficient buildings and use all this new technology, we’re also dealing with a shortage on both the engineering side of the business and the contractor side. Having solutions that are more efficient and easier and faster to install is going to be critical to the success of projects,” Mick says.
We can have a substantial impact on how you’re going to approach building better.
Uponor’s core product, the total polymer solution, is also important to the whole life of a building, Mick says. “A traditional metallic piping system needs to be re-piped every seven to 10 years. With a total polymer solution, we’re looking at 50-plus years.”
Piping is a bigger piece of the whole puzzle than some may think. “It’s not just going to last longer, it’s less likely to become more energy intensive to run water through a polymer pipe than a metallic pipe over time because it’s less prone to corrosion and buildup, which ultimately affects the pressure drop and how much energy it takes to get the water through the pipes. It really is more important than people think. They just never had to look at all of the components at such a granular level.”
Mick has been in commercial construction for almost two decades and has watched what she calls a very welcome shift to working smarter and more collaboratively. “It’s great because when people are willing to share their experience, it can really accelerate technology in this space.”
Walsh agrees and says they’re seeing not just more collaboration across the industry but also a shift to a more systems-based thinking and approach to sustainability. “Every facet of the industry is easing into and simultaneously accelerating the understanding and acceptance that sustainability needs to be a part of how we’re going to build better,” she says. “It’s an exciting time to be working in sustainability and seeing these conversations really move forward in tangible ways. It’s no longer a legitimate thing to say sustainability costs too much.”
In fact, she says that’s no longer true in many cases, as it often costs less over the course of a building’s lifetime. “It’s going to cost you less in maintenance. It’s going to cost you less to operate over the lifetime of the project. And with evolving legislation and investment funding being put in place to scale technologies, a lot of what used to seem unrealistic is becoming cost-neutral or, at least, competitive.”
Real Talk About Radiant
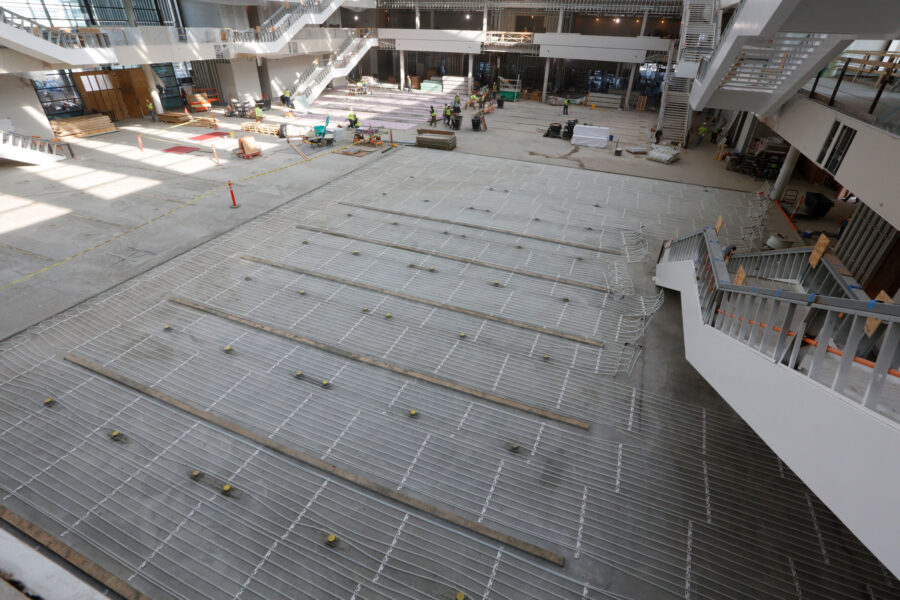
Radiant is an effective way to lower energy demand and gain energy efficiency while providing more designable space to architects, as the panel and equipment in radiant is substantially smaller. Photo courtesy of Uponor
Radiant heating and cooling will be critical to helping both commercial and residential projects reach net zero, Mick says. “Radiant heating and cooling are going to provide that energy efficiency profile you need to integrate into that solution. There’s more and more discussion across industry boundaries—it’s brand agnostic—and we’re starting to see more stakeholders sit down and talk to each other in a way that is meaningful and impactful.”
While more people are considering radiant than in years past, some misconceptions do persist. “People see it as a luxury item,” Mick says. “They think it’s going to cost more, but modeling is key to getting the right data in front of the decision-makers. When you model a building and you account for thermally active surfaces, then you can really see that a radiant system is going to require so much less energy. It’s going to be smaller-capacity equipment that you’re installing.”
Because water has the capacity to transport energy 3,500 times greater than air, hydronic radiant is an effective way to lower energy demand and gain energy efficiency while providing more designable space to architects. Radiant can be installed in renovations, too. “Everyone thinks you have to have a new build for radiant. It’s ideal for a new build, but there are solutions out there; you just have to think outside the box.”
Plus, renovations are critical to the overall sustainability story, Mick says. “We want to talk about renovation because there’s a huge stock of existing buildings that will need to be addressed for efficiency gains and decarbonization strategies. It’s really important we talk to everyone involved in the construction process. We can’t just talk to one stakeholder in a silo; we have to make sure owners, engineers, architects, contractors, and so on are comfortable installing these technologies and know how it works because each has an influential voice in the build process. If they don’t know these solutions exist or that they can be applied in a renovation, they’re certainly not going to advocate for it, and they might even advocate against it.”
Forward-Thinking
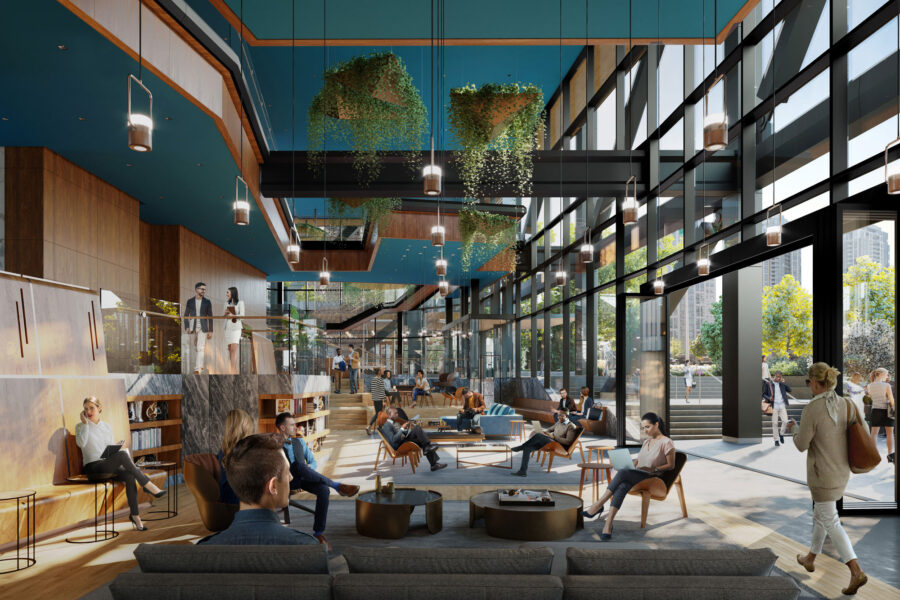
Skanska built The Eight in Bellevue, near Seattle. The 26-story, 541,000-square-foot office tower embraces native landscapes and activates the plaza along NE 8th street with 11,000 square feet of retail, including a 1,900-square-foot standalone pavilion. The Living Room is connected to the lobby and is an indoor/outdoor casual space also connected to retail.
Skanska has been doing sustainability reporting since the mid-90s and continues to look for partners who push the envelope to help them achieve more energy-efficient buildings.
“We want to do the right thing and also attract best-in-class tenants and investors,” Creighton says. “We want to future-proof these buildings and show those investors that we see decarbonization regulations coming and we’ve already designed the building to meet those future regulations, so you don’t have to do really expensive retrofits.”
For example, Skanska is heavily invested in doing all electric buildings ahead of regulations. “We want to keep that forward-thinking lens and really work with our tenants to help them meet their goals and help educate them on how the built environment is part of their Scope 1, 2, and 3 emissions and the goals they set for themselves.”
Skanska worked on the recently opened 1550 on the Green in Houston, designed by Bjarke Ingels Group. The 375,000-square-foot, 28-story office building is on Discovery Green—a beautiful park in the central business district. “It’s a stunning project with outdoor roof terraces on three levels and beautiful views,” Creighton says. “That indoor-outdoor experience and views are becoming increasingly important for projects as tenants want to attract people back to the office.”
The team was able to reduce the embodied carbon by 45% over the baseline for the Houston project, in part thanks to choices like low-carbon concrete, metal framing, aluminum fins, gypsum boards, glazing, and the acoustic ceiling, she says.
The Eight in Bellevue, just outside of Seattle, is another successful Skanska project, with tenants set to occupy the building in January 2025. Creighton says it’s the largest single office transaction in the company’s history and one of the largest leases in the Puget Sound area in the last few years, at more than half-a-million square feet and 25 stories, with an emphasis on native plants and mass timber.
Smart Choices

Uponor is a leader in energy-efficient underfloor heating and cooling and offers reliable, hygienic plumbing and infrastructure solutions that are lightweight and easy to install. Photo courtesy of Uponor
Material choices are easier with the free, open-source EC3 Tool, co-created by Skanska with industry partners. “When you’re procuring materials, it helps you make the best decisions around embodied carbon,” Creighton says. Input your project address and material quantities, and it will search more than 100,000 Environmental Product Declarations to deliver your options, showing the best low-carbon choices and offering a comparison with other materials.
“It was a really exciting commitment in Skanska because we could have just made a tool to use internally, but it’s grown immensely because it’s a free and impactful tool for the industry to use. We’ve committed to using that tool since 2020 on all of our projects,” Creighton says.
Setting sustainable goals clearly and early is more important than ever, she says, and Skanska will continue to invest in low-carbon strategies. “Business as usual isn’t going to continue to work. We need to continue to transform ourselves and innovate and invest in new strategies and technologies.”
Creighton says, “I don’t think anyone should feel like they’re alone in this. All those collaborators and all those partners are super excited to push the envelope, too. I believe our architecture and engineering teams truly enjoy working with us because we are really leading the way, and they get to be an important part of that.”